14 minute read
Precision Valve goes global
Next Article
JUNE / JULY 2021
16 Shiploads of Axe actuators – PRECISION VALVE SA has recently exported a number of containers of aerosol parts to back up the roll-out of a new Axe deodorant range to a surprising range of countries, including Russia, Argentina and Mexico
Precision Valve SA goes global
There’s no Axe to grind as Pretoria manufacturer ships out container loads
PRECISION VALVE SA in Rosslyn established in 1968 and since then one of South Africa’s leading manufacturers of aerosol dispensing products, is living up to its status as a member of the international PRECISION Group by going, literally, global too.
It has recently exported a number of containers of aerosol parts to back up the roll-out of a new Axe deodorant range to a surprising range of countries, including Russia, Argentina and Mexico.
In one case, several 40-foot containers were flown out to Latin America.
PRECISION VALVE SA – one of PRECISION’s 17 manufacturing facilities in 15 countries, the world leader of aerosol valves and a key player in actuators – is the only manufacturing facility of the Group in Africa. It was selected as the pilot site globally to produce the actuator for the new Axe aerosol container in 2019.
According to Robin Rigney, MD of PRECISION VALVE SA, the success of the launch in this country resulted in it being called on to support first the manufacturer in Russia and thereafter in Argentine and Mexico, especially as PRECISION has a global infrastructure that is easily able to ensure logistical support to the market.
“Our process at Rosslyn has proved to be stable and reliable, to the extent that we were called on to support our customer’s plants in other territories,” said Rigney, who has a wealth of experience in large FMCG contracts and complex manufacturing operations. “We have invested in several pieces of high-performance manufacturing and assembly equipment, but probably the main plus for us has been that our production team have been so reliable, innovative and efficient,” added Rigney.
Axe is a brand of Unilever Group, which is also supplied under the ‘Lynx’ brand.
PRECISION has a global infrastructure that is easily able to ensure logistical support to the market
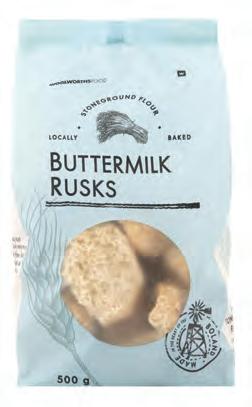
Recycled PS raft cleans up Westlakebites the dust Another box WOOLWORTHS’ vision is zero packaging waste to landfill, promising all BUILT and designed by Hilton Cowie its packaging to either be of Envirolite, approximately 10kg of reusable or recyclable by recycled polystyrene was mixed with 2022. Recently Woolworths Enviolite’s special lightweight cement changed the cardboard box aggregate to form this two-person and recyclable polypropylene raft. Fifty 5-litre PET bottles were also bag used in its Everyday inserted into the cavity of the raft to increase its buoyancy. The raft will be used to remove litter trapped in the river reeds and beds, and also to remove algae from the river. There are currently three nets installed in the river that are used to trap the litter to prevent it from entering False Bay. Rusk range – Bran, Muesli and Condensed Milk – to just a fully recyclable polypropylene bag. Since July 2020, Woolworths have sold over 176 851 bags of rusks, saving a total of 8.44 tons of unnecessary 23 cardboard packaging.
JUNE / JULY 2021 17
23
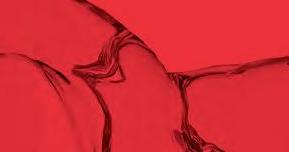
Trade. Create. Elevate.Trade. Create. Elevate. > www.meraxis-group.com > www.meraxis-group.com
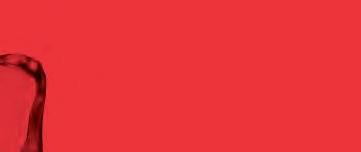
Deep Deep insights,insights, deep deep impact.impact.
Meraxis South Africa (Pty) Ltd Meraxis South Africa (Pty) Ltd Johannesburg +27 11 4552889Johannesburg +27 11 4552889 Cape Town +27 215567787Cape Town +27 215567787 Durban +27 318169381Durban +27 318169381
Thank You!
Twist in the Taili … not quite, CAD Plastics is in fact very happy with its range of Taili injection moulding machines, set up to require minimal operator intervention, and the Pinetown convertor now operates 13 of the machines
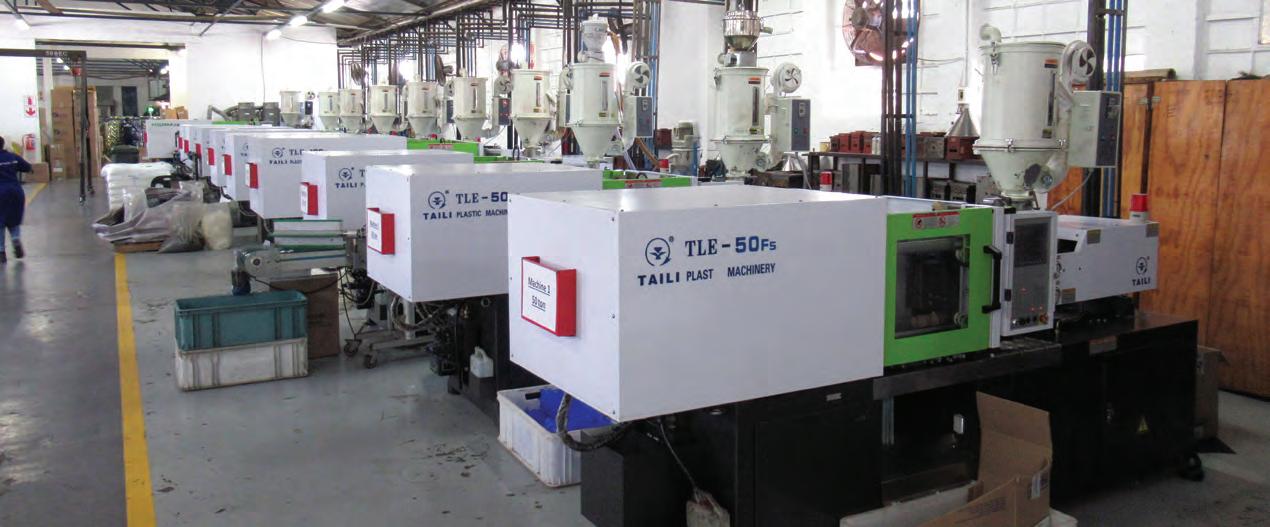
There’s no
twist in the Taili,
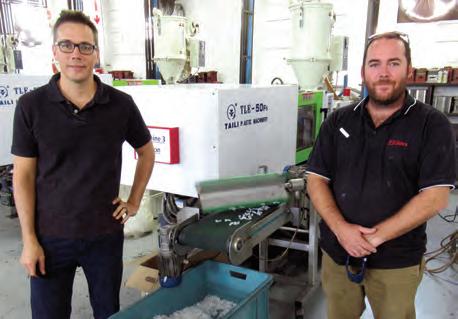
Darren Bezuidenhout, toolroom manager at CAD, with Shane Collier of WD Hearn, the machine technical applications engineer
new machines prove popular
Success at CAD Plastics boosts machine brand
By now skepticism about Chinese injection moulding machine has faded to a distant murmur, although it wasn’t so at fi rst. In the 1980s and 90s most machines from the Far East were treated with much doubt, but then the Taiwanese and after them the Chinese began to supply machines with steadily improving technical abilities and reliability, to the point where they even began to rival the European marques. But each new brand from the Far East, and there have been many, is almost by regulation treated with doubt on fi rst arrival.
And so it has been for Taili, a brand of machines introduced into South Africa by WD Hearn in 2017.
Like virtually all the ex-China machines now available in South Africa, the company (full name Ningbo Tailike Plastic Machinery Co Ltd) does its own metal casting and manufactures all its metal components at its plant in Ningbo in China, possibly by now one of the top global centres for injection moulding technology development. There it operates fi ve workshops. It comes as no surprise that it is fi rst focussing on smaller machine production, with the virtual certainty – as has been the case with the many other Chinesemade machines in SA – that their technology will expand and machine performance will irrevocably improve. That is what the guys over there do: by contrast the only SA-made machines in our industry which have achieved any international success are the bag-makers from Technimac and before that Adron. By contrast, there are hundreds of injection moulding machine brands from China, not to mention other machinery, and all arrive with intensely focussed Chinese personnel who solely committed to machine performance improval.
Among the fi rst converters in South Africa to trial TAILI IMM has been CAD Plastics of Durban, and the need was obvious: They needed smaller machines to produce its range of small components. CAD owner for 27 years, Malcolm Buchanan put one of the machines in, based on an already great working relationship with CNC supplier WD Hearn, then introducing TAILI.
He elected to try one of the machines from the Taili TLE range … and it’s been virtually non-stop Taili since. CAD now operates 13 of the machines, ranging from 50 to 220 tons clamp force.
Buchanan played quite a big part in the Taili roll-out: he suggested that the mould temperature control cards be built into the electrical panel and can control up to 64 zones by the EST control panel (which is possible with Taili’s full range) also protective covers be placed on the hydraulic components. All the TLE range machines at CAD are standard with higher screw speeds creating faster cycle times.
Other proprietary features have been introduced since too, including: • Standard bi-metallic screw and slotted plattens; • Double core pulling and twin air blow; • EST controller system to handle higher screw speeds with high speed data buss to servo drive; • Servo drive software implemented into the system • Visible Machine power usage for Kw/ hour on the control.
According to Myles Crosthwaite of WD Hearn, the success at CAD has been a catalyst that has seen other moulders in KZN opt for the Taili solution, boosting confi dence in Taili and the process has gained further momentum since Brett Shelley, a leading machine control specialist, joined WD Hearn.
www.nb-taili.com
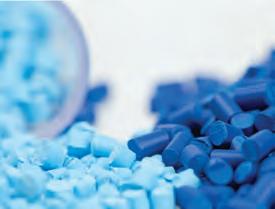
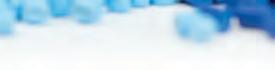
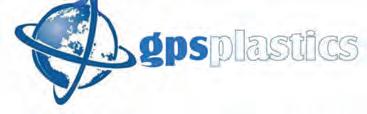
Injection moulding for the medical, transportation, engineering, home appliances & houseware markets Various and vast skill sets, coupled with years of experience in quality and production control, R&D, machine setting, mould designing and procurement. Manufacturing • Injection moulding machines from 100-ton up to 500-ton clamp force • R&D expertise specialising in cradle-to-grave solutions, product design Quality Systems • Effective quality benchmark tool to ensure the precision of all products • Implemented throughout every process in the supply chain Value-Added Services • PAD printing • Product assembly • Re/design consulting • Career development and enhancement
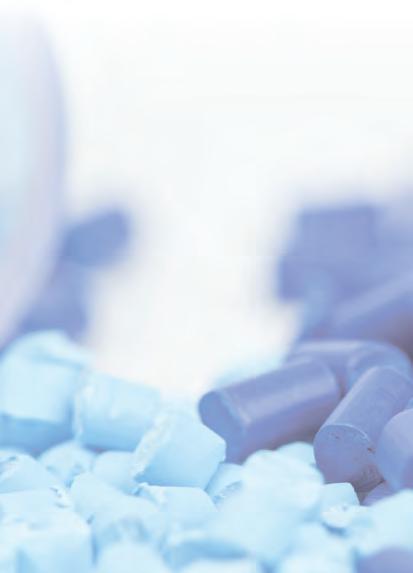
Contact GPS Plastics
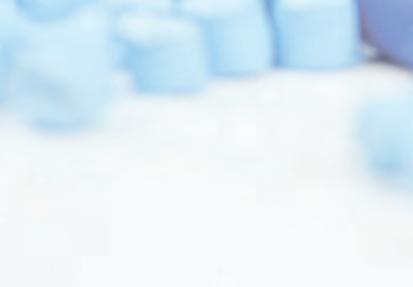
Kevin Govender Tel: 031 700 6900 or email: kevingov@gpsplastics.co.za Diana Govender: 082 997 3205 Preshan Naidoo: 082 768 6114 Email: sales@gpsplastics.co.za
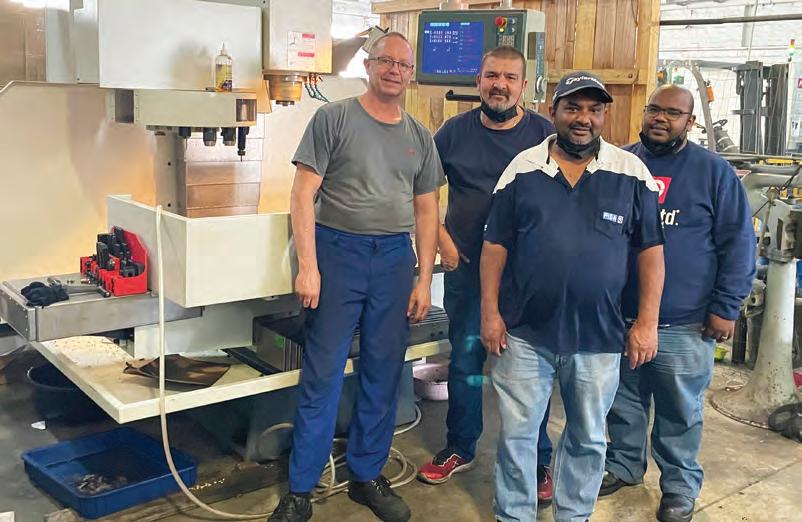
GPS installs own toolroom, now a one-stop shop
Multi-purpose CNC machine gives it new options
GPS Plastics in Durban has installed its own toolroom, giving the KZN injection moulding business considerably more control over its mould manufacturing requirements and closing the loop for it, so to speak.
GPS manufactures a range of technical items as well as domestic appliances and managing director Kevin Govender, a man who’s not scared of a technical challenge, has steadily expanded the range of services it offers in the decade-plus since the company was started in 2006. One of the biggest steps to date was developing its own assembly operation and a number of the products it manufacturers are now fully assembled on site and tested as well as packaged in client brand boxes.
“We are always coming up with new product ideas,” said Govender.
“Installing our own toolroom gives us an advantage in the market. We now have a one-stop-shop. Obviously it gives us far more control over our tools, and it also enables us to amortize the tools more easily as we now exactly what our costs are,” he added.
The main new item in the onsite toolroom is an Akira Seiki KM 150 machining centre, supplied by nearby MJH Machine Tools. This is a multi-purpose CNC machine which can be used for high-precision tool and die making as well as general engineering work.
Govender and his team have been building towards the launch of GPS’s toolroom for a number of years already and, apart from the Akira system, have sourced all the necessary cutting systems to build small to medium sized moulds, with a number of the items being bought on auction. Included in the toolroom are a surface grinder, milling machines and lathes and various other peripherals needed for a standard toolroom as it sets out on this new journey.
Designer/toolmaker Kevin Watson (ex-Jhb) has been appointed to run the facility.
“Some of the moulds are owned by customers, but our goal is to amortize the tool costs as quickly as possible, and we believe this makes us more competitive,” added Govender.
Kevin Watson (tool maker and designer), George Fivaz (technical manager), Kevin Govender (managing director) and Preshan Naidoo (operations manager) at the Pinetown injection moulding business
www.gpsplastics.co.za
New fl oating base for Hope Statue on the Black River


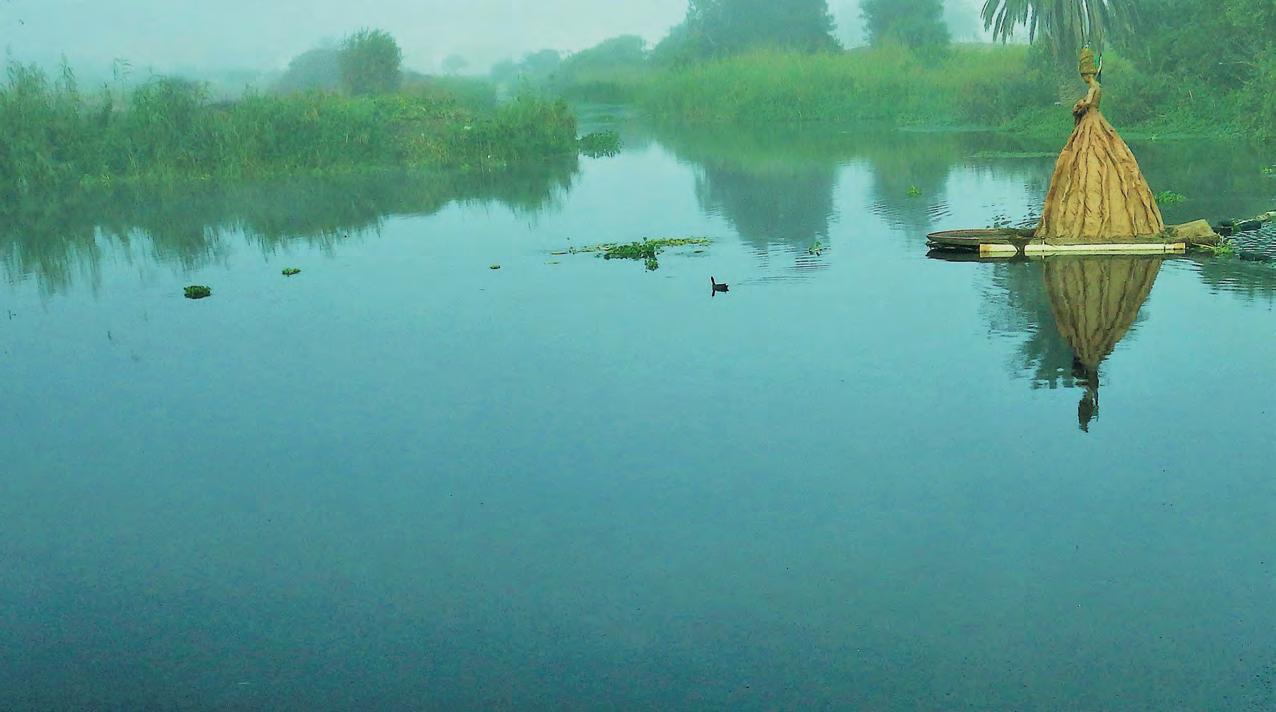
THE HOPE statue placed in the water where the Liesbeeck and Black Rivers converge, has become a much-loved and well-known sight for motorists travelling along the M5 highway in Cape Town near the N2 interchange. The brainchild of Fred du Preez, an art director and self-proclaimed riverman, this symbol of pollution-free rivers and oceans has recently received a brandnew fl oating base made of recycled polystyrene which has been mixed with a special cement aggregate supplied by Envirolite Concrete.
“Polystyrene and other plastics are often the most visible form of plastic pollution in our rivers and waterways due to the fact that they are lightweight and fl oat. The fact that litter that possibly could have ended up in our oceans, have been put to good use to create a new fl oating base for HOPE, makes this whole initiative so much more impactful and poignant,” remarks Du Preez. 400 litres of recycled polystyrene beads (10kg) were collected from the Kraaifontein MRF and used to create the base that measures 2.4m x 2.4m and is 200mm thick. Although it is lightweight, it is strong enough to withstand a load of 500kg. Inside the frame are several 2-litre PET bottles which are used to keep the frame afl oat, as well as compacted polystyrene. This same special polystyrene and cement mixture that was used for the base is widely used throughout South Africa for building and construction projects ranging from low cost housing to designer homes and shopping malls.
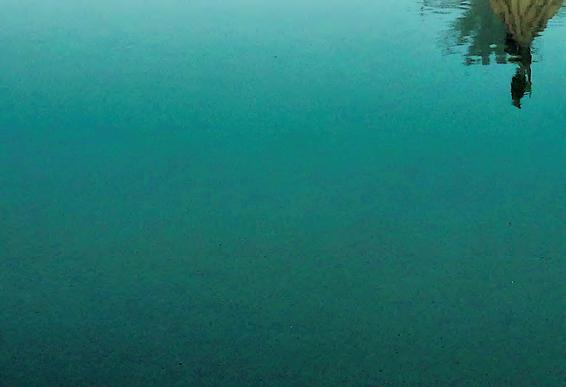


Durban: 031 705 7514Durban: 031 705 7514 Ricky: 079 510 4144 Brandon: 066 234 1702Ricky: 079 510 4144 Brandon: 066 234 1702 ricky@mjhsa.co.za sales@mjhsa.co.zaricky@mjhsa.co.za sales@mjhsa.co.za
JHB sales - Mark Haslam 083 326 0556 mark@sinosia.co.za JHB sales - Mark Haslam 083 326 0556 mark@sinosia.co.za Eastern Cape Sales - Carl Barkhuizen 063 361 7620 carl@mjhsa.co.za Eastern Cape Sales - Carl Barkhuizen 063 361 7620 carl@mjhsa.co.za www.mjhmachinetools.comwww.mjhmachinetools.com

www.evlc.co.za
www.polystyrenesa.co.za
90 90
90 90
JUN / JUL 2021 21
RobotsRobots Durban: 031 705 7514Durban: 031 705 7514 Ricky: 079 510 4144 Brandon: 066 234 1702Ricky: 079 510 4144 Brandon: 066 234 1702 ricky@mjhsa.co.za sales@mjhsa.co.zaricky@mjhsa.co.za sales@mjhsa.co.za
JHB sales - Mark Haslam 083 326 0556 mark@sinosia.co.za JHB sales - Mark Haslam 083 326 0556 mark@sinosia.co.za Eastern Cape Sales - Carl Barkhuizen 063 361 7620 carl@mjhsa.co.za Eastern Cape Sales - Carl Barkhuizen 063 361 7620 carl@mjhsa.co.za www.mjhmachinetools.comwww.mjhmachinetools.com

New use for fi refi ghting tank – Niko White and the Principle Plastics production team in Port Elizabeth have devised a system to circulate water from the large water tank to cool their injection moulds; (right) White with one of the resulting products, an exterior part for one of the new locally produced models currently in production
Principle chills out with new solution
Saves both water and energy costs
PRINCIPLE Plastics in Port Elizabeth has come up with a novel cooling solution for its fl eet of injection moulding machines – by circulating water from its fi refi ghting water storage tanks via a Plate Heat Exchanger system, to keep the moulding machines oil at optimum temperatures.
The solution saves both water and energy costs.
Principle is running a range of mainly polyolefi n materials to manufacture automotive components with the need to tightly control the moulding machines oil temperatures at around 43°C (+- 1°C) and opted to not use a standard solution (the original cooling towers used in plastic converting tended to lose considerable quantities of water to evaporation, amounting to around 400 litres per hour in peak summer conditions – this is now reduced to zero).
The Markman Industrial -based business had been obligated to install two x 400 000-litre water tanks to meet fi refi ghting requirements and the solution devised by Principle MD, Niko White, and the Principle team involved piping the water from the tank to a central pump and then circulating the water to the machines and back to the tanks.
In winter the temperature in the storage tanks could drop to around 6°C, while in summer it can get up to 30°C. As such, each machine is fi tted with a self-regulating 24V valve that opens and closes automatically according to the requirements to maintain oil temps at the optimal 43°C.
White, who is closely involved in devising control technology for production on an on-going basis, believes the advantage of the system is that it makes logical use of the stored water, which would otherwise be a fi xed cost only used in the event of fi re.
“So, we are not using the water at all as it remains in a closed water tight system. We are merely using the ‘cold’ in the water to our advantage. The tanks cool down naturally over the weekends and are ready to go come Monday mornings for startup!
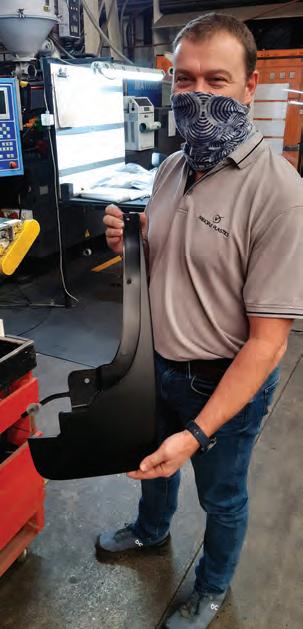
Mould Base moves into own warehouse
Mould Base, the injection moulding machine and accessory supplier, has moved into its own warehouse in Mount Edgecomb, KZN. Located close to the N2, the 1 500m² space is a secure and clean storage area where Dave Moore and his team are keeping a few Yizumi machines in stock, along with spares and other equipment. Part of the logic is that since it’s taking far longer to ship machines out from the Far East (doubled from three months lead time prior to Covid to over six months now), holding machines in stock is the best alternative. The machines being stored have proved popular and delivery to anywhere around the country can be done in days. Dave and technician Arrie Louwrens are feeling quite chuffed about Mould Base’s new situation
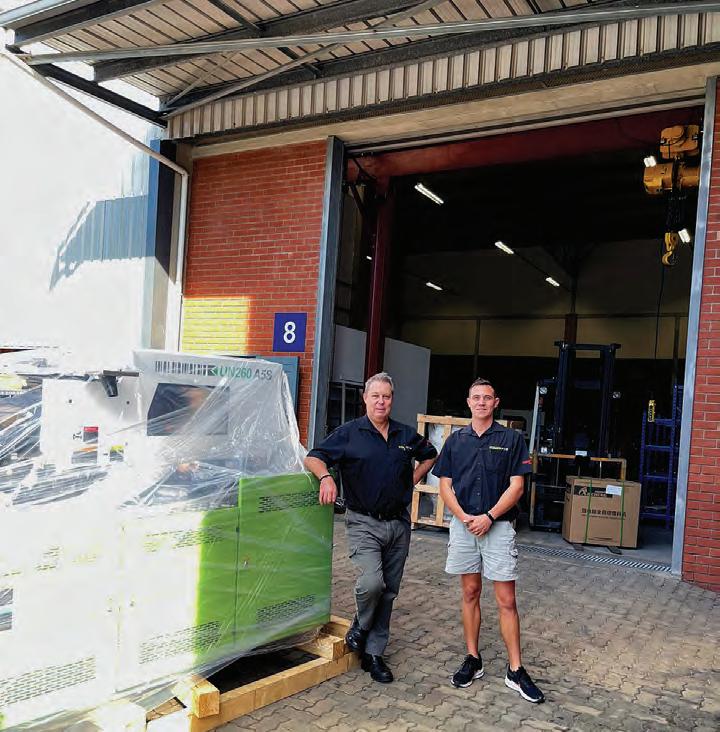
JUN / JUL 2021 23
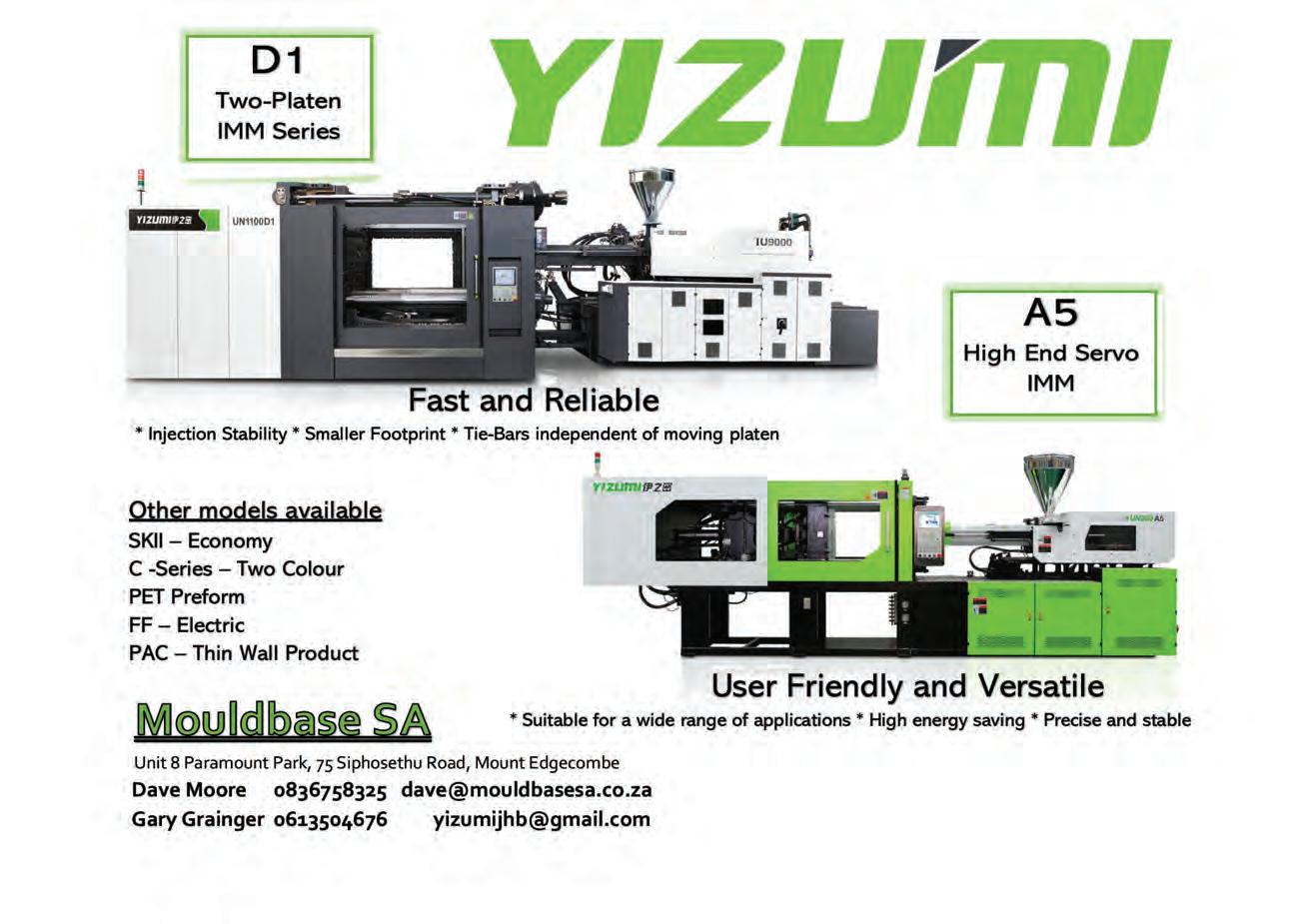