4 minute read
Titanium Forging Process Ready to Embrace ‘Innovations Engineered for Era of Delivery’
By Michael C. Gabriele
As the keynote speaker at the March 2022 AeroMat conference held in Pasadena, CA, Dr. Markus Heinimann, the vice president of technology and quality for the Engineered Structures group of Howmet Aerospace, described his observations on “Innovations Engineered for the Era of Delivery.” Interviewed in May, Heinimann underlined the challenges for this “Era of Delivery” in the near term for the aerospace industry, citing the many disruptions in the global supply chain and the ongoing efforts for airlines to recover from the severe business downturn from Covid-19.
Despite these concerns, Heinimann expressed confidence that, for engineered structures such as titanium forgings, Howmet and other companies will continue to make steady progress on manufacturing technology by focusing on front-end process management and research and development investments to reduce costs and enhance production reliability.
In his keynote address, Heinimann noted that, as of this year, aerospace industry backlogs are close to pre-pandemic levels, but parts of the industry supply chain are considerably weaker than 2019. It’s no secret that the global commercial aerospace industry collapsed during the pandemic years of 2020 and 2021, with revenues, air travel and jet deliveries down significantly. Many business analysts, including those quoted in TITANIUM TODAY’s previous features, anticipated that it would take at least until the 2023/2024 time frame for the aerospace industry to recover.
However, many indications are that the commercial aerospace recovery has accelerated faster than expected, but there’s possible turbulence lurking in the months ahead. The New York Times, in its May 16 edition reported that, while business travel is showing positive signs and gaining altitude, “Russia’s war in Ukraine,

Dr. Markus Heinimann
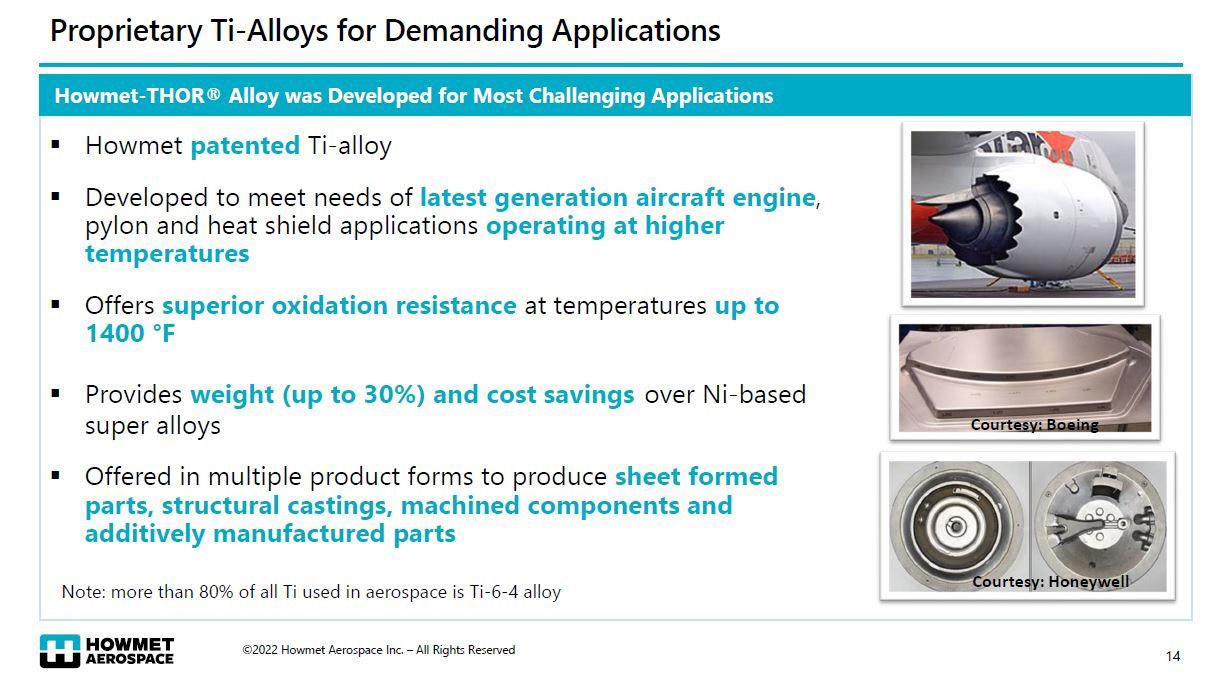

China’s zero-Covid lockdown, and the unpredictable path of the pandemic all threaten to stifle a widespread return to 2019 levels from happening anytime soon.”
“The collapse of the commercial aerospace industry (during the height of the pandemic) had a major impact on our company, but we managed to stay profitable,” Heinimann said. “Our biggest concern right now is to keep pace with the recovery. It’s not that easy.” He explained that, because aerospace manufacturing isn’t highly automated, it takes time to hire and train skilled workers on complex equipment like forging presses, machine tools and melt furnaces.
The focus for process management and research and development in the months ahead will involve removing costs from manufacturing systems while further enhancing quality. Part of that effort involves designing and producing parts from next-generation titanium alloys to achieve greater strength as well as resistance to in-service oxidation and higher temperature. One example is Howmet’s “THOR©” alloy, unveiled in July 2018(under the Arconic name plate). According to a company press release, the patented THOR© alloy achieves up to a 30-percent weight savings “compared with nickel-based superalloys for higher temperature applications in aero engines and adjacent structures— driving cost savings and fuel efficiency for customers.
Howmet’s THOR© alloy offers three times superior oxidation resistance, which enables it to operate at service temperatures higher than any other conventional titanium alloy available on the market, according to Heinimann. The company has completed successful development projects with commercial aerospace and defense customers, including a U.S. Air Force Research Laboratory project with partners Boeing and Honeywell.”
In order to keep pace and prepare for existing production programs and new near-term business opportunities, Heinimann said that the company’s recent thrust for capital investment has been to upgrade existing forging equipment rather than purchase new equipment. Howmet operates 50,000-ton, 33,000-ton and 15,000-ton forging presses at its Cleveland facility. The upgrades involved rebuilding structural components, valves, designing precision tool and die sets, and installing new control systems, all with the emphasis on improving quality and consistency in the forging process.
New generations of software simulation tools allows Howmet and other companies to completely simulate the manufacturing process as well as track costs. The state of the art during the next five years will be achieving incremental improvements that result in a more robust, reliable and uniform forging of titanium parts. Howmet melts ingots and produces its own titanium billets for its forging, extrusion and rolling mill operations.