7 minute read
Enhanced Titanium Tubing Addresses Demands For New Designs in Heat Exchanger Equipment
Next Article
By Wendy McGowan and Craig Thomas
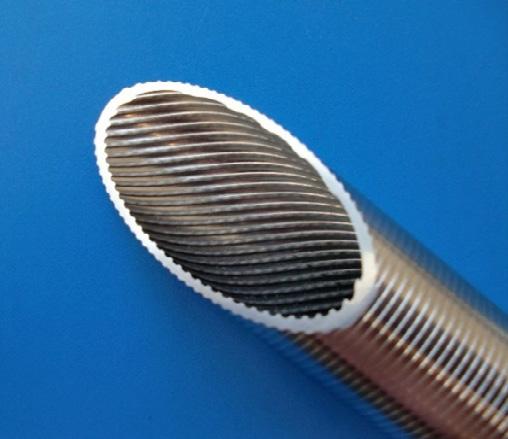
Titanium Fin Tubing
Demand has emerged in many industries to not only provide innovative solutions for new heat exchanger equipment design improvements, but also to replace aged equipment with retrofit solutions that provide improved performance. Enhanced tubing surfaces have been developed as one solution to increase overall plant efficiencies.
An integrally formed low-fin surface in titanium was first developed by High Performance Tube in 1974. The first set of installations took place at the Bayway Refinery in New Jersey, which was owned and operated by Exxon at the time. Brackish water from the Arthur Kill River was quickly destroying copper/nickel (Cu-Ni) tube bundles from the inside of the tubes and at the tube to tubesheet interface.
Over the years, it was discovered that titanium tubes and titanium clad tube sheets would solve the corrosion issue, but these retrofits would become expensive if the heat exchangers had to be completely resized with new shells, new infrastructure, and piping layouts. It also was discovered that retrofitting with finned titanium tubes greatly reduced the installation cost because the added surface area allowed for installing new bundles with higher or equal capacity into existing shells.
The extended fin surface on the outside of the titanium tubing more than compensated for the loss in metal thermal conductivity and allowed for more future capacity. In addition, some of the existing CuNi or admiralty brass bundles were already installed as low-fin type. Replacing these bundles with finned titanium became imperative in order to maintain existing capacity.
Since Neotiss’ acquisition of High Performance Tube in 2008, the range of fin tube products available in titanium has expanded, and with that also the number of different industry applications. One example is the development of both external low-fin surfaces combined with a spirally grooved internal fin surface. This resulting dual enhanced titanium tube further improves heat transfer efficiency by increasing the shell side surface area and the tube-side turbulence. These tubes are commonly used in large refrigerant loop processes serving the commercial air conditioning and industrial process refrigeration markets.
As explained in an article penned by Charles Young, business development manager/metallurgist for Tricor Metals, which was published in the first-quarter edition of TITANIUM TODAY, understanding the elements of designing an effective, efficient heat transfer system is the key to cost-effective manufacturing of most chemicals today. This understanding includes not only knowledge of the fluid’s physical characteristics and chemical makeup, but also flow rates, system temperatures and pressures and pressure drop allowed.
“When the corrosivity of the chemicals make it necessary to use higher alloys (corrosion resistant alloys or CRAs), it is absolutely essential that the system be designed for maximum efficiency to ensure that the overall cost of the heat transfer is minimized,” Young wrote. “Titanium alloys are used extensively in the chemical processing industry in various types of heat exchangers. The relative stability of the cost of titanium and its availability are two factors that have resulted in increased use in heat exchangers in the chemical processing industry. All aspects of the fluid chemistry for a process must be known to ensure a long service life.”
Another common application for titanium fin tube is in liquid natural gas (LNG) and ethylene plants, where seawater is used to reject heat during the compression and condensation of hydrocarbon gases. It’s common in such applications for the fin tube to reduce the total number of heat exchangers required by 30 to 50 percent for the same required heat duty. The value add of this technology is then realized by the client in lower capital cost, and plot space.
While the above types of fin tube are very effective in hydrocarbon and refrigeration processes, they are not appropriate for the largest application of titanium welded tubing, steam surface condensers. To address this gap, Neotiss developed its “Helix Tube” product line—a recent innovation in enhanced tube surface design. In a surface condenser, steam from the turbine is exhausted into the condenser where it is cooled and recycled back through the process.
A typical power plant surface condenser has thousands of tubes. Cooling water, which in the case of titanium will be sea or brackish water, runs through the inside of the tubes and cools the steam on the outside. Steam condensation does not benefit from traditional low fin designs, because the heat transfer coefficient is already very high, and the added metal and fabrication cost of the fins is not needed on the shell-side. There is also an adverse effect of condensate retention inside the closely spaced fins, making the heat exchanger less efficient.
Because of titanium’s superior corrosion resistance, the need to design titanium heat exchanger tubes with a “corrosion allowance,” typical for many standard tubing materials, is not required. For this reason, titanium condenser tubes are already quite thin, typically 0.020 inches. Condenser tubes as thin as 0.016 inches have even been specified. The thinner the tube wall, the lower the metal resistance factor that contributes to the overall heat transfer resistance and the higher the overall thermal efficiency.
Even though market trends have pushed equipment designers and fabricators to use thinner and thinner tubes, there are design and handling challenges and, eventually, a point of diminishing returns. Efforts have been made to coat the outside of the tubes with a nano film that increases the condensation of the steam. This is done by creating a hydrophobic surface where the water will not adhere, and droplets easily bead and fall. However, these coatings have been shown to wear over time.
Given that the titanium tube is as thin as it can practicably be and that improvements on the outside have thus far not been feasible, the next greatest resistance to heat transfer in a condenser is the water side (inside) of the tube. This is how the idea for the Neotiss Helix tube design was conceived. The helix design is a spiral corrugation created by cold deformation and serves to generate cooling water turbulences. This turbulent flow increases the pressure drop while reducing the inside boundary layer thermal resistance, and therefore increases the overall heat transfer. The spiral indentation on the outer diameter of the tube slightly increases the surface area in contact with the steam condensation.
The Neotiss Helix titanium tube was developed through intensive research and trials to find the best parameters to optimize heat transfer performance while minimizing pressure drop. Trials performed in Neotiss’ laboratory have demonstrated that heat transfer improvements over 40 percent versus smooth tubes can be achieved.
One of the key parameters in the helix design is the adherence to dimensional tolerances compared to a smooth tube. When designing a condenser using this helix tube, the engineer can use the same diameter and wall thickness tolerances as those used for smooth tubes. This is especially important on the ends where the tube is attached to the tube sheets. To allow for standard tube to tube sheet joints, the ends of the tubes are left plain. This can also be useful for condenser retrofits (also known as “retubes”). When condenser tubes of other materials begin to fail, rather than replacing the entire condenser, some utilities will opt to remove the old tubes and replace them with new tubes. This can be accomplished with Neotiss Helix tubes since the outside dimensional tolerances will meet current industry standards.
Steam surface condenser tubes are typically very long, in the range of 40 feet or more. To support the tubes, support plates are spaced at calculated intervals along the length of the tube bundle. The distance between the support plates in a titanium condenser is usually shorter to prevent excessive vibration due to titanium’s lower modulus compared to other common materials of construction. To address this point for Neotiss Helix tubes, a laboratory study was conducted and has shown that the natural frequency of the Neotiss Helix tube is slightly less than that of a similar size plain tube.
Another factor to consider is how and when to clean an enhanced tube surface design used in a condenser. Most tube materials are subject to fouling under normal operating conditions. Neotiss performed laboratory tests to show that Neotiss Helix tubes can be cleaned as easily as smooth-bore tubes. Inner grooved tubes have also been used in other industries successfully, including in brackish water and seawater.