10 minute read
ALL ROADS LEAD TO
from TCT Europe 30.6
by TCT Magazine
Next Article
Senior Content Producer Sam Davies goes Through the Doors at Fast Radius.
On a bright Wednesday morning, an Uber powers its way deep into Chicago’s West Loop. This dynamic district is renowned as a dining and nightlife hotspot with a vintage aesthetic that has even attracted McDonald's to base its HQ here. En route, we pass Michelin-starred restaurants, high-end bars, and the iconic Union Station. A mural splashed on a nearby wall proffers that all roads lead back to the Loop.
This morning, a Honda Accord driven by Shantis is on one such road as it pulls up along a side street: “Have a nice day.”
We are four minutes early. Enough time to be convinced by an anxious mind that we’re in the wrong place. That I’m greeted by Daniel Baker and Bobby Bott of Fast Radius as we step into the lobby doesn’t quell those fears. This is just an office, not the factory environment to be expected of a company running two dozen 3D printing systems at this location alone. It looks like the type of place that would be home to Glassdoor.com or Harpo Studios. Because, until 2017, it was.
Then, a company founded in Atlanta but moved to Chicago, took up space on the ground level and basement, turning both floors into microfactories powered by additive manufacturing (AM) technology. As we sit down on three sofas configured around a coffee table, I still can’t see them.
Bott talks first. That’s the first note scribbled on the pad as the recorder is set equidistant between the pair. He is the EVP of Manufacturing Supply Chain at Fast Radius, while Baker leads Strategy and Ops for Additive Manufacturing. “I had this desire to be more innovative and build,” Bott says of his attraction to the role at Fast Radius, which he took up five years ago.
“A college friend of mine was one of the first engineers at the company,” Baker offers. “He showed me his base in Atlanta, the vision that was coming. Two weeks after that, packed my car, drove across the country and I was moving back to Atlanta.”
“It’s about growing manufacturing and changing into the more digital, leadingedge way. And additive is a great way of showing that,” Bott adds.
Behind the sofa, there is much evidence of the value AM is bringing to Fast Radius and its customers. A topology-optimised chassis sits on the floor, while a robotic arm featuring grippers that are flexible in all directions printed with Carbon Digital Light Synthesis (DLS), joints printed with HP Multi Jet Fusion (MJF) and assembly components printed in Stratasys Fused Deposition Modeling, sits on the windowsill.
In pride of place is the REV1X baseball glove additively manufactured with DLS for Rawlings. The glove features stiffness and softness where required, is being sold in sporting goods stores around the US, and is being produced in Fast Radius’ DLS microfactory as we speak. Next to the glove is a completely different product made with a completely different process, though Fast Radius is no less pleased with the outcome. This ground support tooling is one of around 100 unique tools to be additively manufactured by Fast Radius for Airbus with MJF. The tool in Bott’s hand is one that, although Airbus doesn’t know when it will next be required, can be downloaded from a digital inventory, produced, and shipped for the aviation giant to deploy at the point of need. Via this approach, lead times are reduced from weeks and months to days. One step along and Baker is passing over a lowvolume brake component additively manufactured for an electric vehicle on behalf of an unnamed customer. The part has since gone through further iterations and is being manufactured tens of thousands of times per year.
“Our mission is to make new things possible,” Bott says. “We’re a purposedriven company, it’s not just the things we make, it’s the things we make possible. We’re making the world safer with medical devices, more efficient with EV vehicles, more fun with consumer goods. The team dials into how we could do that, that’s what
drives us each day, to advance manufacturing and put new products out into the world. Our motivation is to give engineers, our customers, the ability to design, make and move what they need, when and where they need it.”
“You give people the ability to iterate and to design quickly, which is awesome, but you’re also able to augment existing parts,” Baker adds. “You can take a part that’s been produced via legacy technology, and you can either add features or dial in specifics that you truly need on that part for performance improvement. That’s a huge value add.”
As the brake component is put back in place by the window, we head towards the back of the office space where, I’m told, the DLS microfactory is situated. Behind this door, there are several of the applications already discussed in production. But these products haven’t always been building layer by layer back here. Before this, they were merely a series of data inputs being typed into Fast Radius’ front-end software.
Accessible via the company’s website, registered users can upload part designs, have their manufacturability assessed and then survey the cost it will take to produce the part(s) via Fast Radius. Users can run these checks by selecting between the various additive and subtractive manufacturing processes Fast Radius offers, as well as the material they wish to build their parts with. Once the process and material have been selected, a series of automated checks are populated. In terms of manufacturability, the software takes a red, yellow, green stoplight approach, with red covering major design issues that need to be resolved, yellow indicating non-critical issues, and green signalling all is okay to proceed. Should there be a red flag, users won’t see a quote because Fast Radius won’t produce it.
The software has taken this knowledge from a ‘data lake’ developed from the hundreds of thousands of parts that have been printed with Fast Radius’ suite of AM technologies.
“We are reducing the time for [the user] to analyse parts, reducing the resources and accelerating the speed at which they can determine this part is good for additive, which is a huge part of the battle,” Dan Healy, Head of Business Development at Fast Radius, says as a demo part goes through this process. “In a normal discussion, [we] will spend two to three months, probably four to five conversations, with a new enterprise or company to get to the point we’re on right now in five to ten minutes.”
Through this portal, users can upload dozens of iterations of the same part, search them by name, and resume unfinished evaluations. When a design file has been selected, users can view the part in a 3D space, rotate and spin it around, while also looking at the part in an X-ray view to visualise the internal features. Should there be any reasons for one of the three stoplight colours to be highlighted, there will be some blurb pertaining to three questions to inform the user of the next step. This covers what the issue is, what the impact will be, and how the user can fix it. There is also an option to contact Fast Radius should the user wish to get more information and support. Moving forward, Fast Radius is exploring the potential of providing a suggested material based on the criteria outlined by the user. It is a platform that evolves all the time. The motivation of this portal and all of its features is to ‘take all the knowledge of an expert engineer’ and put it ‘at the fingertips of everyone that uses our platform.’
“With AM, there’s a perception still that you upload a model, push a button and you go,” Healy says. “Additive, as with any other technology, requires a level of expertise to get parts to production and to be able to do that at scale and do it repeatedly.”
In the Carbon DLS microfactory, where ten machines stand back-to-back, Bott is reiterating that point as we come across an M2 platform called Montgomery. All Fast Radius DLS machines have been given names. The M1s are named after international cities, the M2s after domestic cities, and the L1s after fictional cities. Inside Montgomery are several trailer-two connector caps being manufactured for Ford Super Duty trucks to protect electrical connectors from harsh environmental exposure. The application was developed with Aptiv and put into manufacture in the Chicago West Loop facility where hundreds of thousands of the parts have so far been produced. It is the first Aptiv
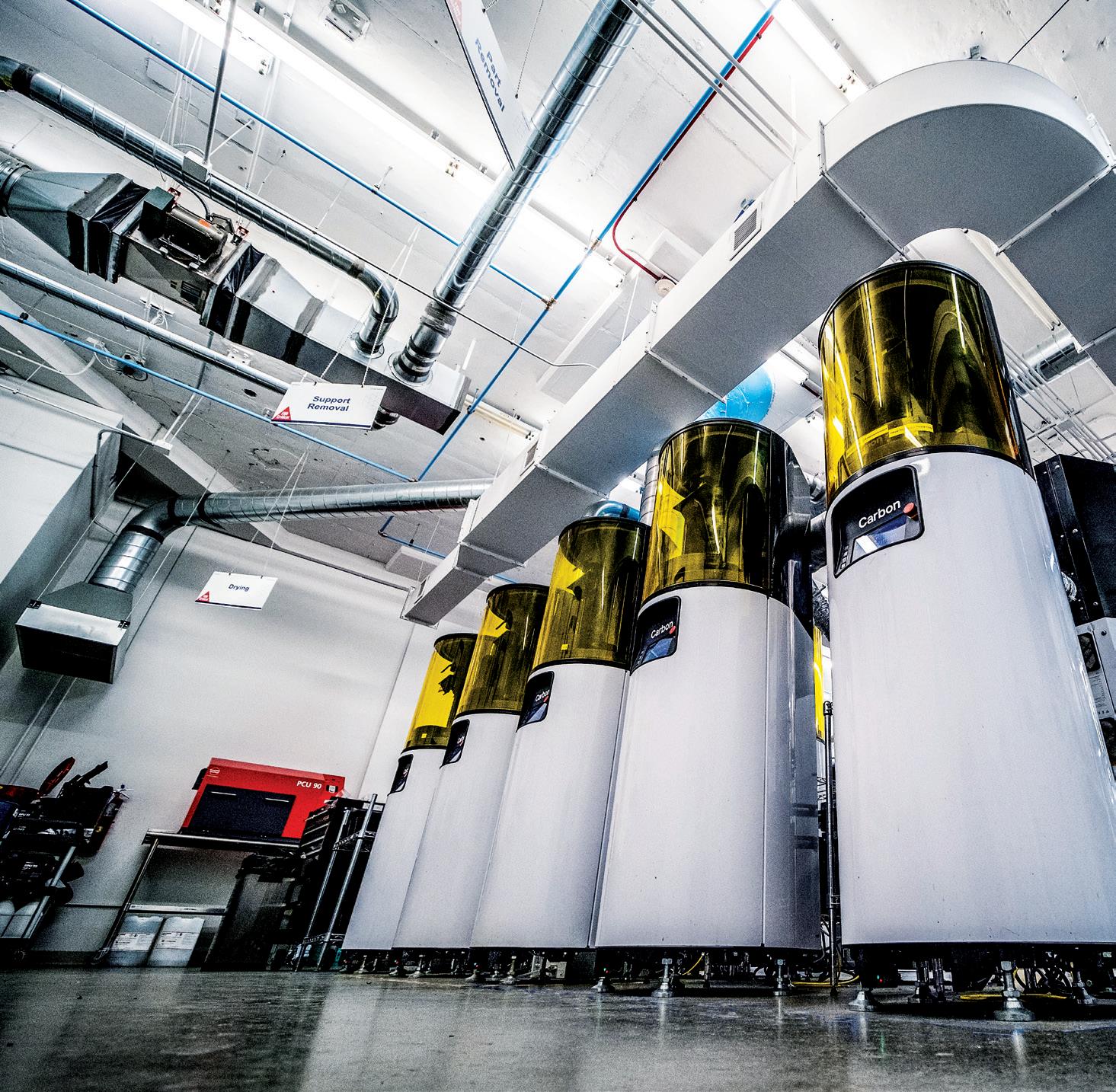
SHOWN:
INSIDE FAST RADIUS’ WEST LOOP CARBON DLS MICROFACTORY “Our mission is to make new things possible.”
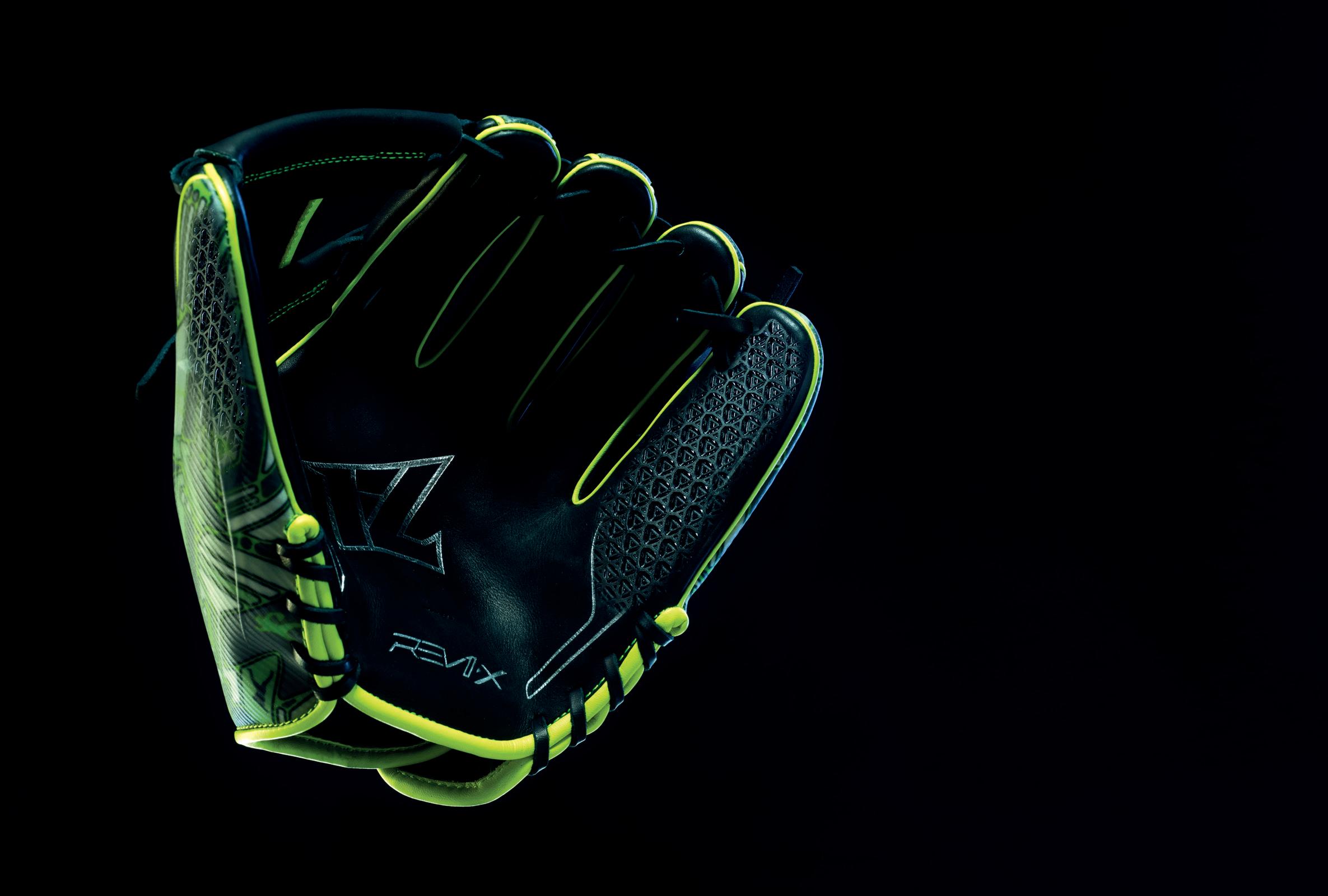
automotive application to be manufactured with polymer 3D printing and is delivering time-to-market reductions of around 20 weeks. Fast Radius is also meeting USCAR-2 validation and ISO 9000 certification in the production of the connector cap while making good use of its virtual warehouse.
The print job inside Montgomery is about halfway finished. There are several connector caps on the build plate, but each with a slightly different orientation. This, along with such things as the temperature and humidity of the microfactory and how the parts are fixtured in the curing ovens, are just some of the considerations Fast Radius has to make to manufacture parts repeatably and reliably.
“As we go to qualify [the Aptiv parts], there are a few features that are critical,” Baker says of the varying orientations. “It’s the stop lock on the side of this piece. We have to orient those in areas on the platform that have the highest level of accuracy. And as you imagine, as this light is stretching from a projector, you get a little bit of pixel stretch. So, we oriented those critical features in zones where they would be consistent time over time over time.”
Next door to Montgomery, Newark is just about ready to have a single Rawlings baseball glove removed from its build plate. This is where the accompanying equipment, from support removal areas, wet blast systems, finishing stations, final wash stations and four thermal bake ovens will come into play. As the parts make their way through this workflow, they go from being cool acts of science to end-use manufactured parts that can be installed on trucks and sold in sporting goods stores.
Directly below the DLS space is a similar footprint occupied by around ten Multi Jet Fusion printers, including a single colour system, two 5200s and about half a dozen 4200s. In this room, it is noticeably cooler than the DLS microfactory, with temperature an important consideration. By the door, there is a tray of real-world applications used to demonstrate the capability of the technology, including Airbus ground support tools and a fixture that holds the Rawlings baseball glove in place during curing. Beyond these applications are the post-processing stations, with several build units queueing up awaiting their turn to move through the blasting, smoothing and /or dyeing steps before being shipped.
The MJF microfactory, like the DLS microfactory above it and the FDM facility in Louisville, has been purpose-built to six sigma standards and designed specific to the processes that yield the parts. Throughout the facility, there is signage for every step of the workflow, coloured bins, tablets, and monitors displaying job scheduling and the progress of prints. When parts are sat ready to go into post-processing, operators can scan barcodes to pull up manufacturing process instructions that will outline what specific details or unique operations need to be carried out. Both microfactories also share the same inspection space, which is certified to aerospace standards.
As we head back up to the lobby, the conversation turns to IMTS, being held in Chicago that week. Bott walked the floor yesterday, Baker goes tomorrow, and the several empty chairs in the office suggest there are Fast Radius staff present as we return to the lounge area. For the Fast Radius team, it has afforded them an opportunity, right on their doorstep, to cast an eye on new tech developments, assess the latest applications, and conclude that what is currently going on in the back and the basement forms part of a wider trend. The feeling is that all roads are leading to production.
“I think additive has a long-standing of rapid prototyping. That tide has turned,” Bott finishes. “We believe it’s turned because we see it every day. What I saw [at IMTS], is that the printer manufacturers, materials, post-processing, and even the business models of support like ours, are trending towards production. It was encouraging to focus on quality, reliability, repeatability, end-use applications at scale. That has been the trend for the last couple of years, and we’re starting to see the fruits of that labour.”
SHOWN:
RAWLINGS REV1X BASEBALL GLOVE