12 minute read
B.C., Japan Renew Energy, Minerals Partnership
Next Article
The Province of British Columbia and the Japan Organization for Metals and Energy Security (JOGMEC) have signed a renewed and strengthened memorandum of understanding (MOU) to explore mutually beneficial solutions to enhance export opportunities and help unlock new sources of energy, such as hydrogen.
“Japan is as a vital market for British Columbian businesses and a key pillar in our long-term economic success that will create jobs and benefit all British Columbians,” said Premier David Eby. “Today marks the renewal of a partnership between British Columbia and Japan that will bolster energy security and leverage B.C.’s status as a cleanenergy powerhouse to help us move toward the clean-energy solutions of the future.”
The renewed MOU builds on a long-standing partnership between JOGMEC and British Columbia. It will foster greater collaboration between the two parties on crucial issues related to energy and environmental sustainability.
“We value the strong relationship with JOGMEC that has contributed to positive developments in our energy and mining sectors, supporting good, well-paying jobs for British Columbians,” said Josie Osborne, B.C. Minister of Energy, Mines and Low Carbon Innovation. “Japan is a critically important export market for our energy and mineral products, and this renewed memorandum of understanding shows our commitment to further strengthening this trading relationship and advancing lowcarbon fuels, like hydrogen.”
The MOU is intended to strengthen collaboration between JOGMEC and the Province in three key areas:
• deployment and use of hydrogen as a low-carbon fuel;

• export of energy and minerals, including critical minerals; and
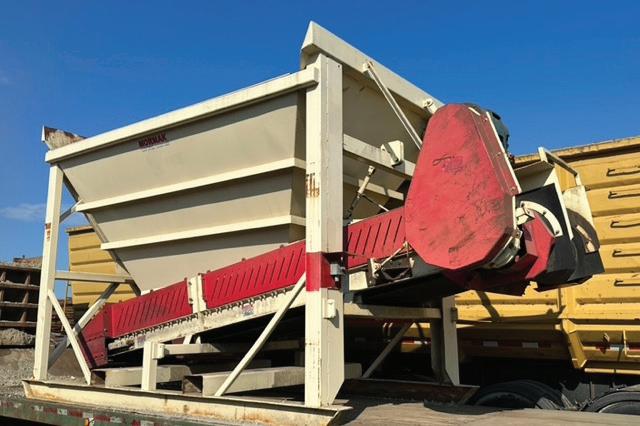
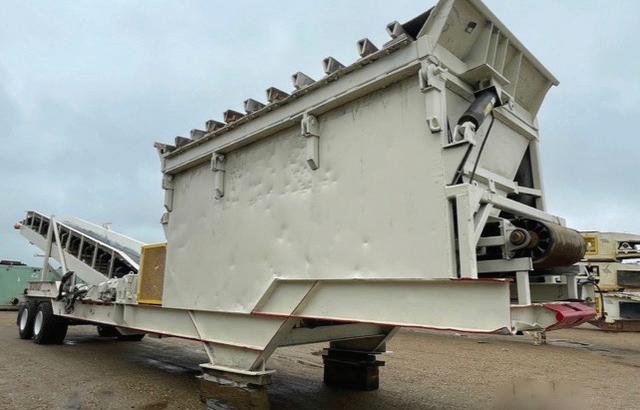
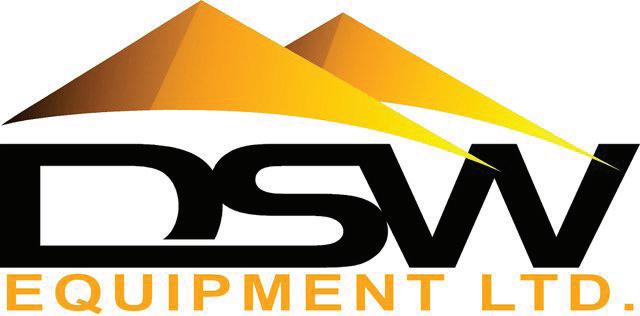
• carbon dioxide capture, utilization and storage (CCUS) technology.
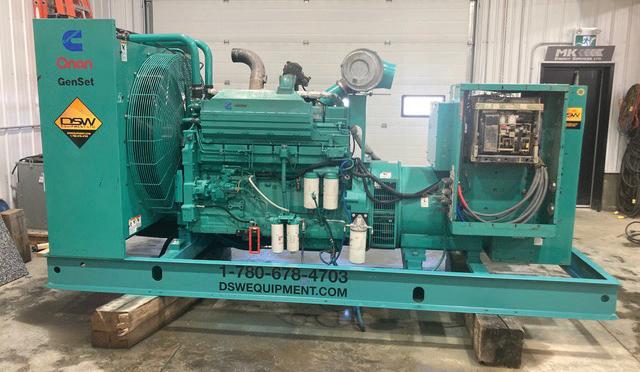
The MOU embraces JOGMEC’s expanded mandate, which includes equity investment for the production and storage of hydrogen and ammonia, and carbon dioxide capture and storage. The inclusion of mineral resources reflects the important trade relationship that exists between Japan and B.C.

“Transitioning and finding more low-carbon solutions are key to a cleaner, more sustainable future,” stated Brenda Bailey, B.C. Minister of Jobs, Economic Development and Innovation. “Renewing this agreement with JOGMEC reinforces our commitment to finding innovative solutions to solve global industry chal- lenges. We look forward to working with our international partners to strengthen our supply chains, support more well-paid jobs and build a stronger, greener economy for generations to come.”
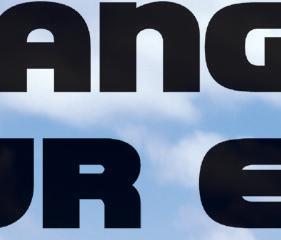
JOGMEC sent the following statement about the MOU renewal: “JOGMEC sees B.C. as an important partner and welcomes the renewal of the MOU. Japan and B.C. have had a long relationship across the Pacific Ocean. Through the MOU, JOGMEC will strengthen the bilateral relationship with B.C., and secure a stable and affordable supply of natural resources and energy to Japan, as well as achieve carbon neutrality.”
Both parties are collaborating on a detailed action plan to follow the MOU to help guide the work required during the term of the agreement.
Quick Facts:
• JOGMEC is a Japanese incorporated administrative agency, which was formed in 2004 after the merger of Japan National Oil Corporation and Metal Mining Agency of Japan.
• JOGMEC reports to the Japanese Ministry of Economy, Trade and Industry (METI).
• JOGMEC’s purpose is to secure a stable supply of natural resources and energy for Japan, and it provides the Japanese private sector with financial and technical assistance to secure natural resources and energy for Japan.
• The first MOU between JOGMEC and the Prov- ince was signed in 2012, with extensions in 2013, 2016 and 2019.
• The initial focus of the
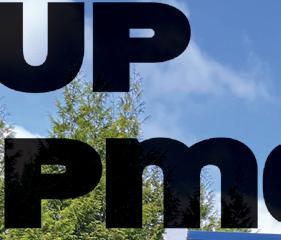

MOU was on natural gas, and focus shifted more toward development of clean energy and critical minerals starting in 2019. SP
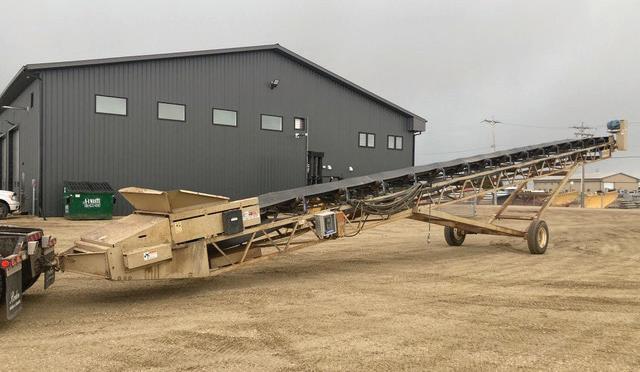
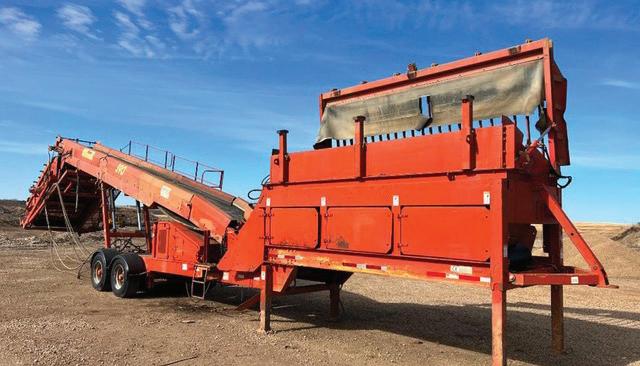
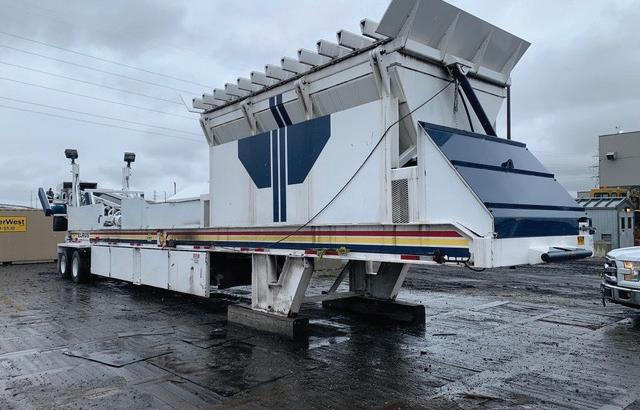
Source: Gov.bc.ca
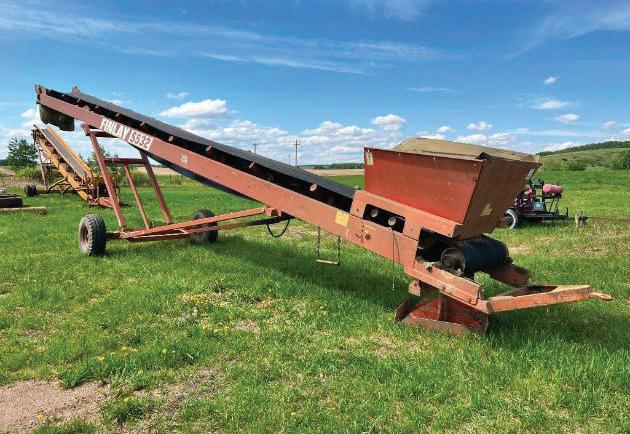

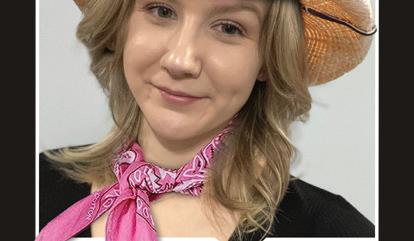
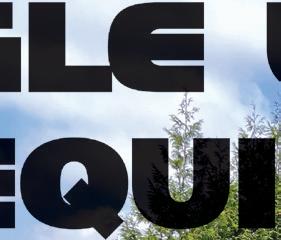
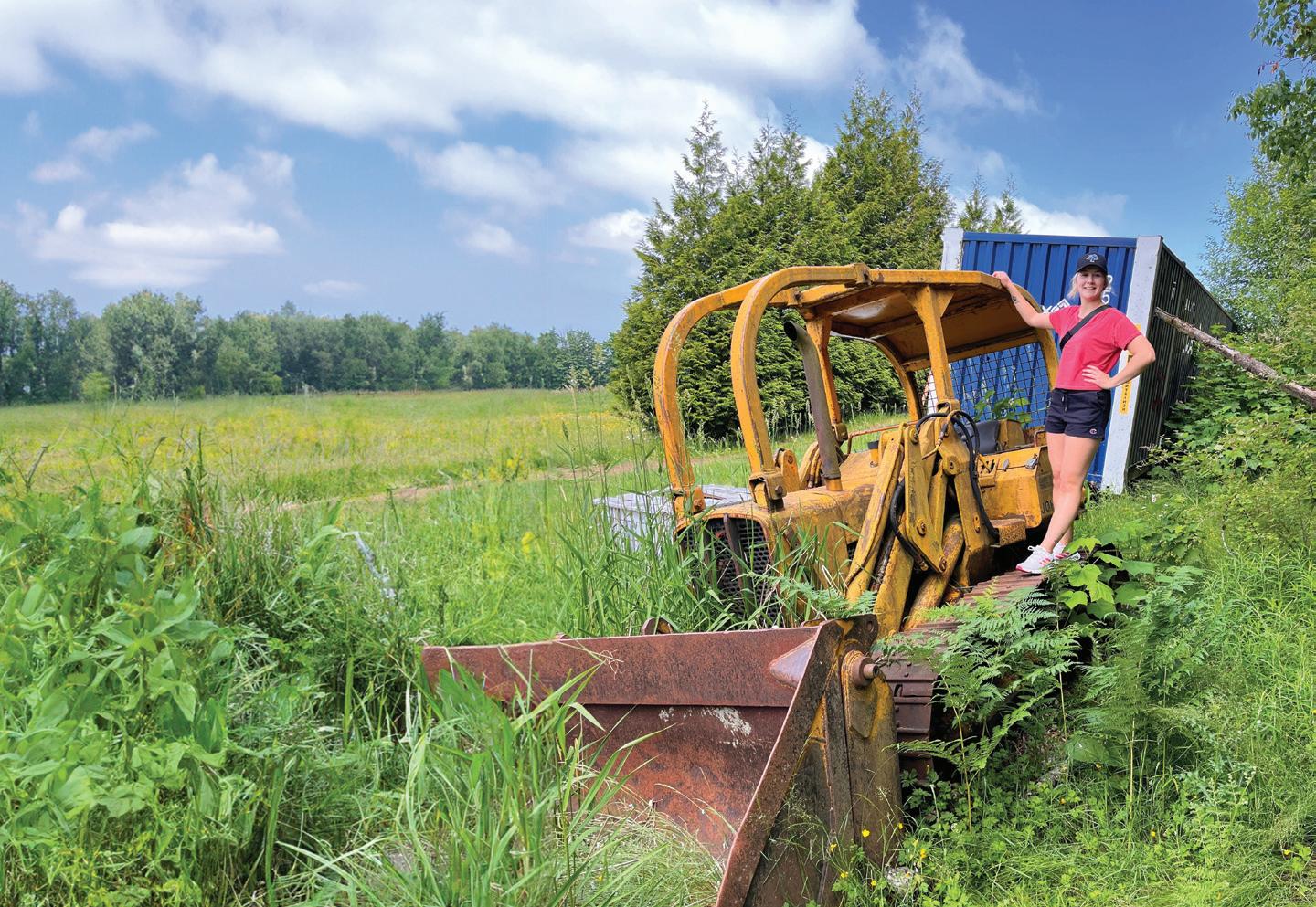
Making Connections
When my dad, Dennis passed in 2019, he left us with quite a collection of old 8mm films and several thousand slides. Brother Barry had them in his storage and asked us brothers if we wanted them. I spoke up and said I could probably find a use for them.
As I was not a computer expert, I went looking for some help. I had been using a local tech company, but they weren’t doing the job. I went to London Drugs and asked them, they gave me a number of a guy who worked for “Apple Support” and we connected.
Dad had some of his 8mm stuff transferred to digital to make a one hour and 45 minute video called “The Day At The Farm.” This video had old 8mm stuff of the family farm from the early 1940s taken by my grandmother Barbara. As near as I can tell, Dad got his 8mm camera when I was about three years old, as there were no movies of me before that. This video was all about my Dad’s side of the family, me and my 3 brothers at Christmas, and lots of birthday parties.
I’m not sure what happened with Kodak in the early sixties, I think they started the Super 8 system, which required a new camera and projector, the film was bigger. So Dad took a photography course from Don McIvor and started taking slides.
My computer guy installed Handbrake to transfer from cd to digital.
The next step was to get an Epson V600 scanner installed, as there were upwards of 7,000 slides plus 1,500 of my own. I spent some time learning how to transfer slides to my computer.
Next I bought an 8mm movie digitizer, and learned how to transfer the movies. Once I got these done I asked my Computer Guy, “I want to be able to cut, copy and paste these movies.”
“No problem,” he said, and installed the iMovie app.
My son Clayton was trying to make some money on YouTube by showing some of these old logging movies which were proving to be really popular. Then another connection was made.
Excerpt from the Supply Post newspaper, August 2021, page 4:
Supply Post would like to introduce our newest column, “Kenny’s Loggin’”. We found a fascinating video on YouTube recently; a digitized version of an old, scratchy 8mm film of logging in action, with a descriptive narration. We were intrigued, and had to know more about it. We caught up with Ken Wilson, whose father Dennis recorded the film, and Ken’s son Clayton who uploaded it to YouTube. By Linda Horn and Ken Wilson.
This is the first story we did.
Some of the movies I knew lots about them as I had worked at the places, but I had a thirty minute video I knew nothing about. We had posted some videos and one day in the comments I received a comment from a Jim Whittaker. He said, “I can remember when your dad Dennis worked for my Dad Phil Whittaker as foreman, and can remember Dennis taking these movies.”
I connected with Jim got his phone number. Jim was able to supply information about this movie. He was about fourteen he remembered logging on Salt Spring Island and travelling around to the various loggers sports and logging operations. Jim is in the Loggers Sports video showing his chopping skills. He was in a blue jacket. [Supply Post newspaper, September 2021, page 31]
These are just some of most important connections I’ve made recently. It has been a steep learning curve and really fun making the connections. This whole experience has been wonderful and rewarding.
Talking To Jim
I saw it was Jim Whittaker’s birthday on Facebook so I gave him a call. I wanted some information about the logging videos of Salt Spring Island.
My dad Dennis started right out of school with Phil Whittaker. In the early 1950s, he was logging some of Salt Spring Island. Dennis showed a lot of promise and enthusiasm, so Phil trained him as a logging foreman. He soon learned how to run all the equipment that was on the claim.
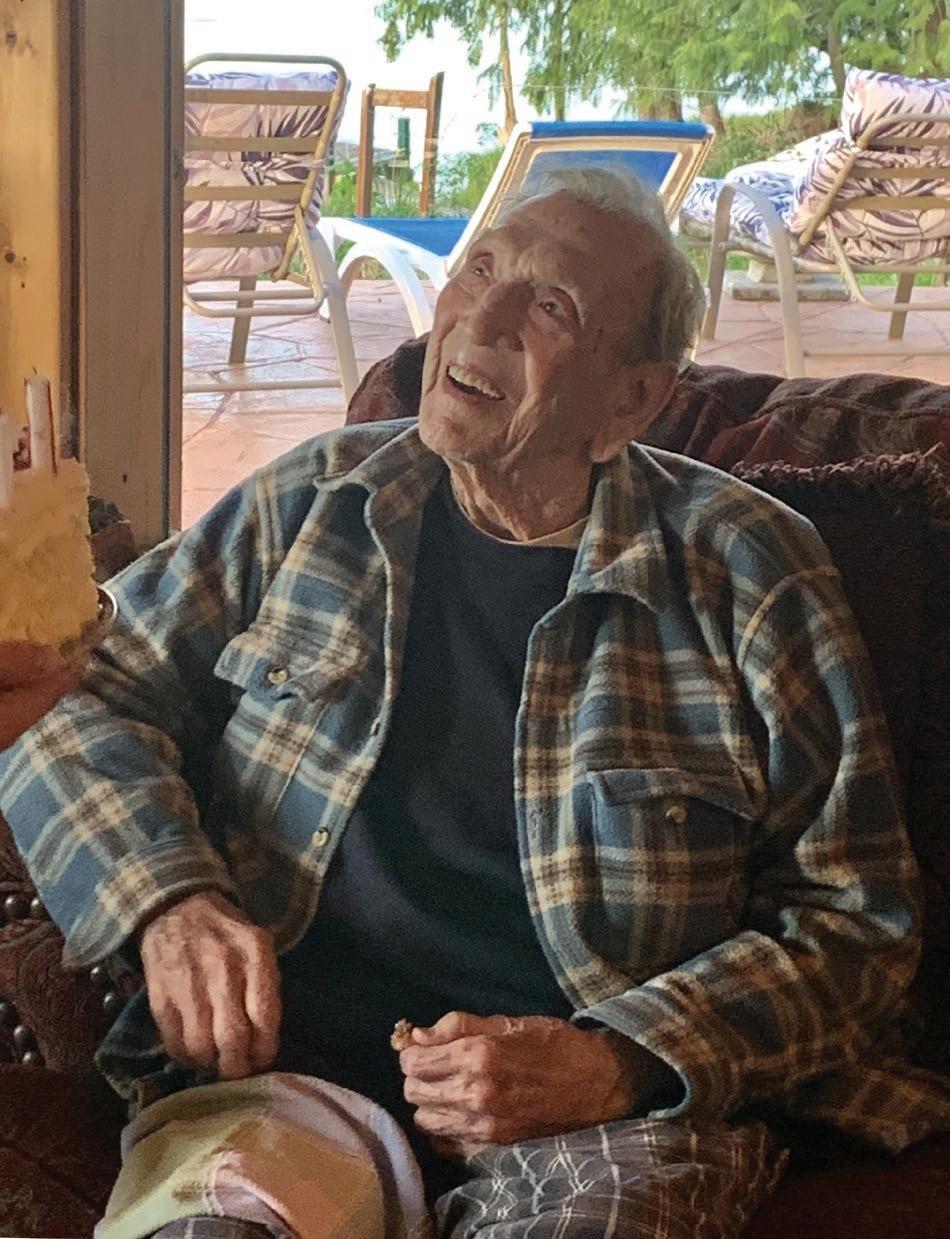
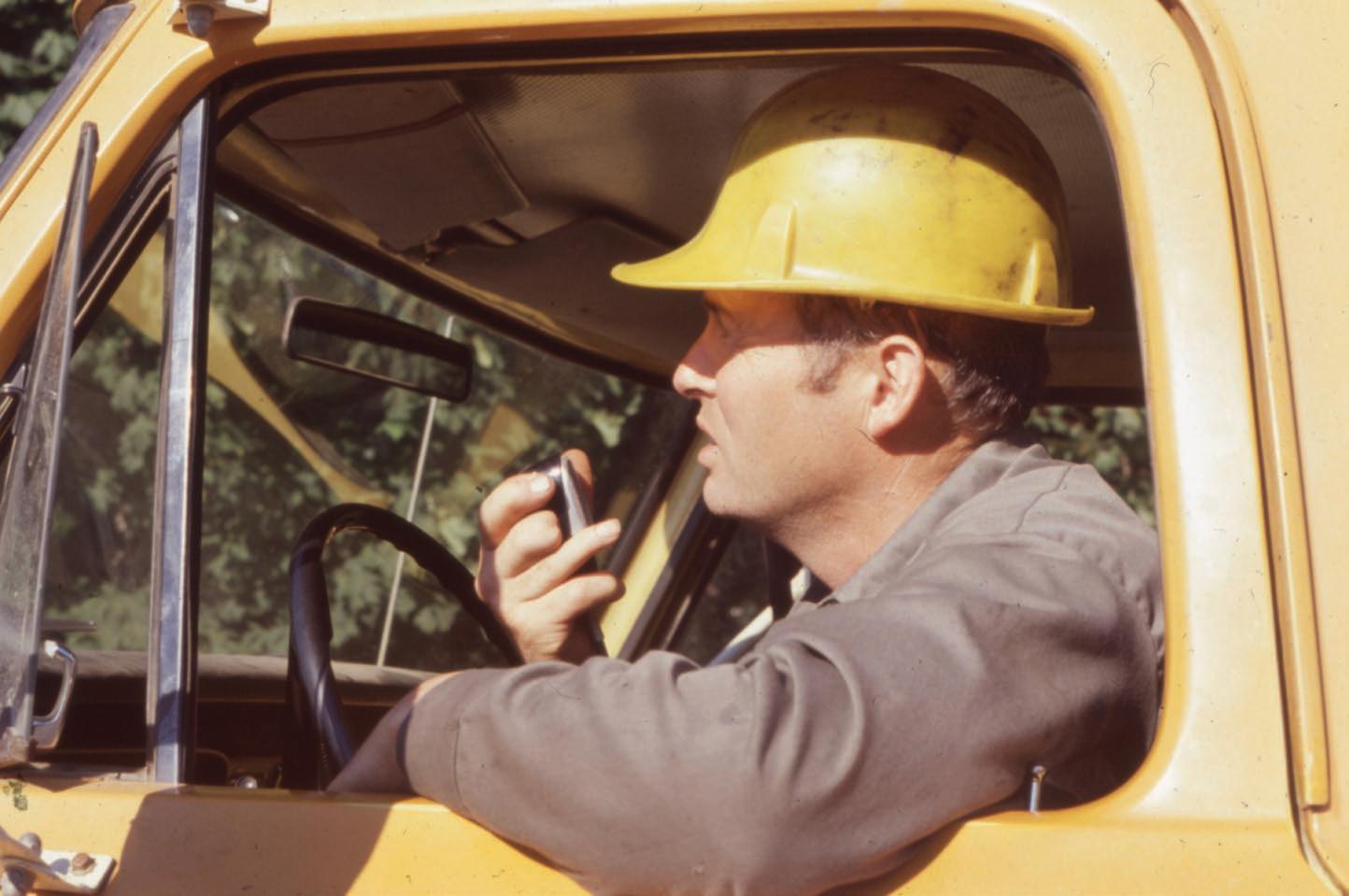
They logged for a few years on the island starting up at the north end and eventually ending up around Burgoyne Bay.
Jim said that they had several donkeys — powered by gas Ford engines. Lots of war surplus stuff. I asked him what they did for fuel as the Cats and trucks were diesel and the donkeys and welders took gas. The biggest war surplus items were 45 gallon barrels. They would load the landing barge with 45 gallon drums, fuel them up and take them to the logging show where they were distributed as needed. At some point they would have to be manhandled and the fuel pumped by hand. Jim mentioned that the fuel was dirty lots of times, always had lots of spare filters standing by.
Some places they loaded trucks and dumped into the water and other places hauled right onto the beach with the Cat and arch, where the logs were bucked and pushed out to the booms at high tide. Some of the roads they hauled logs on are now public highways.
They would run crew boats to the closest tie-up places from their logging. Randells Point, which was at Cherry Point, Maple Bay, and Cowichan Bay. Howard Randell had a wharf and boat launch; they would haul the boats up to scrape the barnacles off. Jim said this was one of his first jobs. Scraping barnacles was ok for the first day or so but once the barnacles died there was a
More ONLINE
Check out video at SUPPLYPOST.COM/NEWS whole lot of stinking going on. Howard Randell had two sons Ray and Billy and they owned the landing barge and boat seen in the video. They were kept pretty busy servicing the logging going on in the vicinity. They were always delivering barrels of fuel. Apparently, they would back the cat and arch down to the landing barge and hook up to a dozen barrels with the chokers on the arch and up the hill to the machines (lots of spillage)
Jim lives in Cowichan Bay right down by the water. He spent lots of years in Squamish just moving back recently. Jim still has some antique equipment which he is donating to loggers museums. Thanks Jim.

Next I start my career at M&B Menzies Bay Division. SP very good work ready condition. Call for details.
Ken Wilson worked in the logging industry in B.C. for over 50 years. Ken is a regular contributor to Supply Post newspaper with his column “Kenny’s Loggin’”, and resides on Vancouver Island, B.C.
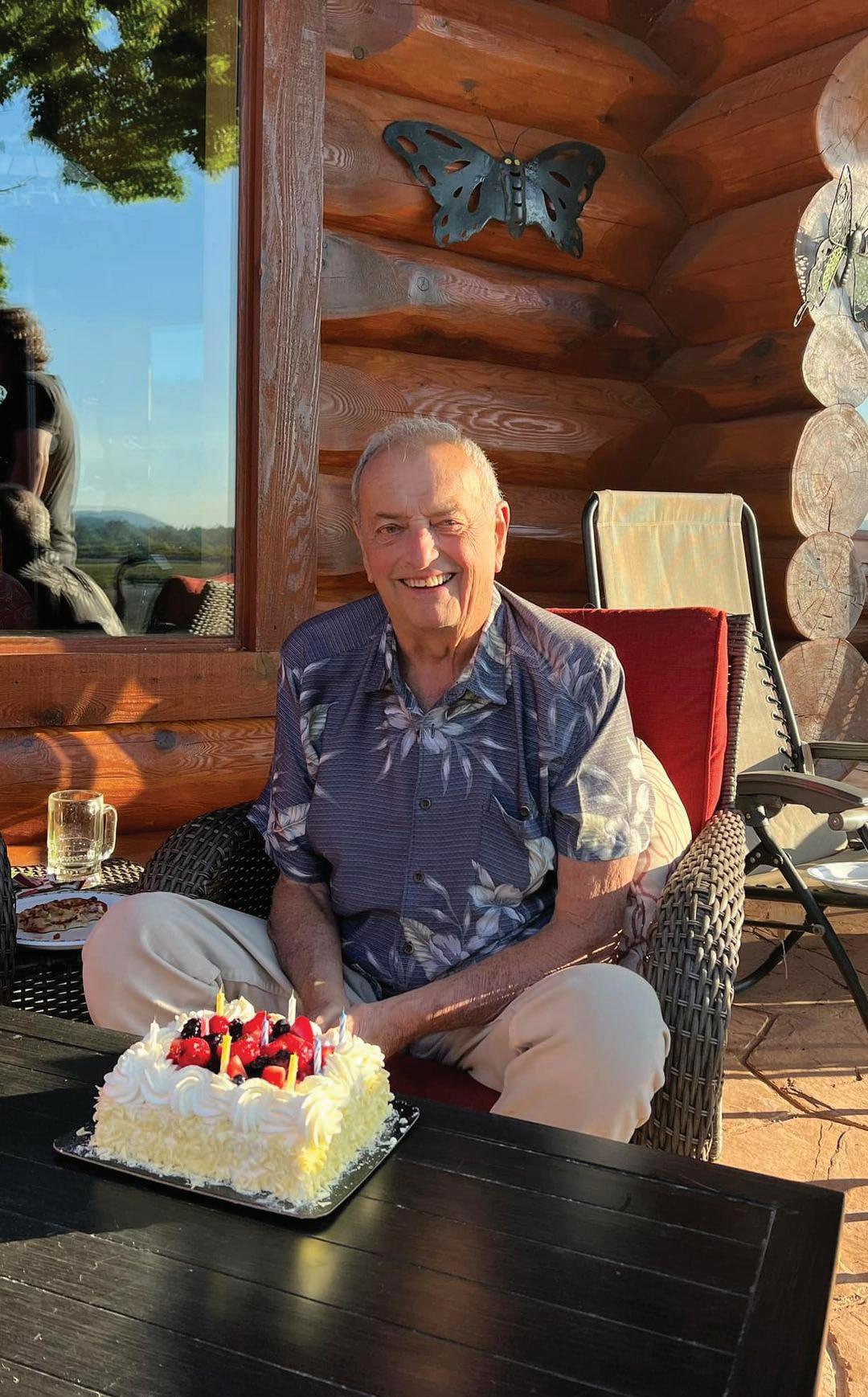
Cat C7.1 power, 4120 hours, in excellent condition.
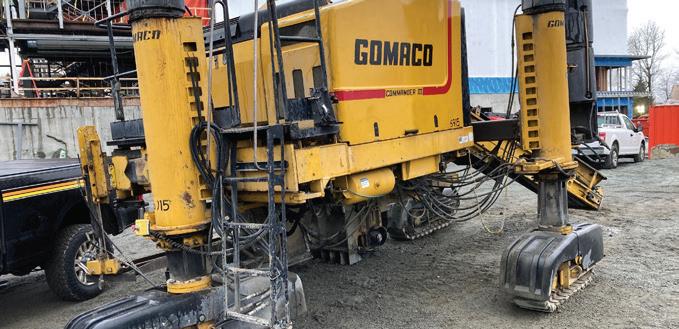
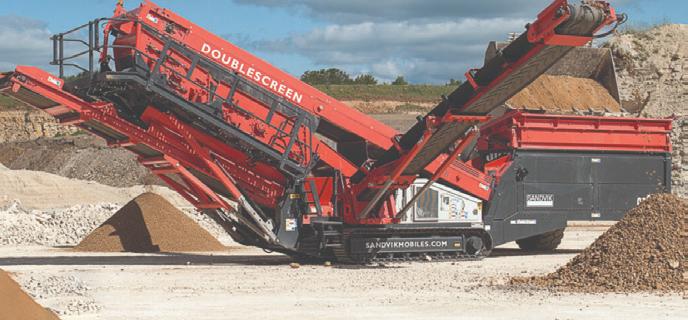
$355,000
Track Finish
Power, 5’ x 13’ – 2
220 hours, available for sale or rent. New unit available as well.
$299,000 motors.
Sandvik Mobile QA441 Track Finish Screen, Cat C4.4 Power, 5’ x 20’ – 2 deck, 800 hours, available for sale or rent. New unit available as well.
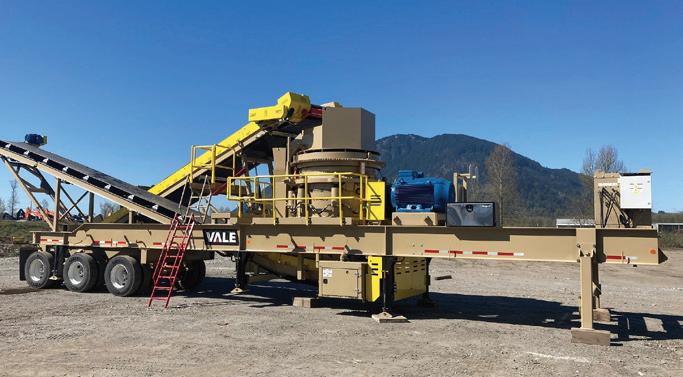
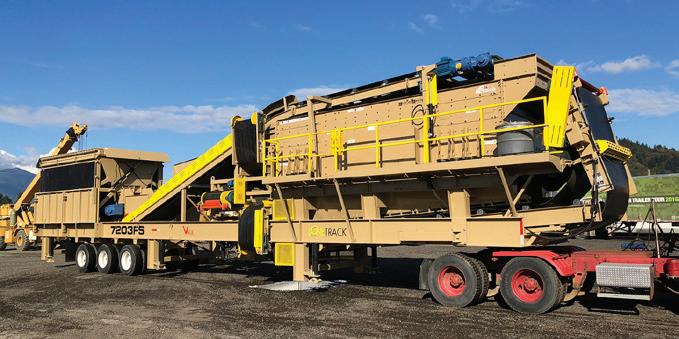
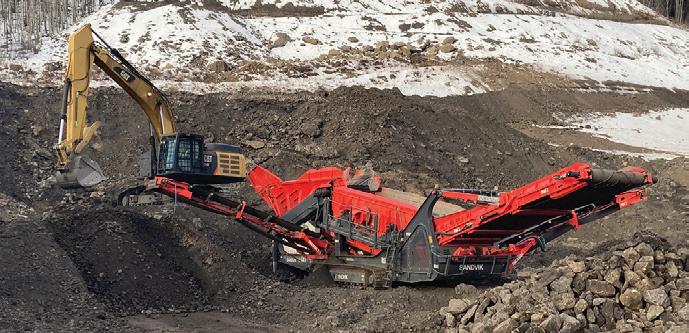

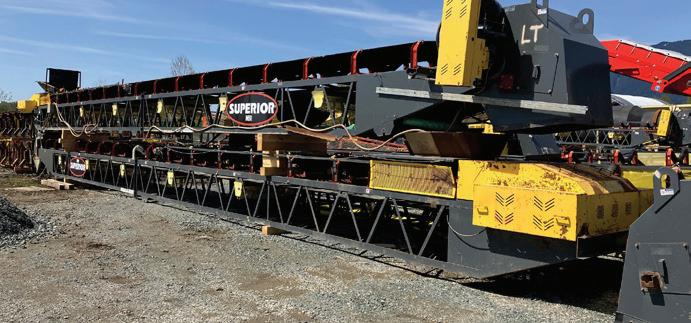
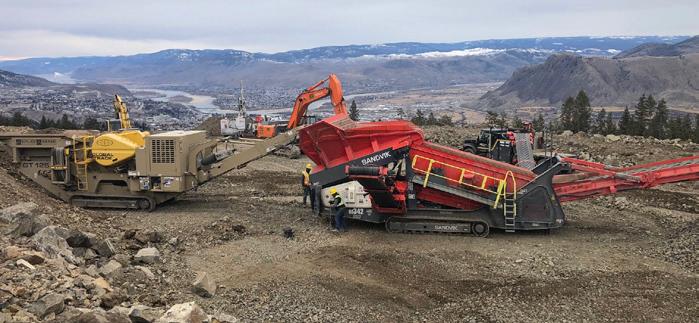
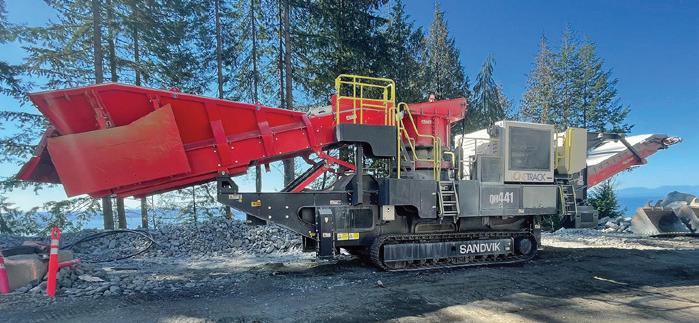
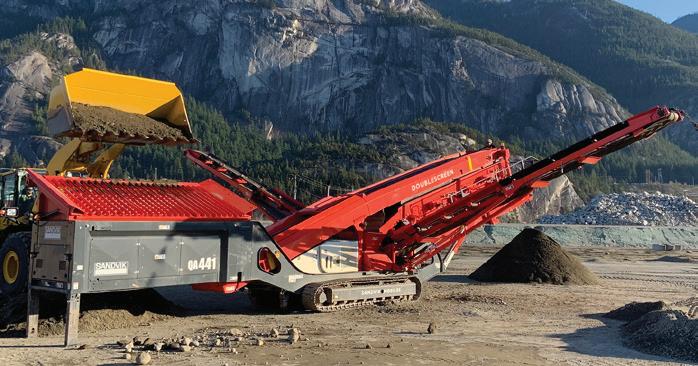
Nordberg (Metso) 21 x 36 Jaw Plant, 100 HP jaw drive motor, 38” x 14’ VGF, Hydraulic tipping grid included, Switchgear & cable available.
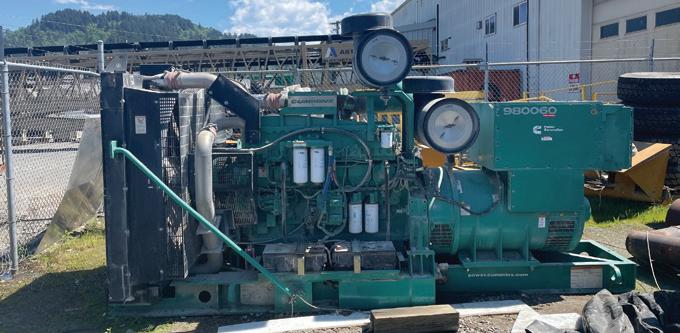
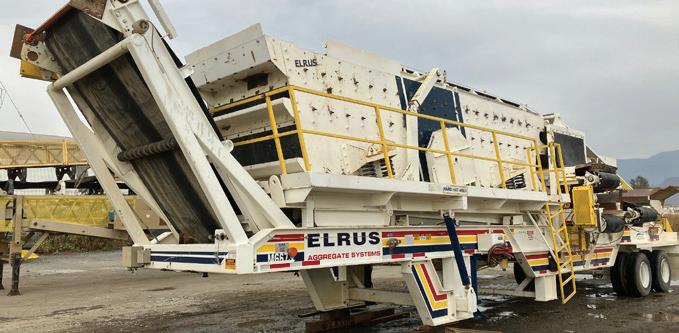
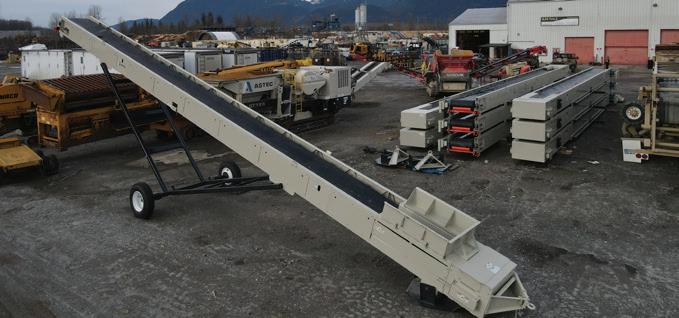

Gomaco
III., 2008 unit with 5420 hours, extensive work just performed, work ready with all sensors, cables, wands.
Generators Available, 700 & 800 Kw. Cummins, 28 liter & 30 liter, under 700 & under 5000 hours.
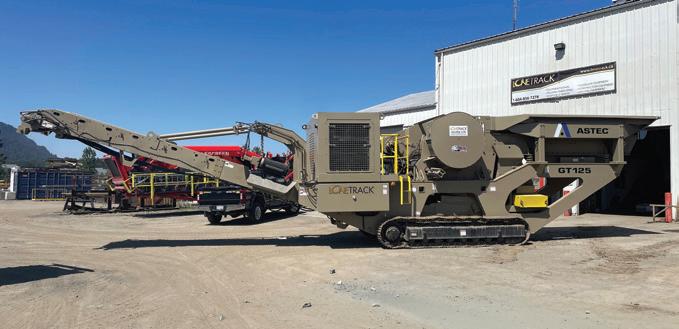

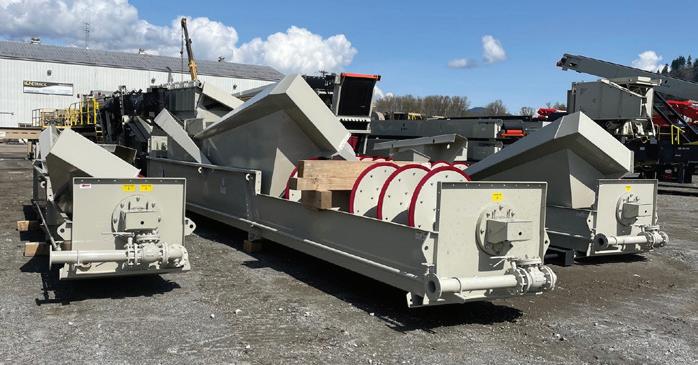
Used Powervan. 53’ tandem, 500 Kw. Cummins, switchgear to run jaw, cone, screen & stackers, tower, tank, plug box, control console.
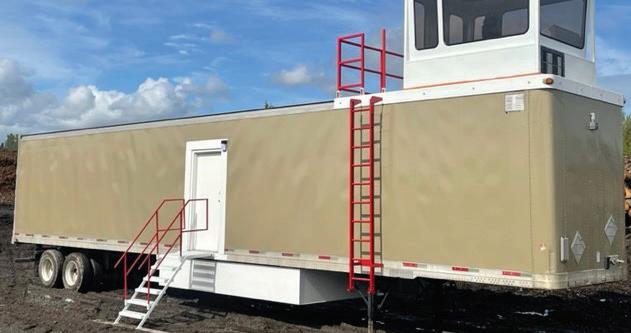
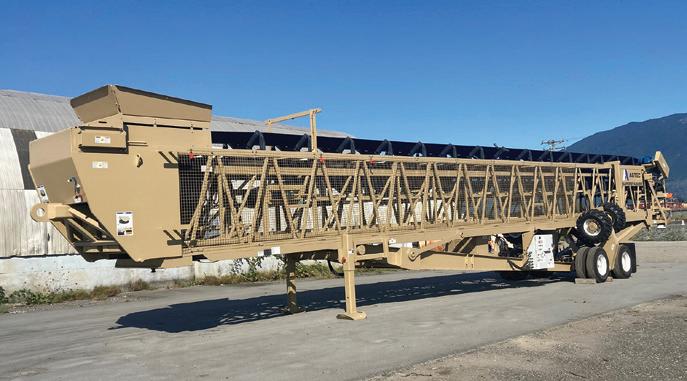
Calgary Aggregate Recycling: Canada’s Largest C&D Waste Plant
Wash plant will be showcased to the industry at upcoming open house event on Sept 7th.
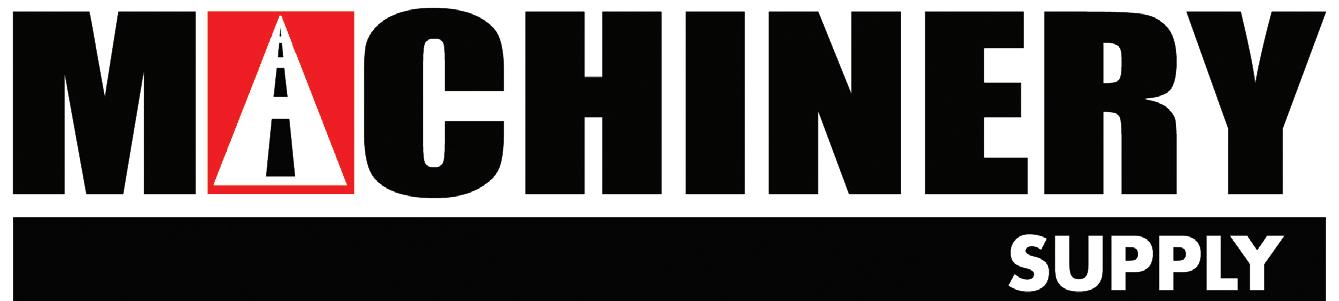
Later this year, washing experts CDE, in partnership with concrete, asphalt and aggregate recycling firm Calgary Aggregate Recycling Inc. (CAR), will host an open house event to showcase the company’s largest construction and demolition (C&D) waste recycling plant in Canada.
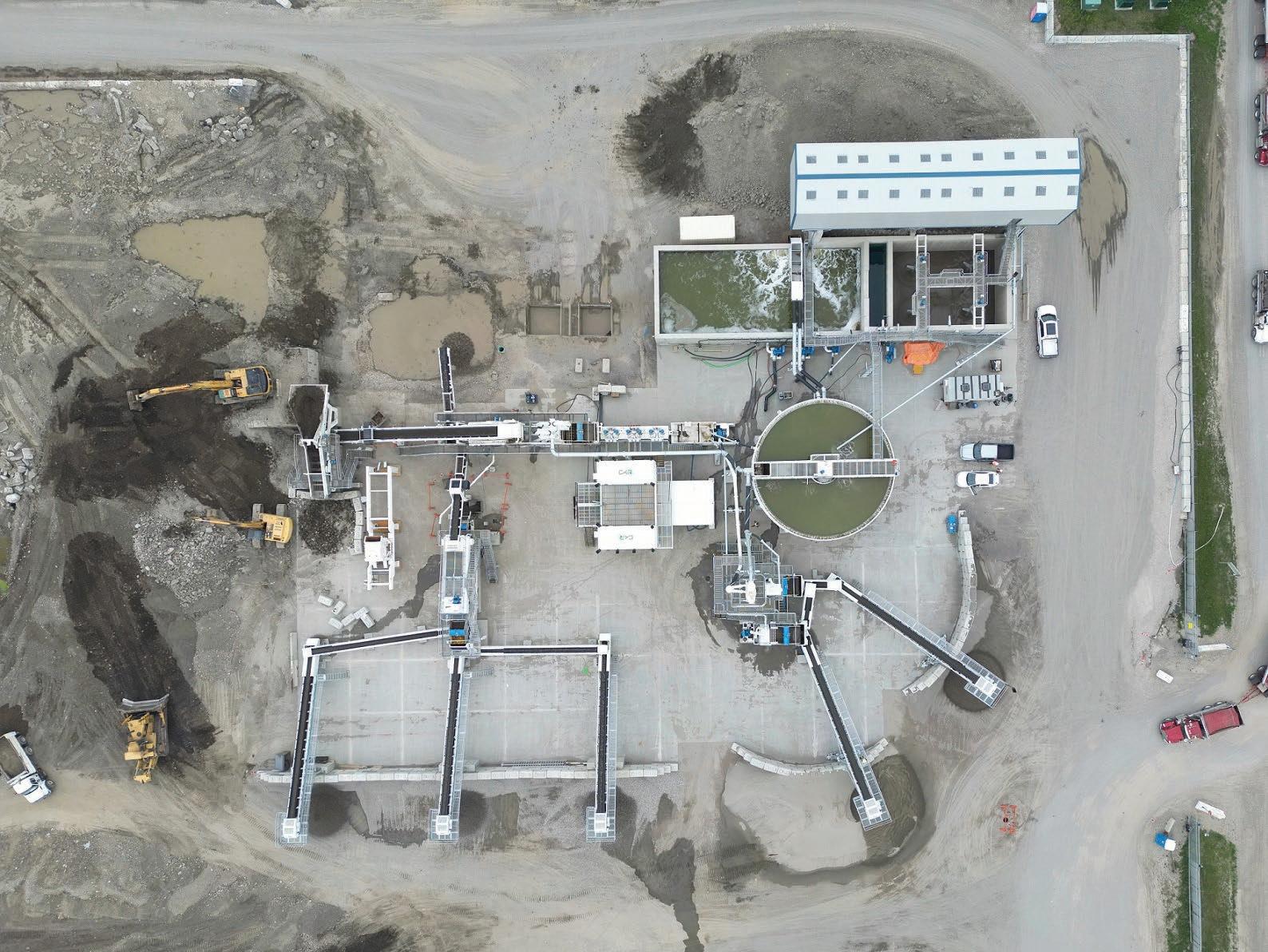
Recently commissioned at CAR’s recycling facility in southeast Calgary, the new 250 tons per hour (tph) washing solution, designed and engineered by CDE, will take centre stage on Thursday 7th September 2023 as industry representatives gather to learn more about CDE’s innovative recycling process and the positive impact its technology is having on resource availability in the Calgary and Alberta areas.
Travis Powell, President at Calgary Aggregate Recycling Inc., says: “We have been very busy hosting tours since opening and have received tremendous feedback from the community on how we can help them achieve their business and environmental goals.” us the start we needed to get to where we are today.
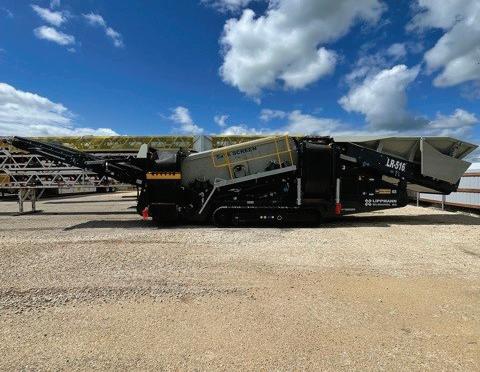
He says the aim of the plant was to disrupt the ‘outof-date practices’ in the construction industry.
“With the ERA’s backing and CDE’s incredible support, expertise and proven experience in this space we are strongly positioned to make significant strides forward in our mission to reduce the cost of construction – socially, environmentally, and economically.”
“We set out to establish economical and viable solutions to position Alberta as a leader in sustainable and responsible construction. We started this process by applying for a grant with Emissions Reduction Alberta (ERA). It believed in the impact our proposal could have and gave
Enabled by CDE washing technology, the company now has the capacity to process an additional 600,000 tons of waste material to produce more than 1.25 million tons of construction sand and aggregate products every year across the wider company operations.

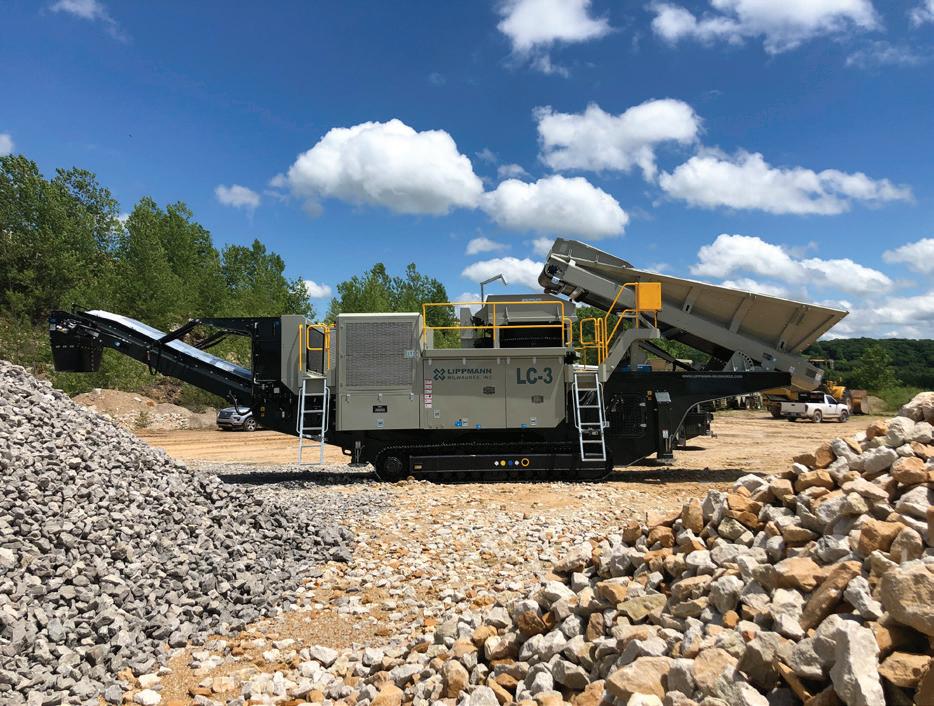
CDE’s Business Development Manager for Canada, Adrian Convery, says: “This plant is both the largest we have ever commissioned in Canada, but also our first partnership with CAR which demonstrates real confidence in our washing technology and recycling process.
“It’s a partnership that is pioneering better ways of managing resources in Canada, driving forward the agenda for change, and building a strong case for the adoption of recycled materials in the construction industry by highlighting the immense potential of C&D waste streams.”
In addition to the significant volume of material the plant is diverting from landfill, the circular approach to resource management is also helping to reduce carbon emissions in Alberta, particularly when it is estimated that the population growth of Canada will double by 2050.
Adrian continues: “CDE waste recycling solutions are perfectly adapted to support urban centres where the need for construction materials is greatest. As well as landfill diversion, our solutions help to realize sustainability aims by reducing, or completely eliminating, the requirement to truck in sand and aggregate resources from other jurisdic- tions – an approach that generally comes at a significant environmental cost.”

It is expected that the plant will help to reduce carbon emissions in Alberta by an estimated 22,567 tons annually.
Engineered for CAR
CDE’s substantial experience in developing waste recycling solutions in North America made the washing expert the ideal partner for CAR when it set out to commission the advanced system
Continued on page 33 to support its economic and environmental goals.
CDE facilitated meetings virtually and utilized 3D modelling and remote technologies to showcase to CAR many of its international waste recycling plants, in- cluding Brewster Bros, based in Scotland, a family business that recently announced it was investing in its second CDE wash plant, and the Long Island, New York-based Posillico Materials LLC, home to the first contaminated soils wash plant of its kind in the US.

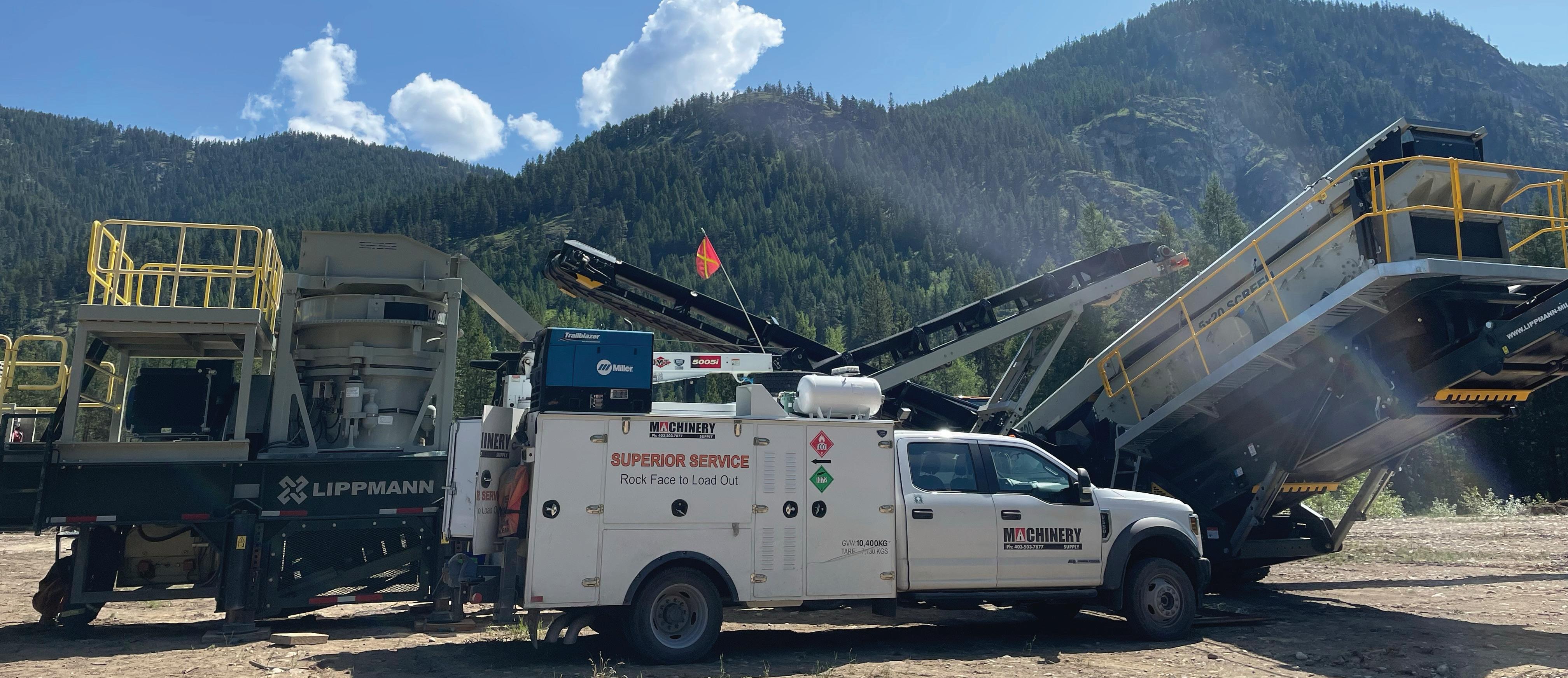
Confident CDE was the partner of choice and its technology best-in-class, CAR commissioned its firstever wash plant consisting of an R4500 primary feeding and scalping screen with the M4500 modular sand washing plant and AggMax 253R

Continued on page 34 scrubbing and classification system, which combines prescreening, scrubbing, organics removal, sizing, stockpiling, fines recovery and filtrates removal on a compact chassis.
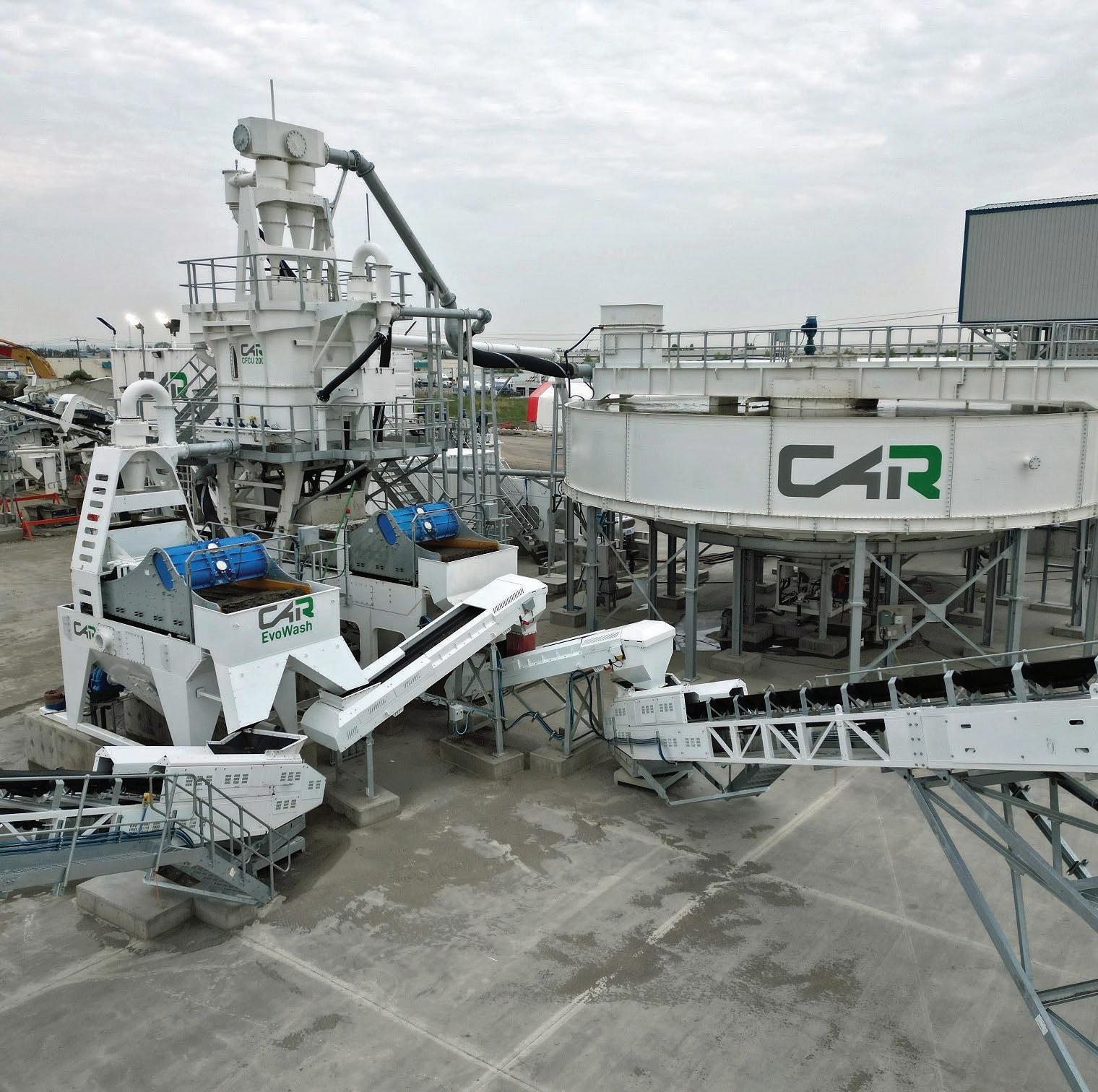
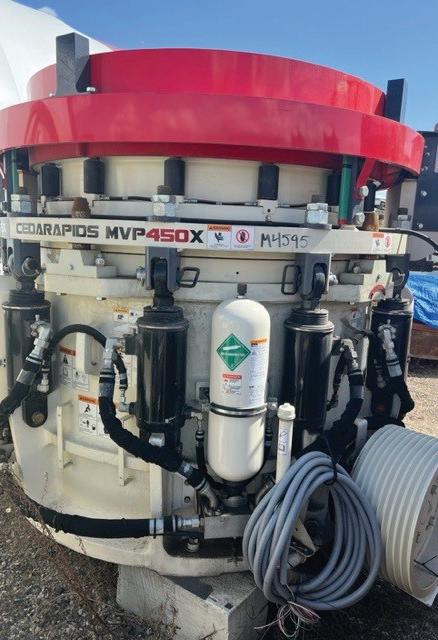


The solution also features CDE’s EvoWash, a modular sand washing system that screens and separates smaller sand and gravel fractions through an integrated highfrequency dewatering screen and hydrocyclone technology to provide unrivaled control of silt cut points and eliminate the loss of fines, as well as its CFCU (Counter Flow Classification Unit) technology which offers a variable cut (separation) point to provide greater control over sand classification.
Underscoring the solu- tion is CDE’s AquaCycle thickener water management system, which offers efficient recycling of up to 90% of process water, and its Filter Press sludge dewatering system which presses sludge discharged from the thickener to recover even more water –bringing recovery up to 95%.
Seven saleable products
Processing up to 250tph of raw feed material, the CDE solution is transforming C&D waste into a high value suite of construction products, helping CAR to generate additional revenue while simultaneously diverting significant tonnages of material from landfill.
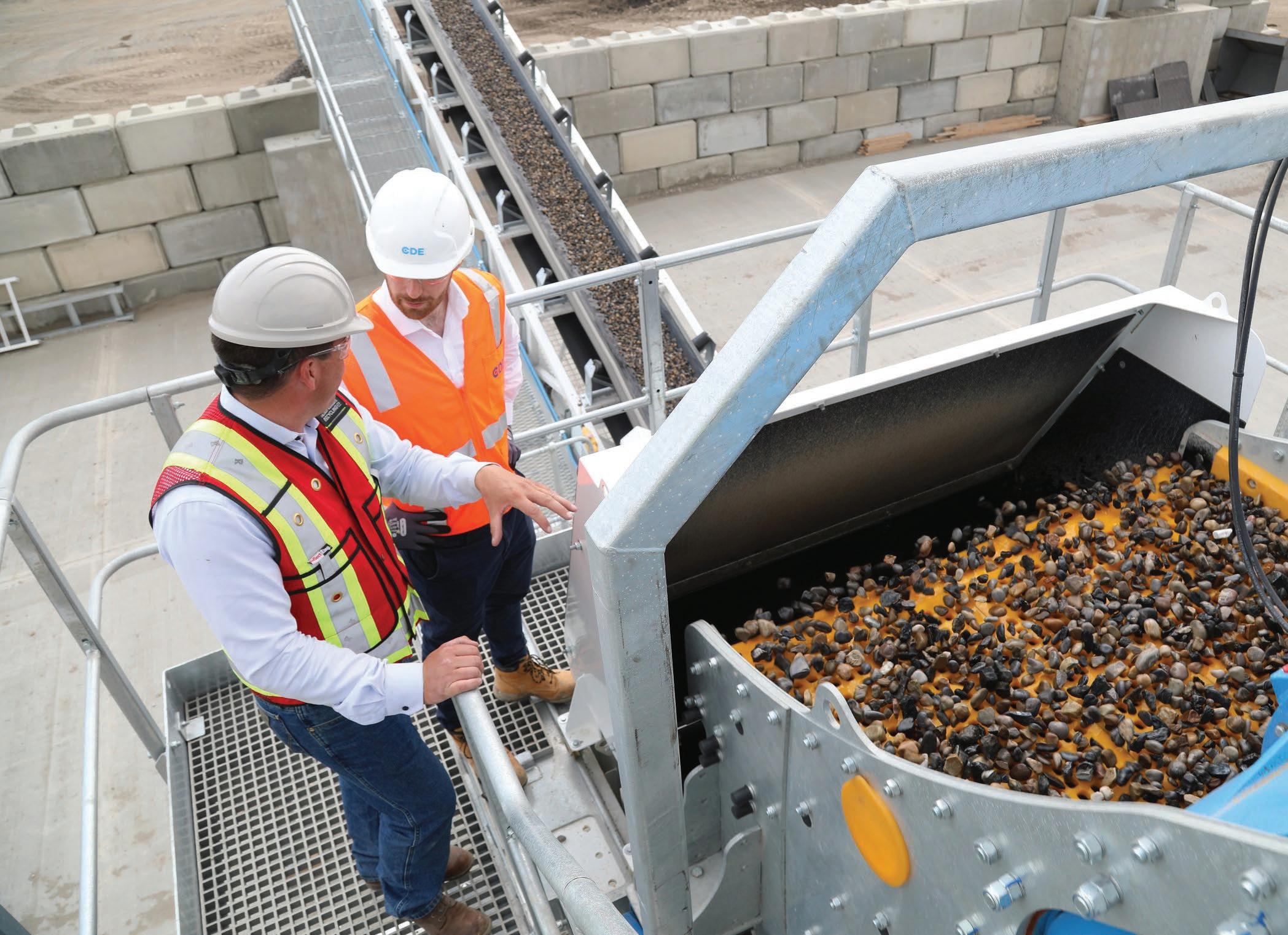

Among the outputs are 0-1mm fine and 0-4mm coarse sands as well as 4-10mm undersize, 10-20mm midsize, plus 20-40mm, 40100mm and >100mm oversize aggregates.
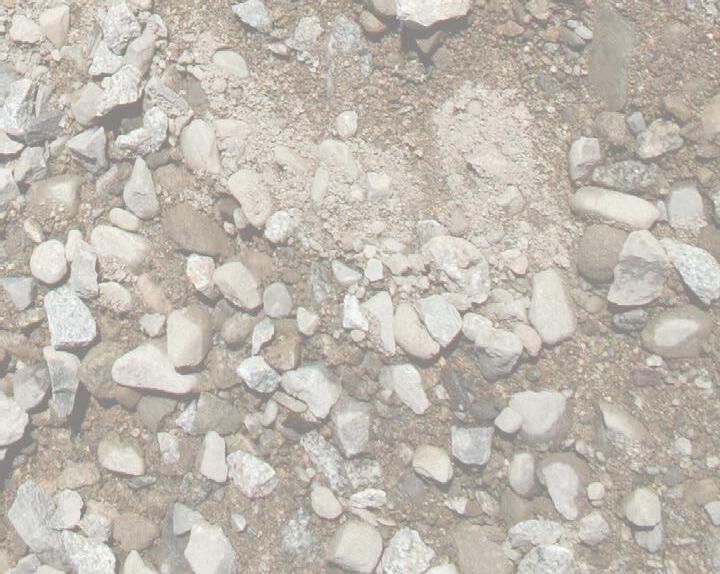
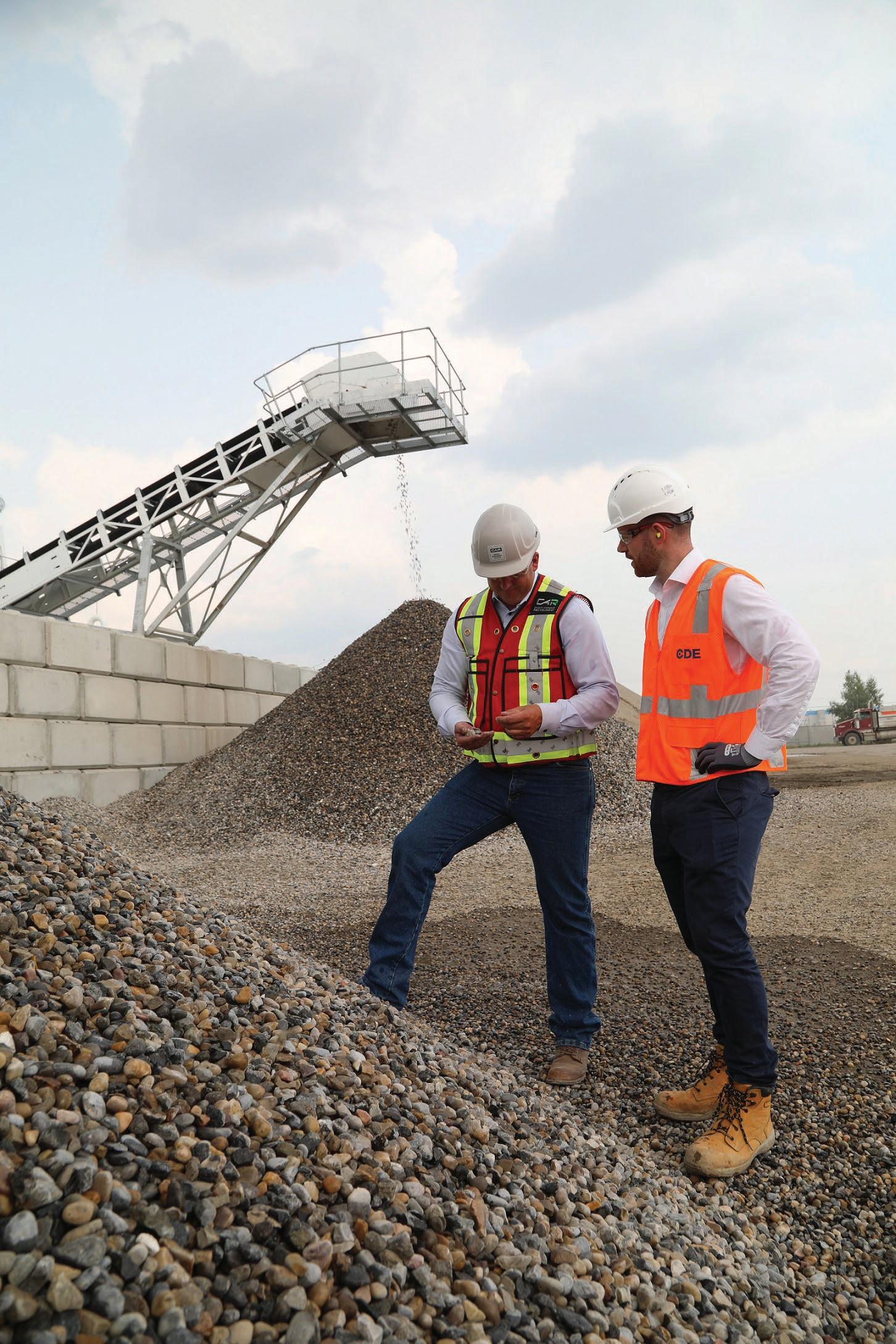

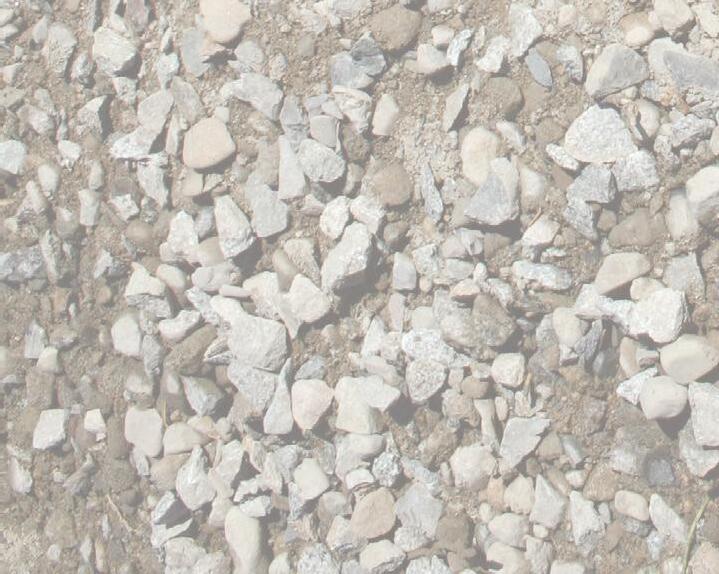
Frequently tested to ensure compliance with City of Calgary standards and specifications, the product suite is being marketed to the wider construction industry in the Calgary and Alberta areas and is supporting a range of major public works and infrastructure projects, including a project with City of Calgary, hauling 1,300 tons of contaminated soils out of the Bow River, this project generate 54 tons of CO2 emissions, saved from the environment.
Stepping up to the challenge
Prior to CAR working with CDE, it did not have an outlet for contaminated soils. Therefore trucks were taking a 350km round trip to dispose of contaminated soils at a landfill whereas now the trucks have increased load frequencies per day, with less servicing required resulting in a reduction in carbon emissions. Additionally, CAR are producing in spec material for the Calgary and wider construction sector.
As Alberta’s population growth continues, the de- mand for infrastructure has never been greater.
Open House
CDE and CAR are extending an invitation to the industry to attend an upcoming Open House event at the recycling facility in south east Calgary on Thursday 7th September 2023.
Commenting on the event, Mr. Powell says: “It is a plea- sure to host this open house event with our partners at CDE to showcase this impressive facility that its team has delivered and to highlight the benefits of waste recycling.”
To register your interest for the event, please visit cdegroup.com/calgary.
Please note that registration is mandatory. SP
Source: CDE
682 Okanagan Ave. E., Penticton, BC, Canada
1-866-344-6480 cturchak@brutusbodies.com
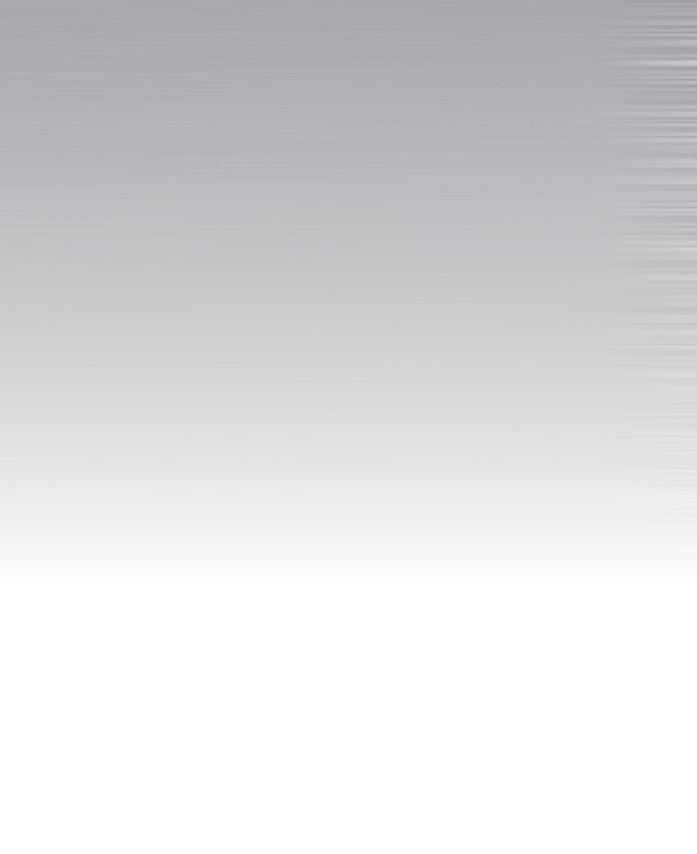
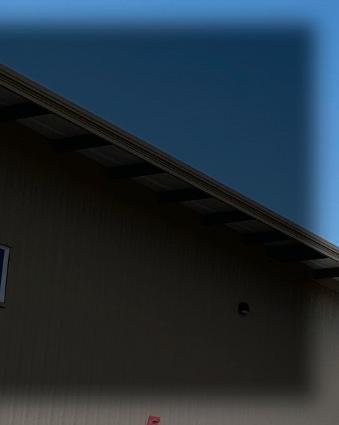
Your Truck Body Building Specialists
Brutus Truck Bodies and Maranda have joined forces to offer the �irst composite-aluminum crane bodies for the North American service truck market. These premium quality bodies utilize Maranda pure resin composite cabinets and doors to withstand the harsh Canadian winter conditions, while advanced Brutus aluminum crane structures allow for rooftop mounted Cobra service cranes or rear workbench mounted Maxilift folding cranes.
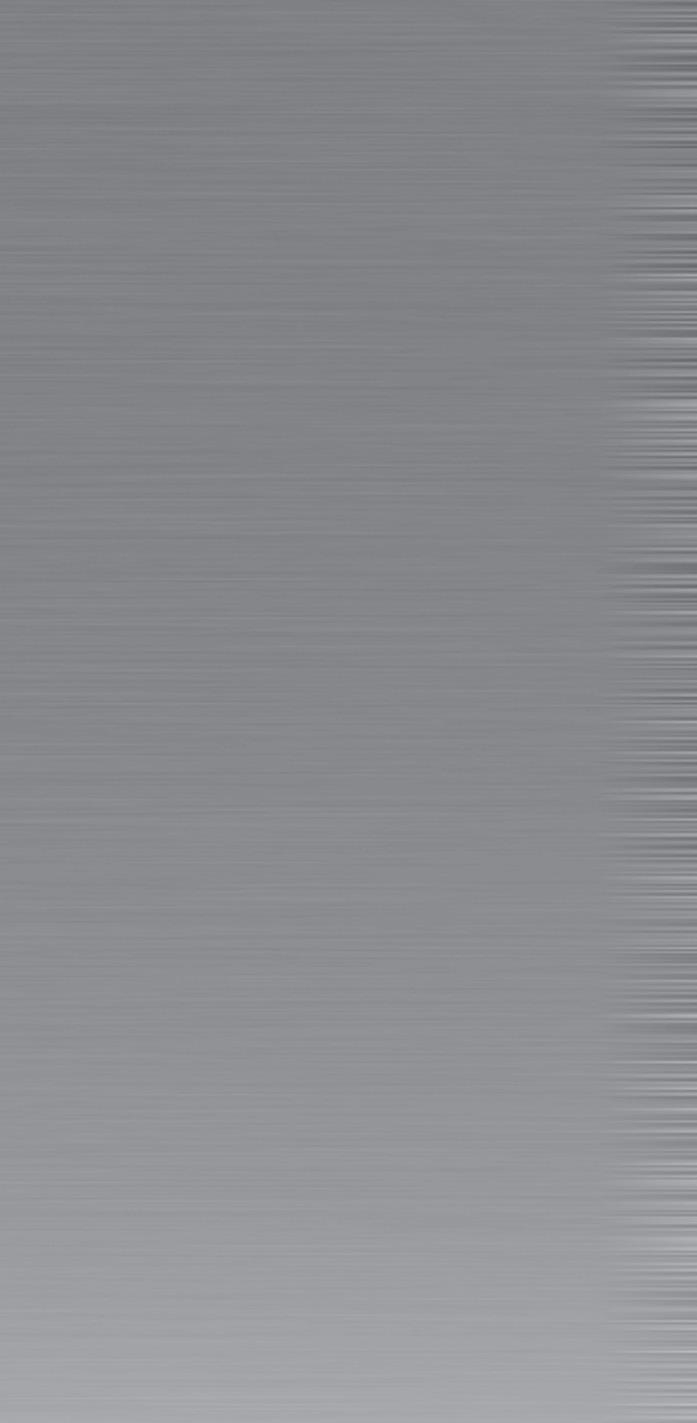

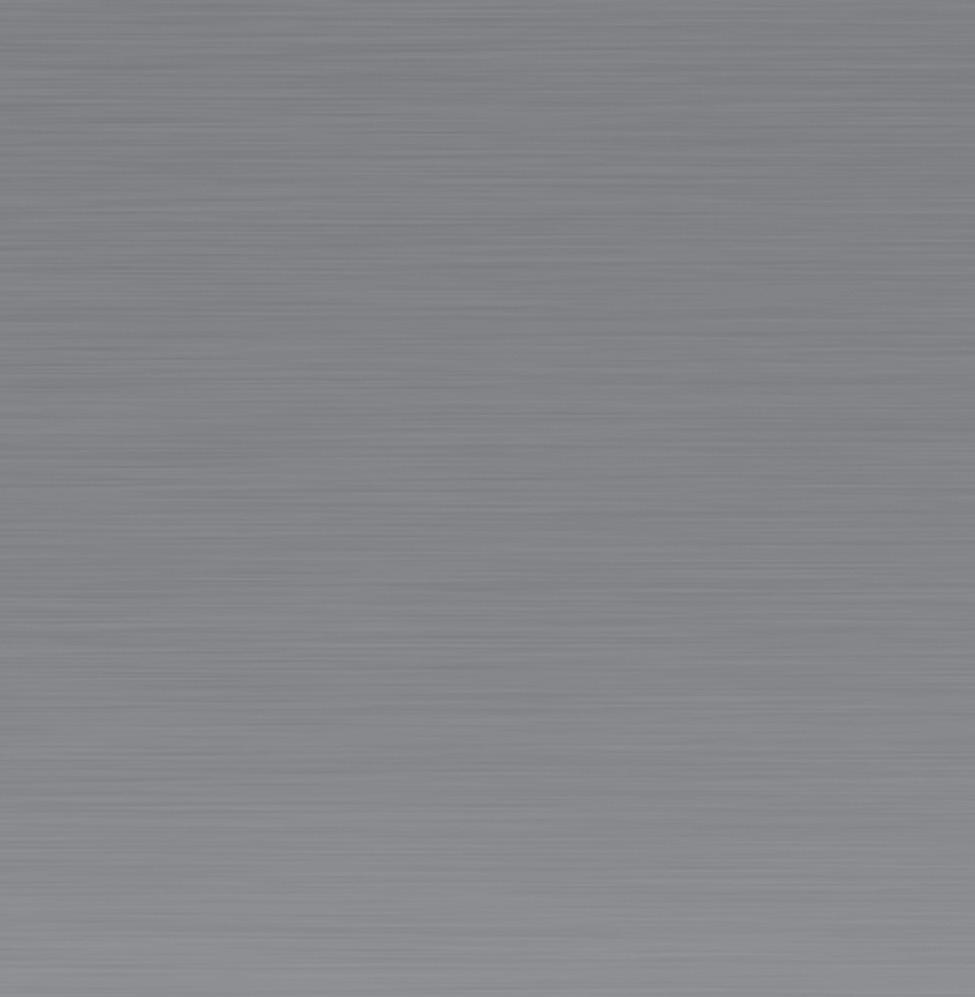
Brutus Truck Bodies also offers the complete Maranda product line of composite transferable canopies for all truck manufacturers with 6’, 6 ½’, and 8’ pickup boxes www.brutusbodies.com
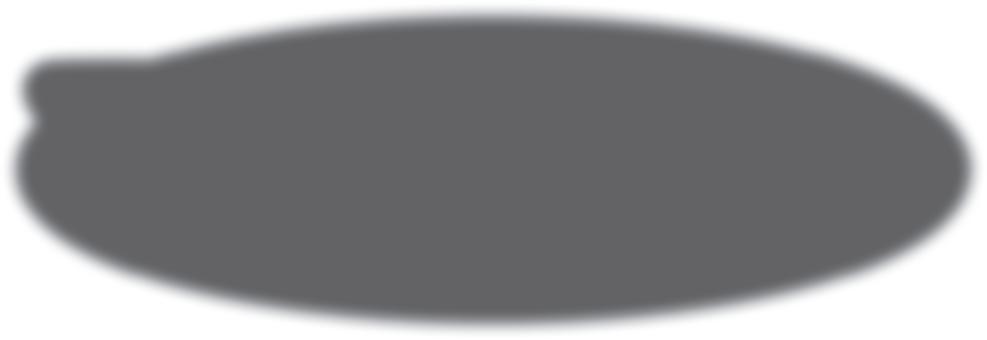

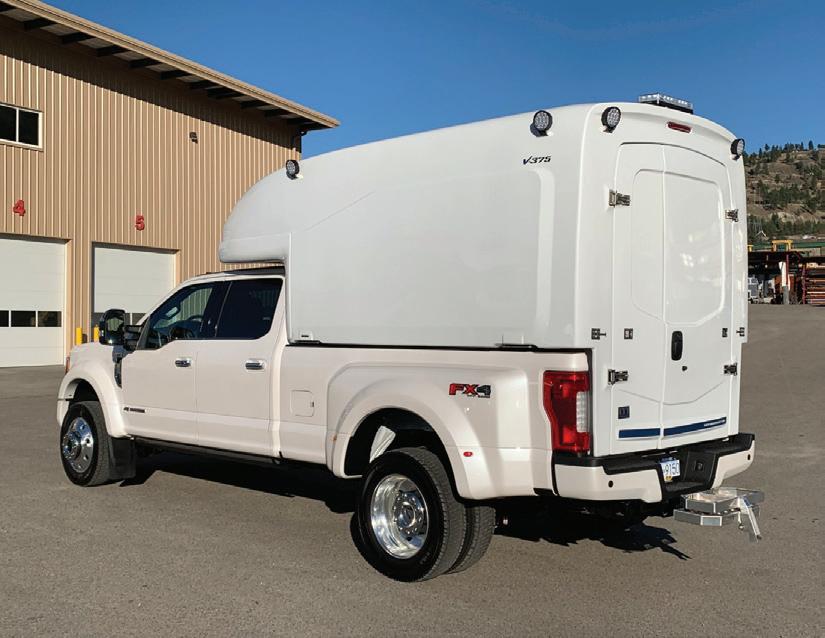
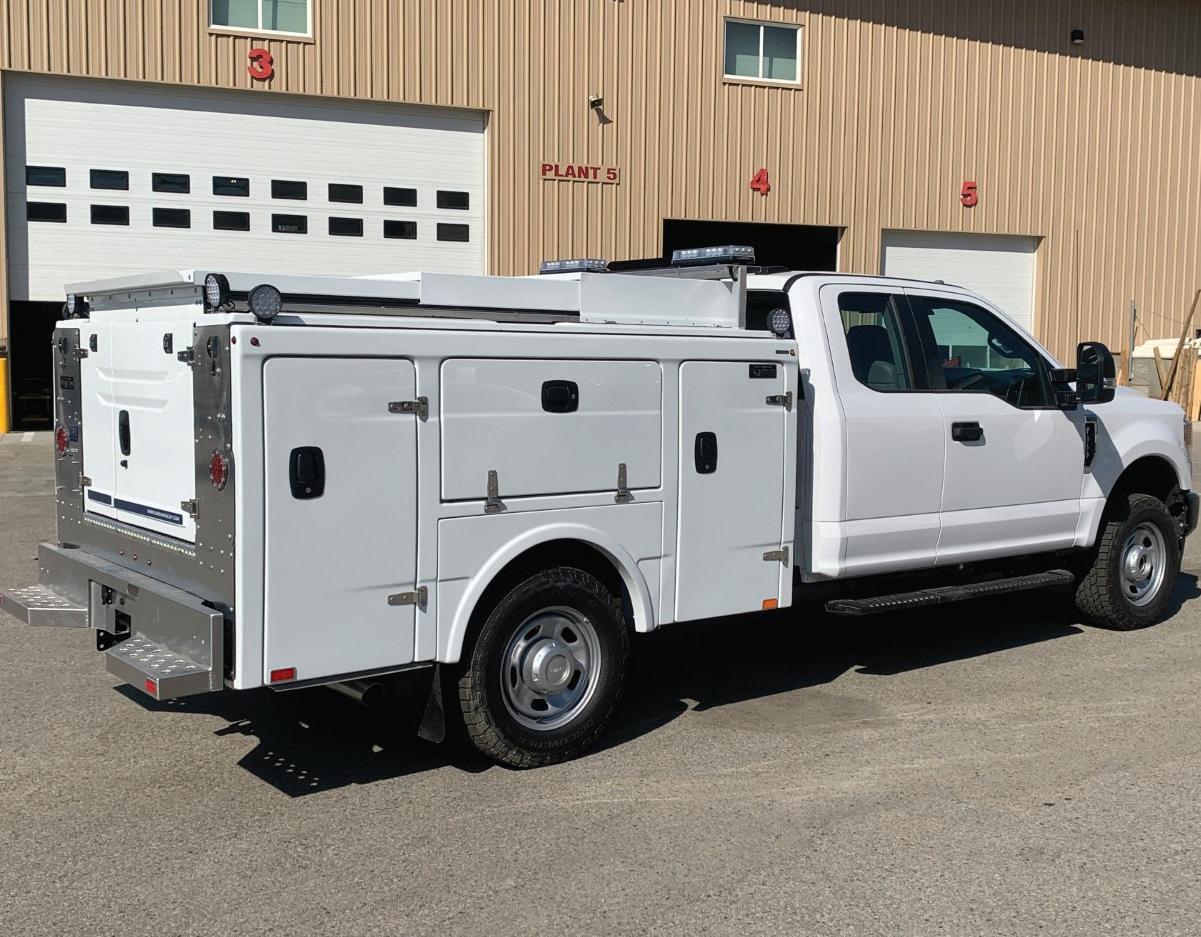

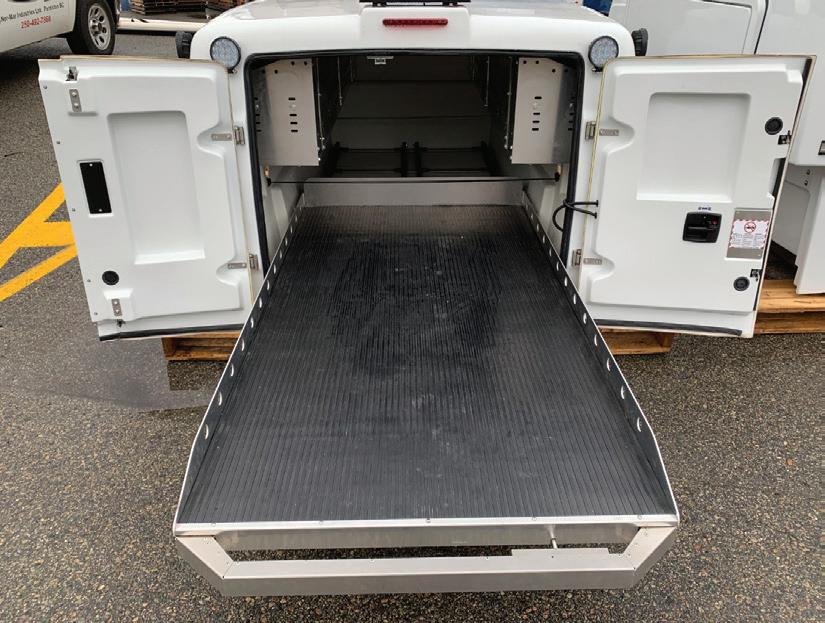
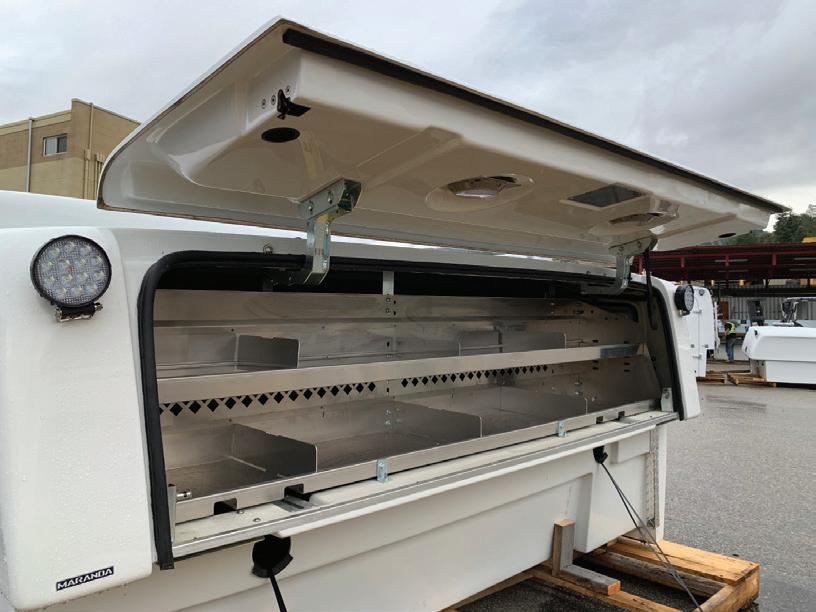
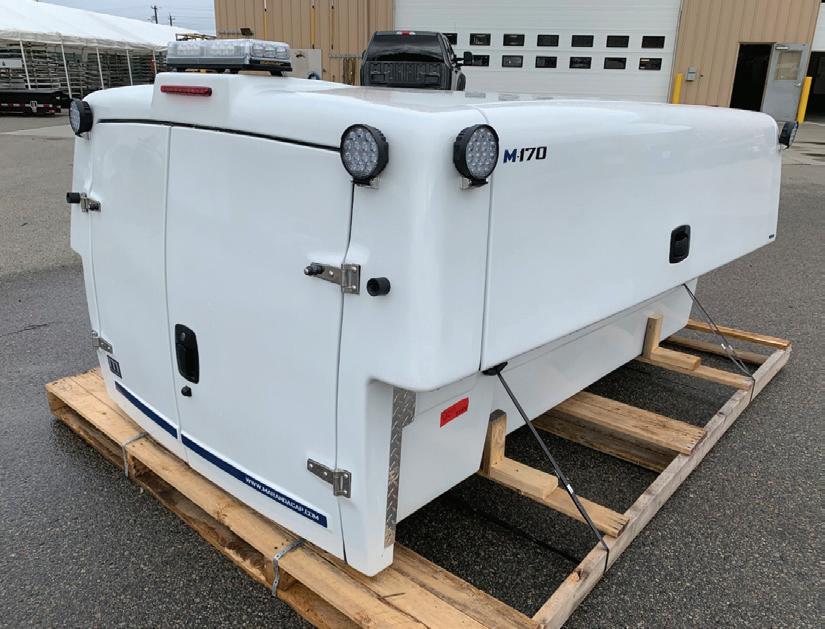
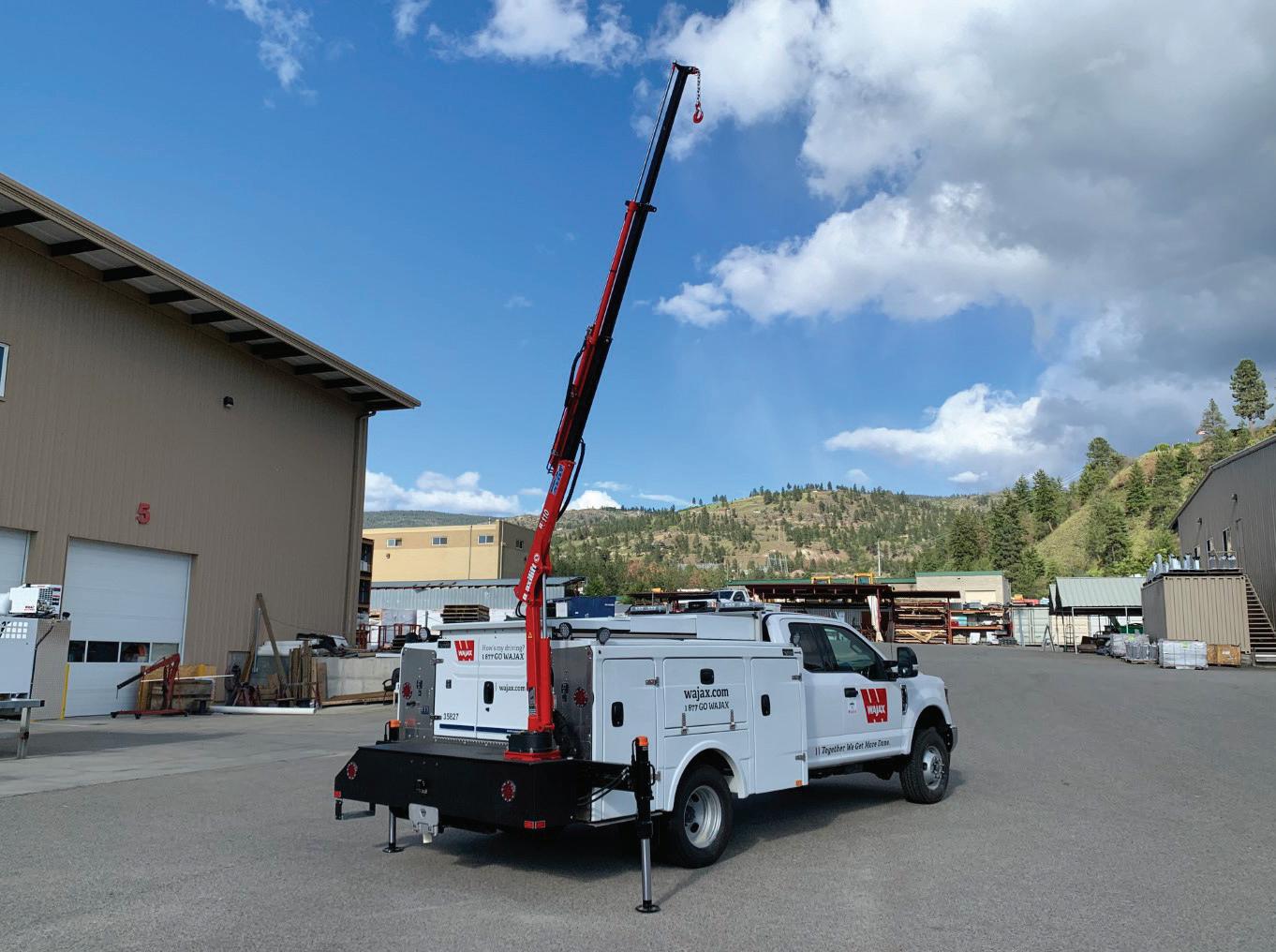
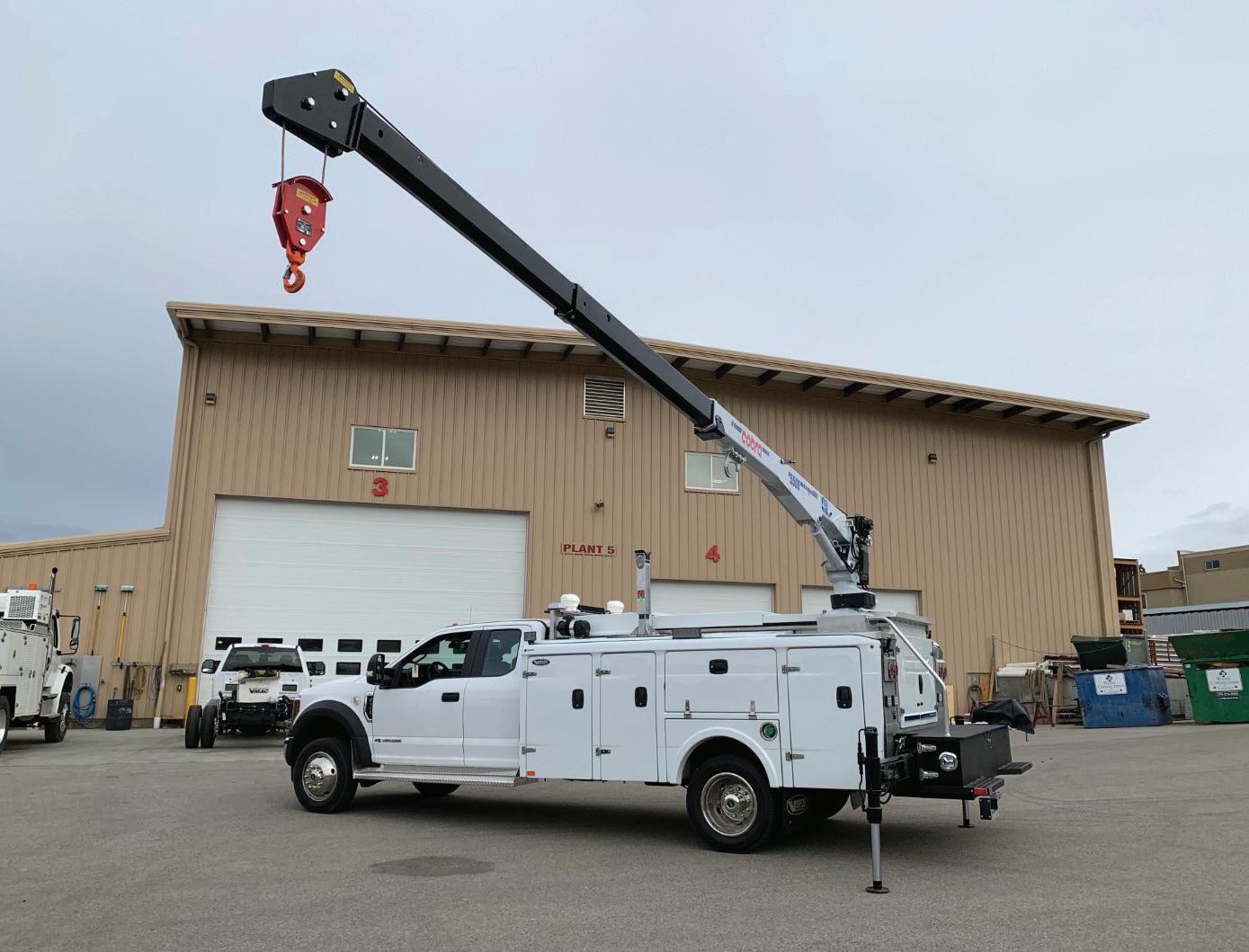

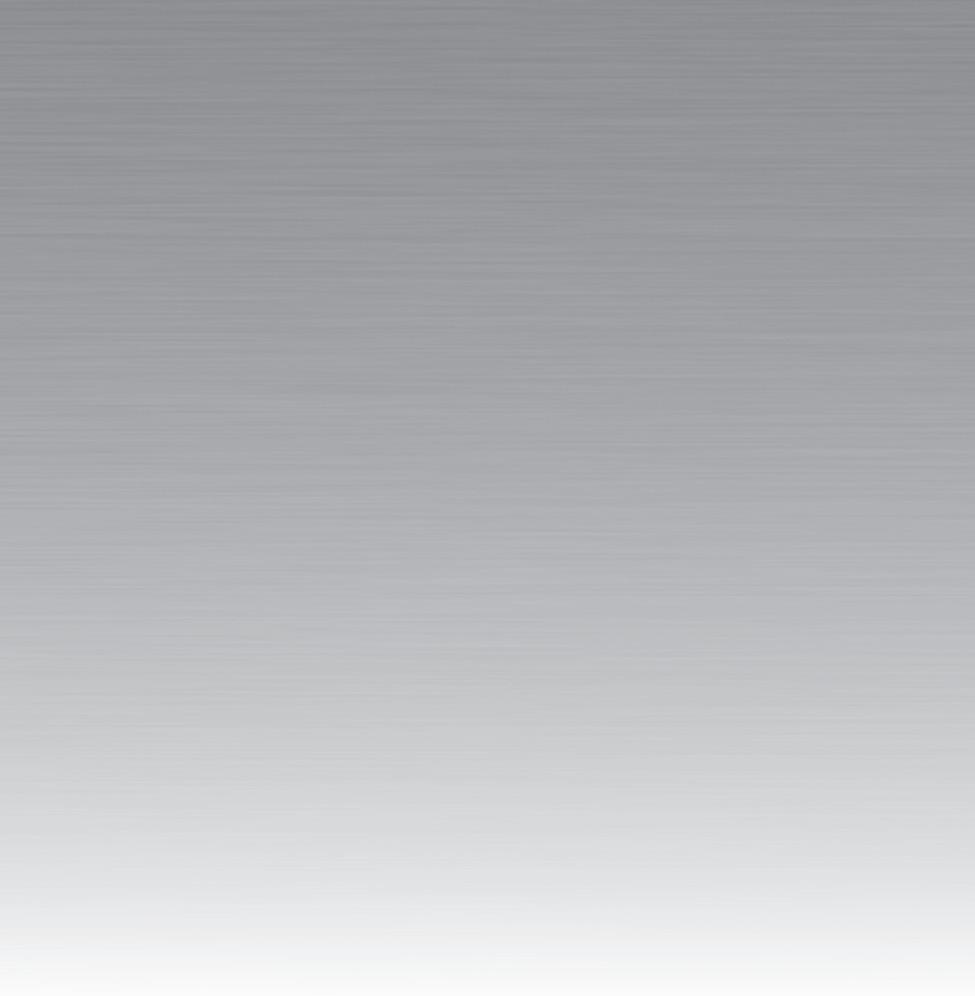
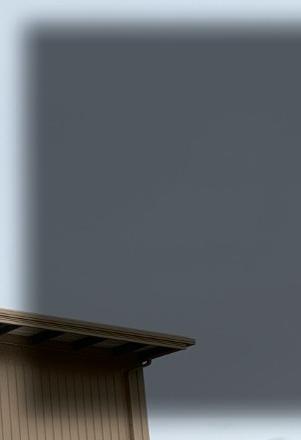

2 – 2022 RM100s IN STOCK
Attachments
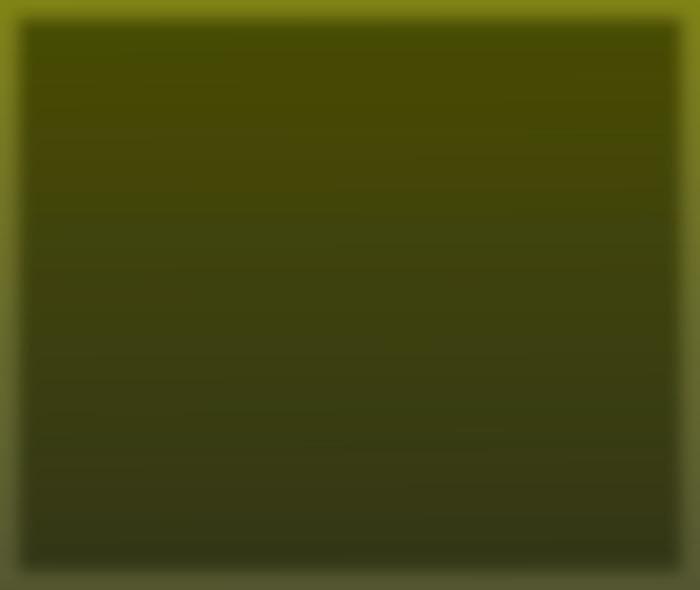