11 minute read
Top 5 Trends Driving Rail Forward
Next Article
TOP 5 TRENDS
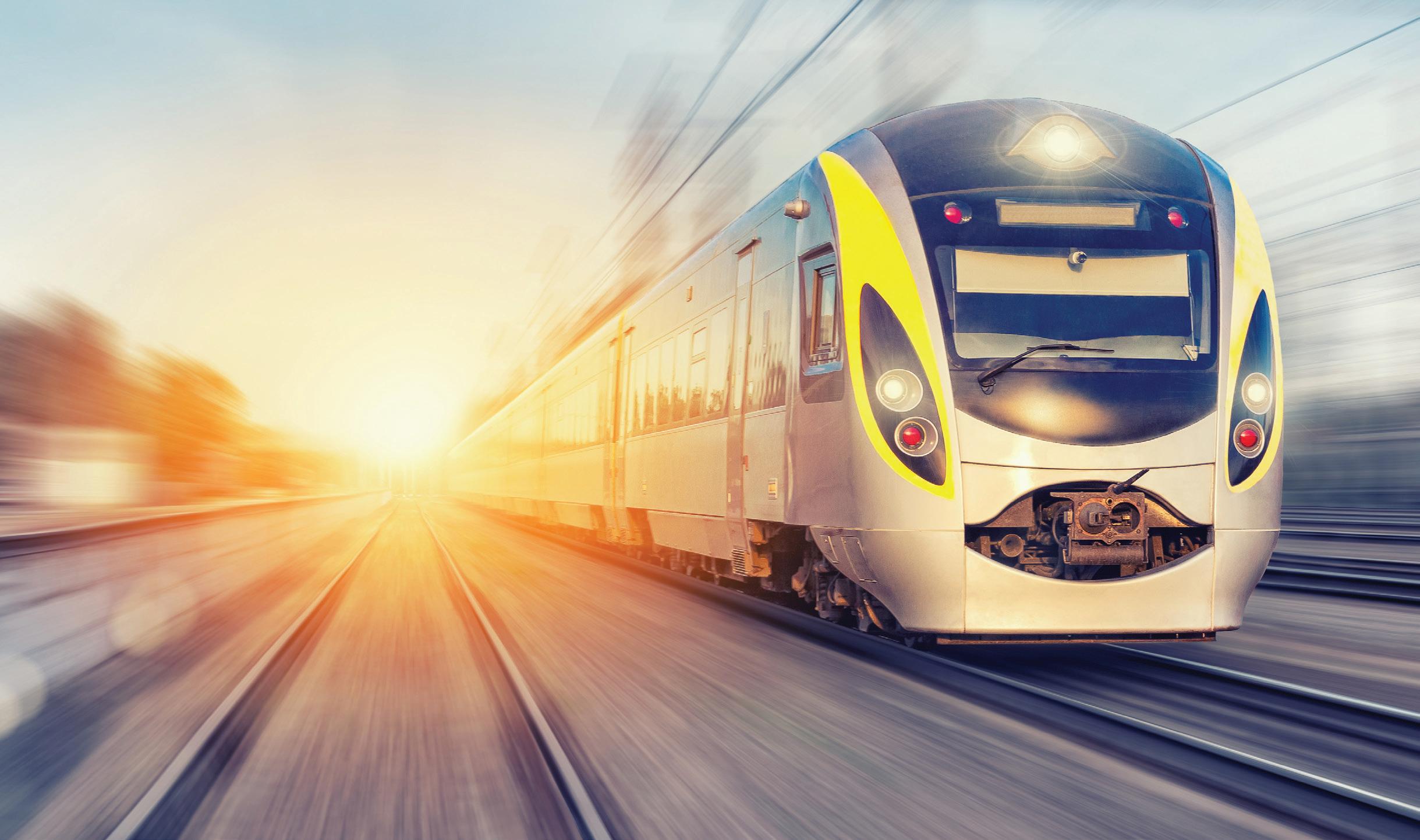
DRIVING RAIL FORWARD
For some time, rail remained the underdog in the transportation sector, taking a backseat to its trucking and shipping counterparts. But, when something like the Coronavirus disease (COVID-19) strikes, rail becomes the go-to solution for moving goods across the country.
Here are Top 5 trends and technologies driving the rail industry forward.
1. Visibility.
Being able to forecast and somewhat prepare for future supply chain disruptions is a key piece to the supply chain puzzle. That’s why many of today’s rail and intermodal providers are implementing supply chain visibility.
For starters, KALERIS launched Transport Analytics, a business intelligence offering to increase enterprise analytics across the rail supply chain. Transport Analytics visualization tools and dashboards help users analyze large data sets, aggregate key performance indicators (KPIs) and quickly identify and manage exceptions to improve asset utilization, inventory turns and productivity.
And, GS1 developed EPCIS for Rail Vehicle Visibility, a new GS1 application standard that allows rail stakeholders to leverage Electronic Product Code Information Services (EPCIS) to obtain complete visibility of rolling stock in realtime.
2. Technology and innovation.
The U.S. Department of Transportation, for example, developed the Automated Vehicles Comprehensive Plan to advance rail safety, promote collaboration and transparency, modernize the regulatory environment and prepare the transportation system for disruptions. As discussed in Food Logistics’ SCN One thing rail has been doing a lot of is Summit: Transportation session (foodl.me/ innovating. Whether it’s implementing wc9bwx), 42.9% of survey respondents augmented reality, holographic projection and 3D laser scanners to shipment visibility solutions, advanced fuel management systems and machine learning, the revival of rail involves everything high tech and Association of American Railroads (AAR) operating With a surge in imports and increased e-commerce demand, intermodal smarter. continues its streak of monthly year-over-year gains.
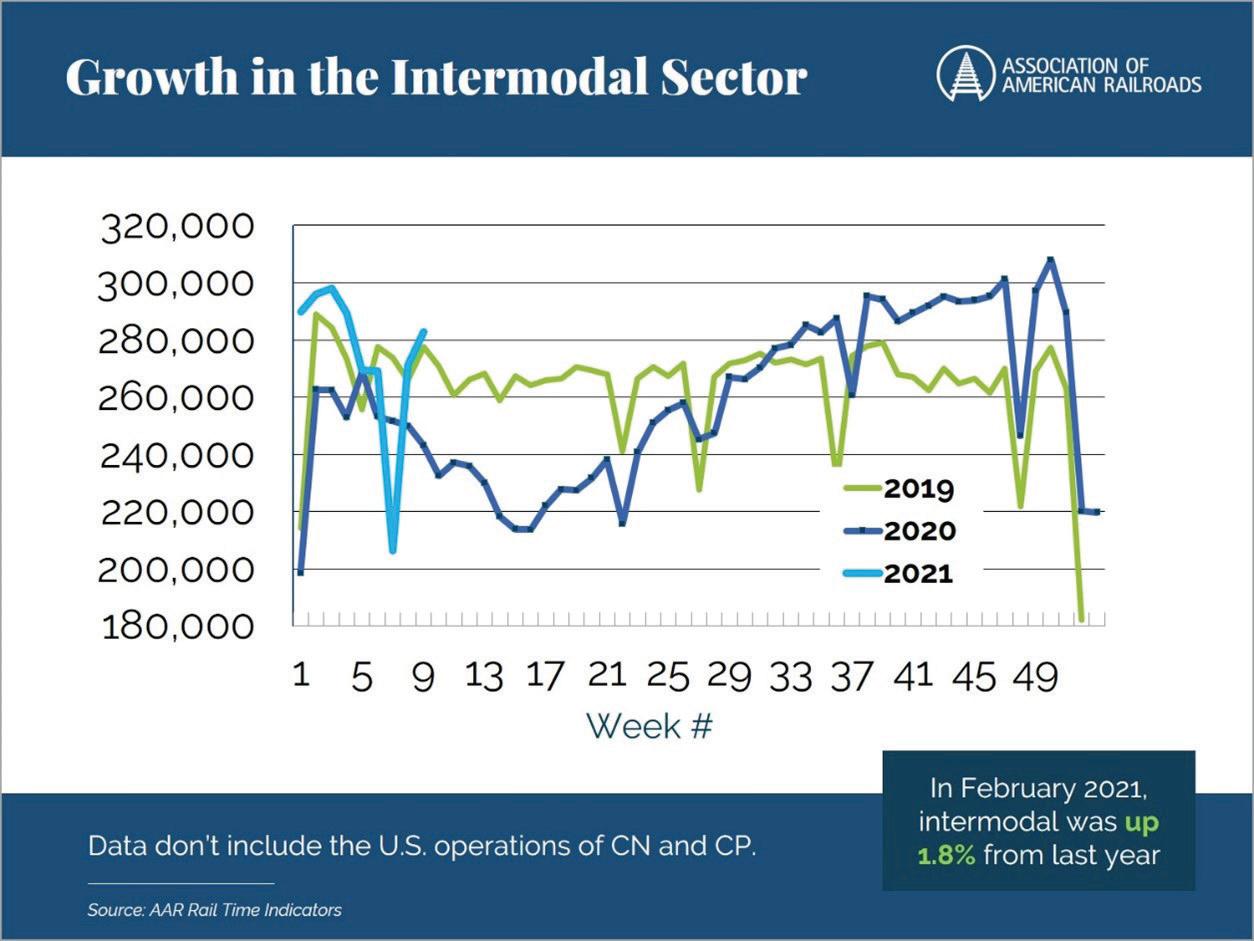
Despite the COVID-19 pandemic, rail and intermodal continue to operate as sustainably as possible.
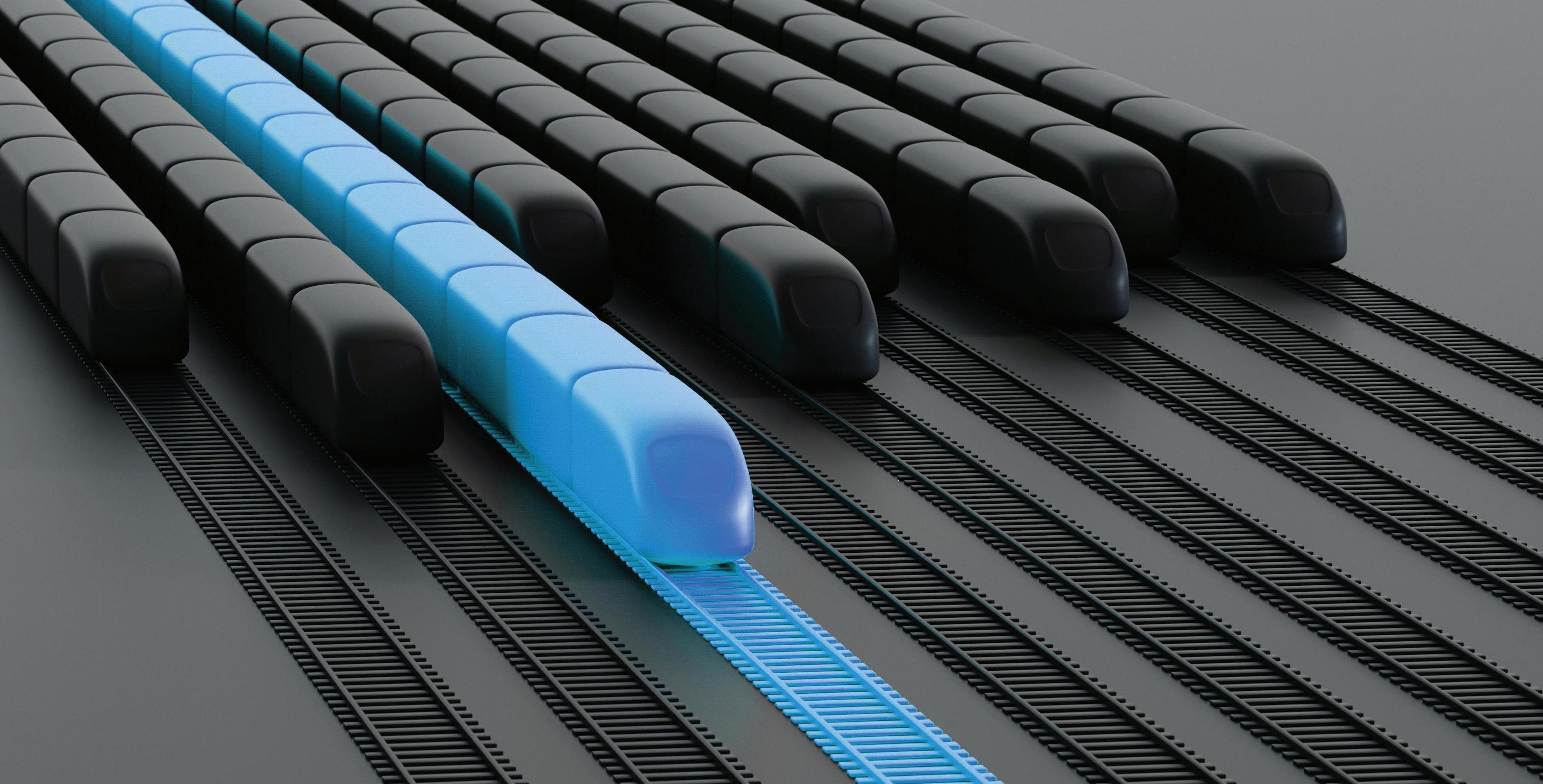
@tostphoto - adobe.stock.com
are investing in Internet of Things (IoT) to optimize their transportation supply chain, while 14.3% are investing in automation.
“Widespread deployment of new technologies like Positive Train Control (PTC)—strategically designed to address human error—are opening an exciting new era of safety and efficiency improvement for U.S. freight railroads,” says Luisa Fernandez-Willey, assistant VP, policy and economics for Association of American Railroads (AAR). “The nation’s largest railroads, known as Class I, successfully met the congressionally mandated deadline to have PTC fully operable by the end of 2020. Today, PTC is fully implemented and in operation on 100% of Class I PTC route-miles network wide.”
3. Sustainability
Despite the COVID-19 pandemic, rail and intermodal continue to operate as sustainably as possible.
For instance, railroads already have deployed advanced fuel management systems, giving locomotive engineers real-time power and speed recommendations to improve fuel efficiency up to 14%, Fernandez-Willey says.
“Improved rail car designs and distributed power (placing a locomotive in the middle or rear of a train) reduce the horsepower needed to move a 125-car train. Additionally, some railroads are also testing potentially game-changing technology such as battery electric and hydrogen fuel cell locomotives,” she adds. “Preserving the environment and combatting climate change is a responsibility railroads take seriously. Thanks to targeted investments, innovative technology and evolving operations, railroads are the most fuel-efficient way to move freight over land. In fact, one train can move 1 ton of freight more than 470 miles on 1 gallon of fuel, on average.”
Ward Proctor, director, business solutions for Railinc, adds that freight rail is the most efficient and sustainable way to transport goods across North America.
“With just 1 gallon of fuel, a ton of freight can be moved more than 470 miles and less than 1% of all U.S. greenhouse gas emissions come from freight railroads,” he adds. “Railinc’s visibility products enable adoption of fuel-efficient rail by a broad spectrum of shippers who require a high level of supply chain visibility when moving perishable shipments or products that must be protected from tampering or contamination. With enhanced visibility through Railinc’s RailSight Suite, shippers can confidently choose rail as a sustainable shipping option.” For its part, Schneider announced a new set of corporate goals in achieving a sustainably-focused culture. These goals includes a commitment to reducing carbon emissions by 7.5% per mile by 2025; a commitment to doubling Schneider’s Intermodal size by 2030, thus reducing carbon emissions by an additional 700 million
pounds per year; and a commitment to achieving net zero status for all company-owned facilities by 2035, among others. “Schneider has committed to the future of fl eet electrifi cation, making necessary short- and long-term investments such as testing electrifi ed powertrains, developing strategic zero-emission vehicle (ZEV) adoption plans and building relationships with key stakeholders and industry partners. The company has been piloting the use of an electric eCascadia truck by Freightliner in California for local and regional delivery and pick up,” says Craig Paulsen, VP, intermodal sales and marketing for Schneider.
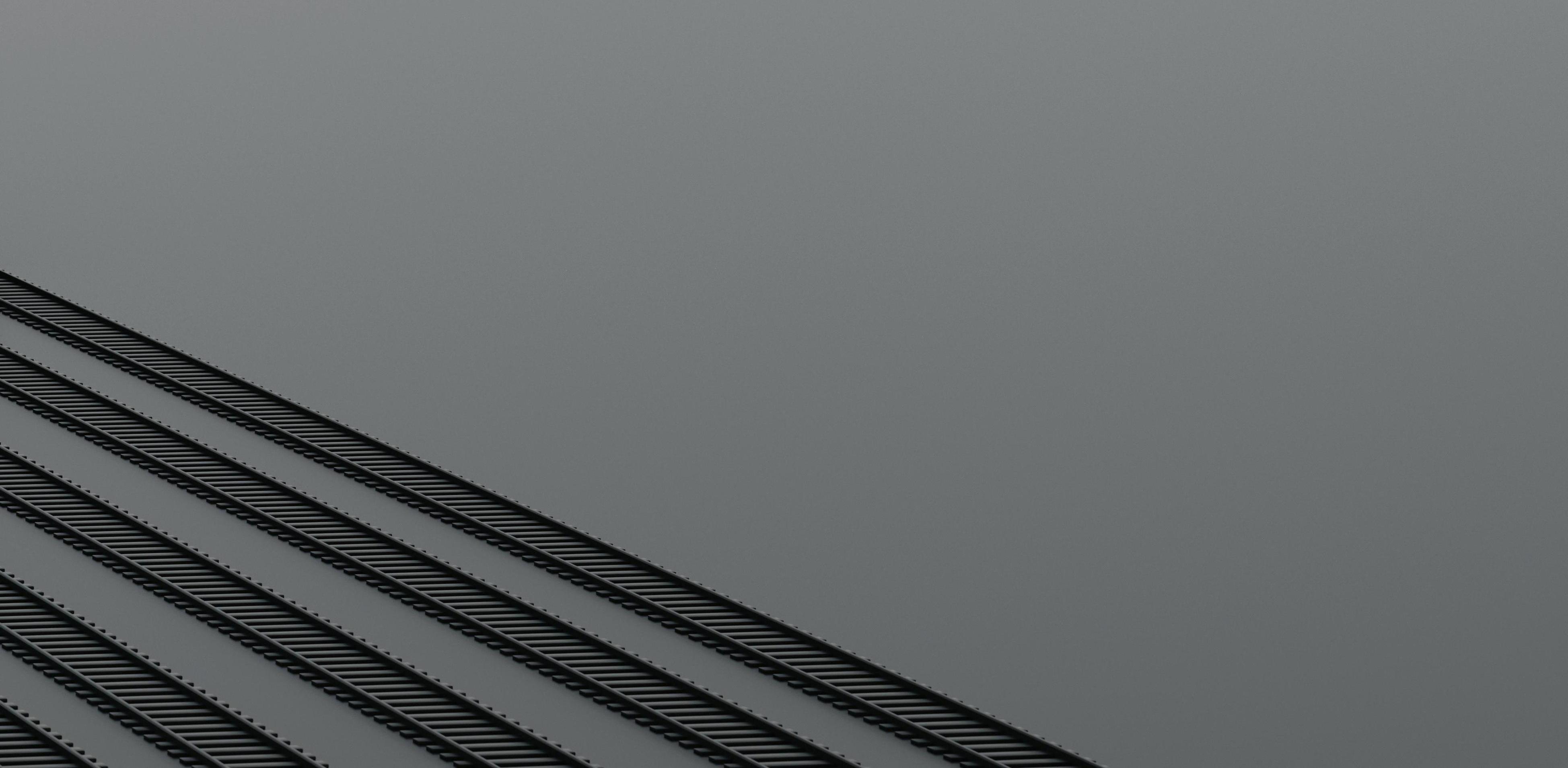
4. Real-time results.
Advances in rail shipment estimated times of arrival (ETA) make it possible for shippers to use both intermodal and carload shipments that provide essential time-to-market performance and reliability, Proctor says.
“The RailSight Suite of Applications provides more than 11 million daily shipment and equipment management events that enable 3PLs, equipment owners and other customers to easily plan operations and respond to issues,” he adds. “Railinc’s RailSight has launched a new advanced ETA service that utilizes machine learning to provide more reliable ETAs than what has been available. Using neural networks, the advanced ETA service now dynamically uncovers origin destination-specifi c patterns from Railinc’s event stream that can more appropriately account for the complexity required to predict arrival times. With the resulting signifi cant ETA improvement for both freight and intermodal lanes, shippers can better plan plant operations, manage inventory and inform customers.”
5. Intermodal makes comeback.
Total intermodal volumes rose 9.6% year-over-year in the fourth quarter of 2020, according to the Intermodal Association of North America’s (IANA) Intermodal Quarterly report. Domestic containers gained 8.7% year-over-year 2020; international shipments, 9.4%; and trailers, 17.5%. “Intermodal continued its comeback in the fourth quarter after declines in the fi rst half of the year,” Joni Casey, president and CEO of IANA said in a press release. “Against the backdrop of COVID, all market sectors posted gains, setting the pace into at least Q1 of 2021.” Intermodal also hit record-breaking levels in November and December 2020 due to imports and increased e-commerce demand and businesses re-stocking inventory, says Fernandez-Willey.
“Once the economy re-opened by mid-2020, we saw recovery across many carload categories and intermodal,” she adds.
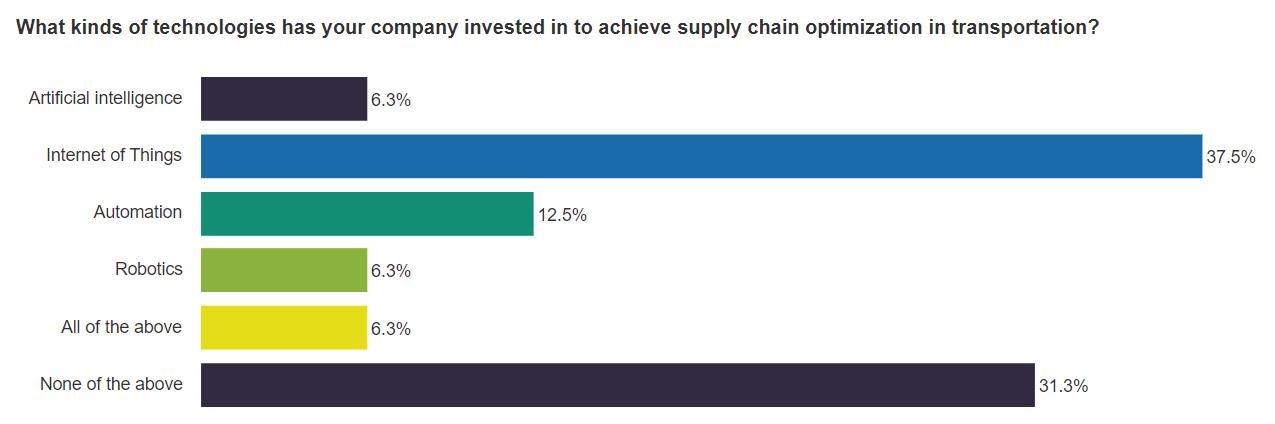
As discussed in Food Logistics’ SCN Summit: Transportation session (foodl.me/wc9bwx), 42.9% of survey respondents are investing in Internet of Things (IoT) to optimize their transportation supply chain, while 14.3% are investing in automation.

FREIGHT TECHNOLOGY:
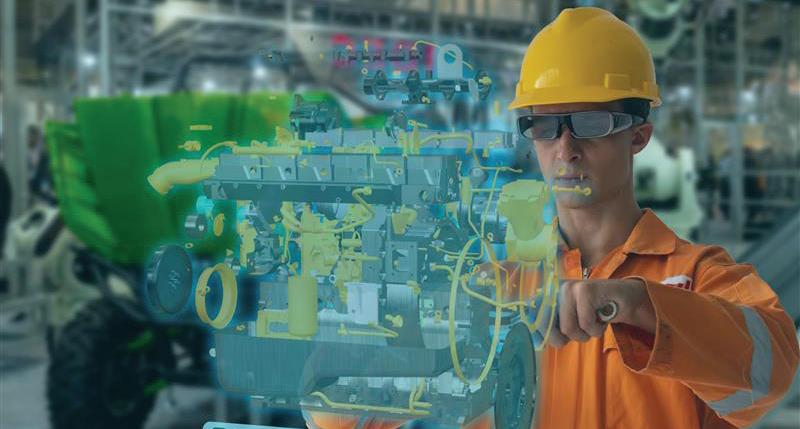
HOW EMERGING TECH IS RESHAPING THE LOGISTICS INDUSTRY
@monopoly919 - adobe.stock.com
For decades, the logistics industry has relied on a core, largely consistent set of methodologies and tools to manage supply chains, people and communications. From phone calls and emails to good old pen and paper, as much as freight has changed over the past decade, many of its processes still rely on analog solutions. The idea that a multi-trillion-dollar industry rests on the shoulders of largely outdated processes is concerning. The truth is, there are a lot of moving parts in logistics, and while these processes are tried-and-true, they are quickly losing their place in an industry that demands effi ciency.
So, what are the alternatives?
To be honest, there aren’t as many substitutions as there are replacements. Companies are quickly beginning to revamp their supply chain’s effi ciency by means of new technology and operational models.
The integrated freight marketplace
The last few years have seen phone calls and email chains replaced by algorithms and digital platforms. Waiting hours for a call or a confi rmation email wastes time, resources, and ultimately, money. More and more logistics professionals are looking for ways to automate away those rote tasks while simultaneously creating a more coherent communication stream across the entire supply chain.
As evidenced by the mass Coronavirus disease (COVID-19) disruptions and the more recent Suez Canal incident, being able to respond to delays in real time is not just convenient, but critical, for modern logistics.
Digital marketplaces are helping move the needle for both data sharing and transactions. By consolidating parties onto a single platform, it’s easier to connect shippers and providers more directly and in real-time.
What is a managed marketplace?
Managed marketplaces are online portals that help shippers and carriers connect via a live, interactive platform while providing the background operational support of a more traditional brokerage.
Marketplaces allow for: · Shippers to fi nd carriers to move their product. · Carriers to fi lter through loads from multiple sources. · Real-time pricing and capacity. · Customer-carrier matching. · Online support.
This means that carriers no longer need to make multiple phone calls to fi ll their trucks or get details on a specifi c load. It can also help reduce their empty miles and improve overall effi ciency.
For shippers, marketplaces provide access to a large network of carriers and an easy way to intake bids. Because the marketplace is managed, the carriers are all fully vetted, and in some marketplaces, scored based on service. This means that shippers can enjoy the volume of carriers offered on a traditional load board, while still having the peace of mind provided by a more carefully cultivated pool of drivers.
Integrations have become a popular feature of transportation management systems (TMS) as well as managed marketplaces. Rather than having to learn how to use a new platform, many businesses are now able to integrate these new tools and features into their current TMS and existing portals.
Integrating enhancements into pre-existing platforms creates a shorter learning curve and speeds up adoption for users. This translates into less time fi guring out how to use something and more time actually using it.
Tracking and visibility
One other feature some platforms offer is real-time tracking, which brings invaluable visibility to shippers. Drivers are spared the hassle of reporting their location and ETAs while shippers can regularly check in on their freight’s location whenever convenient. This is particularly useful and arguably necessary when transporting goods cross-border.
The case for cross-border technology
Mexico is notorious for being a region where freight can become lost or unheard of until it arrives at its destination. Known as the “black hole” of freight, Mexico does not have the same ELD regulations as the United States or Canada. A cross-border shipment is a multi-party process with numerous handoffs on both sides of the border. A typical Mexico-U.S. northbound shipment can involve up to six people just to effectively communicate a truck’s location: 1. The driver 2. The dispatcher 3. Mexican fl eet manager 4. U.S. fl eet manager 5. Logistics provider 6. A rep from that same provider This same group of people would be responsible for communicating location on a southbound leg as well. What you get are hours of waiting and multiple phone calls before a shipper knows where their freight is. By that time, the location has already changed. This wastes time and money, can create freight safety concerns, and ultimately, hinders a supply chain’s effectiveness. By taking a proactive approach at utilizing tracking tools, shippers and carriers can improve visibility and ultimately profi t by maintaining a tighter grip on their freight and minimizing the parties involved in their cross-border supply chain.
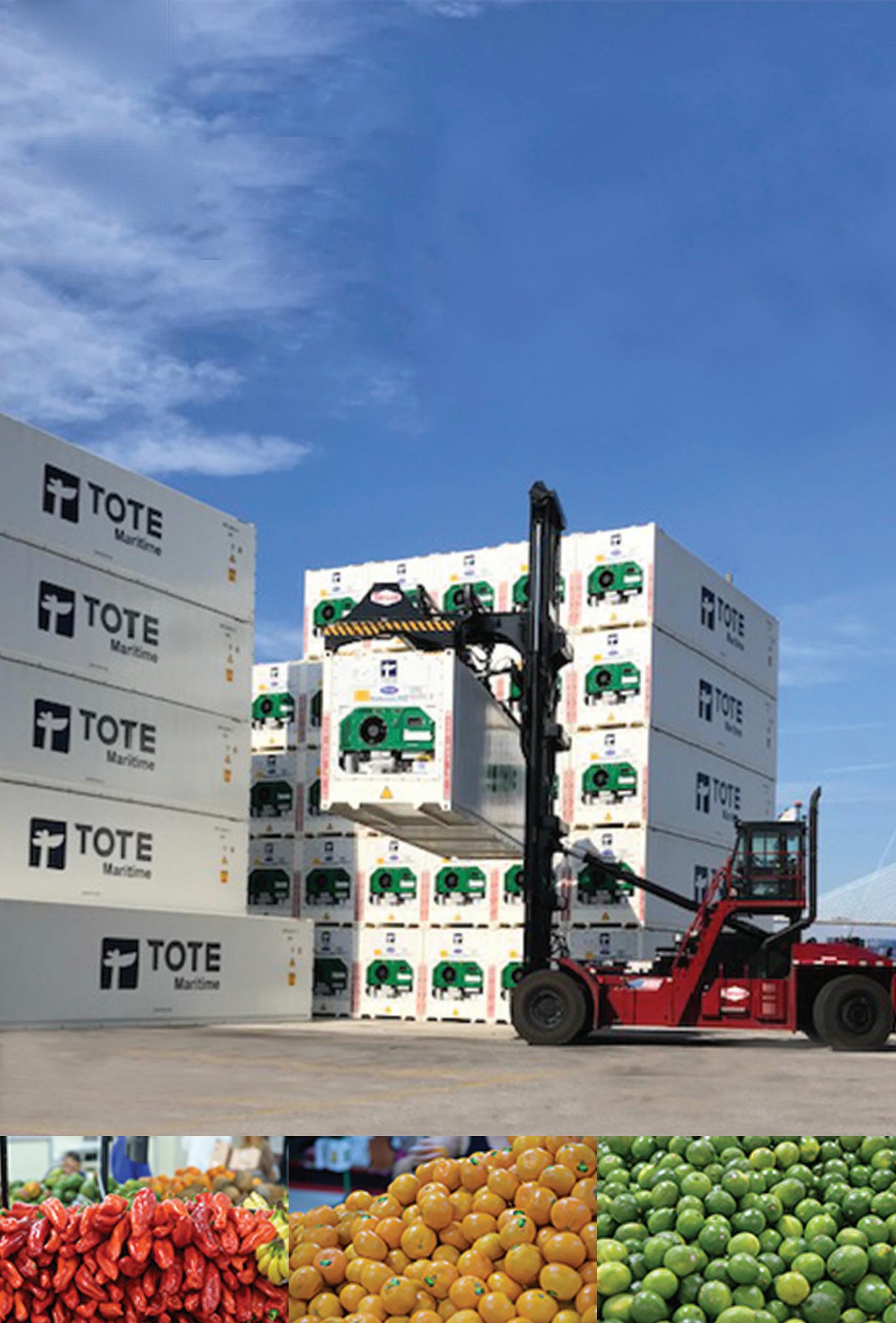
Technology adoption in the age of pandemics
Many of these tools and platforms have existed for a few years, but the arrival of the COVID-19 pandemic has accelerated the need for their utilization.
When the pandemic hit, leaky and infl exible supply chains broke down. Many companies were left scrambling to rebuild while fi ghting for capacity or attempting to relocate production out of China. Digital supply chains were able to respond to the crisis and adjust their operations more quickly and easily. Some were able to leverage their tech adoption to meet demand and even grow. The collapse of many small companies, the disruption of markets and the fi nancial burdens that came from the early days of the pandemic gave the logistics industry a very clear message—adapt or die.
Whatever the next crisis is, companies are more likely to survive (and even fl ourish) if they are willing to leave the pen and paper behind.
ABOUT THE AUTHOR
CHRISTIAN GUAJARDO digital marketing specialist,
Forager Group Inc.
DEDICATED. RELIABLE.
BUILT TO SERVE
TOTE specializes in shipping temperature-controlled cargo across the sea using our best in class technology which includes NaturaLINE® and CoolConnect. Our smart refrigerated containers and longstanding expertise in handling both fresh and frozen cargo makes us the best in the business for handling your refrigerated goods.