7 minute read
Shipyard waste
Next Article
Should shipyard waste be added to shipping’s carbon footprint?
It’s remarkable how much wastage and emissions goes into building a vessel. Sooner or later this will come into the spotlight
Although the majority of carbon emissions from shipping currently occur during a ship’s operational phase as a result of fuel combustion, the industry’s decarbonisation is expected to shift this balance, with carbon emissions from components, building, and recycling accounting for a larger share of a vessel’s total lifecycle emissions.
Lifecycle assessment is a technique to assess environmental impacts associated with all the stages of a ship’s life, from raw material extraction through materials processing, manufacture, waste, running life, repair and maintenance, and recycling.
Nicolas Duchene, chief operating officer and vice president at French carbon emissions verification company Verifavia Shipping, observes that more and more people and organisations are interested in the carbon footprint lifecycle, well-towake emissions and carbon intensity aspects of transporting cargo.
“The all-inclusive carbon emissions from ships, not only from operations but also design, construction, repairing and recycling, is an emerging issue for institutions, organisations and sectors regarding carbon-neutral growth,” he says.
Shipbuilding is known as one of the hardest metal industries with several chemical and hazardous material exposures and is termed as a high energy, high material consumption, and high pollution industry. The whole process is said to be responsible for more greenhouse gas (GHG) emissions than ship repair and recycling combined, with emissions from steel production at the top of the ladder accounting for nearly 90% of the total CO2 emissions.
The industry aims to build cleaner vessels, and it is likely that this trend will continue. The term “green shipbuilding” has been used for a while, wherein in addition to designing more “eco-friendly” ships, shipyards should ensure the high efficiency of materials and energy in shipbuilding, reduce harmful emissions and smooth the process of integrated hull construction, outfitting and painting.
However, Karl Rugen from Worldwide Marine Technology argues that the vast amounts of construction waste involved with the entire shipbuilding process should also be considered.
“Even well-run shipyards in Korea and Japan have dozens of containers filled daily with massive piles of scrap cuttings, plastic, wrappings, wood and packaging, rubber, caballing, paint cans and on and on and a large portion of which is not recyclable and therefore taken to landfills, he observes.
When contacted by Splash Extra, a spokesperson for the International Maritime Organization said: “I am not aware of this being raised at IMO so far, so we cannot really give a comment or opinion.”
Petter Heier, the former head of Norwegian green recycling consultancy Grieg Green and now founder and CEO of maritime life cycle services firm Calmocean, believes that when it comes to shipping’s carbon footprint, newbuilding, repair and recycling activities should also be part of that and not only waste disposal.
“The entire carbon footprint for the construction, repair or recycling of a vessel should be calculated. It is, of course, about the waste generated but also the processes that are used, which can have a very different impact on the environment,” he stresses.
Shipbuilding has been growing fast, but a huge volume of energy, waste and pollutants being released during the construction of vessels poses a major risk to human health and the environment that could add further pressure on shipowners and the industry in general to clean up its act and take action.
Comparing shipbuilding with never-ending discussion around producing e-cars and the overall environmental effect, Henning Gramann, the CEO and founder of ship recycling consultancy GSR Services, points out that much
more energy and raw materials are required for building a ship.
“A lot of steel is required, which then has to be connected by kilometres of welding lines. Most of us know how this smells and then the paint job comes on top. Not all is CO2, but there are many more emissions that must not be forgotten. Light, noise, gases, liquids and solids, not to forget the wastes caused during ship construction,” he points out, asking: “Should all these be added to shipping’s carbon footprint as well?”
A study published in the International Journal of Global Optimization and Its Application finds that the waste in the production process occurs without the company’s realisation because it is not considered a cause of significant losses. Meanwhile, the emergence of operational cost components that are not needed in the production process is due to the company’s inability to control waste in the production process leading to suboptimal productivity and cost-efficiency in shipbuilding, the study said.
Steen Lund, CEO of shipping risk management organisation RightShip, reckons that while this is an issue to be tackled by the right industry owners, he would encourage a larger debate around the lifecycle analysis of vessels inclusive of building, operating and scrapping vessels.
For Lund, waste at shipyards would be a subset of that transparency, while the end-to-end lifecycle assessment would span not only that “relatively small” element but many more complex aspects contained within recycling standards.
“The circular economy would demand a far wider review of recycling opportunities held against newbuildings versus extending the lifespan of an existing vessel, that at the face of it might emit more than a newly built vessel, but when assessed in totality for its cradle to grave and back into usefulness via recycling might have a different lifecycle emission than first meets the eye,” he tells Splash Extra.
The topic of newbuild waste came up at this month’s Maritime CEO Forum held at the Monaco Yacht Club. Danilo Fumarola, CEO and chairman of Gestion Maritime, said that extending the life of existing ships makes the most sense as 40% of the emissions of an entire lifecycle come at the newbuilding stage.
Chris Waddington, technical director at the International Chamber of Shipping, agrees that life extension will be an option that some shipowners may take up, as this will be driven both by the GHG regulations, and also economic considerations.
In many cases repairing is more sustainable and saves resources than purchasing new. This has been ignored more and more in the last decades, GSR Services’ Gramann also believes.
Additionally, in Monaco, Michael Parker, chairman of global logistics, shipping and offshore at Citi and the main man behind the Poseidon Principles, noted that shipbuilding comes under the domestic contributions countries emit, but he reckoned IMO will be looking at it soon, while Alan Hatton, CEO of Foreguard Shipping, said that when it came to energy used to build new ships - “we need to be looking at the entire lifecycle.”
Calmocean’s Heier acknowledges that, from a general perspective, the longer a ship can trade, the better it is from a financial and environmental perspective. But in saying that, he indicates that the equation is not that simple when it comes to the environment. “It is crucial to measure the total impact of the entire value chain in order to be able to compare,” he says.
Gramann adds that forecasts see many ships heading for the torch due to new emissions requirements, which will need to be replaced with new, more environmentally friendly and efficient ships to ensure sufficient transport. Still, despite many different approaches showing positive results when looking at emissions per ton-mile, daily fuel consumption, fuel used and so on, he questions the overall equation.
He warns that whatever we do causes disturbance and emissions. “We´re still far away from an environmentally harmless economy and style of living. When we want to change for the better and most urgently protect the climate, we need to consider the whole lot, including how and what we produce.”
As shipbuilding is a very complex activity and requires high standards, scientists at the School of Environmental Science in Jakarta, Indonesia suggested in a recent study that shipyards should collaborate with the community in managing production waste to be reused by providing training related to waste management.
Chief executive of class society Lloyd’s Register, Nick Brown, feels that all maritime stakeholders should be aware of the overall carbon footprint over which they have influence.
Verifavia’s Duchene asserts that usually only direct emissions (scopes 1 and 2 of shipping’s carbon footprint) are considered, but lately people have realised that some sources of emissions under scope 3 must be included in carbon neutrality targets.
The surplus of emissions because of scrapping old or designing new ships (scope 3) is difficult to estimate and compare to scope 1 reductions, as it relates more to a lifecycle approach.
“This is a complex topic in its infancy and we are at a pioneering stage, where there is no legal requirement or standard associated with it,” he says.
It’s something that industry leader Maersk has recently taken action on. Earlier this year the Danish carrier joined SteelZero, a global initiative to procure, specify, or stock 100% net zero steel.
Maersk has committed to using 100% net zero steel by 2040, with an interim target of using 50% responsibly produced steel by 2030, something well ahead of the curve for shipping. Others will have to follow sooner or later. ●
Flagship makes return to Monte Carlo
October saw shipping’s version of Davos making plenty of headlines from the Monaco Yacht Club
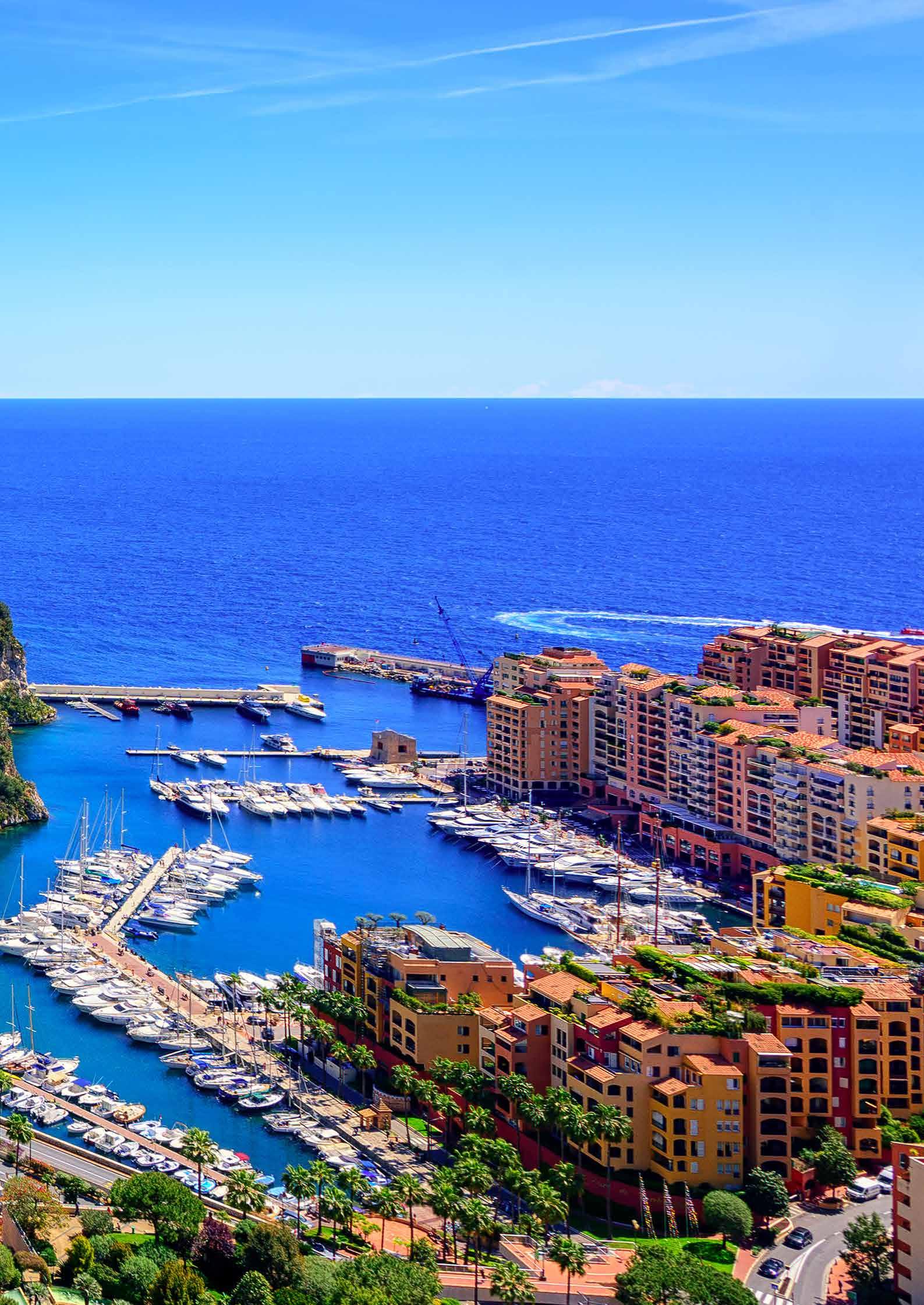