5 minute read
PROJECT PERFORMANCE Energy intensity (building and process energy) = 94KWhr/m2/year Energy intensity reduction relative to reference building (under NECB 2011
Next Article
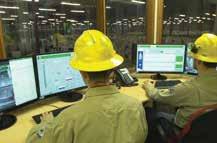
Jeff Gold of Nexus Circular LLC
Jeff Gold is the COO/founder of Nexus, the leading circular waste-plastics solution company based in Atlanta that converts landfill-bound plastics to reusable plastics. nexuscircular.com
4. What have been the challenges you have encountered?1. What does Nexus do exactly?
Nexus converts waste plastics that are typically bound for a landfill or incineration into chemical feedstocks that are used to create new, virgin plastics. We take the polyethylene, polypropylene, and polystyrene that cannot be economically recycled through mechanical systems and transform them into valuable liquids and waxes that our partners use to create a huge range of new plastic products. Our process is very energy efficient and by directing our output into new plastics versus fuel products that are burned, we sequester the carbon in those plastics and prevent their entry into the environment as harmful greenhouse gases.
2. How does the waste plastics conversion work?
Nexus uses a process known as pyrolysis, or “thermal depolymerization” to transform waste plastic back into its basic molecular forms. This process works by applying heat to the plastic but excluding all oxygen so that instead of burning, the plastic simply liquefies and decomposes into a variety of hydrocarbon molecules. Most plastics are made of long hydrocarbon chains and pyrolysis provides a way to “cut” those chains into smaller pieces that become liquids or waxes once they are cooled. It is these liquids and waxes that can then be used in the industrial systems that make new plastic resins.
3. Is the conversion process truly a ‘closed loop’?
We consider our process to be “closed loop” because all the plastic that goes into the system is converted into a new product that is captured at various points in the system. For example, most of the incoming plastic is converted to liquids and a wax product that is collected and shipped off directly to our off-take partners. The process also produces a flammable gas that we likewise capture and then use to heat the pyrolysis reactors. A fourth product that results from the process is a carbon-black char material that forms in the reactors from small amounts of paper and cardboard that are mixed in with the plastic feedstock and from normal decomposition of plastic when it contacts very hot surfaces. This char is collected and can be used as an asphalt additive. In this way, all the products formed from the plastic feedstock are converted, captured, and used in some way making the process truly closed loop.
Converting waste plastic at a commercial scale into useful products and doing so economically is very hard.
The principle technical challenges we have encountered revolve primarily around feedstock in terms of collection, contamination, and composition. The challenge has been to create a highly adaptable system that can accept a wide variation of inputs and produce a uniform, consistent, high-quality output. Maintaining reactor performance in the face of a variable feedstock stream has also posed technical challenges around managing heat distribution to yield our desired products while minimizing energy consumption which is why we have taken all the learnings from our first plant and are now applying them to a third- generation design.
Another challenge involves proving that chemical recycling is a viable technology in the fight against plastic pollution. There have been numerous press releases and announcements by groups in the chemical recycling space touting a solution that fails to materialize and when this happens often enough, a perception is created that this is something that does not really work. While there is a lot of progress yet to be made, Nexus has shown that the technology can be effective and that it merits serious consideration.
5. What is the future? How far to do you see an operation like yours going?
We feel very optimistic about the future! We have a team in place that has built an innovative and economic process that addresses the pressing environmental issue of plastic pollution and we have proven that Nexus is one of the few companies that can deliver our product at commercial scale and consistent quality.
Demand for our products is extremely high as many companies work towards satisfying consumer demands to increase the amount of certified recycled content in their products and take positive steps to improve the planet’s environmental quality. Our challenge now is to scale the business at a rate that can keep pace with our customer’s needs, and to that end, we are working very hard to establish new locations both at home and overseas. Given that the use of plastics is expected to continue its upward trend over the next several,Nexus is poised to expand on its industry leadership position and play a major role in combatting plastic pollution for years to come.
PRECAST CONCRETE BUILDS ON...
PREFABRICATED MODULAR PRECAST CONCRETE WINDOW WALL SYSTEMS
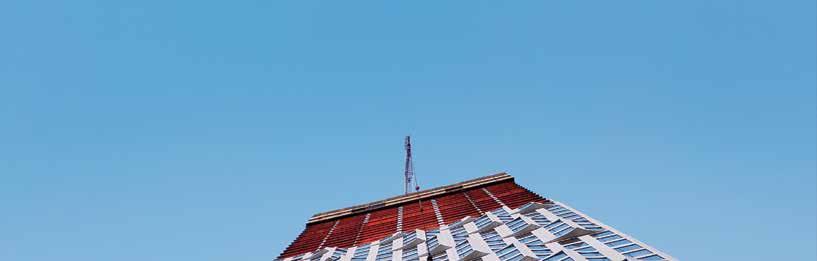
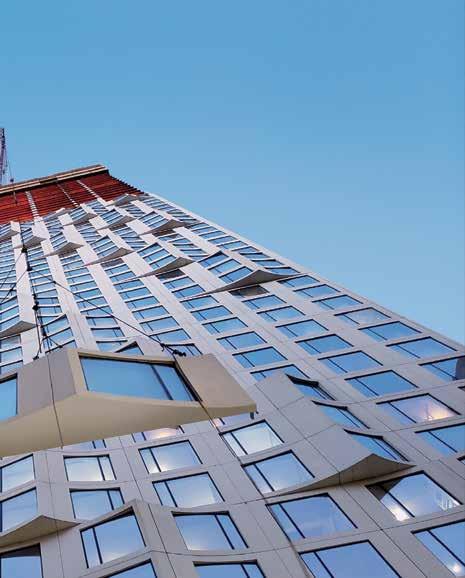
Prefabricated Modular Precast Concrete Window Wall Systems outperform other systems in:
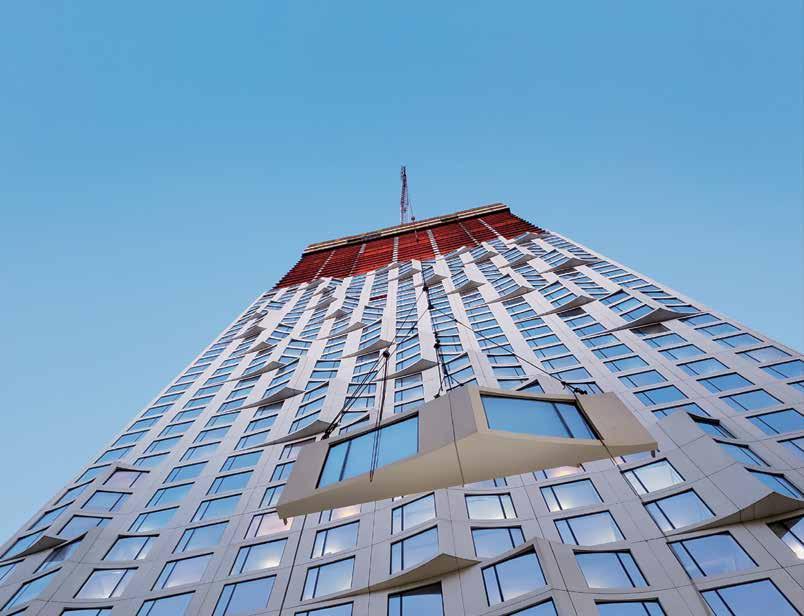
·Pre-assembled, caulked, vapour air tested windows are installed in the panel at the precast concrete facility which provides improved quality assurance. · The rapid installation allows the building enclosure to be completed sooner, giving the interior trades faster access to a more climate-controlled building and therefore ensuring the project is completed quickly and efficiently.
11 Hoyt, Brooklyn, NY | Architect: Studio Gang and Hill West | Photo: Guy Tremblay, BPDL, Quebec
PREFABRICATED MODULAR PRECAST CONCRETE WINDOW WALL SYSTEM ADDED BENEFITS:
• Prefabricated modular precast concrete construction provides significant improvements in terms of cost, schedule, quality, productivity, safety and the ability to reduce waste and increase client satisfaction with a quicker return on investment. • An unlimited array of architectural designs, colours and textures are available including heightened durability and lower maintenance costs.
For more information and educational courses, check out Learn on Demand, CPCI’s 24/7/365 interactive educational platform: cpci-learnondemand.com/ Visit www.cpci.ca/publications to download your free copies of the CPCQA Structural Solutions Technical Guide and High Performing Precast