
10 minute read
Decarbonizing cement30
The ReCover Initiative
A deep energy retrofit methodology to cut energy use and upgrade ageing buildings
Advertisement
By Emma Norton, Nick Rudnicki and Lorrie Rand
Nova Scotia has committed to aggressive reductions in greenhouse gas emissions, targetting a 53% reduction below 1990 levels by 2030, and net zero emissions by 2050. A recent report by Brendan Haley and Ralph Torrie states that existing buildings are responsible for 47% of Nova Scotia’s GHG emissions.
In 2030, more than 75% of the building stock in Nova Scotia will be composed of buildings in use today, and an estimated 60% of those buildings will still be in use in 2050. This means that existing buildings will have a large impact on meeting Nova Scotia’s emissions targets.
In light of these facts, the ReCover Initiative was established to develop a deep energy retrofit methodology for Nova Scotia that can be implemented at a large scale to reduce GHGs emissions from existing buildings.
Our team performed a pilot design, with the support of Quest Canada and the Nova Scotia Department of Energy and Mines, to demonstrate the potential reductions in energy consumption and GHG emissions through a deep energy retrofit of a low-rise MURB (multi-unit residential building) pilot building in Halifax.
Conventional methods of performing deep energy retrofits are slow and expensive, because every project is custom, as every building is unique. The ReCover Initiative is based on a systematic, turnkey approach to affordable deep energy retrofits, developed in the Netherlands, called Energiesprong (“energy leap”). The ReCover process involves wrapping the building in a new prefabricated skin and replacing the mechanical systems with smaller, more efficient components.
This work is faster and less disruptive than a typical renovation, and it allows for occupants to remain in their home throughout the work. Additionally, following a systematic process reduces risk to the contractor and reduces costs to the owner.
Low-rise MURBs are ideal candidates for the ReCover Initiative due to their compact size, simple form, and uniform window dimensions. In Nova Scotia, there are over 40,000 households in pre-1996 low-rise MURBs. Retrofitting these units to 75% improved efficiency, would save 1,500,000 gigajoules of energy and 140,000 tonnes of GHG emissions annually.
The ReCover Initiative is committed to promoting retrofit solutions that achieve reductions in both operational carbon and embodied carbon. This includes using building products made in Atlantic Canada. The best materials for making low-impact buildings can already be sourced locally but the supply of these products will need to increase to meet the demand from low-carbon retrofits.
1
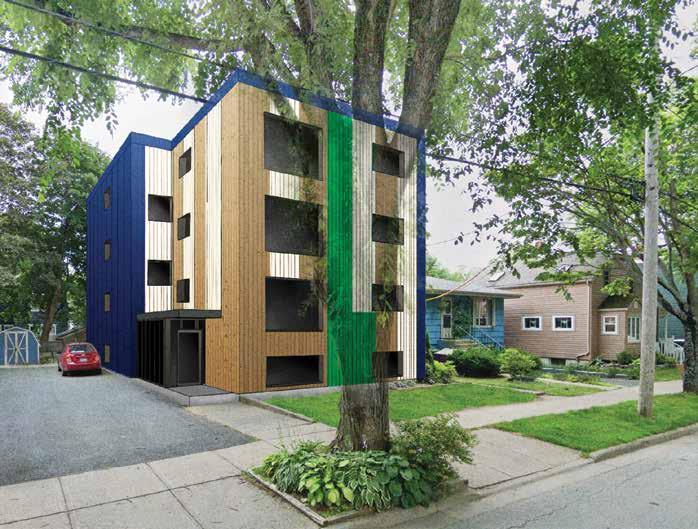
2
PROJECT TEAM
Emma Norton, Climate Emergency Unit Nick Rudnicki, RSI Projects CEO, Passive House-trained builder Lorrie Rand, Habit Studio President, Certified Passive House Designer Greg Hanlon, Smarter Spaces, LIDAR Scan and CAD Andrea Doncaster P.Eng, Andrea Doncaster Engineering, Structural Consultant Aaron Smith P.Eng, LEED AP BD+C, BEMP, M&R Engineering, Mechanical Consultant Liam Kidston E.I.T, M&R Engineering, Electrical Consultant William Marshall P.Eng, LEED AP, CMVP, WUFI modelling Jim Nostedt P.Eng, SEEFAR Building Analytics, Cost Analysis and Optimization Drawings RSI Projects
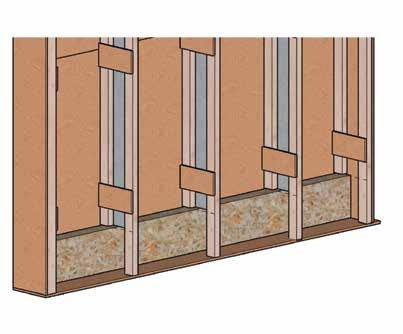
1. The building in its current state. 2. Rendering of the building after the ReCover process. 1 2
3 4
Wall panel schematic
1. 1/2” plywood sheathing - taped for air tightness 2. Double 2x3 studs, 24” o.c. - Filled with dense pack cellulose (not shown) 3. 8” wide 1/2 plywood gusset every 48” of height 4. Cellulose bib at each stud - 1/2” plywood sheathing on interior face of wall assembly (not shown)
THE PILOT BUILDING
The pilot is a four-storey residential building in Halifax, constructed circa 1980. Each floor consists of a two or threebedroom dwelling unit as well as common stairwells. The first floor also contains a garage space, laundry room and a mechanical room.
All spaces in the existing building are heated using hot water baseboard heaters served by an oil-fired boiler. Domestic hot water is heated through an indirect tank from the boiler water. The dwelling units are provided with cooling by mini-split heat pumps. These heat pumps are not currently operated in heating mode, presumably because they would increase tenant energy cost. Existing walls consist of brick cladding and 2x6 stud walls with batt insulation. Roof construction is 2x10 joists with batt insulation. Existing windows are double- glazed vinyl with sliding sashes.
The Covid-19 pandemic situation limited physical access to the pilot building at the time of the study, however, the team was able to develop an understanding of the building condition and current energy use. All assumptions have been documented and verification will occur in Phase Two when access to the building is less limited. The plan is to proceed with the pilot build, however, funds are not fully in place.
Performance targets were set as:
1. Air leakage maximum of 1 Air Changes Per
Hour (ACH) (Passive House retrofit target) 2. 25 kWh/m2 heating demand (Passive House retrofit target) 3. Net-Zero Energy Performance
Windows would be replaced with locally made triple-pane, PHIUS-certified units. The retrofit includes converting the garage to a fitness room and replacing the garage door with a window.
The three options considered for the insulated panels to the above-grade walls and the roof were:
1. EPS panel with plywood nail base (walls and roof), with metal siding 2. Larsen truss wall panel, TJI roof with cellulose insulation, with wood siding (option chosen) 3. Prefabricated metal panels with mineral wool insulation (walls and roof)
All options include the addition of three inches of rigid insulation to the exterior of below grade walls, and we made the assumption that the envelope improvements would meet the airtightness target of 1.0 ACH.
Options considered for replace the oil-fired boiler were:
1. new electric baseboards 2. an electric boiler (option chosen) 3. hot water heat pump + electric back-up boiler
The photovoltaic (PV) system planned has a capacity of 24.19 kW DC using 59 410 W modules and producing 25,233 kWh/year.
KEY FINDINGS
1. By investing about $350,000 to undertake a deep energy retrofit, including PV modules, to achieve the Net-Zero Energy level, the net Total Cost of Building Ownership (TCBO) could be lowered by $1,532,000 or 38% over 60 years.
2. The Deep Retrofit without PV modules did reduce the TCBO, but not as much as with PV modules. This highlights the need for all three components to be part of the solution: a deep energy retrofit to reduce the building energy load and improve building durability, electrification to reduce GHG emissions, and solar generation to achieve Net-Zero Energy consumption.
3. By shifting the analysis goal to optimizing owner investment with energy and GHG emissions reductions, the project becomes sustainable financially and environmentally. Lower TCBO is a significant factor for encouraging investment in Deep Retrofits.
4. Using a TCBO approach, like the SEEFAR-Valuation©, at the beginning of the project will help to optimize the design, minimize the TCBO, and generate high-quality input data for the analysis.
5. Since utility costs are a major driver of TCBO, doing the full retrofit all at once, instead of incrementally over time, results in larger savings. Not factoring operational/utility costs into capital planning can present a large financial liability.
6. Maintenance and renewal, property tax, and energy are big cost drivers for the TCBO.
Panel: 1/2 standard plywood Seams taped to air tight Panel: 2x3 studs with 1/2 plywood gusset
Weatherresistant barrier Panel: 10” dense pack cellulose Panel: 1/2 plywood interior face Existing basement walls Interior of foundation wall Additional insulation assumed
Existing 1/2 drywall
Existing basement walls 2x4
1x4 strapping
Pre-finished od siding Existing fiberglass batt 5.5 inches thick Existing vapour barrier
Existing 2x6 framing Existing basement walls 1/2 drywall
Bug screen
Existing soil
Wall Panel - Foundation connection exploded view

3” EPS insulation all the way down to footing New water proofing membrane for foundation wall Existing 10” foundation stem wall
Air barrier membrane adhered to foundation wall brackets mounted to it taped to new panel to continue air barrier
1/2” Dens Glass sheathing
Liquid-applied roofing membrane
Roof to wall flashing
Siding trim - crown frieze board Wall panel - 1/2 Plywood - Flange that extends past end of wall panel - Attachment point between wall and roof panel
Roof panel - 1/2 plywood at eaves end of panel - Air-Seal taped to underside of panel - Then taped to flange of wall panel
I joist
1x4 strapping as rain screen
Weather-resistant barrier
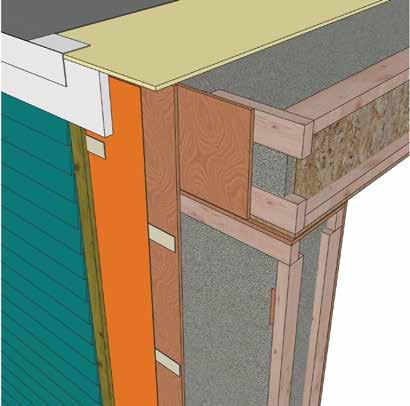
Pre-finished wood siding
Roof panel 1/2 plywood seams taped for air tightness 1/2 plywood gusset for double stud
2x3 double stud
Wall panel 1/2 Plywood
10” dense-pack cellulose
Wall to Roof Panel Connection Detail
1/2” exterior plywood taped at seams
FINANCIAL SUSTAINABILITY
The Energiepsprong program in the Netherlands is successful because it includes a comprehensive funding model that delivers Net-Zero homes at no extra cost to the owners. Innovative financing structures will likely be needed to influence property owners to ReCover their buildings.
The TCBO analysis for the pilot building shows that completing a deep retrofit will save the owners $1.5 million over the life of the building, cutting the cost of ownership nearly in half. However, the savings are not reflected in the owners’ cash flow for 25 years, which may be a disincentive. But, over time, the ReCover process will become faster and less expensive.
In the immediate future, the need for new buildings and added density must be balanced with carbon storage needs that benefit the environment. Building owners must be encouraged to renovate rather than rebuild, and where that is not feasible, salvaging and reuse of timber must be promoted to prevent the release of stored carbon in wood that is sent to landfill.
As for current status, RSI Projects has set up a panelization facility in a warehouse space in the Halifax Dockyard and refined the panel design and assembly process. It is now installing the panels on a building as a smaller test before the real deal. We also have only half of the funds committed to complete the work on the pilot building.
Implementation of a repeatable deep retrofit system, such as the ReCover Initiative, will make retrofit projects more desirable to builders and reduce the financial and technical risks. Details, research, and lessons learned will be shared in an open-source library, to support the community in undertaking deep energy retrofits.
Emma Norton is with Climate Emergency Unit; Nick Rudnicki is CEO RSI Projects and a Passive House-trained builder; and Lorrie Rand is president of Habit Studio and a Certified Passive House Designer.
The IDEA and Design Buildings were recently awarded first place worldwide in the Educational Facilities — New category at ASHRAE’s 2020-2021 Technology Awards, an international competition celebrating energy efficiency and sustainability in building design.

Our 2021 Partners
SITE | LANDSCAPING | RAINWATER HARVESTING
ACO Systems Molok® Deep Collection™ System Roth North America Wishbone Site Furnishings
STRUCTURE & EXTERIOR ENVELOPE
475 High Performance Building Supply Architek SBP Inc. Arriscraft Building Stone CBC Metals and Processing Fraser Wood Siding LiveRoof NATS Nursery Ltd. Radon Environmental Thames Valley Brick & Tile
THERMAL, WINDOWS & DYNAMIC GLASS
Cascadia Windows & Doors Duxton Windows & Doors ENERsign Windows+Doors Inline Fiberglass Ltd. Innotech Windows + Doors Kohltech Windows & Entrance Systems JELD-WEN Windows & Doors LiteZone™ Insulating Glass Pollard Windows Inc.
Dynamic Glass
SageGlass
YOUR LEED v4.1 QUICK-REFERENCE
Visit our on-line Directory to see hundreds of listings of companies which supply products and services for sustainable, high-performance building. Listings are organized by Product Category and by LEED v4.1 Category. Our LEED v4.1 Directory is created with the help of our partner:
COATINGS AND INTERIOR
Artech Ceiling Specialties CBR Products Dulux/PPG Forbo Flooring Systems Masonite Architectural Teknion Limited
ELECTRICAL | PLUMBING | HVAC | RENEWABLES
Acuity Brands Aquatech Daikin Applied Elkay Fantech Klimatrol Mitsubishi Electric Sales Canada Inc. RadiantLink In-wall Heating Sloan Valve Tempeff Termobuild Viessmann Manufacturing Company Inc.
GREEN DESIGN SUPPORT + PROFESSIONALS
Canadian Precast Concrete Quality Assurance Certification Program Efficiency Nova Scotia FABRIQ architecture RJC Engineers Sustainable Forestry Initiative
PASSIVE BUILDER APPROVED
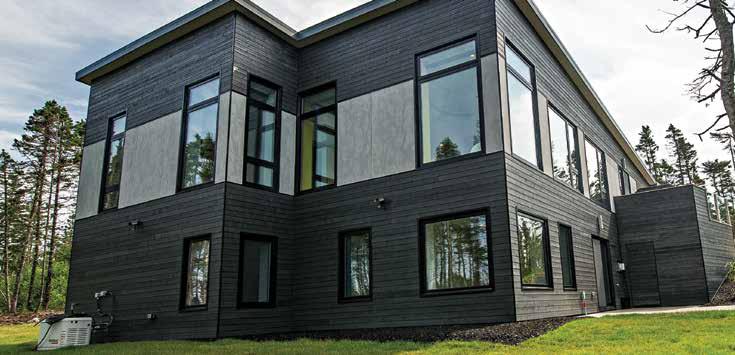
Kohltech is proud to be one of only a handful of Passive House Certified window and door manufacturers in North America.
Our dedication to energy-e ciency allows us to supply companies with the best triple-glazed windows to complete their Passive projects.
kohltech.com
