16 minute read
Editor’s Choice for May
by RTC Media
Next Article
May 2021 COT’S PICKS
Crystal Group, Inc. announced the newest addition to its lineup of highperformance edge computing solutions for intelligence, surveillance, and reconnaissance (ISR) applications
The new RS1104 ISR encoder integrates the Haivision Makito X1 into a Crystal Group FORCE™ server to deliver real-time streaming of MISB-compliant, full-motion video capabilities.
The ultra-compact RS1104 1U server consolidates the workload of three separate 1U units into one by integrating the Haivision’s Makito X1 video encoder, an 8-port switch, and six 2.5” SSD drives. This includes compressing a high-quality raw video source with two separate encode engines, which enables both a high-quality video stream for machine learning applications running on the RS1104 and a low-bitrate video stream to reach remote users over constrained network links.
“Consolidating our rugged server and Haivision’s rugged video encoder into a single unit enables the needed video quality and capabilities for accurate, live situational awareness at the tactical edge in a smaller footprint,” said Alan High, technical director at Crystal Group. “Eliminating the extra box, multiple mounts, and additional power supplies saves integration time and reduces installation challenges in compact spaces, like aircraft, drones, and tanks.”
In addition to the RS1104 video encoder, Crystal Group can integrate the high-quality video performance of the Makito X1 into any Crystal Group FORCE server or rugged embedded computer with 2.5” drive bays.
Crystal Group rugged servers are engineered to meet strict military and industrial standards to ensure seamless reliability in the harshest environments when speed, accuracy, and security are mission-critical. Haivision’s rugged video streaming appliances are deployed in similar applications when situational awareness requires real-time video surveillance.
Crystal Group, Inc. www.crystalrugged.com
Kaman Introduces New AMS Family of High-Precision Non-Contact Displacement Sensors
Products are rugged, reliable, and designed for environments from 500 psi to over 22,500 psi
The Measuring Division of Kaman Precision Products, Inc., announces the release of its new AMS family of high-precision non-contact displacement sensors ideal for condition monitoring of rotating machinery in extreme-pressure environments from 500 psi to over 22,500 psi.
AMS sensors deliver high reliability and superior performance in high-pressure environments enhancing any condition monitoring systems’ ability to measure and monitor runout, speed, and changes in machine vibration profiles. This helps to reduce risk, minimize damage and unplanned downtime due to unanticipated failures in the field.
Designed for a wide range of pressure environments, Kaman’s proprietary AMS, AMS-HP, and AMS-XHP precision sensing systems do not require a magnet and work with any ferromagnetic target. This innovative design detects target position through non-magnetic, conductive, and non-conductive barriers making leakproof, penetrator-free equipment instrumentation installations possible and economical without special magnets. With an RMS resolution down to 1 micron, and a standard measuring range up to 7mm, Kaman’s AMS sensors are compact and versatile.
Kaman Precision Products’ line of rugged AMS non-contact displacement sensors are IP67 rated with hermetic options available. For installation versatility, Kaman’s AMS sensors come in standard IP-67 rated threaded, flanged, AS4320 pressure port compatible, and bolt head style configurations with hermetic options available. In addition to Kaman’s standard sensor configuration options, Kaman’s AMS sensors are easily tailored to meet semi-custom and custom OEM integration requirements.
Kaman Precision Products, Inc. www.kamansensors.com

May 2021 COT’S PICKS
Supermicro Expands NVIDIA Ampere Architecture-based GPU Product Line for Enterprise AI Including an Industry-First 5 petaFLOPS in a 4U Tier 1 AI Platform
Super Micro Computer, Inc. extends its market in the growing areas of Artificial Intelligence (AI), Machine Learning (ML), High-Performance Computing (HPC), 3D-Graphics Visualization, and Desktop Virtualization. Supermicro has the broadest Tier 1 portfolio of systems that integrate state-ofthe-art capabilities achieving 5 petaFLOPS
of AI performance in a 4U form factor with the latest NVIDIA A100, NVIDIA A40, NVIDIA RTX A6000, and the new NVIDIA A30, NVIDIA A10, and NVIDIA A16 GPUs.
“Our collaboration with NVIDIA enables us to design a complete portfolio of GPU systems and platforms empowering maximum customer choice. Customers can exactly match their workload requirements to system architecture to achieve superior scale, performance, efficiency, and cost,” said Charles Liang, president, and CEO, Supermicro.
“Supermicro offers multi-GPU optimized systems that deliver advanced solutions to AI, Deep Learning, HPC, and video streaming applications. Leveraging our building block solutions and our time-tomarket advantage, we continue developing and releasing application-optimized solutions. Our flexible 2U 2-node GPU system with PCIe 4.0 is tuned for cloud gaming and social media and leads the industry with support for up to three double-width or six single-width GPUs per node.”
The breadth of Supermicro’s systems includes the flagship Intel-based SYS420GP-TNAR or the AMD-based AS -4124GONART(+), featuring the 4U Server powered by the NVIDIA HGX A100 8-GPU board, with the option of either 40GB (HBM2) or 80GB (HBM2e) of memory on each GPU. These systems are currently shipping worldwide.
“From AI-powered drug discovery to designing advanced, efficient factories, accelerated computing is essential to powering the most innovative work in the world today,” said Justin Boitano, vice president and general manager, Enterprise and Edge Computing at NVIDIA. “Supermicro’s NVIDIA-Certified Systems provide customers with a broad range of servers built to deliver top performance for AI, graphics and simulation workloads across the data center, to the cloud, to the edge.”Crystal Group Introduces ISR Video Encoder for Secure, Real-Time Video Streaming.
Super Micro Computer www.supermicro.com
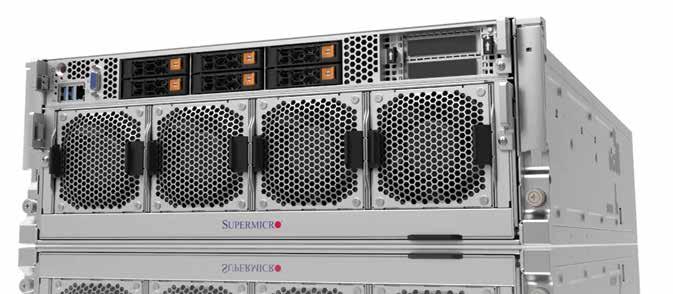
May 2021 COT’S PICKS
Pentek 8-Channel Phase Coherent RF Signal Recorder Extends Recording Capability for Beamforming and Radar Applications
• Rugged RF signal recorder with eight phases coherent RF tuners
• Ideal for signal intelligence, phased-array radars, beamforming, and direction-finding
• Records RF frequencies to 6 GHz with bandwidths to 80 MHz
• 3.2 GB/s real-time aggregate recording rate
• 122 TB of storage allows for hours of data recording
• SystemFlow software GUI with Signal Viewer analysis tool
Pentek, Inc. introduced a new addition to the Talon® series of recorders, the Talon Model RTR 2628 8-channel, phase-coherent, 4U 19-inch rackmount recorder with integrated RF tuners and A/D converters. The rugged rackmount system is designed to operate under conditions of vibration and extended operating temperatures. The Talon RTR 2628 accepts signals from eight antennas to provide eight channels of phase-coherent RF signal recording. Each channel is tunable up to 6 GHz and captures up to 80 MHz of instantaneous bandwidth.
“With an excellent dynamic range to pick up low-level signals, the Talon RTR 2628 is an ideal choice for spectrum monitoring applications that need to accurately interpret synchronized signals. Targeted applications including beamforming, direction finding, phased-array radars, and multi-antenna diversity receivers can all leverage the phase-coherent capabilities of the Talon RTR 2628,” noted Rodger Hosking, co-founder, and vice-president, Pentek.
Each input channel includes a 250 MHz 16bit A/D and an FPGA-based digital downconverter with programmable decimations from 2 to 65536 for instantaneous bandwidths from 80 MHz down to 3 kHz. RF signals up to 6 GHz in frequency can be tuned, sampled, digitally downconverted, and streamed to disk in real-time at sustained aggregate recording rates up to 3.2 GB/sec. RF tuning frequencies, A/D sampling rates, DDC decimations, and trigger settings are among the selectable system parameters, providing a system that is flexible, yet simple to configure and operate.
The RTR 2628 is configured in a 4U 19-inch rack-mountable chassis, with hot-swap data drives, front panel USB ports, and I/O connectors on the rear panel. It is optimized for cooling and ruggedized to operate in challenging environments. Systems are scalable to accommodate multiple chassis’ to increase phase-coherent channel counts and aggregate data rates. All recorder chassis are connected via Ethernet and can be controlled from a single GUI either locally or from a remote PC.
The RTR 2628 includes as many as 32 hot-swappable SSDs to provide flexible storage capacities up to 122 TB. The 2.5-inch SSDs can be easily removed or exchanged during a mission to retrieve recorded data. Multiple RAID levels, including 0, 5, and 6, provide a choice for the required level of redundancy.
Ease of Operation
All Talon recorders are built on a Microsoft Windows platform and include Pentek’s SystemFlow software, featuring a GUI (graphical user interface), Signal Viewer, and API (Application Programming Interface). The GUI provides intuitive controls for out-of-the-box turn-key operation using point-andclick configuration management.
Configurations are easily stored and recalled for single-click setup. The Signal Viewer provides a virtual oscilloscope and spectrum analyzer to monitor signals before, during, and after data collection. The C-callable API allows users to integrate the recorder control as a front end to larger application systems. Enhancements to the GUI support efficient configuration of the recording channels.
The data format used for storage follows the NTFS standard, allowing users to remove drives from the instrument and read the data using standard Windows-based systems, eliminating the need for file format conversion.
Pentek, Inc. www.pentek.com
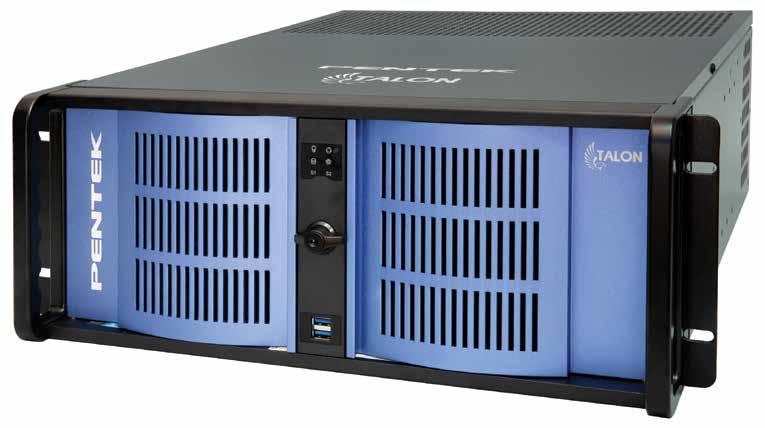
May 2021 COT’S PICKS
Green Hills Software and MathWorks Create Integrated Code Development Toolbox for Wide Range of Embedded Processors
- The MULTI Toolbox for Embedded Coder enables users to easily run, verify and test Simulink and MATLAB models on thousands of embedded processors
- Qualified for developing code at the highest levels of functional safety for automotive, industrial, railway
- Provides seamless Processor-In-the-Loop (PIL) test and validation
Green Hills Software announced the immediate availability of the MULTI® Toolbox for Embedded Coder, enabling engineers to easily and efficiently develop and deploy their Simulink® and MATLAB® models on a wide range of embedded processors. The integration bridges advanced software development products from industry leaders in their respective domains – MathWorks®, the leading developer of mathematical computing software, and Green Hills Software, the leader in safe and secure embedded software solutions. Engineers and scientists who develop algorithms in MATLAB and Simulink now have a simple and safety-qualified way to develop, debug, optimize and deploy their programs on thousands of embedded processors supported today by Green Hills.
The MULTI Toolbox for Embedded Coder connects Simulink and MATLAB on the desktop with the MULTI integrated development environment (IDE) that comprehends and controls embedded target processors. On the desktop, users develop Simulink and MATLAB models and generate C/C++ source code. MULTI then compiles, connects, and runs the optimized binaries on either the target processor or on the MULTI IDE’s built-in embedded core simulator. MULTI feeds back results to Simulink via Processor-In-the-Loop (PIL), enabling the user to visualize the results or to confirm programmatically that results from Simulink algorithms on the workstation match the actual results run on the embedded processor.
“Connecting Simulink to embedded simulators and debuggers is the next milestone in our customers’ desire to move testing and verification from the field to the lab to the desktop,” said Tom Erkkinen, Product Manager, Embedded Code Generation at MathWorks. “Green Hills shares this vision and has worked closely with MathWorks to develop its MULTI Toolbox for Embedded Coder. As remote work and online collaboration continue to grow, the need for virtual testing and development environments will accelerate.”
“Many of our customers use MathWorks products to create algorithms destined for embedded systems,” said Rob Redfield, Director, Business Development at Green Hills Software. “Now, they not only have an easy-to-use way to run and verify these algorithms on embedded processors but they can also debug, analyze and optimize their code with safety-qualified MULTI and its optimizing C/C++ compilers.
Once the program completes, users can run, debug and analyze the program at any point in its execution using MULTI and the TimeMachine® debugger. They can: • Run the program backward and forward, set breakpoints, debug and view variables • Debug INTEGRITY®, µ-velOSity™, and AUTOSAR real-time operating systems, or Linux and other operating systems • Verify adherence to MISRA C/C++ rules
• Perform Run-time Error Detection & Memory Leak Detection • Optimize the program with Performance Profiling • Analyze code coverage with DoubleCheck™ source code analyzer • functional safety is important, MULTI and its C/C++ toolchain are certified at the highest safety levels and standards, including Automotive (ISO 26262 ASIL D), Industrial (IEC 61508 SIL 3), and Railway (EN 50128 SIL 4).
The MULTI Toolbox for Embedded Coder supports thousands of 32- and 64-bit embedded processors from leading processor manufacturers, including NXP, Renesas, Qualcomm, TI, and Microchip, built on the popular embedded core architectures: • Arm® Cortex®-A (both Armv8-A and Armv7-A) • Arm Cortex-R (Armv7-R). Armv8-R support is in progress and will support Cortex-R52/82 • Arm Cortex-M (Armv7-M) • RISC-V • Renesas RH850 • Power Architecture
Pixus Technologies, a provider of embedded computing and enclosure solutions, now offers a conductioncooled model for their 3U OpenVPX Chassis Manager
Compliant with the VITA 46.11 specification for system management and to VITA 48.2 for mechanical design, the Tier 2 Pixus OpenVPX Chassis Manager monitors at least 6 temperature sensors and 10 fans with custom options available. There is fan PWM/Tach control, along with 16 digital inputs and outputs. A Level-2 unmanaged 3- port Ethernet hub is also optional. The standard panel interface has RS-232, RJ-45, USB, and LEDs.
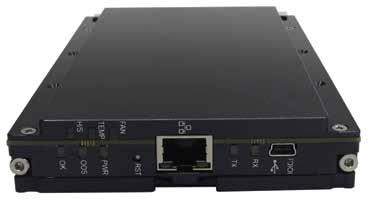
The Pixus SHM200 features a Web interface to remotely query the system and the user can import images of their boards. By clicking on the image for each slot, the user can drill down to the monitored status of the module.
Pixus Technologies https://pixustechnologies.com/w
Compa
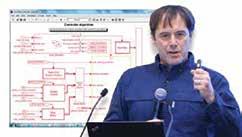
Tom Erkkinen
VProduct Manager, Embedded Code Generation at MathWorks
Green Hills Software www.ghs.com
May 2021 COT’S PICKS
Galleon Embedded Computing Releases the New Product; XSR Tactical Secure Server
Galleon Embedded Computing has announced their new ground vehicle computer, the XSR Tactical Secure Server. A server specifically engineered for tactical military vehicles, the XSR TSS meets the rugged requirements for the most severe environmental conditions without compromising performance, functionality, or reliability. Equipped with removable storage supported by dual-layer Data-at-rest encryption, the XSR Tactical Secure Server ensures consistent and secure data management.
With the latest 9th generation Intel® Xeon® E and Xeon® D processor options, the XSR-TSS offers up to 16 CPU cores and 128Gb SDRAM with ECC. Its flexible architecture can provide the modern warfighter with advanced I/O, cutting-edge processing power, and ultra-high storage density. Housed in a SWaP-optimized design, the XSR TSS is protected by one of the most rugged and deployable mobile platforms available.
Galleon Embedded Computing https://galleonec.com
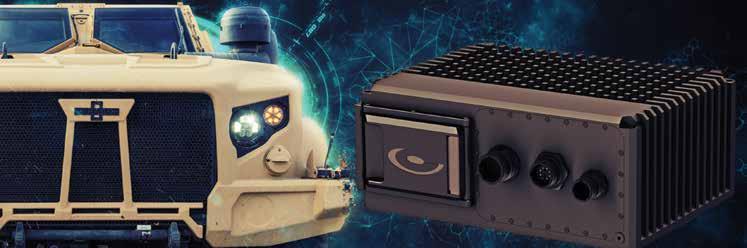
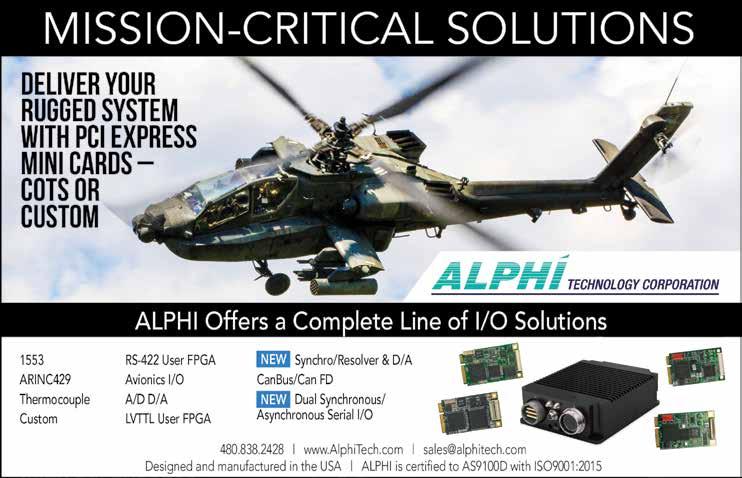
May 2021 COT’S PICKS
New dSPACE MicroAutoBox III variant with a comprehensive range of bus and network interfacesr
In the development of self-driving and electrically-powered cars, the connectivity requirements for in-vehicle prototyping systems are constantly growing. This is why dSPACE offers its MicroAutoBox III in-vehicle prototyping system with a high number of channels and an extended range of bus and network interfaces. With the addition of the new DS1521 I/O board variant, the system is particularly suitable for communication-intensive developments that take into account the centralization of the E/E architecture, among other things.
Typical applications for the MicroAutoBox III with the new DS1521 Bus and Network Board include intelligent gateways, running supervisory controllers to control other ECUs in real-time via buses and networks, and designing central control units with service-based Ethernet communication. To ideally address these applications, the DS1521 Bus and Network Board provides eight CAN FD channels, three automotive Ethernet ports (100/1000BASE-T1), two FlexRay connectors (A/B), three LIN channels, and additional UART, digital, and analog interfaces. For particularly communication-intensive applications, the MicroAutoBox III can also be equipped with two DS1521 boards, which results in doubling the number of the above-mentioned interfaces. A combination with other MicroAutoBox I/O boards is also possible.
The system is configured using the ConfigurationDesk implementation software, including the integrated Bus Manager. This allows for configuring the bus communication based on the latest standards and protocols, such as AUTOSAR (ARXML), FIBEX, DBC, or LDF. For integration into an existing vehicle electrical system, current AUTOSAR features such as secure onboard communication (SecOC), end-to-end protection, and global time synchronization (GTS) are also supported on all relevant bus systems, including service-based Ethernet communication (SOME-IP).
dSPACE www.dspace.com
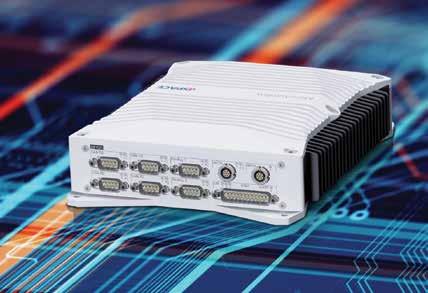
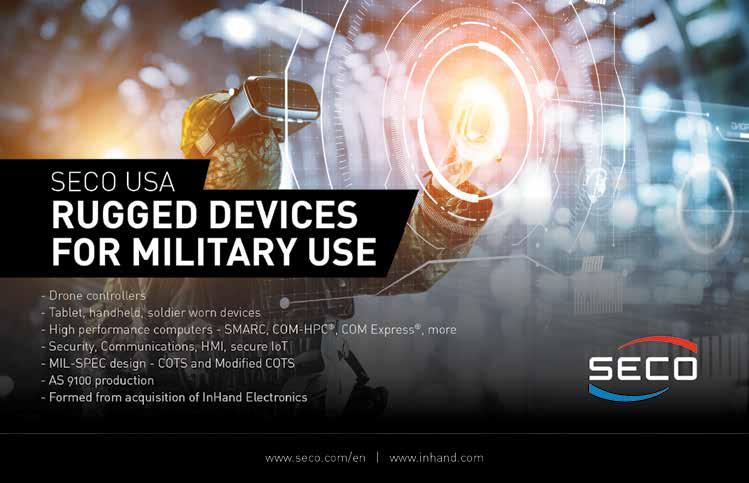
May 2021 COT’S PICKS
Cincoze GM-1000’s New Quadro MXM GPU Modules Satisfy Stringent Machine Vision Performance Requirements
Cincoze expands the Cincoze GM-1000’s machine vision application performance with two new Quadro MXM GPU modules. Building on the GM1000’s powerful processing base, the MXM-RTX3000 and MXM-T1000 provide the additional GPU capacity for rapid adoption of machine vision in smart factories, from simple environmental perception applications such as positioning, measurement, identification, and sorting, to more complex vision-guided automation functions. GPU requirements for each scenario are different, so specifications must match the environment and application. The two new Quadro® MXM GPU modules broaden the GM-1000’s available selection to cover a wider range of uses.
The GM-1000—part of the Cincoze GOLD series—is positioned as a high-performance machine vision system featuring high computing performance, high-speed I/O, and industrial-grade reliability. It is the preferred choice for machine vision system integrators and AOI (Automated Optical Inspection) manufacturers. The GM-1000’s unique carrier board can be matched with a selection of Cincoze MXM GPU modules, including the MXM-RTX3000, MXM-T1000, MXM-P2000, and MXM-E9174, providing a precise match for different computing requirements.
Upgrade flexibility has always been a proud advantage of Cincoze. The GM-1000 only needs a carrier board and MXM GPU module replacement to facilitate future performance upgrades without replacing the computer host.
Computational Prowess While Saving Power
The new Quadro® MXM GPU modules, the MXMRTX3000 and MXM-T1000, use the latest NVIDIA® Quadro® Turing™ GPU architecture based on the latest 12nm process.
In terms of core computing power and performance, the MXM-RTX3000 has 1920 CUDA cores, 5.3 TFLOPS peak FP32 high-end computing power, parallel integer execution, AI computing Tensor core, and specialized RT core for ray tracing. Together these provide fully integrated GPU features to face complex visual image calculations. The MXM-T1000 has 896 CUDA cores, 2.6 TFLOPS peak FP32 computing power, and only 50W power consumption for power-conscious high-speed computing. Both models support GDDR6 memory. The MXM-RTX3000 has a single card capacity of up to 6 GB and 336 GB/s memory bandwidth. The MXM-T1000 has 4 GB capacity and 192 GB/s memory bandwidth. The faster memory smooths data reading and multiplies computing performance.
In addition, both modules have different form factors, the MXM-RTX3000 sporting an MXM 3.1 Type B form factor, while the MXM-T1000 has a Type A form factor, allowing for free choice according to the situation.
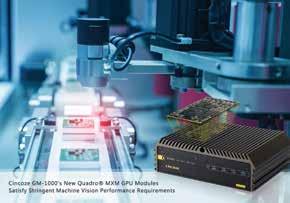
Cincoze www.cincoze.com
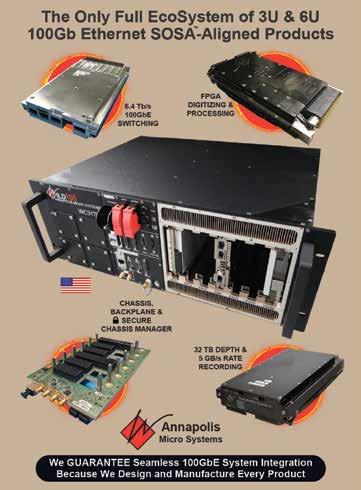
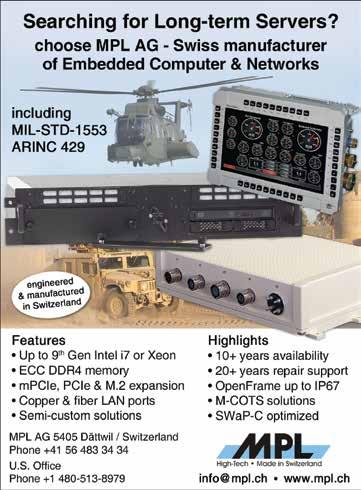
COTSCOTS
ADVERTISERS
Company Page # Website
Annapolis Micro Systems ........................................ 30 ........................................ www.annapmicro.com Alphi Technology Corporation .................................. 4 ............................................ www.AlphiTech.com Broadcom ............................................................... BC ............................................ www.broadcom.com Diamond Systems .................................................... 25 ...................................www.diamondsystems.com GET Engineering ..................................................... 17 ............................................... www.getntds.com Great River Technology ........................................... 4 ....................................... www.greatrivertech.com Kingston Technology .............................................. IBC ............................................. www.kingston.com MPL ...................................................................... 30 ..................................................... www.mpl.com Neonode ................................................................. 5 ............................................... www.neonode.com OSS ........................................................................ IFC .................................. www.onestopsystems.com Pentek .................................................................. 8 ................................................. www.pentek.com PICO Electronics, Inc ............................................. 15 .................................... www.picoelectronics.com Pixus Technologies ................................................. 14 .............................. www.pixustechnologies.com Sealevel ................................................................. 16 .............................................. www.sealevel.com SECO ...................................................................... 21/29 ................................................... www.seco.com U-Reach ................................................................. 20 ........................................ www.ureach-usa.com Versalogic .............................................................. IBC ............................................. www.versalogic.com
COTS Journal (ISSN#1526-4653) is published monthly at; 3180 Sitio Sendero, Carlsbad, CA. 92009. Periodicals Class postage paid at San Clemente and additional mailing offices. POSTMASTER: Send address changes to COTS Journal, 3180 Sitio Sendero, Carlsbad, CA. 92009.

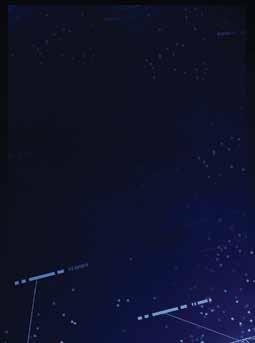
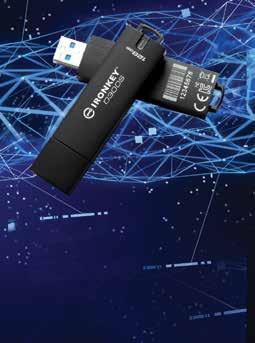
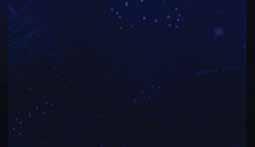
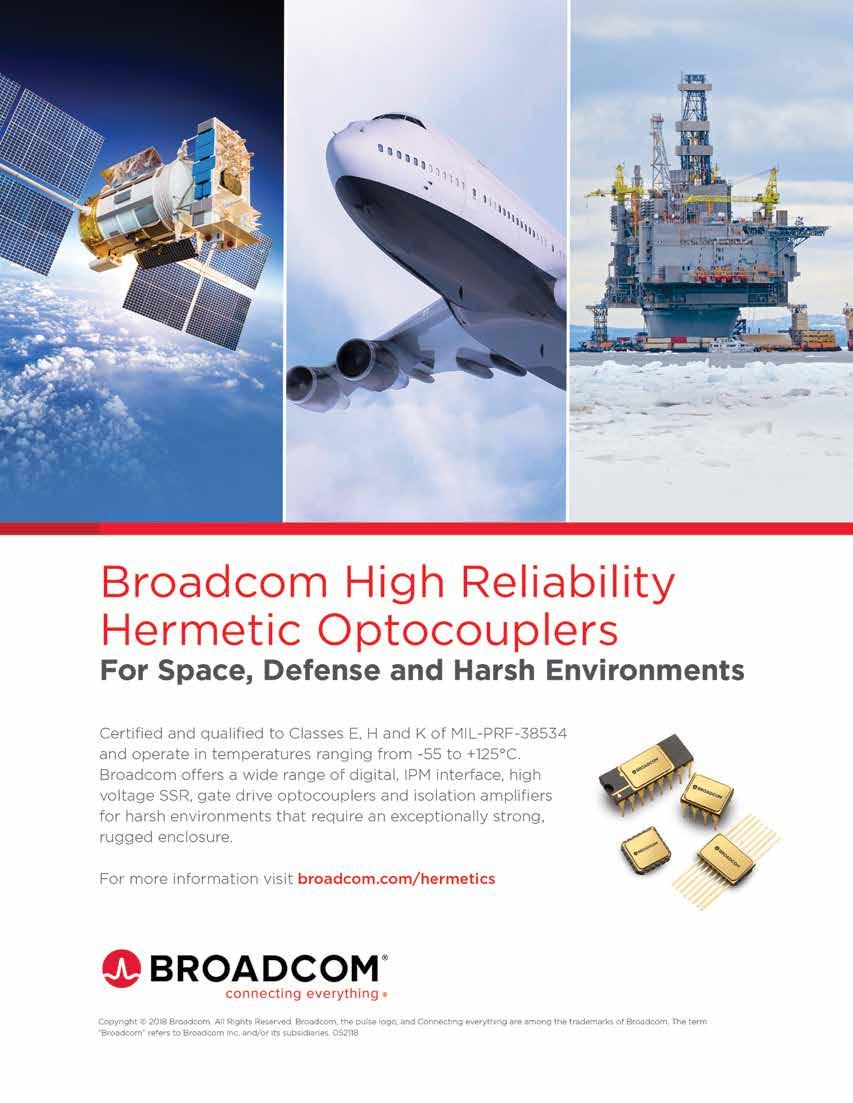