2 minute read
Leading leadworker tells the story of giant planter installation
[FURTHER DETAILS have come to light of the magnificent lead planter produced by Brian Turner of Turners Ornamental Leadwork for a private client in Norfolk, as featured in Ecclesiastical and Heritage World last autumn.
The trellis tree planter is three metres in diameter and 560mm high. Each of the individual cast panels is 1,710mm in length, giving a circumference of 9.426 metres. Each panel is decorated with motifs designed by the client, depicting items of significance to the family.
The total weight of the planter is 1,584 kilos and even the circular part of the base that was cut out to allow roots to grow through weighed 307 kilos.
It was, as Brian observed with typical understatement, ‘a challenge to make’ and pushed all his skills to the limit in order to keep moving forward.
The pictures below tell the story of the planter’s installation.
5. All done! A very happy customer and a very satisfied Brian: all went as planned. Said Brian: “When I started off I was asked could I do it? I said ‘I don’t know’. Now I know there is a way!”
1. Making the sand mould: on the panels the motifs were arranged so each numbered panel was different.
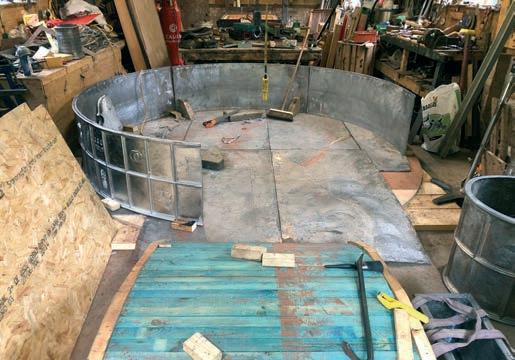
2. Brian practised preparing all the panels before taking them to the site. The side panels were put in position to mark out the base sheet, which was then cut out using a router. All the parts were numbered before being loaded onto a pallet to take to the site. 3. Putting it all together with the help of a derrick. That was another ‘first’ for Brian as it was the first time he had assembled a cistern on site. The base was laid on a wooden deck and the pattern marked out; then fully burned in. The gaps in the lead were about 6mm, which made sure that the burn was full.
Said Brian: “My main concern was to make sure there was full lead joint penetration, so I had to make sure to do all the burning in the horizontal, as the joints were on the vertical moulding line. The joints were 25mm deep, so I had to burn on the face of the moulding, then fettle it all when the joint was at the top of the vertical – three metres high.”
The planter was then rolled 180º so the joint was at its lowest – 300mm high. Then, on the inside of the planter the joint was filled with solder and back-burned. That was repeated until all the joints were completed.
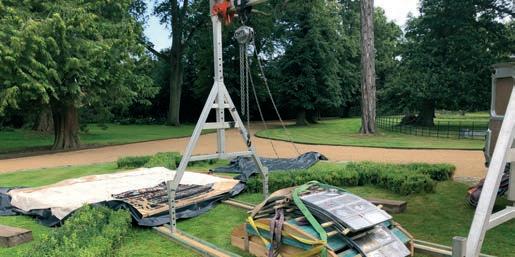
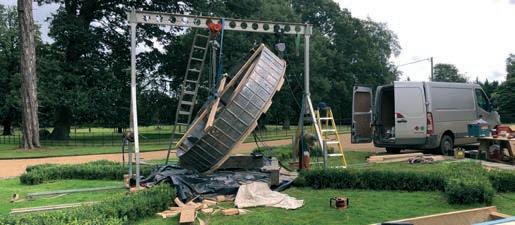
4. It was challenging rotating the planter, to say the least! Brian explained: “I had to make the lifting jig a bit bigger as all the braces had deep-filled burns. Everything was at its limit – I had about 50mm spare head room to turn the planter.”
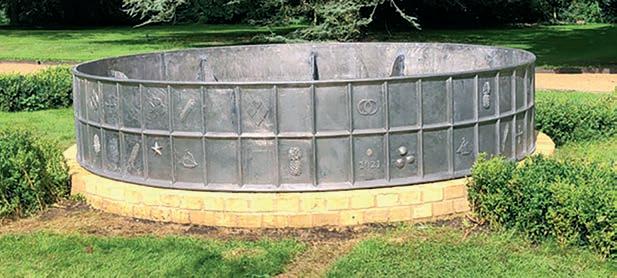