3 minute read
Thermal Management in the Electric Age
from OOH May/June 2023
Next Article
Across the country, commercial fleets are transitioning from internal combustion engine (ICE) vehicles to electric vehicles (EVs). A shift of this magnitude comes with challenges, including higher vehicle acquisition costs and the need for charging infrastructure. However, the total cost of ownership (TCO) of commercial EVs will likely outperform ICE vehicles as soon as 2025. Given the increasing availability of EVs and their improving range, the need to reduce carbon emissions, and government incentives and regulations, the commercial EV market is primed for growth.
Questions continue about how commercial EVs will perform compared to their ICE cousins. Can a battery store enough energy to reliably power rugged medium- and heavy-duty vehicles? Will those EV systems withstand the harsh, dirty environments? Which technologies best protect and optimize the performance of commercial EV components? Being asked with increasing frequency are questions about whether EVs require seasonal, temperature-related preparation like the winterization ICE vehicles undergo. The answer is a qualified yes because the most important aspects of EV winterization happen in manufacturing, not at the depot.
The lithium-ion (Li-ion) batteries in modern EVs are larger versions of those in smartphones. Anyone who has left a phone in the sun or in a car on a cold night knows that temperature extremes negatively affect a phone battery’s life and performance. Similarly, maintaining the right battery temperature range is essential for reliable EV operation.
In cold temperatures, the chemical reactions inside Li-ion batteries slow
How to keep commercial EVs working yearround
by Gina Bonini, Modine Manufacturing
down, increasing internal resistance, which reduces battery capacity and, in turn, reduces vehicle range. Cold temperatures also result in slower charging. On the other end of the mercury, high temperatures cause chemical reactions in the battery to speed up, draining the battery more rapidly. If it is continually exposed to extremes, it will degrade.
The good news is that vehicular thermal management is well-trodden ground. Some companies have more than 100 years of experience in the field. Some thermal management companies have developed new technologies and methods, including high-fidelity temperature control for EV components using refrigeration and heating circuits with sensors and sophisticated controls. Using these technologies help make commercial EVs viable in even the most severe environments.
What Is Battery Thermal Management?
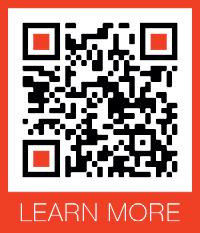
Battery thermal management is one of the less visible but critical frontiers in EV transportation. Ambient temperature impacts the range, charging time and the lifetime of batteries. For rugged specialty and commercial EVs, however, battery thermal management systems (BTMSs) must efficiently manage battery temperatures, be able to accommodate novel space constraints, and survive unforgiving and often dirty environments.
For peak performance during charging and operation, what is effectively a double-duty cycle, battery pack temperature should ideally remain between 25°C and 35°C (77°F and 95°F). As such, a BTMS should heat and cool the battery pack. In practice, if the ambient temperature drops too low, the BTMS heating loop will increase the temperature of the coolant circulating within it until the battery pack reaches the ideal temperature. Once the vehicle is in operation—or while charging—the BTMS removes the resulting heat to prevent overheating. The switch between cooling and heating, as well as the intensity of each, are managed automatically by the system.
A key consideration in a BTMS design is optimizing temperature control while minimizing power consumption. A BTMS, therefore, may have an active loop with a refrigerant circuit to remove heat in hotter temperatures and a passive loop with a radiator and fans—which draws less power—if the ambient temperature is moderate. For off-highway applications, BTMSs can be designed to protect fans or exposed heat transfer modules from potential clogging by dirt and debris.
As with all batteries of this type, maintaining optimal thermal conditions shortens charging time and maximizes the range and battery lifetime.
Other Considerations
The inverters, converters, traction motors and related power electronics that charge the batteries or turn battery-stored electrical energy into kinetic energy are similarly affected by ambient and operating temperatures. Given the weight, payloads and workloads of heavy-duty commercial EVs, their powertrain electronics require significantly more power than average light-duty or consumer passenger EVs. With more and higher power comes more heat and more stress on electrical components. As a result, performance, durability and safety may be affected. With inverters, for example, power output is limited by the maximum temperature threshold of the power module, impacting performance. It may even shutdown without intervention from a BTMS.
Commercial EVs are typically equipped with a cooling package for inverters,