4 minute read
Chain Reaction Key questions to ask about Warehouse Automation Technology
ProMat 2023, the largest supply chain and material handling show of the year, took place in Chicago in late March. With a record number of exhibitors and attendees, it was an interesting and busy four days. And just like at MODEX last year, MHI’s sister show in Atlanta, warehouse automation was the hot topic of the show.
Trending Topics
Whether you were a first-time visitor or are a perennial attendee, you likely heard conversations about automation and the issues surrounding it. Here are five questions automation vendors, software providers, and system integrators were asked and some tips about what should happen next:
1. What is the warehouse automation technology that is the fastest and simplest to adopt?
With so much pressure on achieving more with less, many warehouse managers want to test out automation in a simpler way to see if it works for them before diving into a large warehouse automation technology project. A tour of the various automation vendors at ProMat revealed some quick automation wins that solve simple problems like automated tugs to shuttle goods from place to place around the warehouse.
2. What is the lead time for the automation vendor or project I might be interested in?
This high demand for automation, and the major supply chain disruptions affecting automation vendors’ ability to service existing projects, have led to ballooning lead times for the implementation of certain types of automation. The larger and more complex the warehouse automation technology project is, the longer you will likely have to wait before you can kick off the project with some of the larger automated storage and retrieval system (AS/RS) vendors reporting 18-24 month wait times. Be sure to follow up with the automation vendor contacts you made at ProMat to understand their lead times and ability to deliver as part of your broader strategy.
3. How will this automation integrate into my existing systems and environment?
Most warehouse managers already have warehouse technology in place. Whether it’s a warehouse management system (WMS), a carousel, or some traditional conveyor-based technology like a diverter, figuring out how any new warehouse automation technology will affect and be affected by those systems is vital to your success. Older WMS simply lack the capabilities to consider automation in their workflows and others make getting the data needed to run the automation a nightmare. If you already have material handling technology in place, the question to ask is, “Will it play nicely with the new automation?” The last thing you need is your new system being slowed down or not operating due to existing systems.
4. What happens if I want to implement a second type of automation later?
Gartner predicts that most warehouses will have at least one type of warehouse automation technology by the end of the decade. The key to that sentence is “at least one type” since it’s clear that there are many forms of automation, and each is especially good at solving one type of warehouse process for one type of order. If you are going to need several types of automation that work together, has your choice of automation been considered for future implementations or was it developed in silos with little consciousness of the rest of the warehouse infrastructure?
5. What is the data I need to prepare before we go deep into the ROI conversation?
Regardless of your warehouse technology or automation, there will need to be a return on investment (ROI) to make it make sense and an evaluation of the ROI. If this serves you, you will need to produce data around the volume, cube, and velocity of your orders. If any of this data is a ‘guesstimate’, then so will the likelihood of your project’s success. The most critical part of any automation project is having solid data from the very start; ask and understand what those critical data elements are and make sure they are 100% accurate.
Consider a Vendor-agnostic Technology Partner
With hundreds of automation vendors entering the market, it may be challenging to separate the wheat from the chaff. It may be useful to confer with a technology partner that understands this evolving landscape. For example, Tecsys is a warehouse management system solution vendor that drives automation through platform-agnostic software. Their industry experts led automation tours for ProMat attendees to introduce warehouse automation technology and present a general 'lay of the land' of modern automation solutions. Each of the major types of automation was exhibited (e.g., AS/RS, cobots, etc.) while indicating their strengths and what to look out for when considering each specific warehouse automation technology.
Whether you caught up with them on their Automation Tour at ProMat or want to strengthen your automation strategy with The Ultimate Guide to Warehouse Automation e-book, it is valuable to understand the landscape so that the steps you take are in support of a well-considered plan.
Bill Denbigh serves as the vice president of product marketing at Tecsys. Bill started working in supply chain software some 30 years ago; his entire career has been laser-focused on designing and building pragmatic supply chain solutions that address the real problems that customers are facing in their supply chain operations. Bill has worked on virtually every aspect of the software in the supply chain, gaining insight into the inner workings of some of the industry’s most complex challenges; Bill, however, tackles those challenges with a no-nonsense levelheadedness that has earned him great repute both internally and among customers.
• Ideal for storage of items with legs or point loads (furniture, equipment with wheels, etc.)
• Easy to install in either pallet rack or cantilever rack
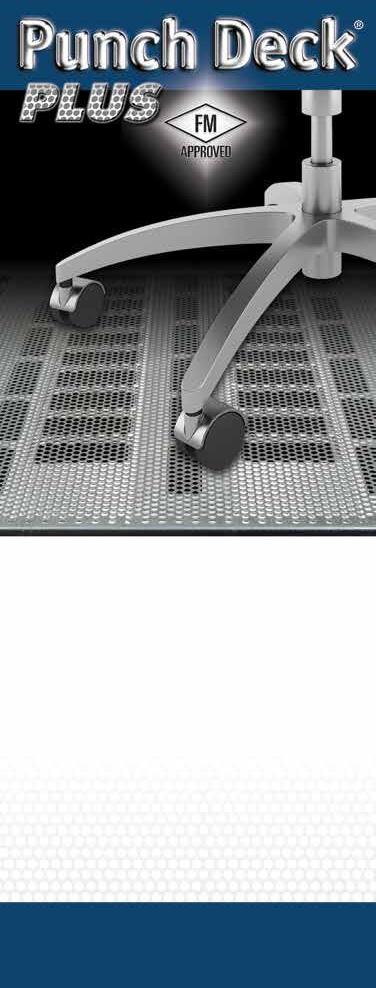
• Galvanized finish is bright and maintenance free
• Offered in a wide range of shelf sizes and load capacities