10 minute read
Future Looks Comforting In Furniture Manufacturing
About two-thirds of Vallero International’s tannery drums are made of wood, but the company also makes versions in plastic and stainless steel. Future Looks Comforting In Furniture Manufacturing
Furniture makers in the United States are going strong and expect continued growth, with annual production increases of 3% through 2019. Italian manufacturing machinery makers are helping them keep up, with innovation and automation in the wood, textiles, leather and plastics sectors.
“From a technology standpoint, Italy’s textile machinery manufacturers are at the forefront of research and innovation, and their primary focus is on continuing to innovate,” said Raffella Carabelli, president of the ACIMIT - Association of Italian Textile Machinery Manufacturers (www.acimit.it).
The professional organization for companies that make shop machinery for processing and manufacturing with animal hides, ASSOMAC - The National Association of Manufacturers of Footwear, Leathergoods and Tannery Technologies (www.assomac.it), said its members are making automation and connectivity a priority. “Our members’ biggest concerns in 2016-17 are to increase machine automation and software simplicity,” said Andrea Favazzi, of ASSOMAC’s technology department. “That includes making hardware and software more friendly for the users.”
Shoe manufacturers, especially, are working toward increased process control of production systems, Favazzi said. Italian manufacturers supply over half of the world’s shoe and leather goods machines. ASSOMAC members include ALC Tecnologie Adesive Srl, (Robassomero, Italy; www.alcgruppo.com) and DAP Italia Srl Cinisello Balsamo, Italy; www.durkoppadler.it), each of which produces both footware and leather goods machines.
While critically important, automation isn’t the only criterion North American furniture makers use when choosing manufacturing machinery.
“Our manufacturers’ customers are demanding technologies capable of creating products with the least possible environmental impact, and with significant savings in energy, raw materials and chemical substances,” Carabelli said. “The efforts placed in R&D by our affiliated members are focused in this direction, developing machinery that provides high productivity, cost savings and a low environmental impact.”
The innovation from Carabelli’s organization’s members is paying off in rising exports across the Atlantic.
In 2015, Italian sales of textile machinery to the United States reached a value of about $99 million, an increase of 8% over 2014 sales.
Industry 4.0
While the term Industry 4.0 may have been coined outside of Italy, Italian companies that make manufacturing equipment for the furniture industry have embraced its foundational concept of computerizing manufacturing.
“It’s a new concept, but companies are moving there,” said Karen Koenig, special projects editor for the Woodworking Network who visited Biesse Group (Pesaro, Italy; www.biesse.com) and five other cabinet and furniture manufacturers throughout the country on a weeklong technology tour in October 2015. “The equipment Biesse had was very high tech and the software that goes with it allows the machines to talk to each other.
“All the CNC companies, that’s what they’re going for.” Federico Broccoli, president and CEO of Biesse America and Canada, told Koenig: “For us, 4.0 is not simply a number representing what has been hailed as the new industrial revolution, but a real commitment that Biesse has made to our customers, with a view to uniting them with our ‘4.0 ready’ technologies, to achieve levels of efficiency which today, more than ever, are crucial for keeping abreast of the competition in an increasingly global market.”
In order to serve the North American market, Biesse has two permanent showrooms in the United States, and an equal number in Canada. Broccoli said his company is so committed to Industry 4.0 that it’s developed a business plan to hire additional people to guide customers, including small and medium businesses, as they incorporate computer-driven manufacturing in their shops.
Koenig noted that Biesse’s showroom included CNC machining centers; edge banders; boring, inserting, calibrating and sanding machines; and flexible beam saws.
Broccoli said in a press conference that while CNC machining centers have accounted for a little more than half of the company’s sales in past years, sanding and edge banding, particularly Biesse’s innovations in zero-edge banding, are spurring growth in those segments.
Broccoli also said his company is committed to producing machinery for materials other than wood, including plastics. He noted that while Biesse has “always been supplying” equipment to the rigid plastics market, the company is developing a new division specifically for that sector. “We’re going from advanced materials reactive to advanced materials proactive,” he said.
Biesse’s trade organization, ACIMALL - The Italian Woodworking Machinery and Tools Manufacturers’ Association (www.acimall.com), said “The Italian industry has excellent actors across the entire value chain, from primary processing technology, through machinery and tools for solid wood and panel processing, up to surface finishing.”
ACIMALL represents over 220 of the most qualified companies in their field, which represent 90 percent of the whole industry, both in terms of employees and in turnover.
Back in the United States, Biesse designed a system for commercial cabinetmaker Contemporary Cabinets to smooth out its workflow. “When we purchased a new machine, we would position it wherever there was space, without considering the workflow and consequently, where the machine would be best placed for maximum efficiency,” said plant manager Don Wiggins in a case study. “As a result, the pieces moved through the factory without any logical sense.” With Biesse’s help, Contemporary Cabinets reconfigured the workflow into a “U” shape that follows the most efficient route through the factory.
Every element of a cabinet being manufactured travels along the production line, and is subject to all of the machining processes, edge banding, dowelling and insertion of hardware, before eventually being loaded onto pre-assembly carriages. The cabinets are then assembled and placed on conveyor belts to be completed. The backs are secured in position to keep them square until the bonding process is complete, while a belt transports the drawers and doors. Finally, the cabinet is packed and loaded on a truck.
Contemporary Cabinets makes closets, lockers and more for furniture stores, schools, dentists and doctors offices, churches and small residences, among other clients, in five plants.
“We mainly produce cabinets for commercial projects,” Wiggins said. “We have a factory for customized products such as reception desks, conference tables and more complex pieces which cannot be introduced into the production flow of the main plant.”
In addition, Contemporary Cabinets uses a Biesse (Charlotte, NC; www.biesse.com/na) WinStore material handling system for its custom work materials. WinStore includes an overhead travelling crane system that stores information on the characteristics and positions of up to 2,000 panels inside it.
Workers position stacks of panels in the plant’s external warehouse and inform the control system the type and amount of material. WinStore then places them in the warehouse. If there is a new material with characteristics that are not already stored in the memory, the weight of the sheet is recorded.
“Before we implemented this system, the machine remained stationary for 20-30 minutes while waiting for the necessary material for machining to be loaded,” said Wiggins. “Now, however, almost all the material is stored in WinStore and there are no waiting times.”
WinStore also keeps track of the material in stock and how many sheets the beam saw and the North Carolina machining center use. “We started using WinStore in March 2013 and since then, our entire production flow has been redirected to work around this system,” Wiggins said. “Both the Selco beam saw and the Skill machining center are also incorporated into WinStore’s working area, and as such, both can also be rear-loaded directly from the latter.
“The mere fact that we now have a significant production flow has greatly helped us. We have enhanced the drilling and inserting machine with a numerical control machining center and this has given us excellent results.”
Another Biesse North America client, Closet America (Lanham, MD; www.closetamerica.com), a leading home and professional closet system manufacturer, is the proud owner of the first Biesse AirForce edge banding system in the United States.
“In our efforts to provide our customers with a high-quality, customized closet system along with our topnotch customer service, we were excited to invest in the Biesse AirForce system,” said Skip Labela, president. “Our investment in the AirForce system is another step toward continuously exceeding our customers’ expectations.”
Woodworking in Big Sky Country
Earth Elements also turns out custom cabinetry, millwork and furniture with manufacturing equipment sourced in Italy from SCM Group North America (Duluth, GA; www.scmgroupna.com).
Mike Wolfe, cabinet shop manager, said his Morbidelli Author M800 CNC router, Olimpic k800 edge bander, and DMC Eurosand L wide belt sander are some of the nicest, most advanced set of tools he’s ever used in his 13 years in the furniture business. “I’m extremely happy with them,” Wolfe said. Cabinet Vision, his preferred software for designing the custom cabinetry that makes up 80% of Earth Elements’ business, works “great” with his CNC, Wolfe said. Also, the Morbidelli, with its 16 foot by 6 foot table, is large enough for the live-edge – where the carpenter incorporates the natural edge of the wood – counters, bar tops, tables and headboards that are so popular in homes and businesses in Montana’s Big Sky Country.
“The capacity of the router is amazing,” Wolfe said. “It’s a great tool.” Wolfe dealt with the question of whether to have a pod-and-rail or nested-based router by having both. He designed a modification so that the Morbidelli can fulfill both roles.
Earth Elements in Bozeman, MT, turns out custom cabinetry, millwork and furniture with manufacturing equipment made in Italy by SCM Group.
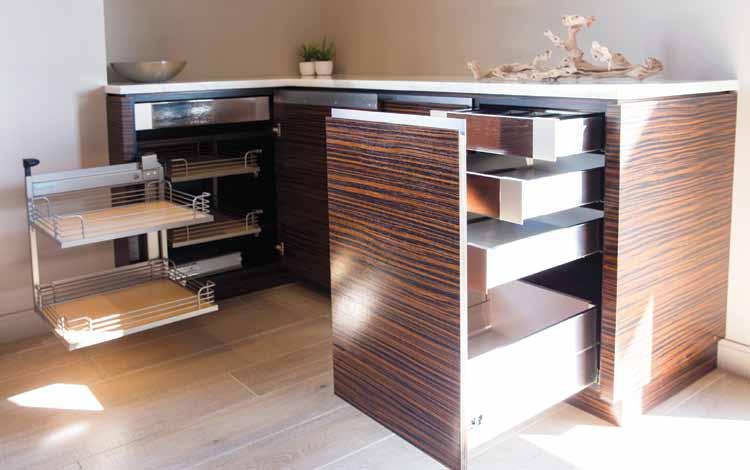
“It’s a pod-and-rail router, and I’ve converted half of it to a vacuum table,” he said. “This gives us the best of both worlds.
We can machine all four edges on the pod side. We can cut big tenons, which you can’t do on a table router. On the table side, we are able to do all of our nested-based routing. This is how we process all of our case parts for any cabinet job we are working on.”
SCM Group North America has five branches. In addition to the Duluth, GA, location, branches are in Carson, CA; Concord, NC; Toronto, Canada; and Guadalajara, Mexico.
SCM Group SpA (Rimini, Italy; www.scmgroup.com) was founded in 1952 and developed the first solid wood machining centers and door and window systems. It gained leadership in panel processing machinery through the acquisition of Morbidelli in 1985, followed by other companies. In 1992, SCM diversified into machinery for wood building components through acquisition of Routech and by developing new technologies. In 2002, it added machinery for processing advanced materials such as plastics, composites, glass and stone.
From grapes to leather
For another application for wood, take one look at the wooden tanning drums that Vallero International Srl (Torino, Italy; www.vallerointernational.com) makes, and you’ll instantly see the company’s roots in the Italian wine making tradition. The giant cylinders used for leather tanning and dyeing look like wine barrels that have been tipped on their side and pumped up with steroids.
Vallero has diversified the materials it uses to make the drums, but wood is still the most popular, accounting for two-thirds of production, said Marco Maroglio, sales area manager for North America and the northern part of South America. One-third of Vallero’s drums are plastic, and a small number that are used in laboratories are made of stainless steel.
“We have practically invented the drum as it is intended nowadays,” said Maroglio. “So this is the reason why in some countries Vallero means tannery drum just like Rollerblade means in-line skates.” North America represents 10-15 percent of Vallero’s overall business, with about 300 drums in use in Canada, Mexico and the United States, Maroglio said.
Vallero’s Vortex drum is one of the most advanced models available, and allows tanning and dyeing with low speed and a low environmental impact. Vortex represents operational energy savings of up to 70 percent, a 40-percent reduction in water used, and up to 50 percent more loading capacity.
Biesse Group is committed to Industry 4.0-ready technology, a crucial factor for operating in an increasingly global market.
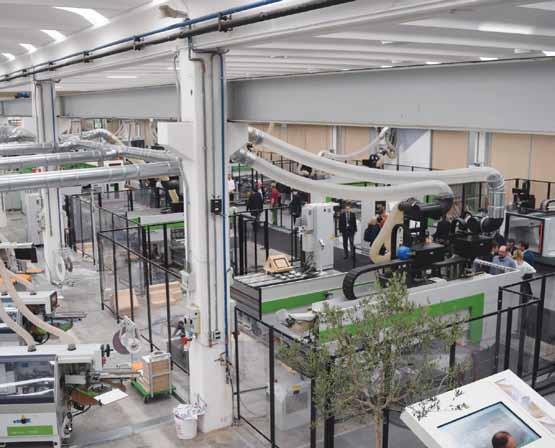
The interior of the drum is equipped with three wave-shaped “dragon” shelves to produce a “sponge effect” on the skins, which promotes better penetration of the chemical bath, guaranteeing uniform results. The dragon shelves also help to separate the skins for better exposure to the tanning and dyeing chemicals.
Vallero’s Eco-Drum, another advanced technology, is a modular system composed of a batch recirculation system, an automatic heating and temperature control system, and an AISI type 316 stainless steel filter.
Vallero’s advancements are right in line with the power-saving features that ASSOMAC’s members in the tanning industry have made a priority in their machinery, said the association’s Favazzi.