12 minute read
Heavy-Duty Machinery is Smarter and Nimbler Thanks to Italian Advances
The MAUS North America grinder installation at Pier Foundry & Pattern Shop in St. Paul, MN, was prompted by capacity constraints. It represents the ferrous foundry’s first use of automatic grinding. (Courtesy MAUS North America.)
Smarter and Nimbler Thanks to Italian Advances in Sensors, Processors & Information Networks
Frank Cunningham, founder and president of World Wide Stone Corp. (Scottsdale, AZ) so values quarry and stone processing machinery from Italy for his highly prized Durango Stone limestone and travertine that he describes his factories as being “Italian manufactured.”
Cunningham estimates his 22-year investment totals $17 million at World Wide Stone’s four quarries and three factories in Durango, Mexico, including purchase of state-of-the-art heavy earth moving equipment for his quarries and stone processing machinery for his factories.
Cunningham’s factories are equipped with loader/unloaders, bridge saws, high-speed gang saws, roller benches, robotics, gantry cranes and dryers from such Italian companies as Pedrini SpA (Bergamo, Italy; www.pedrini-italia.it) and Zonato SpA (Vicenza, Italy; www.zonato.eu).
Processing stone is a job that includes working with 30-ton (27.2 metric ton) blocks of limestone, swarms of dusty grit and rivers of water to manage the heat created during cutting to produce tiles, pavers and slabs along with custom countertops, fireplace mantels, fountains and more. Fortunately, Cunningham’s processing line is equipped with technology, such as robotics and sensors, that keeps things moving and eliminates the back-breaking work of pre-automation days.
MAUS grinders’ work on castings ranging from .5 to 5,000 lb (0.23-2,268 kg) can make robotics a necessity. Courtesy MAUS North America.
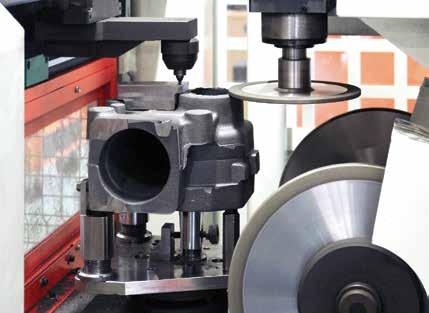
“Robots fill the production line,” read narration on a video showing World Wide Stone’s factory operations. “Sensors constantly monitor the strips (cut stone) as they move through the line.”
Cunningham didn’t just fall in love with Italian-made machinery; he may owe his success to the country.
One day, a client requested a stone called “statuary white” for his home. The client was from Carrara, Italy, and he explained to Cunningham that a mountain of white marble existed there. When Cunningham replied that the stone was not available in the U.S., the customer insisted that Cunningham go to Italy to acquire it—and that’s exactly what he did.
“The experience cemented my love of stone, its importance in the history of the human race and the joy and permanence of living with material that was only afforded kings for centuries,” Cunningham wrote on his company web site. Not only that, it introduced Cunningham to a number of old-timers in the stone industry who passed along their knowledge and backed him financially.
Pedrini and Zonato are represented by CONFINDUSTRIA MARMOMACCHINE, the association representing the Italian marble and stone machinery industries (www.assomarmomacchine.com). The technical and promotional group has about 320 members among producers of marble, granite and other ornamental stone, and the makers of machines, tools and equipment to work them.
Critical to mining that stone are earth movers like the ones Cunningham uses in his Mexican quarries.
Those types of machines represent a growing sector among exports from Italy: the industry saw a 14% growth in machinery shipped to other countries in 2017, according to figures from Unacea, the Italian trade association of construction equipment (www.unacea.org). Unacea, which has attracted about 50 members since its founding in 2010, also reports positive export growth in 2017 over 2016 for other sectors it represents, including road machinery (+20%); crushing and screening equipment (+15%); tower cranes (+9%); and concrete equipment (+7.5%). Only the exports of drilling machines decreased.
In fact, the Italian construction machinery and equipment industry continues to be one of the best in Europe in terms of production volumes. Italian products, renowned and appreciated worldwide, stand out for their high specialization, continuous technological innovation and elegant design. With a turnover of over 2.5 billion euros in 2014 ($2.9 billion in current valuation) and around 70% of its production exported, this Italian industrial sector includes about 200 companies.
Foundry parts largely untouched by human hands
Far from Cunningham’s quarries in Mexico is Cadillac Casting Inc. (Cadillac, Mich.), a major supplier of engineered ductile iron for the automotive, commercial vehicle, off-highway, industrial and railroad industries that recently bought a 600 G grinder machine from MAUS Srl’s (Campodarsego, Italy; www.maus.it) MAUS North American Corp. (formerly Palmer MAUS). Cadillac Casting was so impressed with the grinder that within a couple of months of installation, they ordered two more.
MAUS North America has been sending its automated and CNC grinding machines, high-volume/high-production vertical lathes and core shooting machines to locations in the U.S. and Mexico for about 20 years, with more than 70 installations. These are huge, costly machines that usually require up to nine months for a company to take the necessary budgetary and acquisition steps, so a sales volume of 10 of these behemoths each year is good business, said Matt Lis, general manager and chief operating officer of MAUS North America.
The North American division was established about three years ago and has eased any hesitation on the part of American and Mexican companies to buy from overseas because they know that technical support, service and parts are now readily available, Lis said.
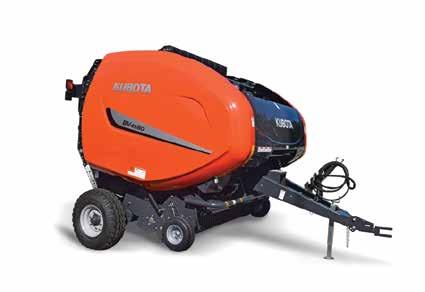
Kubota branding on balers made
in Italy may blur the lines of what defines an Italian company, but there’s no mistaking Italian
design and engineering. Courtesy Kubota.
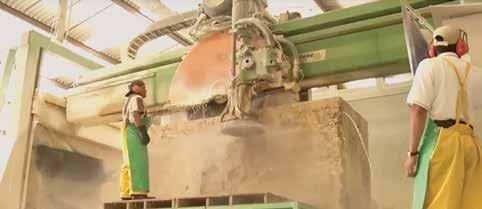
Robots fill the Italian-made production line at a World Wide Stone Corp. factory in Durango, Mexico. Image courtesy of World Wide Stone Corp.
“MAUS North America has invested in the U.S. market and intends to keep it,” Lis said. “The whole idea is to help the customer.”
The grinder machines and vertical lathes from MAUS North America are used by foundries for post-processing on castings made of iron, steel or aluminum to make parts primarily for the automotive industry, but also for the aerospace sector and job shops. The grinders work on castings ranging from .5-5000 lb (0.23-2268 kg): Cadillac Casting has the model equipped to handle parts ranging from 2.2 lb to 275 lb (1-150 kg).
The vertical lathe from MAUS North America has a smaller weight range, and is limited to turning, drilling and tapping parts, such as brake drums and wheel hubs of up to about 200 lb (90.7 kg). Core shooting machines are used to make the hollow portions of sand molds for parts, such as exhaust manifolds.
With the extremely heavy parts the company’s machines can accommodate, it’s not surprising that robots play a big part in their operation, and MAUS North America does a lot of work incorporating robotic gantries for machine loading or robotic arms for a variety of tasks, or both, in an installation. In their machine grinders, for instance, a robotic arm can either hold the part being machined or the grinding apparatus itself. The company has experience with robots from a number of companies and can often recommend the right robot for the right application. On networked automated lines, robotic arms are deployed for pick and place, vision systems, machine tending and more.
“Sometimes a part doesn’t get touched by a human until everything is machined,” Lis said.
Another foundry bought machinery from Lis’ company to double its finish capacity, according to an article on the Foundry Management & Technology website.
The installation at Pier Foundry & Pattern Shop (St. Paul, MN), was prompted by capacity constraints, and represents the ferrous foundry’s first use of automatic grinding. Pier Foundry manufactures gray and ductile iron and austempered ductile iron castings.
MAUS North America installed its 300 G automatic grinder there, which is designed for small- and medium-sized production lots of parts weighing up to 50 lb (22.7 kg). The flexibility of the range promotes complete part grinding, rapid changeover and simple offline programming. Along with the new machine, MAUS North America provided training on the programming table and software to create the tool paths. Pier Foundry’s 300 G grinder was installed in December 2017 over a week’s time.
1-888-italtrade “Overall, Pier Foundry was pleased with the fast installation,” Pier Foundry President Matt Grilz said. “Meeting the needs of our customers is very important to Pier, and we expect this machine to be a part of our steps into automation to improve efficiency, safety and deliveries.” Since 1946, MAUS and similar companies have benefited from membership in AMAFOND, the Italian Foundry Suppliers’ Association (www.amafond.com). At present, AMAFOND comprises the most qualified companies specializing in foundry products; machinery and plants; furnaces for melting and heat treatment; and die casting machines and equipment.
Back in Mexico, a group fostering the use of Italian-made foundry and metal forming machinery and expertise, the Italian Center for Innovation and Manufacturing-Hidalgo (Hidalgo, Mexico, www.ciimmath.org.mx), has reached a very special milestone. The center, also known by its abbreviation, CIIMMATH, is marking 10 years of representing Mexican-Italian technological cooperation, including teaching and manufacturing. CIIMMATH was created with the involvement of the Italian Ministry for Economic Development, the Italian Trade Commission and two Italian associations of machinery producers, UCIMU-SISTEMI PER PRODURRE - Association of Italian Manufacturers of Machine Tools, Robots, Automation Systems and Ancillary Products (www.ucimu.it) and AMAFOND, in collaboration with the Mexican Ministry of Economy, National Council of Science and Technology and Hidalgo’s Council of Science.
The underlying principle behind CIIMMATH was to create a center where industry and educational institutes could join forces to learn about Italian advanced technology and either function as an outsourcing site or learn about the processes and apply them elsewhere. Working within its walls are some prominent names in the Italian industrial sector, including Prima Industries Srl (Correggio, Italy; www.primaindustries.it), Colgar International Srl (San Pietro All’olmo, Italy; www.colgar.it), Tiesse Robot SpA (Brescia, Italy; www.tiesserobot.com), Promau Srl (Cesena, Italy; www.promau.com) and Idra Srl (Travagliato, Italy; www.idragroup.com).
Working on farms from sea to sea
In addition to heavy machinery used to mine and process stone and foundry equipment, Italian farm equipment is second to none.
Italian farm equipment manufacturers rank No. 1 in the world for the range of the types of machines they produce. Italy’s diverse climate and geography give its agricultural equipment producers
an edge over competitors because they require development of creative solutions for growers. Through their skill and expertise, the agricultural equipment companies consistently produce farming innovations.
FederUnacoma—the Italian Agricultural Machinery Manufacturers Federation (www.federunacoma.it)—represents a wide sector of mechanical engineering industries and brings together manufacturer associations of machinery, equipment and technologies for agriculture, gardening and groundskeeping. FederUnacoma’s member manufacturers account for 80% of Italian production and 65% of exports in the sectors it represents.
One of the manufacturers it represents is Enorossi Srl (Perugia, Italy; www.enorossi.it), a maker of heavy-duty farming, soil preparation and haymaking machinery.
Among the haymaking machinery are rakes and tedders Enorossi makes that practically fly out the doors of ACI Distributors (St. Louis, MO) during the summer months, said Brad Stout, co-owner. These are mid-level pieces of equipment that range in price from $3,000-8,000 and are used primarily by cattle operations for livestock feed. Stout said ACI sells to cattle ranches in 21 states in the Midwest, on the Gulf Coast and on the Eastern Seaboard of the U.S.
“The functions that they perform could not be done by hand,” Stout pointed out. “And they make it more efficient than any other means.” Balers and wrappers are manufactured at the Baler Competence Center in Ravenna (Ravenna, Italy; ien.kvernelandgroup.com). Baler manufacturer Gallignani SpA (Russi, Italy; kvg.gallignani.com) designs and engineers balers. for companies such as Kubota, also at its competence center in Italy.
If he were describing the advantages of Italian-made balers, he would point out how thorough and quick the intake mechanism performs, and the ability to pack more crop into a bale, said Tim Baker, product manager. While the models may differ, they all work on the same principle of rolling and compressing dry straw or wet hay under hydraulic pressure, he added.
“We make a very nice-looking bale,” Baker remarked. “Users have told us how much they like the density of the bales our balers produce.” Contributing to the balers’ performance is a group of almost 10 sensors that control bale formation: processing and measuring the growth of the bale, telling the driver when a bale is complete, and applying netting around the bundle that can weigh from 661-2,425 lb (300-1,100 kg).
These Italian-engineered and -made workhorses benefit from the massive distribution network and market share for tractors over many years in the U.S. and Canada, Baker said. He declined to share hard numbers but said the company’s balers and wrappers have “good” market share in Canada and “big volumes but building market share” in the U.S. These companies’ offerings are available via the Kubota dealerships in the United States, where it sold its first tractor in 1969, according to the website.
“We’re very strong in North America, and getting stronger,” Baker added. The logo for the Agency's U.S. Innovation Days Program, which was inaugurated in Sterling Heights this June and continues through 2019. The program focuses on Italian excellence in aerospace, automotive, advanced manufacturing and life sciences.
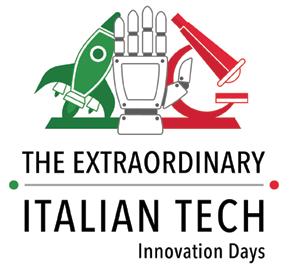
Italian, si, but with a U.S. presence All of the Italian-made hay tedders and balers, along with foundry grinders made by companies like MAUS and bridge saws used by World Wide Stone contribute to the growth of heavy machinery makers in the Mediterranean country, many of whom have set up shop across the Atlantic Ocean.
Based on the Agency’s sources, there are no fewer than 955 Italian companies with a presence in the U.S., with a majority (67%) along the Atlantic Seaboard and the South, according to Maurizio Forte, executive director of the Italian Trade Agency for the United States and Italian Trade Commissioner in New York (New York, NY; www.ice.it/en/markets/usa/new-york), who presented at Innovation Days 2018 in Sterling Heights, MI (www.id.ice.it). The remainder are in in the West (11.7%) and in the Midwest (21.3%).
Of the Italian companies with a U.S. presence, 35.1% make machinery, some with the latest technology: Among metalworking and machinery companies, 64% use additive manufacturing. In the Italian machine tools industry, there was a positive trend of 8.1% in exports to the U.S. from 2013 to 2017, Forte told Innovation Days attendees. Just as in the automotive industry, there will always be machinery that defines what is an Italian company.
As Cunningham of World Wide Stone saw when he traveled from Arizona to Italy, there is no mistaking the elegant design and robust engineering of heavy machinery—whatever the industry—made in the Mediterranean country. Maurizio Forte, ITA