33 minute read
INDUSTRY NEWS
CEOS KEEN TO BRING MANUFACTURING BACK HOME
Continued from cover
A new report has found a majority of business leaders across the Asia Pacific are actively reducing their reliance on China in their supply chains, which will reinvigorate the local industry.
The latest Asia Pacific CEO survey conducted by Westpac’s institutional arm found 57 per cent of large corporations in the region have begun to onshore supply and/or manufacture, to minimise risks within supply chains.
Surveying 113 chief executives, the report found two-thirds of firms had experienced significant supply disruptions during the coronavirus pandemic, and more than half had decided to manufacture onshore.
Some 63 per cent expected to continue this direction in the future, as CEOs are “likely to see such measures as helping to reduce supply dependence on China,” the survey found.
Westpac executive Anthony Miller said the new approach presented an opportunity to “reinvigorate” local manufacturing.
“We’re going to see a focus on smart manufacturing, which will create jobs – particularly high-skilled opportunities – and it’s going to see us build capability in areas where we can be very competitive on an international scale,” he said.
This shift coincides with fracturing trade relations between Australia and China, which has hit major exporters in the agriculture and resources sectors.
The relationship soured further when Chinese authorities slapped Australian wine makers with import tariffs of up to 200 per cent.
Mr Miller noted the responses by senior management during the pandemic had accelerated digitisation strategies, particularly using technology to cope with a remote workforce.
“A lot of businesses took actions to stabilise their operations out of urgent necessity, but in the process, many have brought in changes that promise future benefits — some unanticipated — in terms of efficiency and team cohesion,” Mr Miller said.
Westpac’s report also highlighted a number of firms remained resilient during the pandemic and were able to adapt to changing demand and operating conditions.
According to the survey, 69 per cent of CEOs said they had become more resilient as a leader, while 72 per cent of respondents said organisational decision making had become quicker.
Westpac’s report surveyed chief executives from 113 companies located in Australia, China, Japan, Singapore, Indonesia and New Zealand. The survey was conducted in July and August.
One-quarter of the respondents are based in China, 20 per cent are based in Indonesia, and the balance are divided equally between Australia, New Zealand, Japan and Singapore.
Their companies are distributed across a wide range of industries, with the largest representation from consumer goods (14%), construction and real estate (11%), and financial services (10%).
Anthony Miller - Westpac institutional chief
THE DEATH OF FIELD SALES
This book shows a better way to grow sales significantly faster than expenses, as we return to business as usual. Get the first four chapters FREE at deathoffieldsales.com
Yours FREE
The days of large field-based sales teams are numbered. Most customers don’t want it and most businesses simply can’t afford it! The Machine presents a radically different approach to sales where salespeople just sell. 11x more selling
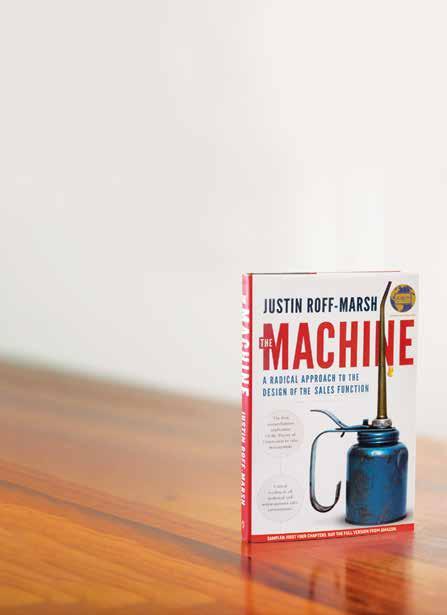
It shows how to generate up to 11x more selling conversations for salespeople compared to what your competitors are doing—without adding significant expenses.
GET IT NOW:
deathoffieldsales.com
NEUMANN STEEL CELEBRATES 50-YEARS IN BUSINESS

The oldest, family-run reinforcing steel business in the country, Neumann Steel, is celebrating 50 years in business.
Part of the Neumann Group, the company has grown from a tenacious operation to a proudly Australian-owned and operated company, employing more than 220 people.
Run by second generation directors – Marc and Paul Neumann along with Mark Shearman – as part of the wider Neumann Group, the steel business has flourished over the decades.
“We’ve always innovated, delivering steel solutions to support projects big and small,” said director Marc Neumann.
“In the 1980s, we were the first in the country to innovate with rib wire and rib mesh, transitioning it to the domestic market. We’ve always been responsive, serving our customers’ needs, no matter the size of the job.”
The company has had a hand in many projects including the Q1 tower, Jewel Resort, the Gold Coast Light Rail, the Toowoomba Range Crossing. Neumann Steel also supplies residential home builders throughout south east Queensland and the Hunter Region.
The Neumann Group started its first business, sand mining in Currumbin, in 1948. It then began Neumann Dredging to mine for more sand as demand grew. With the excess gravel from dredging, it started Nucon and produced concrete. In 1970 the family opened Nucast to manufacture precast concrete products, which evolved into Neumann Steel in the late 1980s.
Neumann Steel operates the largest mesh manufacturing facility in Queensland supporting the reinforcing steel for a large portion of the residential housing market, while also specialising in the supply of custom reinforcing steel required in the commercial and civil markets.
Neumann Steel www.neumannsteel.com.au
HOLLOWAY GROUP LEADS CALLS TO ‘BRING IT HOME’
Continued from cover
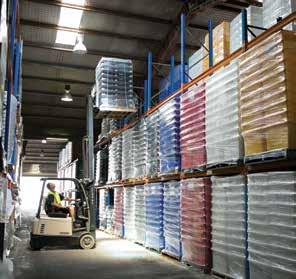
As the economy recovers from an unprecedented 2020, there is a renewed focus from government and industry to bolster the local manufacturing sector through both innovation and onshoring production.
At its height, Australian manufacturing accounted for roughly 25 per cent of Australia’s Gross Domestic Product. But in 2019, manufacturing was reported to account for a mere 5.65 per cent.
Many companies who left our shores are finding freight costs increasing, supply chains disrupted and impacts surrounding uncertain trade relations.
“We’re getting people to really think it – if I get a Chinese supplier quoted and an Australian supplier, well, the Chinese supplier still might be cheaper, but if you look at all the added costs, lead time and some of the less tangible as well, I think you’ll find it’s just as appealing to procure locally.”
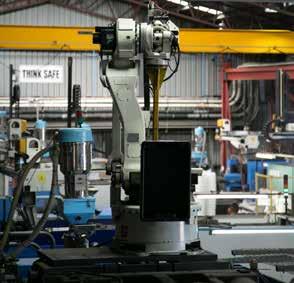
But now, many are returning.
With the economic, logistics and health impacts of Covid-19 continuing to ripple through global markets, one Sydney company has taken up the charge to be a leading voice in promoting Australian-based manufacturing.
Innovation facilitator and manufacturer Holloway Group has launched a call to action for local businesses to refocus their efforts to onshore production, with their ‘Bring it Home’ campaign.
Spearheading this initiative is Holloway Group Managing Director Matt Holloway, who sees 2021 as the perfect time to embrace the opportunities and benefits presented by manufacturing in Australia.
“Our goal is to get our industry and prospective clients to think a little bit differently and to change their behaviour around purchasing,” says Matt. “The ‘Bring it Home’ campaign is an educational piece for us to make some noise about our industry and for manufacturers across Australia.”
The campaign highlights four key advantages to local manufacturing: Avoiding up-front payments leading to better cash flow; the ability to not having to hold so much inventory; avoiding many costs associated with overseas markets and exchange rates; and faster lead times and better customer support.
“The stereotypical thinking that it’s cheaper to get something manufactured overseas – we really wanted to shift that paradigm. It’s not the case anymore at all,” says Matt.
“Lead times are one issue, but the actual bottom line expense cost has literally doubled.
“A container out of Malaysia has increased by 80 per cent over the last 6 months and climbing. Companies have to absorb that cost. You can try to subsidise as much as you can, but it gets to a point where you have to pass it on to clients.
After operating as A Plus Plastics for the past 20 years, the company rebranded to Holloway Group last year. Their subsidiaries include Ausdrain, GEOHEX and Group Tooling – A Plus Plastics remains as a brand for their range of industrial grade packaging solutions for supply chain markets.
Holloway Group specialises in the design, tooling and manufacturing of plastic injection moulded products, with a real focus on research and development. Ausdrain manufactures and distributes drainage cell products and stormwater management products, specialising in modular underground tank systems.
Holloway has implemented a successful social media campaign to get the ‘Bring it Home’ message out there as well as via a rigorous sales team throughout Australia.
Matt is hoping for more engagement in ‘Bring it Home’ and says the industry should band together.
“I think this is definitely a precedent for more companies like ours to bind together and really promote the campaign.
“This is a real opportunity for like-minded companies to come together to rally and make some noise about Aussie manufacturing.
“If we could convince even one new client to come on board, then it was well worth it.”
Holloway Group 02 9603 2088 www.bringithome.net.au
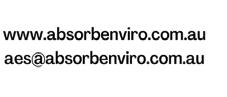
SA LEADING NATION INTO THE FINAL FRONTIER
South Australia has flagged its intentions to be the nation’s leaders in the emerging space manufacturing sector.
The state government has launched its Space Sector Strategy, which will focus its activities in space industry and research to propel SA’s growth in the area and contribute to the national agenda.
The new strategy will aim to drive the state’s contribution to the Australian Space Agency goal of tripling the size of the nation’s domestic space industry to $12 billion by 2030, helping to create thousands of jobs.
Premier Steven Marshall said jobs creation was a major factor in South Australia’s eagerness to expand its space capabilities.
“Our vision for growth is simple – by 2030, South Australia will be designing, manufacturing, launching, and operating SmallSats (small satellites) to deliver actionable, space-derived intelligence for sovereign Australian missions – creating hundreds of jobs in the process,” he said.
“Businesses in the space sector will be creating thousands of job opportunities for South Australians over the next decade which is great for our economy.”
Mr Marshall made it clear that South Australia’s space sector will be critical in the state’s economic recovery from the global coronavirus pandemic.
“While the impact of the COVID-19 pandemic has unequivocally affected the space sector, South Australia’s space sector growth target projects above average growth of 5.8 per cent for the next ten years,” he said.
“Space is one of the nine sectors we have identified as a priority in our plan for further economic prosperity, helping to keep SA safe and strong and helping to create new jobs in this exciting sector.”
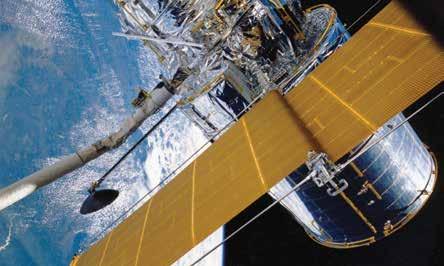
The strategy was drafted in collaboration with industry and is a crucial part of South Australia’s broader Growth State Strategy, a partnership between the South Australian Government and industry to accelerate our economy through business expansion and innovation.
South Australian Space Industry Centre (SASIC) chief executive Richard Price says the already thriving South Australia innovation ecosystem is already in take-off with the emergence of new and disruptive markets.
“While traditional space-related services fundamentally underpin our way of life on Earth and deliver a large proportion of the revenue attributed to the space sector, there are phenomenal opportunities for the new breed of spacerelated services that are unencumbered by legacy practice,” he said.
“These NewSpace-enabled products and services have strong potential to improve the productivity and competitiveness of virtually every sector of the broader economy, as well as making a direct contribution to growth in South Australia.
“We are committed to getting behind new entrants in the space industry and supporting domestic and international companies to develop and grow innovative and disruptive ideas contributing to our space sector.”
NEW LOGISTICS HUB SET FOR WESTERN SYDNEY
The NSW Government has approved construction of a new warehouse and distribution hub, securing up to 1,650 new jobs and $242 million in economic investment for the surrounding region.
Minister for Planning and Public Spaces Rob Stokes said the approved new Kemps Creek Warehouse, Logistics and Industrial Facilities Hub will help combat the economic impacts of COVID-19 by delivering investment and new job opportunities for Western Sydney.
This approval will allow for the construction of eight buildings as well as earthworks to be carried out and infrastructure built across the entire hub. The development of the rest of the hub will be subject to future development applications.
Construction is expected to begin this year and will be undertaken in stages with the first building to be completed within 12 months.
“This development will create 700 construction jobs and 950 operational jobs while injecting $242 million into the Western Sydney economy,” Mr Stokes said.
“The approval means we can get shovels in the ground faster. This government is committed to fast-tracking planning assessments to help stimulate the economy during the pandemic.”
The new development is a joint venture between Frasers Property Partners and Altis Bulky Retail. The hub will include major global retailers, e-commerce providers, health and pharmaceutical industries, warehousing and logistics operators, light manufacturing and data centres.
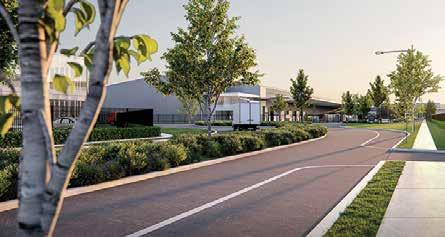
Minister for Jobs, Investment, Tourism and Western Sydney Stuart Ayres said the investment was a vote of confidence in the future Aerotropolis.
“Creating jobs and boosting business is a priority for the NSW Government and this Hub means work for hundreds of people, during both construction and when the warehouse becomes operational,” Mr Ayres said.
“This is just another example proving that COVID-19 won't stop NSW from growing stronger, and the Hub also supports our plan to foster new sources of growth, jobs and investment in Western Sydney.”
Member for Mulgoa Tanya Davies said that the development will contribute to Western Sydney’s growing employment force and benefit from its prime location close to the Western Sydney Airport.
“Western Sydney is establishing itself as a strong industrial and employment growth area. The construction of a new warehouse and logistics hub is going to substantially add to this growing reputation and attract more investment that will benefit our western Sydney community,” Mrs Davies said.
“Once fully complete, the entire hub could support up to 2,000 operational jobs.”
“I couldn’t be happier with the service provided by Applied - it’s been terrific. I wouldn’t go anywhere else for my next machine.”
KEITH MORTON, LASERMECH, SALISBURY PLAIN, SA
At Applied Machinery, we treat our customers business’ as an extension of our own. We view ongoing service, training and support as critical to ensuring our customers can extract maximum return from their machinery investment. Our number one priority is ensuring that our customers across the country get the machinery they need, with the support they expect. With nearly 30 years’ experience, and thousands of satisfied customers across the country we’re here for the long term. We’re a true machinery partner – just ask Keith Morton. Real Service. Real Support. Real People. That’s Applied Thinking.
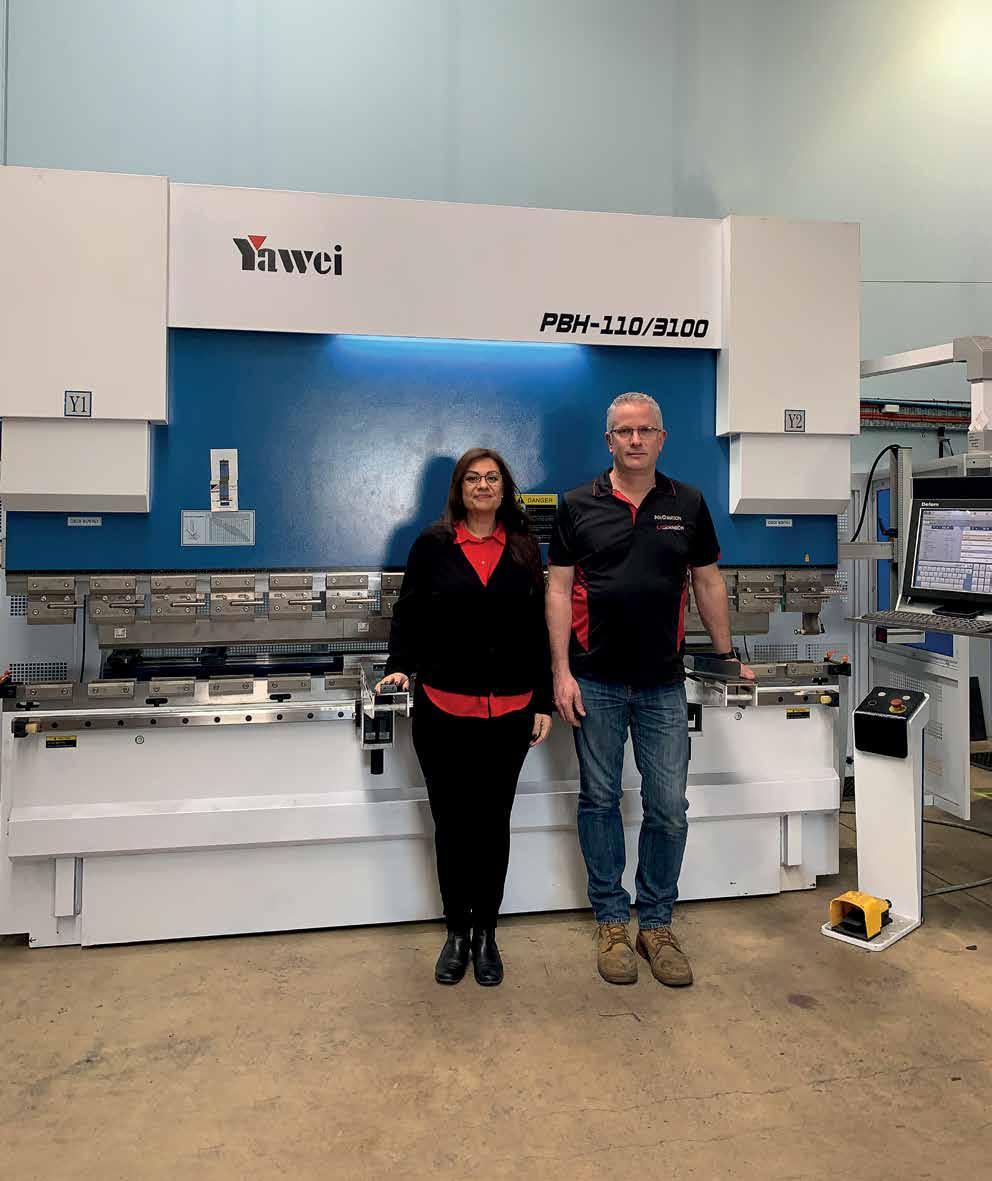
AUSTRALIAN MANUFACTURING WEEK 2022 OPEN FOR EXHIBITOR BOOKINGS
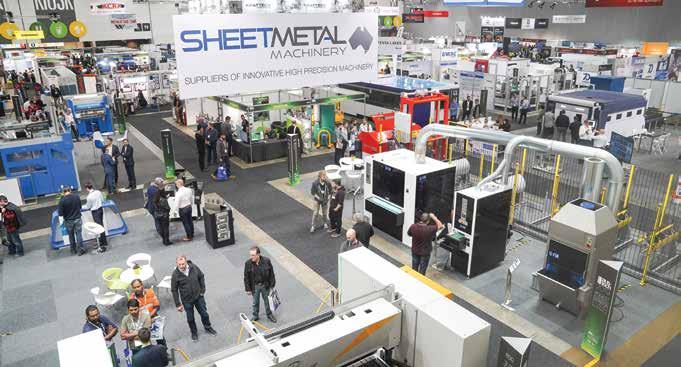
Looking to get your company or product front and centre of prospective clients?
The Australian Manufacturing Technology Institute Limited (AMTIL) has announced the opening of space bookings for Australian Manufacturing Week 2022, to be held in Melbourne next March.
Proudly owned and operated by AMTIL, Australian Manufacturing Week (AMW) is Australia’s premier manufacturing solutions event.
Co-located with Austech, AMTIL’s longstanding advanced manufacturing and machine tool expo, the inaugural edition of AMW will take place at Melbourne Convention & Exhibition Centre (MCEC) from 8-11 March 2022.
As the largest event covering manufacturing and engineering scheduled to be held in this country, AMW 2022 promises to be an unmissable highlight of next year’s Australian manufacturing industry calendar.
With significant advanced interest from industry since AMW was first announced last July, the opening of bookings marks a major milestone in preparations for the show. Organisations considering participating are strongly advised to contact AMTIL promptly to secure their place.
“We are excited to announce that Australian Manufacturing Week (AMW) is now open for stand bookings,” said Kim Banks, AMW Exhibition Manager and Head of Events at AMTIL.
“With a strict cap on available space for 2022, exhibitors may find themselves jostling for a position as the postponement of several exhibitions in 2021 increases demand for stands.”
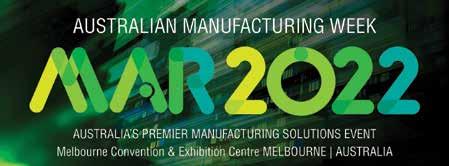
AMW was announced in July 2020, following the decision by Reed Exhibitions to cease operation of National Manufacturing Week (NMW), which had been held in colocation with Austech for 20 years.
With NMW’s discontinuation, AMTIL saw an opportunity to build on the consistent success of Austech and broaden its events portfolio, developing a comprehensive showcase that would highlight the full extent and diversity of Australian manufacturing today and the technologies, processes and innovations shaping its future.
“AMW is the natural new home for exhibitors who have participated in NMW in the past,” Banks added.
“Australia is a complex marketplace for metalworking trade shows or machine tool expos, so to have one single event that showcases Australian manufacturing in its entirety is something we believe the industry will value and benefit from.
“Our ambition is for AMW to become not just an exhibition, but the focus of a weeklong celebration of manufacturing and its value for Australia today.”
Exhibitors at AMW 2022 will have the opportunity to present their products and services to some of the most influential customers from across Australian manufacturing.
AMTIL prides itself on the high calibre of visitors it attracts to its events. Visitors to AMW will represent industries such as: aerospace; defence; automotive; marine/ shipbuilding; medical, biotechnology & pharmaceutical; petroleum, coal & chemicals; plastics & rubber manufacturing; materials handling & warehousing; recycling; electronics; and telecommunications & IT,
With AMW covering the entirety of modern manufacturing, and with such a diverse array of visitors in attendance, the exhibition will feature a number of dedicated Product Zones covering specific segments or aspects of the industry.
These specialised areas will help visitors to AMW find the products and services of most interest to them, while giving exhibitors the option to choose the most suitable location for their stand.
AMW 2022 will include the following Product Zones: showcase of state-of-the-art machine tools and ancillary equipment.
• Additive Manufacturing. The latest advances in 3D printing, featuring exhibits from users, suppliers and supporters of additive manufacturing.
• Digitalisation (IoT). Exploring how developments in digital technology and the Internet of Things (IoT) are ushering in a new era of smart, connected manufacturing.
• Air Technology. Highlighting a range of cutting-edge compressor systems and associated technologies.
• Engineering Solutions. Engineering plays a vital role in modern manufacturing – this pavilion will display equipment and tools for a broad cross-section of engineering disciplines.
• Manufacturing Solutions. Optimised solutions to the most common challenges experienced by manufacturers, from materials handling and warehousing to integrated manufacturing solutions.
• Manufacturing Safety. The latest technologies, products, and services to improve occupational health & safety (OH&S) standards and compliance and reduce safety expenditure.
• Robotics & Automation. Featuring the latest cutting-edge equipment and processes for the optimisation and automation of manufacturing operations.
• Weld Solutions Zone. Highlighting advanced welding processes, with high-quality interactive experiences that demonstrate new developments and applications in the welding sector.
• Australian Manufacturers Pavilion. First launched at Austech 2013, this area showcases the capabilities of some of
Australia’s precision engineering and advanced manufacturing businesses.
“There’s definitely going to be a lot going on at AMW next year, and we’ll be making further announcements over the coming months,” said Banks.
“Keep an eye on the AMW website (www.australianmanufacturingweek.com.au) or follow our social media channels to stay up to date. And if you are thinking of exhibiting, don’t hesitate to get in touch – you don’t want to miss out.”
HOW THE PANDEMIC BECAME THE CATALYST FOR CHANGE IN MANUFACTURING
For all the challenges COVID-19 has delivered, it has also highlighted the agility and innovative nature of Australia’s manufacturers. This report by Industry Update, based on a St.George special report – The 2020 Revolution – examines the impact on the sector.
As the coronavirus pandemic has upset just-in-time global supply chains, Australian manufacturers large and small have moved with extraordinary agility during the crisis – quickly transforming to produce products most immediately needed to keep Australians safe, from face masks to hand sanitiser.
Simultaneously they have been shoring up their own longer term futures by finding different ways to co-operate, manage supply chains, accelerate innovation, transform business processes and reach new markets.
Along with exposing the gaps in Australia’s manufacturing supply chains, COVID-19 also revealed the nation’s vulnerability, as a commodity-based economy, to external shocks, and highlighted the need to reverse the hollowing out of our manufacturing capability, says Professor Roy Green, Chair of the University of Technology Sydney Innovation Council.
While many businesses have been severely compromised by the effects of the global pandemic, a large number of Australia’s quick-acting manufacturers have capitalised on the opportunity to transform, tapping into a groundswell of support for local products while also becoming more globally competitive.
Overall, manufacturers are finding innovative ways to do almost everything, from changing the types of products they make, to rethinking production methods, supply chains, distribution models and logistics.
Typically, they are collaborating online to achieve success with new partners. “They’ve realised the power of working together … and sharing that knowledge to transform their business. It’s really the digital transformation of manufacturing,” says Michael Sharpe, NSW Director of the Advanced Manufacturing Growth Centre (AMGC).
Commonly, companies are initially agreeing to collaborate in the national interest. Take the example of US company Stryker. Faced with surging demand for hospital beds, Stryker called the AMGC for help in establishing manufacturing in Australia.
Within hours the centre had pulled together a local supply chain. Mattress manufacturer A.H. Beard, wheel and castor maker Fallshaw, vehicle conversion specialists AmTek Australia, and fabrication and engineering company Varley Group joined Stryker South Pacific to get production moving ASAP.
“Within two weeks the first hospital beds were being produced”, says Mr Sharpe. Now, 500 hospital beds have been procured by the Department of Health in Western Australia.
For the Australian businesses involved “the goodwill and the willingness to adapt and stand up for the nation was certainly a proud moment”, he says.
There has also been a welcome fundamental shift in how manufacturers market themselves. “We’ve got members that are doing heavy engineering work, producing low-
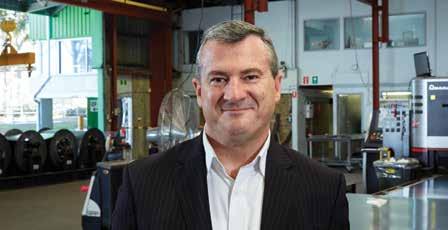
Matthew Kelly - St.George’s Head of Manufacturing and Wholesale
It’s a wake-up call. Frankly I don’t think people want to be – as dependent on China anymore.
“They are able to support each other across phone calls and sharing knowledge about what it takes to incorporate robotics technology into an engineering firm,” says Mr Sharpe.
Next horizons: what lies ahead?
loader trailers in the mining and earthmoving sector … but suddenly advertising on Facebook and finding new customers. It shows a new willingness to try new things in new ways,” says Mr Sharpe.
What the next normal means for manufacturers
Plans for greater national selfsufficiency, shorter supply chains and onshore manufacturing are well underway.
While a post-COVID world will certainly look different, the pandemic won’t spell the end of doing business globally for Australian manufacturers. However, there will “definitely be a reset”, says Tim Harcourt, the J.W. Neville Fellow in Economics at UNSW Business School, and part of that will involve a diversification of supply chains.
The pandemic provided a wake-up call.
“I don’t think people want to be – frankly – as dependent on China in the global supply chain anymore,” Mr Harcourt says. Certainly some will bring their manufacturing back home, he predicts, while many others will trade and work more widely around South-East Asia and North-East Asia.
St.George’s head of manufacturing and wholesale Matthew Kelly says the early government support to bring more manufacturing back onshore is encouraging. Federal Minister for Industry, Science and Technology, Karen Andrews has already flagged the need to “get behind the push to diversify our supply chains”.
One of the challenges will be skilling of the workforce, says Mr Kelly. With higher unemployment, some deep thinking is needed on how TAFE, government and industry can work together to attract and train potential new manufacturing workers, including those recently unemployed from different industries.
Just what policy settings are needed is something many hope the National COVID-19 Coordination Commission – tasked with breaking through bottlenecks and fixing economic and social problems caused by the pandemic – is examining.
While the COVID-19 crisis has exposed deficiencies in Australia’s economic approach, Professor Roy Green, Chair of the University of Technology Sydney Innovation Council is asking for a fundamental redesign. He is calling for a new National Industrial Strategy Commission, or similar central agency, to develop priorities in consultation with industry sectors, aimed at growing industries of the future with new technologies, skills and business models.
From the Australian government, a robust, properly funded national policy framework is required, while the states should carry much of the responsibility for delivering business services and infrastructure for innovation hubs and industry clustering, he says.
Building capabilities for the future
Manufacturers are primed to bounce back and for those who do, the pandemic-induced trend towards collaboration will need to continue into the future.
“Collaboration is a key driver for advanced manufacturing,” says Michael Sharpe. “We need more and more companies working together and supporting each other.”
Currently many companies are sharing resources – including staff and skills. “There’s a great community movement happening out there right now,” says Mr Sharpe. He cites the example of metal fabricator Rose Valley Steel Works in Armidale in north-west NSW collaborating with industry counterpart R&R Murphy, four-hours’ drive south, to share knowledge on robotics production.
Many Australian manufacturers have been operating at warp speed since coronavirus hit.
Their “fluid and fast-moving” response demonstrates beyond measure the smarts of our manufacturing community, says AMGC’s Michael Sharpe. “We’ve got 47,000 manufacturing companies in Australia and I see that as a key strength, because the majority of them are small and family businesses, but the ability to be agile and adapt quickly is a key strength to Australia’s economy.”
St.George’s Matthew Kelly is convinced many of the changes adopted to date will stick. He looks to the future of the sector with a fresh positivity. Clear indicators are in simple facts, such as the 30 per cent of manufacturers who, amid the turmoil and uncertainty, have actually changed their processes in recent months, he says.
“There needs to be a positive out of this pandemic, and in the vast majority of cases, I think it has been good for the manufacturing industry,” Mr Kelly concludes.
This information is general in nature and has been prepared without taking your objectives, needs and overall financial situation into account. For this reason, you should consider the appropriateness for the information to your own circumstances and, if necessary, seek appropriate professional advice.
St.George Bank 0412 265 197 www.stgeorge.com.au/ manufacturing
DELPHI DELIVERS A LOAD CELL RECORD
A Queensland bespoke manufacturer has crafted one of Australia’s largest wireless tension load cells, with a lifting capacity of 300 tonnes.
Delphi Measurement answered the call of a client who saw a gap in the market for a “Big Daddy” of load cells, after learning there were none on the entire east coast of Australia.
Queensland Rigging Hire approached Delphi to see if it was up for the challenge of manufacturing a customised large-scale load cell at its Burleigh Heads factory.
“The largest we’d previously made was 250 tonnes,” Delphi co-owner Mike Leonard says. “But we were confident we had the equipment and the skills to do it.”
This “can do” attitude is at the heart of Delphi’s reputation as a small Australian manufacturer holding its own in a market rife with ready-made, often lower quality overseas product.
Delphi has consistently invested in larger machining and material handling capability to accommodate such orders, including designing and building its own curing oven and portable lifting equipment to manufacture supersized load cells.
“We’re well set up now to meet those large-scale orders,” Mike says. “We take pride in being able to deliver exactly what our clients are looking for.
“For us, it’s always about quality and making sure that everything is 100 per cent right.”
The cell was too large for Delphi to calibrate in-house so it was sent away to an independent calibration lab where it achieved Class A accuracy across its range.
“We were pretty proud of that,” Mike says.
Delphi has been specialising in customised load cells, load pins, tension cells and force measurement equipment for more than three decades.
The company is highly valued by its clients for coming up with bespoke solutions across a range of applications and industries, including mining, gas, defence, heavy industry, construction, marine and food and beverage production.
The owner of the “Big Daddy” load cell Queensland Rigging Hire boss Ben Fitzgerald says the cell found fame of its own after he posted news of its arrival on LinkedIn.
“There was a huge response to it in the industry,” Ben says. “It’s a pretty rare, big piece of equipment and it’s great to be able to say that it was designed and manufactured in Australia.”
Ben says he was confident Delphi was the company for the job, having purchased more than 30 Delphi load cells since he launched his business five years ago.
“Going with Delphi is honestly the best decision I’ve made for the business,” Ben says.
“A lot of my other equipment comes from Europe and to get it serviced, I have to send it back overseas. It’s expensive and it can take gear out of the system for months.
“It’s been great to be able to source good quality and well-priced equipment made in Australia. You also get the service too and that’s a big reason we keep going back.”
It’s a glowing endorsement of Delphi, an Australian manufacturer committed to delivering solutions, not just products.
NEW RISC-V RESOURCE PAGE FROM MOUSER
Mouser Electronics, the New Product Introduction leader empowering innovation, has created a new resource site dedicated to RISC-V, an open source instruction set architecture (ISA).
RISC-V offers exceptional freedom for extensible hardware and software on architecture, as it is unconstrained by proprietary architecture standards.
The open source ISA is a key factor in the continued development of revolutionary technologies such as 5G, artificial intelligence, and the Internet of Things (IoT). RISC-V is supported by a worldwide community that believes in the sharing of ideas inherent to the open source vision.
Mouser’s new RISC-V resource site features articles on several innovative uses of the technology, such as internetconnected AI facial detection, open source security, and flexible processor design.
The site also explores some of the key strategies used in RISC-V development, and includes videos and product information for RISC-V-based development kits.
Mouser offers a broad selection of RISC-V-based devices, including the Microchip Technology PolarFire SoC FPGA Icicle Kit. The kit is a low-cost platform that enables reliable computing for applications including industrial automation, IoT devices, and automotive applications.
The Terasic Technologies T-Core FPGA MAX 10 development board is a robust hardware design platform that supports protocol bridging, analog-todigital conversion, and motor control drive.
Engineers and designers can access the comprehensive new site by visiting https://resources.mouser.com/risc-v
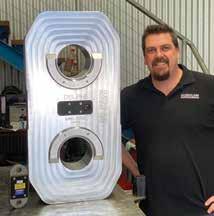
It certainly underscores the company’s unofficial motto: “no job is too big or too small”.
Delphi Measurement (07) 5508 2498 www.delphimeasurement.com
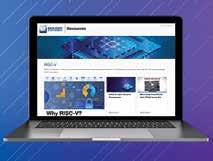
Mouser Electronics +852 3756 4700 au.mouser.com
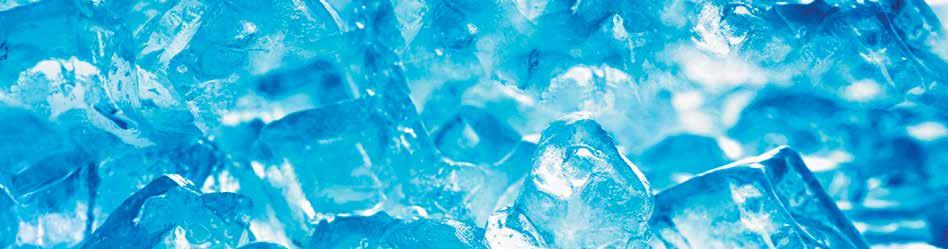
KEEP COOL
ENCLOSURE CABINET PRECISION COOLING
Designed to keep your electronics cool and operating at optimum performance.
- Cooling capacities range from 200W to 6kW. - IP Ratings – IP54 & IP56. - Mild Steel and Stainless Steel finishes. - Seifert also offer Heat Exchangers, Peltier Coolers and Fan Systems - complete Thermal Solutions.
info@seifertsystems.com.au / +61 3 9801 1906 seifertsystems.com.au
NSW BUILDS WORLD-CLASS INTERMODAL HUB
Construction is underway for the Riverina Intermodal Freight and Logistics hub which will enable the exporting of freight across Australia and abroad.
Deputy Premier John Barilaro said the development of the 60-hectare Bomen Industrial Precinct near Wagga Wagga is fantastic news for the Riverina region, boosting the capacity to share our exports with the world.
“This precinct will make Wagga Wagga a major player in domestic and international freight export, making the town even more attractive to local and international businesses,” said Mr Barilaro.
“This intermodal facility will be a worldclass business hub servicing the region’s advanced manufacturing, recycling and renewables industries and help local businesses reap the benefits of the Inland Rail and Wagga Wagga Special Activation Precinct.”
With a view to creating vital jobs in the region, the NSW Government is investing $43.7 million in the project – due for completion by mid-2022 – and has significant investment from Wagga Wagga City Council and commercial partner Visy Logistics.
Minister for Regional Transport and Roads, Paul Toole, said the RIFL hub, the Inland Rail and the Wagga Wagga Special Activation Precinct will work hand in hand to fast-track access to national and international markets for regional businesses and products.
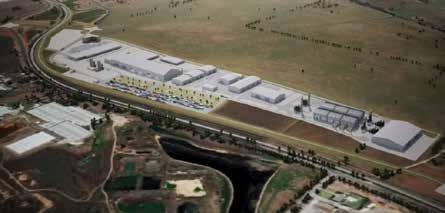
“When completed, this hub will give regional businesses ready and cost-effective access to markets across Australia and around the world, and there’s never been a more important time as we recover from drought, bushfires and the Covid-19 pandemic,” said Mr Toole.
“It’s also going to reduce the number of trucks moving through the Wagga Wagga central business district, giving local roads back to the local community.
“The upgrade will provide the precinct with enabling infrastructure and a 4.9-kilometre master rail siding and container transfer terminal.
“Preliminary site preparation work and earthwork activities are already underway, ahead of the construction of power, stormwater and sewerage connections to the industrial precinct and the laying of rail tracks and turnouts.”
NSW Nationals MLC Wes Fang said the project will deliver incredible benefits to the Riverina, cementing its reputation as a manufacturing and freight hub.
“This is a great example of how state and local governments can work together with industry to deliver projects that will benefit regional communities and economies in the Riverina for generations to come,” said Mr Fang.
Wagga Wagga City Council Mayor, Greg Conkey, said it was exciting to finally see the start of site works on the ground-breaking investment in the city and its surrounds.
“It has been 15 years in the making and it is an example of a genuine partnership between state and local government and industry,” said Mr Conkey.
“The RIFL hub terminal will be the core for future growth and expansion in the Bomen Special Activation Precinct, generating up to 6,000 jobs in this region, and has the potential to drive the economic future of the city for decades.”
SCLAA HIGHLY COMMENDED AUTOMATION SOLUTION: SAFELY STORES 6 CLASSES OF DANGEROUS GOODS
SCAN THE QR CODE BELOW TO SEE THIS AUTOMATION IN ACTION
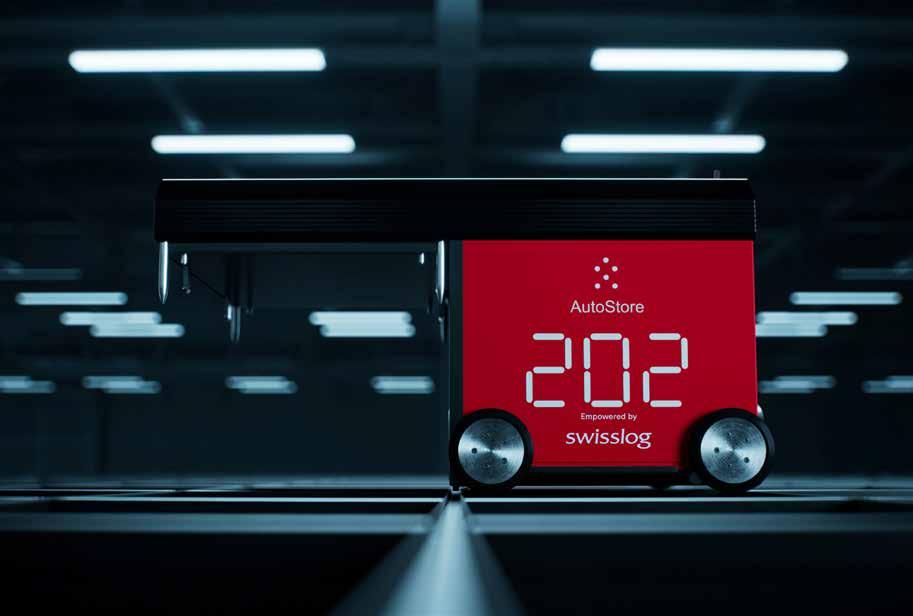
RADIO-CONTROLLED ROBOTS HELP LINFOX BLAZE PATHWAY TO WAREHOUSE AUTOMATION
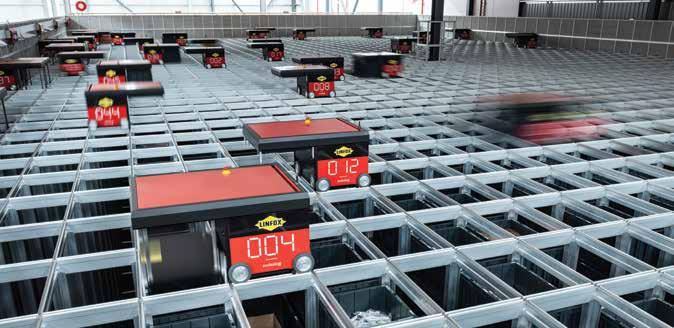
The world’s most compact and secure goods-to-person automated storage and retrieval systems is being used by Australia’s largest privately-owned logistics company to deliver speedy and safe service to its client’s customers.
The ultra-high density AutoStore system, powered by Swisslog, has been chosen by logistics leader Linfox for a new consumer products facility in western Sydney.
The facility accommodates more than 20,000 bins of high value product served by 45 robot-wheeled bins in an automatic storage and rapid despatch system occupying a floor of just 700 square metres.
The efficient new automation system received “highly commended” recognition by the Supply Chain & Logistics Association of Australia (SCLAA) in the “Best Supply Chain Management” category of their annual awards held in December 2020.
Linfox President, Consumer and Healthcare Group, Kylie Fraser, says the system places Linfox “at the very forefront of efficient automation, a subject about which we are passionate because of the benefits it brings our customers.”
“Linfox is leading the way with investment in exceptional supply chains to help our customers grow stronger and work smarter,” Ms Fraser said.
“We work with our customers and partners using business insights and technology solutions that create better operational models and performance.
“Our valued global consumer goods customer required a bespoke solution to deliver growth through more efficient capacity, productivity, accuracy and speed to market. After an extensive selection process to find an automation partner that understood our customer’s needs, we chose Swisslog.”
Compared with conventional nonautomated warehousing, AutoStore systems offer a 60 per cent reduction in inventory storage footprint, a 50 per cent increase in picking speed and inventory record accuracy of more than 99.9 per cent.
The highly secure but easily operated system is among the latest of more than 500 AutoStore systems delivering such benefits globally, including one employed by the FBI in the USA to safeguard and efficiently manage millions of paper records.
It works by using radio-controlled, battery-powered robots which move along a grid on top of stacks of bins. When a picking order comes in, robots lift bins from the stacks and deliver them to the picking station, where an operator verifies the contents and adds picks to the order.
The robot then returns the bin to storage. New stock is loaded into bins for storage, and as soon as those bins are stored, they are ready to be picked.
Swisslog Australia Managing Director, Francis Meier, says the system is ideal for fast, accurate, secure and clean picking of smaller high-value goods in a greatly reduced space compared with conventional warehousing.
The rapidly expandable and adaptable system is ideal, for example, for consumer goods such as sports, fashion, gifts, electronics, beauty and household products, as well as global uses such as medical, surgical, pharmaceutical, high value e-groceries and the huge diversity of personal items in the rapidly expanding retail and ecommerce markets for which hygienic, safe and secure automated despatch is accelerating post-COVID.
“AutoStore systems are very clean and safe, eliminating multiple handling by storing internally up to 100,000 products or more that would otherwise be placed in cages on rows of racks,” says Mr Meier.
Mr Meier says Swisslog worked collaboratively with Linfox and its customers to create a solution that increased storage density to decrease the facility’s overall footprint. AutoStore was selected as it could effectively store and manage the customer’s increasing SKU range whilst increasing operational efficiencies.
Linfox’s installation is the first by the diverse logistics company, which employs more than 24,000 people across 10 countries and is one of the most compactly product-dense of any AutoStore installations.
AutoStore systems are one of a comprehensive portfolio of Swisslog automation systems for different industries and product types and sizes, including ASRS, automatic conveyor and transport systems, picking and palletising solutions, and flexible and intelligent software solutions.
“Swisslog’s easy-to-use SynQ warehouse management software – an essential component of the system – accurately tracks and traces all stock whilst orchestrating the flow of stock for despatch. The flexibility and grid expandability allow for future automation expansion as the customer’s business grows,” says Mr Meier. Stringleman said the Swisslog team developed a software package that would support the operational modes of Linfox’s customer to ensure a seamless transition of daily replenishment, storage, picking and despatch.
Ms Fraser says Linfox understands that, to meet changing customer needs, “We need to equip their businesses to be more agile, fast and flexible. This is why traditional supply chain models need to be enhanced through intelligent future-ready technology, like automation.”
“Linfox chose Swisslog as our automation partner for our consumer goods customer due to their extensive multinational experience with technologies such as AutoStore and because of:
Their proven experience in AutoStore technology with over 200 installed projects in over 20 countries worldwide
Their deep understanding of our customer’s needs, and
Their ability to deliver solutions that help us work smarter.
“These smart solutions start with high performing teams,” she says. “Together with Linfox’s in-house experts, we are proud to collaborate with customers and partners to develop next-generation automated warehouse solutions.”
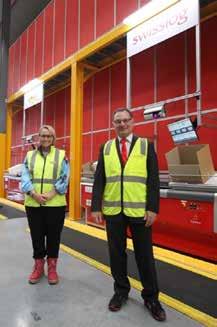
“This type of automation also gives our people the chance to gain new knowledge and skills in technology-enabled warehouses as we boost the efficiency and capability of our customers’ supply chains.”
Swisslog Australia 0416 865 553 www.swisslog.com/en-au