7 minute read
Create a Culture of Safety
Next Article
All employees should keep safety top of mind for the good of themselves, your customers and your company.
BY ERIC KNAAK
Ask yourself a simple question, “Do I promote a culture of safety here at work?” Do you educate your team about safety on a scheduled basis or only when something happens? Do you hold people accountable for their unsafe working practices or do you turn a blind eye to the little things? Do the members of your team understand the expectations placed on them when it comes to safety?
Take that pause now and honestly answer those questions for yourself.
If you feel good about where you and your team are when it comes to safety, good for you. It takes time, effort and commitment to create a culture of safety in any organization and those of us in the HVACR industry have the unique challenge of being at new locations every day, so that effort is multiplied.
When you work at the same location every day, it’s easier to identify and educate people about potential safety hazards, the necessary personal protective equipment (PPE) and best practices. When you travel to a new home, building or job site every day, you need to start at the beginning each time.
More importantly, you need to rely on your team members to identify potential hazards and to mitigate or work around those hazards in a safe manner and that’s where a culture of safety comes into play.
The goal is to create as safe of a working environment as possible for your employees so that everyone goes home to their families at the end of the day.
EMBEDDED IN CULTURE
A culture of safety is one where the thought of working safe, using proper safety practices, and not taking any chances is embedded in the DNA of an organization. From the newest employee to the most senior, there is an understanding and an expectation of what is safe, what is not and what to do when a potentially unsafe situation is identified.
In a culture of safety every member of the team has the ability to stop work and if needed, call for assistance when an unsafe situation exists without fear of reprimand or retaliation from supervisors, managers or owners. Not only does it negatively impact the trust of the team to retaliate against someone who halts work because of a safety issue, it is also a federal OSHA violation.
IMPLEMENTATION
What do you do if your organization is not where you would like it to be when it comes to safety and you would like to create an environment where your team feels compelled and empowered to work safely?
Every company is different and therefore approaches things differently. The goal is to create as safe of a working environment as possible for your employees so that everyone goes home to their families at the end of the day, and that may not mean doing things exactly as we are doing here at Isaac Heating & Air Conditioning
For Isaac it starts with a 100 percent commitment from the leadership team, that safety is the most important part of our workday and that we will not compromise on safety for any reason whatsoever.
Any member of our team has the ability and the empowerment to stop a project, no matter the size if there is an unsafe or potentially unsafe situation that they have identified.
Safety is one of our core values, along with Uncompromising integrity, Continuous improvement, Community, Family and Fun. Safety is also our number one ranked ordered priority, meaning that
Every field employee attends a monthly safety meeting where the safety director or the department manager will cover a specific topic that applies to that group.
this trumps everything and everyone else in the organization.
Our ranked ordered priorities are Safety > Employee > Client > Company … safety comes before everything else. It always has and it always will.
When a new member joins the Isaac team, they spend the first day in orientation and as part of that day they will spend about 2.5 hours with our safety director who goes over basic safety practices, expectations, and reporting procedures.
Each new employee is issued their basic PPE which includes two different types of gloves, safety glasses, hearing protection and, as of last March, a face mask. Depending on the group they will be working in, there may be some additional safety items issued as well.
Any other safety equipment that they may need on an occasional basis or that is job specific is also issued. This safety equipment is paid for, tracked, and maintained by the company.
Every field employee attends a monthly safety meeting where the safety director or the department manager will cover a specific topic that applies to that group. These meetings range from 30-60 minutes in length and include handouts, PowerPoint presentations, interactive learning and occasional guest speakers.
The topics covered include vehicle safety, lockout-tagout, MDS, fall protection, electrical safety, ladders, lifts & booms, haz-com, PPE, proper lifting techniques, respirators, hand tools, power tools, safety reporting and many others. The purpose of these scheduled monthly meetings is to be sure that every member of the team is aware of potential safety hazards and held accountable for their actions.
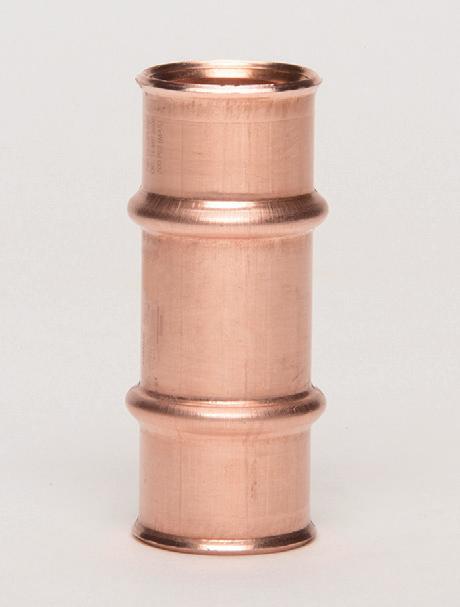
On commercial job sites we also have a 5-minute toolbox talk each morning before we begin, and we do the same on our loading dock for the residential installers. The intent is to make safety the first thing on everyone’s mind each day.
TAKE ACTION
When an incident does occur, either the safety director or the group manager will respond immediately, fill out an incident report, take photographs if necessary and report the situation to HR.
The safety director, along with the VP of HR will investigate the incident and have a meeting with the team member affected and their manager within 24 hours if possible. The purpose of this investigation is to determine the cause and to decide if we need additional training for that employee and possibly others to prevent it from happening again.
The critical safety numbers are tracked and reported monthly to the leadership team and are reviewed semi-annually with our insurance group. You must know your numbers; you need to know where you are today so that you can determine where you want to be in the future.
SAFE REPORTING
One final and very important consideration is that safety and safety tracking programs should not be punitive. An effective safety program and reporting structure should help employees to feel comfortable by coming forward as opposed to the fear of being disciplined.
When team members know that they can come forward you will begin to learn about near misses (accidents that did not but could have happened) which gives you the opportunity to prevent them from ever occurring. Establish the expectations, educate, and train your team to understand safety inside and out and promote a safe working environment for everyone.
When done properly, your employees will be safer, your workers comp rates will drop, your safety MOD rate will drop (we are currently at .76) and the entire team will begin to live by a culture of safety. u
Eric Knaak is vice president of operations for Isaac Heating & Air Conditioning in Rochester, N.Y. and past-chairman of the Air Conditioning Contractors of America (ACCA). For additional information, visit isaacheating.com.
The proven solution for faster, easier, safer HVAC/R connections.
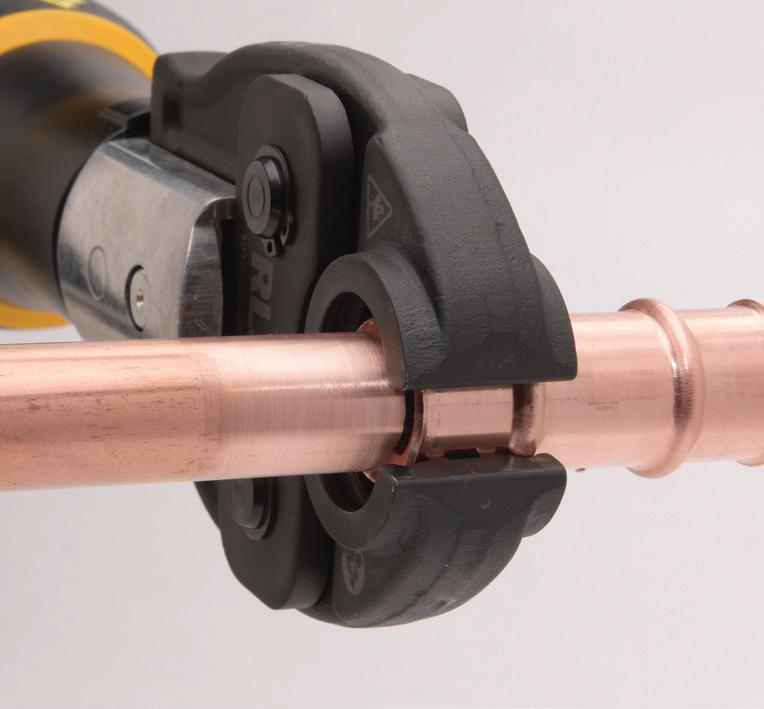
L o o k f o r t h e fl a r e !
T h a t ’ s h o w y o u k n o w i t ’ s f o r H VAC / R .
If your technicians are still brazing ever y HVAC/R joint, you’re missing out on huge time and cost savings. RLS press fittings connect in just 10 seconds, so your crews get in and out of jobs faster and get more jobs done. These are the same exact fittings that were formerly sold as ZoomLock®® – so they will always work with the original ZoomLock jaws.
RLS ADVANTAGES:
• Connects in 10 seconds • No gas or brazing materials • No flame, no fire hazards • No hot work permits • No fire spotters • No nitrogen purging • Works in tight spaces • UL listed 700 psi • Millions installed since 2015 • Made in America
Ask about our limited-time rebates: $500 on tools/jaws and up to $1,000 on fittings! Scan code for details.
A M E R I C A N M A D E
rapidlockingsystem.com training.rapidlockingsystem.com
ZoomLock® is a registered trademark of Parker Intangibles LLC, which is a subsidiar y of Parker-Hannifin Corporation.
A Whole New:
Machine Warranty Ballgame
Introducing the new Ameristar. Designed and engineered by American Standard Heating and Air Conditioning®—with the ease of use, support, and distributor network you’d expect from an industry leader. When it comes to affordable equipment, it’s setting a whole new standard.
Learn more at ameristarhvac.com/contractors