52 minute read
My Take _________________________________________________6 NewsLines _______________________________________________8 Safety: Are We Learning?
Next Article
Logging Safety: Are We Learning?
NIELSde Hoop
Logging is known as one of the most dangerous industries and occupations. Most years, loggers and fishermen vie for the top spot in fatal accident rates (think of rates as being percentages of workers).
Generally, fishermen fall overboard and loggers get crushed by trees.
When I worked in Canada in the late 1970s, I remember reading that the forest products industry (including mills) ranked in the top three industries for accidents, along with construction and mining.
In the 1980s, there were about 200 fatal logging accidents nationwide per year. Louisiana alone had four to eight per year. These numbers declined over the years.
Since 2007, the nationwide number ranged 63-105 per year, and the Louisiana number was usually zero or one.
Even the 1990s safety numbers were improvements when viewed over the decades. For example, in the 1930s, Oregon alone suffered 300-400 fatalities annually.
Non-fatal accident rates also have made progress, dropping roughly sixfold since the late 1980s in both the U.S. and Louisiana. In fact, the logging accident rates in Louisiana have dropped so low that the federal Bureau of Labor Statistics (BLS) has not reported a number since 2013. That doesn’t mean “no accidents.” It means that the numbers are so low that the statisticians worry about keeping the data anonymous.
This is the reason that the Louisiana Logging Council maintains its own database of logging accidents in the state. This is the only effective source we have. So, when the Logging Council’s Gracee Texada contacts you each January for the previous year’s accident reports, please help out by sending in your responses.
How does Louisiana stack up against other states? Our numbers are roughly equal to that of Alabama and Arkansas. Our accident rates are half the national average. By contrast, Oregon’s accident rates are double the national average. The difference, of course, is terrain — the mountainous terrain of Oregon demands a lot of cable logging accompanied by manual felling. To what can we attribute the improvement in logging accidents in Louisiana? The most obvious answer is—chain saws, or rather the trend toward a lack of chain saws in the logging woods. Mechanized felling has largely replaced manual felling. Operators sit safely inside enclosed cabs that are built to rollover and designed to falling object protection standards (ROPS and FOPS). Essentially, the only time operators get hurt is when they are outside the cab—such as when doing maintenance.
Mounting and dismounting used to be the major problem, with operators jumping off machines. Education can take the credit here. Talking and writing about 3-point mounting and dismounting has been effective. OSHA inspectors watched for it, getting the attention of truck drivers, and the drivers helped spread the word to other logging sites.
Where do the problems remain?
Maintenance and repairs remain an issue, but most of today’s accidents in Louisiana center around the trucking part of the logging industry.
Even the trucking accidents have changed. In the 1980s and 1990s, most truck driver injuries occurred while the driver was outside the cab—throwing binder chains, walking on rough terrain and slipping while mounting or dismounting. Replacing chains with cables or straps has helped a lot. Today, most truck driver injuries occur on the roads.
Vehicle accidents remain a nagging problem. In fact, according to the BLS, one-third of all occupational accidents are actually transportation accidents. This holds true for logging, the mills and all industries combined. This says something about the importance of defensive driving education and other programs designed to reduce road accidents.
Also, the numbers I discussed do not include members of the public injured or killed in vehicle accidents with trucks. Those numbers are typically one to three per year in Louisiana. Most are not the fault of the truck driver, but dead is still dead, and it takes more than just a safe driver to prevent accidents.
Because we have to share the road with the public, we need to interact more with the public to prevent accidents. This means funding for better roads and educating the public to respect trucks.
One of the most interesting ways of analyzing our progress is to look at which occupations now have the highest accident rates. I found the list of Highest Incident Rates of Total Nonfatal Occupational Injury Cases, 2020. Of the 25 top industries on this list, logging was not on it! In fact, No. 1 on that list was Skiing Facilities, followed by Nursing & Residential Care.
While there are always unsafe conditions and unsafe acts to improve, it is nice to reflect on the progress the logging industry has made. Our accident rates have fallen to just above the industry-wide average of all industries (2.3 v 2.6) in recent years, and we still have the institutional memory to apply our lessons learned to the remaining problems and even to other industries.
So, take heart that logging has become much safer, but be cautious of ski slope work. TH
C.F. “Niels” de Hoop is an associate professor at the Louisiana Forest Products Development Center, School of Renewable Natural Resources, Louisiana Cooperative Extension Service, LSU AgCenter
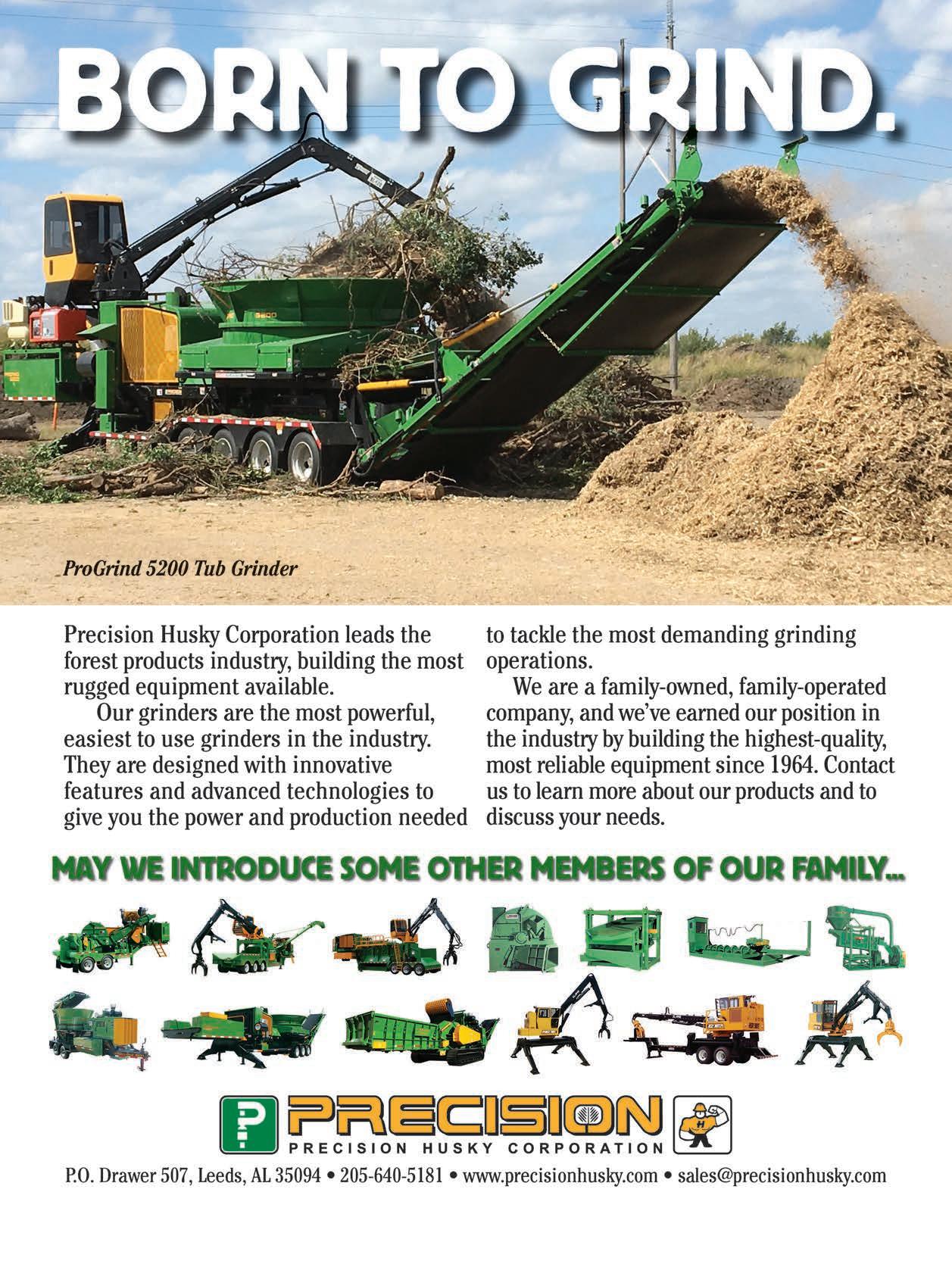
Guts & Glory & Grit
The third winner from South Carolina, Robert Lussier, Jr.’s Great Woods Companies, is the 2022 Timber Harvesting Logging Business of the Year.
JESSICAJohnson
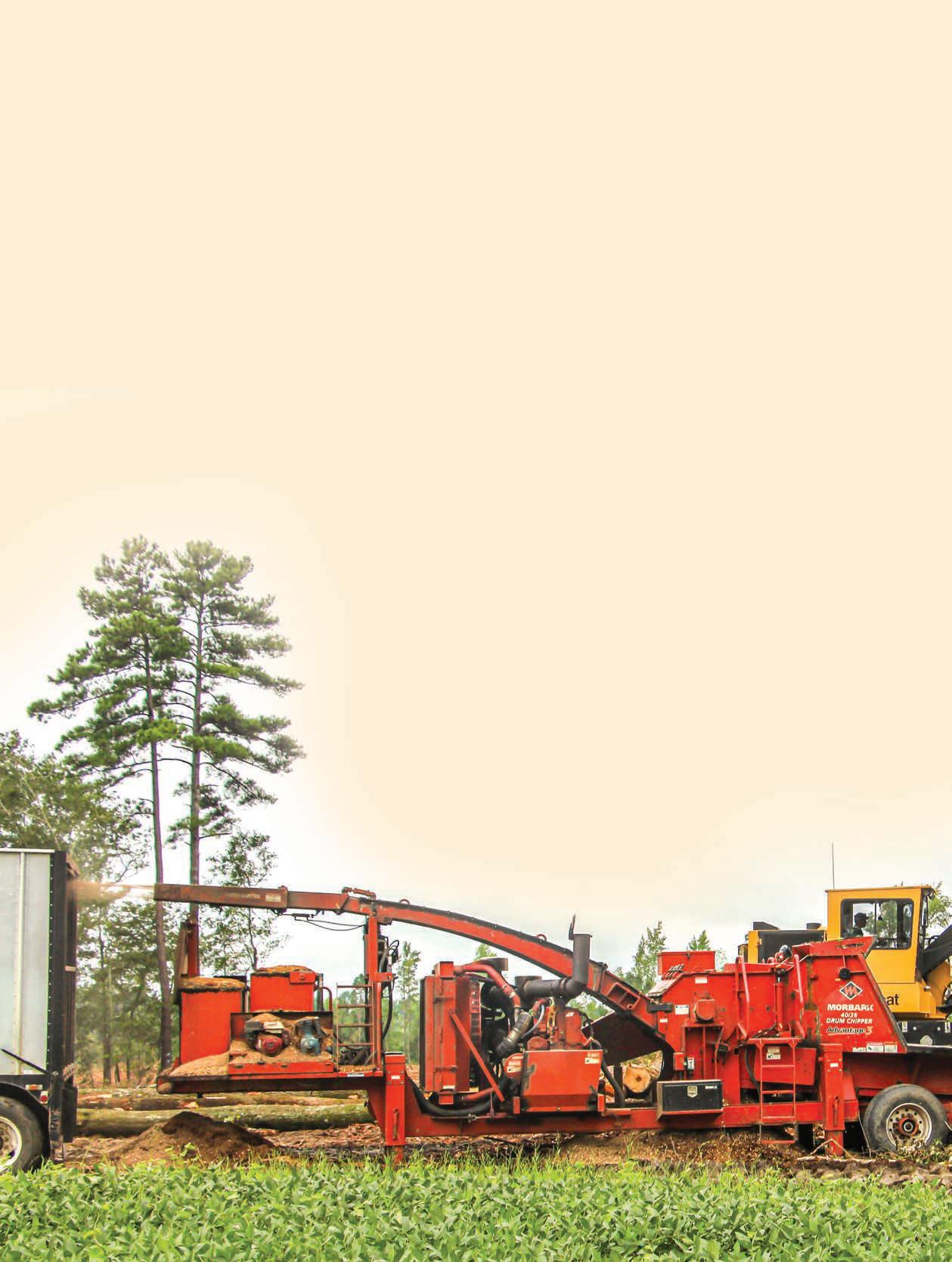
BENNETTSVILLE, SC
Grit is defined as a person with courage and resolve, having a strength of character that others might not. It’s that trait a person has to keep pushing, take chances and not stay silent. It’s something Robert (Bob) Lussier, Jr. has by the bucketload. How else can you explain someone who steps out on faith to move their business 900 miles? Puts themselves out front on industry hot topics, serving organizations looking to influence policies to make things better for himself and other loggers? Someone who’s not afraid to say the culture of the forest products industry needs to change, and in a big way, before it becomes filled with insurmountable problems? Someone who takes a near fatal accident, and invites anyone and everyone into that day via video and countless words to hope that it will reach even one other logger and possibly save someone else the pain his family went through after he almost lost his arm? That’s all grit.
That grit, those reasons, are why Lussier’s company, Great Woods Companies, has been named the 2022 Timber Harvesting Logging Business of the Year. Lussier is the third winner from his adopted home state of South Carolina, and the 25th winner overall.
Lussier says that often when he talks with other loggers he feels like he’s preaching to the choir. But every choir needs a preacher, and for South Carolina, you’d be hard pressed to find a better one. His personal story is not unlike others, having been raised in a rural community in the Northeast, starting his company, procuring timber for his crew, running a machine himself every day, and getting the wood marketed. Fast forward 20 years, and things started slowly turning downward. Having been the first person to run a rubber-tire Tigercat feller-buncher in southern New England, Lussier had relationships with folks in the Carolinas and Virginia. His Tigercat dealer was Tidewater.
That’s when the opportunity to work for a timber buyer in South Carolina presented itself to Lussier. They came down in June and talked about it. After they returned he talked to his workers about the proposition. Then, after some deliberation and number crunching, Lussier and his business drove 900 miles south. Now he says, he wishes he had done it earlier. The move south was the best thing he could have done for the business, he believes, and the success he’s had since in a new area is, again, a testament to his grit. But success over the last 39 years doesn’t
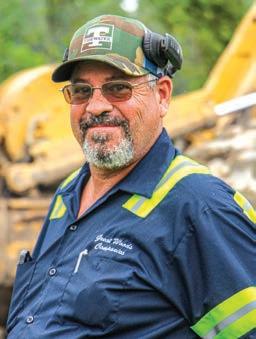
Robert (Bob) Lussier, Jr.
Guts & Glory & Grit
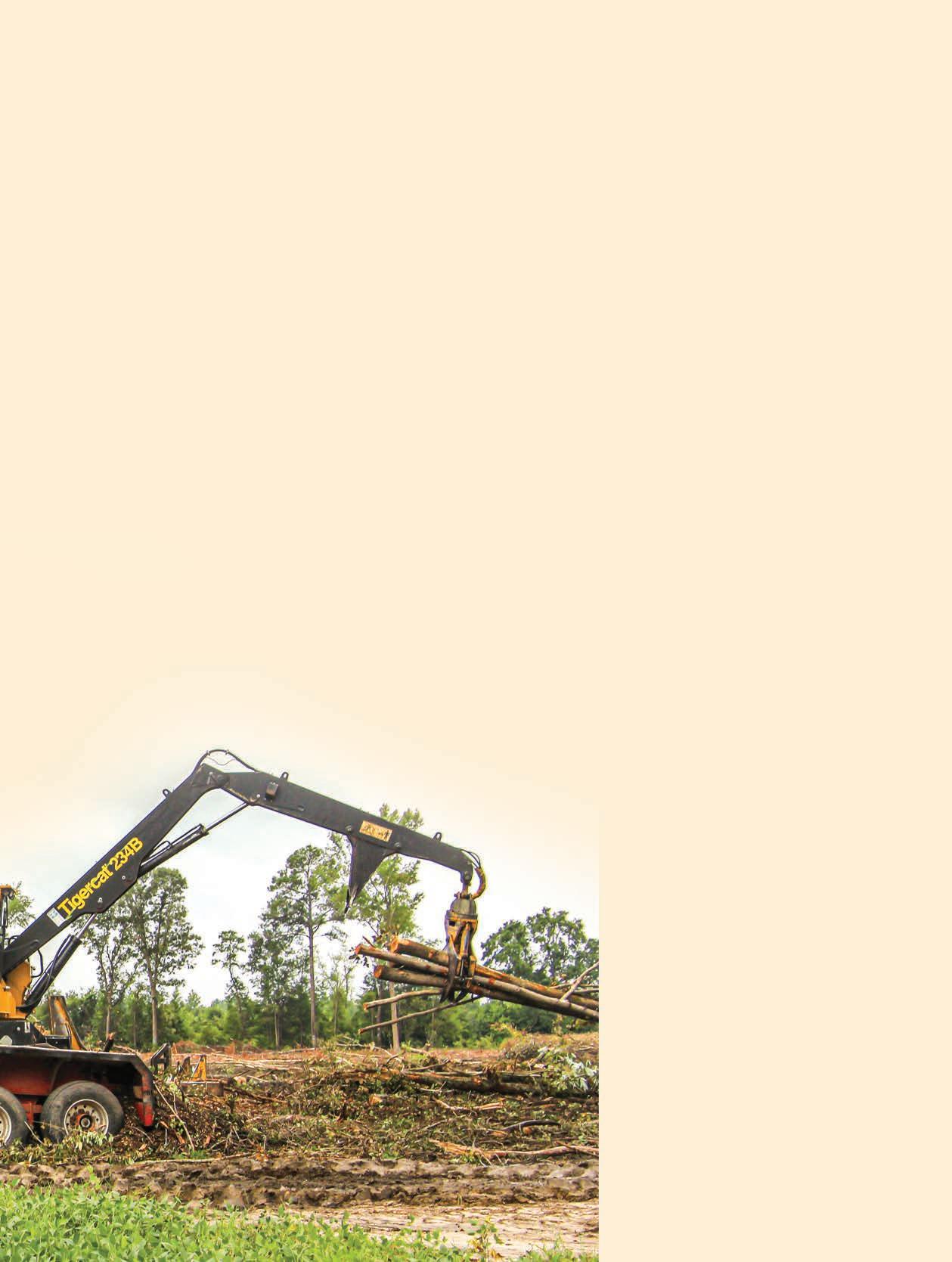
mean success has been easy or is guaranteed for the next 39—though Lussier is quick to say he doesn’t want to work that long! Lussier believes there are a lot of changes coming to the industry in the next 12-18 months, and his personal plan for the future is to bring on an operations manager.
Lussier says this hire means he can force himself to slow down. It makes sense, given his place in life, grandkids and his desire to desire to turkey hunt, now that his Grand Slam has been done, to complete the NWTF 49 state challenge.
“I have to learn how to slow down. Hiring an operations manager is going to take a year. How do we find somebody outside of our industry and give them the knowledge? There’s no training class they can take, basic business management, sure, but there’s so much that’s so different. It’s going to take a unique individual,” he says.
And he’s right, while operator schools are cropping up around the country, there’s no Logging Business 101 to teach someone how to do the books, plan tracts and all the things logging owners handle. For most loggers, those financial and operational skills are learned by doing, and for Lussier, he wants to ensure his company and crew are in a positive position. So bringing on just anyone isn’t going to cut it.
While the plan might be a forced slowdown with the end of the tunnel being retirement, Lussier, 57, isn’t gone just yet and he’s got plenty still on his proverbial plate—and mind.
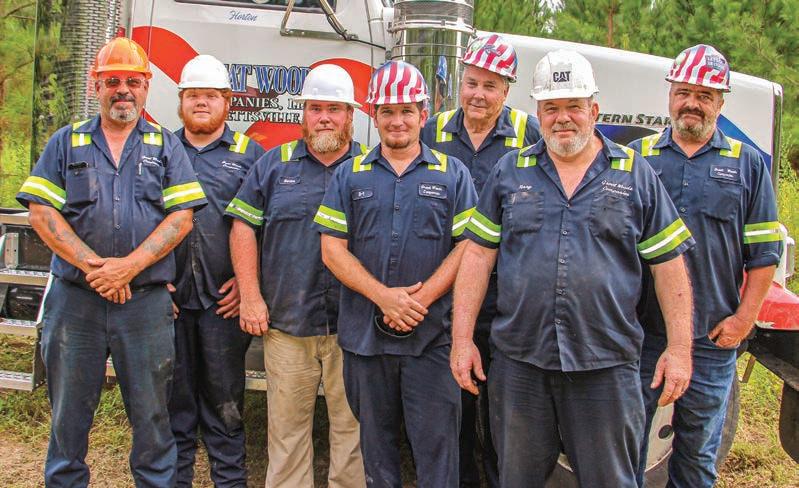
The Great Woods Companies employees, from left, Bob Lussier, Garrison Horton, Bryan Horton, Brian Shoemaker, Russ Cracraft, Terry Hannan and Schuyler Whitney
Business Awareness
A Board Member for the South Carolina Timber Producers, active in the Forestry Assn. of South Carolina and the current President of Team Safe Trucking, Lussier has a very full plate indeed. “People need to get involved, that’s been the problem. Us Baby Boomers, we became loggers because we didn’t like other people,” he says.
“Most of us are not people persons. We want to be in the woods where nobody bothers us,” Lussier says. “We’ve been our own worst enemies, because we’ve done a disservice to the younger generation because we didn’t speak up. Our timber industry in the South has a 60-year-old system and it’s broken.”
Now, Lussier has the chance to help fix the system of working 12+ hour days, seven days a week, for pennies on the dollar just to ride the rollercoaster of his mills’ needs. He got a hard lesson on how the system worked when he moved from New England to South Carolina, and he’s been fighting against the system ever since. At first it was against the timber dealers that controlled the wood baskets, but now, Lussier’s got his eye on what the mills are, and most importantly aren’t, doing for their suppliers.
“The only way I make money is if I take control of the system. I don’t like the system but if I take control of the system, I can make the system work for me. It used to be you had to watch your quarters and dollars. Now, you have to watch your pennies and nickels,” he adds. Lussier’s wife, Cindy, handles all office work for the company and is trained to run some equipment and drive set-out trucks. She’s in every sense of the word Lussier’s right hand (wo)man.
In order to help watch the pennies and the nickels, every weekend the pair sit down and she brings a box with the bills and reports out, going through everything so Lussier knows what has been taken out and what has gone in that week. Cindy explains this helps him know where he is finan-
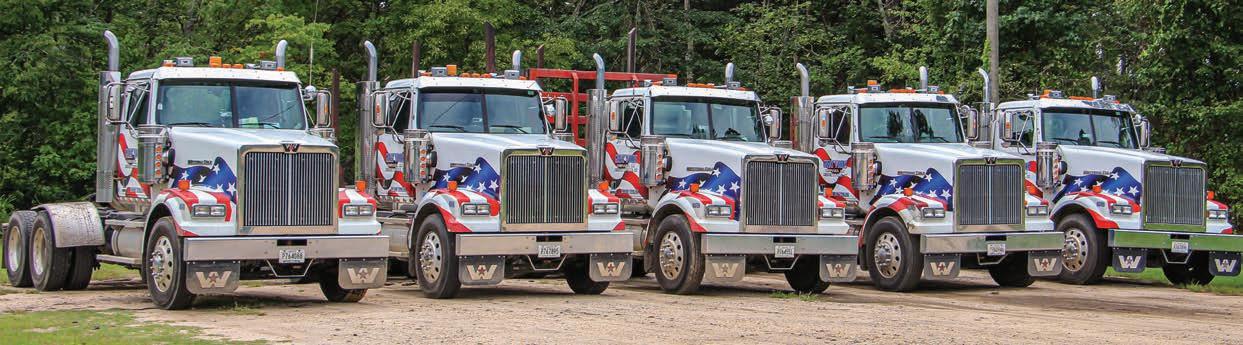
Company owned, filled with American pride, trucks handle between 75 and 80 weekly loads.
Great Woods Co. main market is chips, and after Lussier suffered a near-fatal accident during a knife change, he made the incident a “teachable” moment to warn other loggers.
cially, and exactly what everything is costing him.
Lussier admits that the pair started the practice, but for a while he quit because it was just easier to let Cindy handle it. But then he realized he had no idea why more money than he thought was being spent from the account. After reviewing cost increases he found where the money was going, and the ritual resumed.
“I don’t go to the office much,” he says like the true logger he is. “She prints my reports, I look at them. We keep track of a lot of little things. How much we pay for everything—from tires to shop rags. And we pay essential bills every week. Help is paid every week.”
This level of cost control allowed Lussier to know that his single crew with just three machines, moving between 75 and 80 loads per week, couldn’t keep up with the volume he was able to purchase and consistently haul to his main chip market. So, Great Woods was able to add Goodnow Timber as a contract chipping crew a few years ago—to great success. In doing so, Lussier was able to help another New England family, Chris and Jennifer Goodnow, drive south and restart their business 900 miles away.
Lussier says both his contract crew and his own are great assets. The current 75-80 loads range could be higher, but like every logging operation Great Woods struggles finding truck drivers. “It’s very discouraging right now because you can’t find truck drivers. You can be the best logger in the world, but until that load gets to the mill and you get the ticket, you aren’t getting paid,” he emphasizes. Always willing to try something different, Lussier has even taken out billboards and radio commercials in surrounding areas soliciting drivers and offering sign-on bonuses for those who are able to begin hauling for him. With inflation, he adds it has made the trucking component of his business even more of a challenge. Not only does he have two new trucks sitting without drivers, he’s also struggling to match up what he’s been offered for fuel surcharge pricing with what he is actually paying at the pump.
With three in the woods full-time, and four drivers cross-trained enough to load themselves if needed, Lussier is satisfied. The crew has been together for a long while, and Lussier’s two pile system—everything with leaves goes in one and everything with needles goes in the other—keeps things simple and quick. Lussier, who runs the loader, takes out logs, and chips mostly everything else for his main market, Enviva.
While the crew is mostly older, one new member represents the younger generation. “It is hard to find guys to work in the woods. But the crew I have is amazing. Without them I am not who I am. I am just the director, and the guy who signs the checks,” Lussier says emphatically.
He works hard to create a culture within Great Woods that isn’t just a family—it is a family with pride. Making sure employees know they are a part of something, they are involved in decisions and they are able to make decisions for themselves. Gone are the days where you could tell an operator or driver to do the job the way you want or they can forget about it.

Pursuing Quality
And the Great Woods crew really stepped up when in July 2021, Lussier suffered what could have been a fatal injury. During a routine chipper knife change, he was cut in multiple places, and in some instances down to the
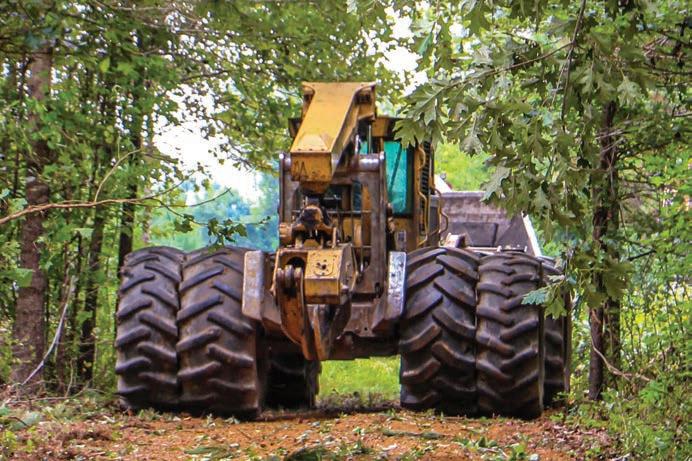
Three employees get it done in the woods for the 2022 Logging Business of the Year.
bone. He was helicoptered to a hospital where ultimately, he retained his arm. But the sound of steel-on-steel triggers Lussier. Being around chipper knives is emotionally taxing for him. “I still have post-traumatic stress disorder,” Lussier says. “I sold that chipper two months ago. The person that bought it came to our parts shop and I had to give him all the knives, for me to still go around chipper knives...” he adds, trailing off for a moment. “I can do it, and I try not to show a weakness, but inside I am still really nervous around them.”
Lussier says that looking back, he’s frustrated with himself. He’s the one who does all of the company’s safety meetings. He’s been around this equipment for 30 years. “I should have paid better attention to what I was doing,” he says. But always in a hurry, isn’t that almost like a logger’s motto? He was off the plan he had initially set. And that’s when it all happened, in a blink of an eye.
“The biggest thing I learned was don’t be in a hurry,” he adds. “Think about what you’re working with and how dangerous it is. We don’t have a lot of accidents in the woods anymore but when something happens its more catastrophic.” Lussier is very fortunate to live to tell the tale, and serve as a living reminder that safety always has to be everyone’s top priority no matter how veteran the operator.
The chipper knife accident is not why he got involved with Team Safe Trucking, but the irony is not lost that his tenure as president began just after the accident. “I got involved in Team Safe because of an industry that’s been good to me. It’s just like my involvement with the forestry association and being on the board with the timber producers: I want to give back to an industry that has been good to me and try to make a difference for the younger generations that are coming,” he says.
His involvement and activism has garnered him acknowledgement and awards, but he hasn’t let that affect him and he’s remained independent. Just like he knows his fellow loggers are.
For Lussier, one of the goals with his various involvements is help other loggers be aware of how critical the work of the associations are and how much they need to get involved. “Loggers need to learn the difference between ‘no’ and ‘know.’ A lot of loggers can’t say no because they don’t know. Sometimes working harder does not mean making more money,” he emphasizes.
Recently, he and Cindy completed a cost of business study, taking each of them about 40 hours to complete their portions, and through that study, they learned that the only way you can combat inflation is to work closer to the mill, and to produce more tons with less equipment. Now he knows when he can say no.
“Our analysis was very different from what we’ve seen in the industry, our analysis was essentially cost per hour,” he explains. Frustratingly, he had markets that weren’t interested in even meeting with him to look at the numbers he had, to discuss why he needed the rates he had asked for.
The lack of willingness to even look at the analysis is why Lussier is worried about the sustainability of the industry. Sure, we all use forest products every day. At a regular rate there is new mill announcement after new mill announcement. But Lussier wonders if the mill doesn’t care how sustainable loggers are and timber dealers are and truckers are, will there not be an ability to remain sustainable as an industry?
“I have invested heavily in land as part of our retirement portfolio,” he adds. “We have all these mills around, but if Bob decides to retire and then we don’t have any of the logging crews that are capable of keeping our management goals met, what happens to the retirement?”
An answer, in his mind, is thinking outside of the box: viewing markets and suppliers as a partnership. While Lussier admits there aren’t many guys out there like him left, there are some young loggers, and keeping the industry that has given him so much going is what he’s dedicating some of his time to. It’s a worthy cause, because what happens if there’s none left? TH
Trucks & Trailers: ● 6 Western Star 4900 SF Gliders (2019 and 2020 models) ● 17 Trailers: 8 logs/poles, 6 chips, 2 lowboys, 1 flatbed ● 2 Ford F-350 service trucks: Each fully equipped with tools and parts, air compressors and 100 gal. fuel tanks ● Shop trailer: Equipped with tools, parts, fluids (hydraulic oil, DEF, etc), hydraulic hose machine,1000 gal. fuel tank
Equipment: Feller-Bunchers: ● 2017 Tigercat 720G ● 2018 Tigercat 720G ● 2021 Caterpillar 538LL Grapple Skidders: ● 2017 Tigercat 620E ● 2016 John Deere 648L ● 2019 John Deere 748L II Log Loaders: ● 2015 Caterpillar 559C ● 2018 Tigercat 234B Chipper: ● 2017 Morbark 40/36 Miscellaneous: ● 2012 John Deere 670 Grader ● 2020 John Deere 700K Bulldozer ● 2012 Caterpillar 299DXHP Forestry Mulcher ● 2018 Caterpillar 320 Excavator
Great Woods Companies preferred vendors include Flint Equipment, Aynor, SC; Blanchard Machinery, Florence, SC; Tidewater Equipment, Polkton, NC; Schwab Brothers Hydraluics, Perry, Fla.; and Swamp Fox Agency, Moncks Corner, SC.
Building Future Timber Supply
Top reforestation contractor Adam Mizell: replanting key to substainability.
CALLAHAN, Fla.
Every day, Adam Mizell and his crew at Mizell Development, Inc., plant the seeds for tomorrow’s timber harvest. After earning a forestry degree from Lake City Community College and building a business specializing in logging roads, Mizell found himself doing more and more site prep contracts. He discovered that he was drawn to the reforestation side of the timber industry. After a little over 10 years in the reforestation business, Mizell was named the Florida Forestry Assn. Silviculture Contractor of the Year for 2016.
“I’m a farmer at heart,” says Mizell, who represents the fifth generation of a poultry producing family. “I have no doubt if I lived somewhere else, I’d be growing corn or soybeans.”
In The Field
On a fall day on a cut-over softwood site outside of Callahan, Fla., one of Mizell’s Tigercat 630E skidders was pulling a 20,000 lb. Marden Industries drum chopper, preparing the ground for a stand of slash pine. Mizell’s skills in site preparation will put that land on the fast track to its next timber harvest, helping make the tract more sustainable than ever. In 15-20 years, the trees on this parcel will be ready for the pulp mill; in about 30 years, the landowner will have a nice stand of sawlogs.
Site prep and replanting can account for as much as 20% of a timber harvest budget, so reforesting a site is a major investment for landowners—but
STEVEWerblow
Replanting uses similar equipment as logging but specific with applications related to ground preparation.
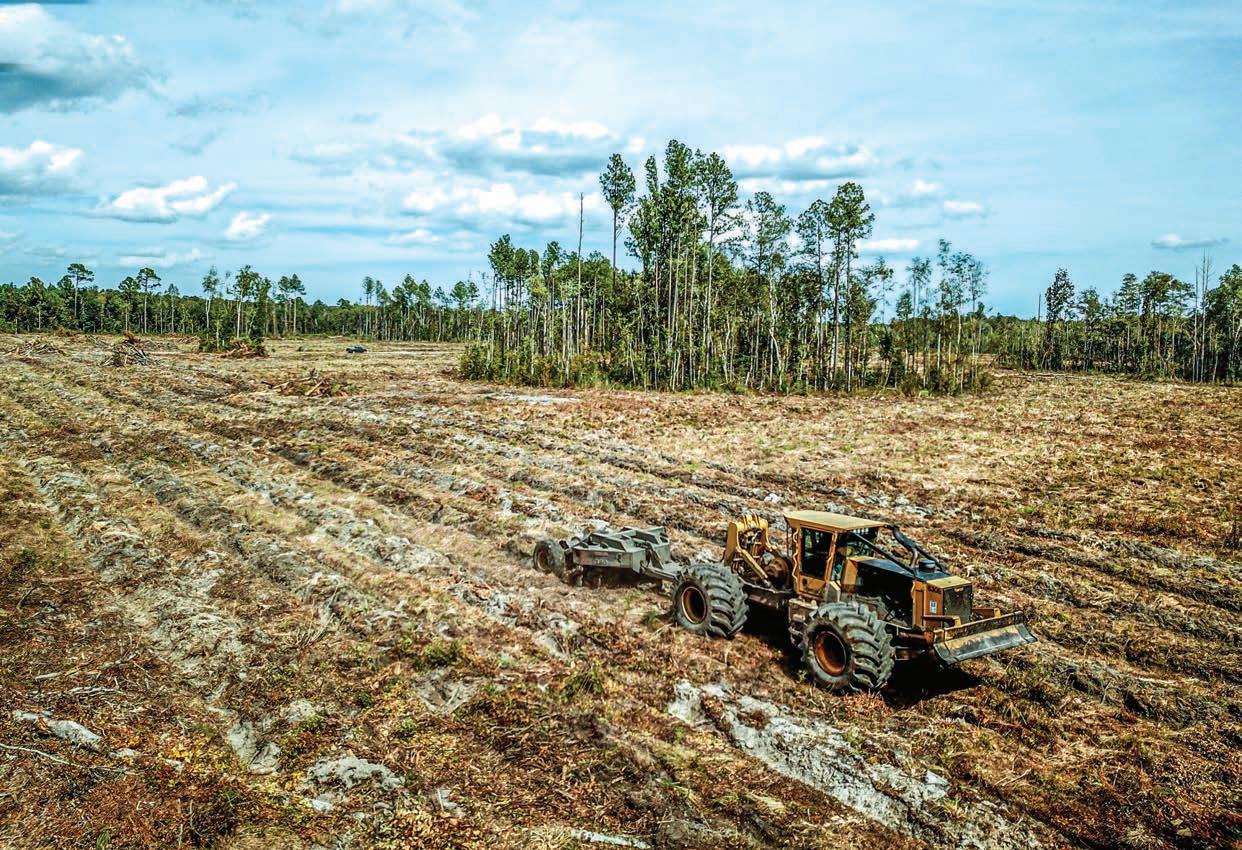

Studies show lands that are mechanically prepared and replanted are more productive.
it pays off. A University of Georgia study documented the benefits of replanting: Slash and loblolly pine planted into prepared land had almost twice the growth rate—5.85 tons per acre per year vs. 3.0—and greater economic returns than naturally regenerated stands of the same species.
Operations
The reforestation process starts with a herbicide application soon after logging has ended. Mizell likes to let a clear-cut sit for about a year before site prep, giving some of the debris a chance to start breaking down, but he says he and his team are often chopping within a few months. Large stumps with a lot of heartwood can be sold to an explosives manufacturer, but the stumps are generally chopped to fertilize the next generation of trees.
“Chopping softens the soil so that the new roots can grow vigorously throughout the bed,” Mizell says. “You want a chopper with good, long blades so it will get down there and break up the lateral roots on the residual stumps and split the residual stumps as much as possible so it encourages the breakdown of all those things. The pine needles, the palmettos, the gallberries, all that gets broken down and folded into the bed and serves as nutrient and organic matter to help the new seedlings get ahead.”
Mizell follows chopping with a Fleco root rake, originally designed for wheel loaders and modified by Stokes Welding to fit Deere or Tigercat feller-bunchers. On the Callahan project last fall, a Tigercat 720G piled debris too big for the drum chopper to break up.
“Feller-bunchers make a fantastic raking tractor,” he explains. “We’ve used wheel loaders and dozers in the past, but the undercarriage cost is prohibitive. You have to guard them up with forestry packages, and sticks still get in there and break things. A feller buncher is made from the ground up to be protected from debris and logs and sticks stabbing up through the machine. They were engineered for this application, and you can get bigger tires on them.”
Mizell uses a variety of equipment, including both Tigercat and John Deere machines, and works with dealers Tidewater Equipment Co. in Brunswick, Ga., and Ring Power Corp. in Jacksonville, Fla.
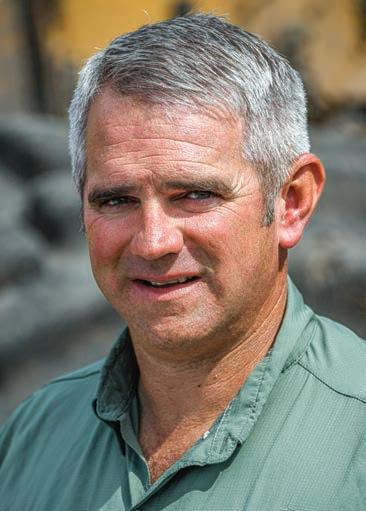
Adam Mizell: “I’m a farmer at heart.”
Final Phase
The final step in land prep is pulling beds, which Mizell forms with Savannah Global Solutions bedding plows pulled by Deere or Tigercat skidders in the 250-300 HP range. “They have the strength to pull through without having to gear down,” he notes.
About half of the sites Mizell prepares for planting are on beds 12 ft. apart on center. The rest range from 11
to 16 ft. on center, depending on soils and the foresters’ plans for stand density. Drier sites can be bedded in a single pass. On wetter ground, Mizell prefers to build the beds higher— about two feet from the bottom of the furrow to the top of the bed—with a second pass.
“It’s so flat here we get ponded water,” Mizell says. “None of it is very deep, but it will stagnate the tree’s growth if it’s just sitting in sour water.” Mizell’s work in the 150-mile radius around Callahan falls mostly in the heavy soils of the Okefenokee Swamp region.
In January or February, crews come through to plant seedlings. Mizell says 95% of the trees planted on the land he prepares are slash or loblolly pine, and the other 5% are longleaf pine. With a skilled crew and bareroot or containerized seedlings, Mizell says stand survival can be 98% or better.
Gearing Up
Mizell attributes successful site prep to simple factors. “Having good quality equipment with good tires and a good man running it—that’s the key,” he says. “What makes a good contractor is someone who does what he says he’s going to and follows through with it, who has good equipment and good people on his team to make good on that.”
Mizell points out that horsepower is critically important, but so is making sure that all the horsepower reaches the ground.
“Tires are extremely important to my business,” he notes. “Our tires aren’t as susceptible to torque or puncture as a logging tractor because we’re not carrying the weight of the trees. All we
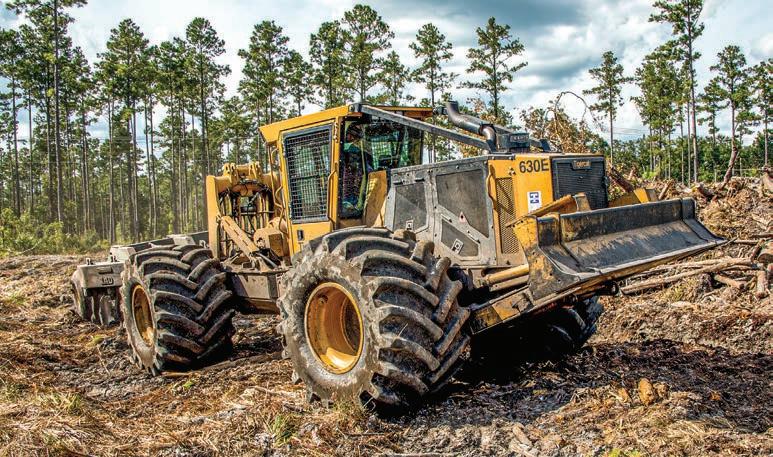
For Mizell, transferring horsepower to the ground is critical to job success.
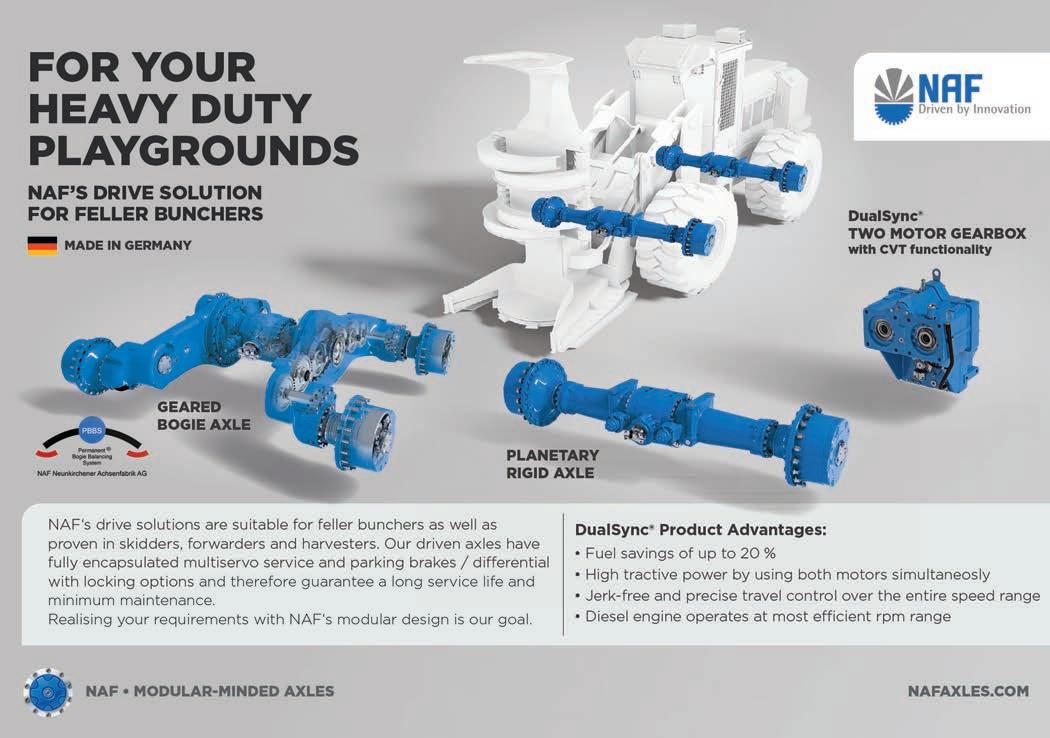
have is the weight of the tractor and the tread of the tire—so if I don’t have good tires, I’m just spinning in place.
“Most particularly, when you’re pulling beds and your tire spins, the tractor sinks down some,” Mizell continues. “That makes the disk sink down some, and it becomes a tougher pull on your tractor,” he explains. “So now the tractor’s dug itself into a hole it’s trying to climb out of, and that takes more fuel and horsepower—and if you don’t move on, you’re stuck.”
Deep Treads
Years of trial and error, and the evolution of logging tire design, led Mizell to Primex Log Stomper Xtreme tires. The 82/32" depth and wide construction of the tires’ curved lugs had instant appeal, and the durable compound reaffirmed his choice.
“They’ve got a thick, deep bar, which makes a lot of difference,” he says. “I try to stay on the new side— the first 50%—of a tire. I can have 3,000 hours on the Primex Xtreme and it will still have a bigger bar than other tires. In my business, if your tires start to get bald or worn down, they’re fine when you’re on dry ground, but we’ve got to work the whole field: the good, the bad or whatever. You’ve got to have what it takes to get through those wet areas. We don’t want to leave those acres out, because they’ll grow a tree.”
Most of Mizell’s tires are standard 30.5 and 35.5 widths, but in some wetter ground, he has experimented with 73x44.00-32 Log Stomper Xtremes. He says the extra wide tires have provided both better traction—helping his operators work swampy areas that would otherwise have to be bypassed—and better flotation, which minimizes soil compaction to maintain a healthier root zone for seedlings.
“A 300 horsepower skidder, whether it’s a John Deere or a Tigercat, is a heavy tractor,” he points out. “I needed more flotation and hoped to achieve a little more traction, and I think I got both things.”
Thin Margins
Mizell points out that, like every aspect of the logging business, reforestation is tougher than ever. “It’s all about efficiency nowadays,” he says. “You can be inefficient. But you just won’t be inefficient for very long.”
The name of the game is working more acres at thinner margins, and keeping crews active all the time. “I look at labor as a fixed cost,” Mizell says. “If you’re going to have good people, you have to pay them consistently. If you send them home, you can’t blame them for looking for something else. You’ve got to keep them working. And if they’re out working, they have to be able to do the job. If they’re stuck, just sitting there spinning in place, they might have to get on the lowboy and leave and then come back later. We don’t get paid to move back and forth—that’s counterproductive.”
In the end, Mizell sees the results of his investments and his people in the tall stands of pines stretching through north Florida and south Georgia—tomorrow’s timber growing straight, tall and fast. “I still have to be competitive,” he says, “but I always think first, ‘this is what we need to do the job right.’” TH
This article submitted by Yokohama Off-Highway Tires America, Inc.
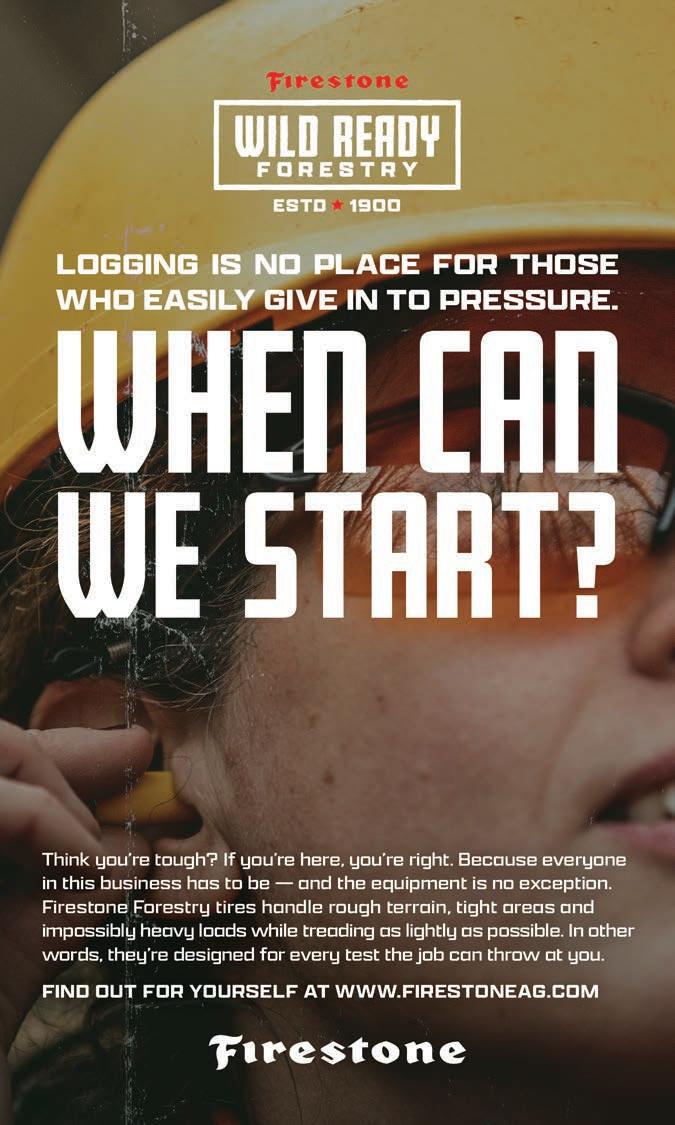
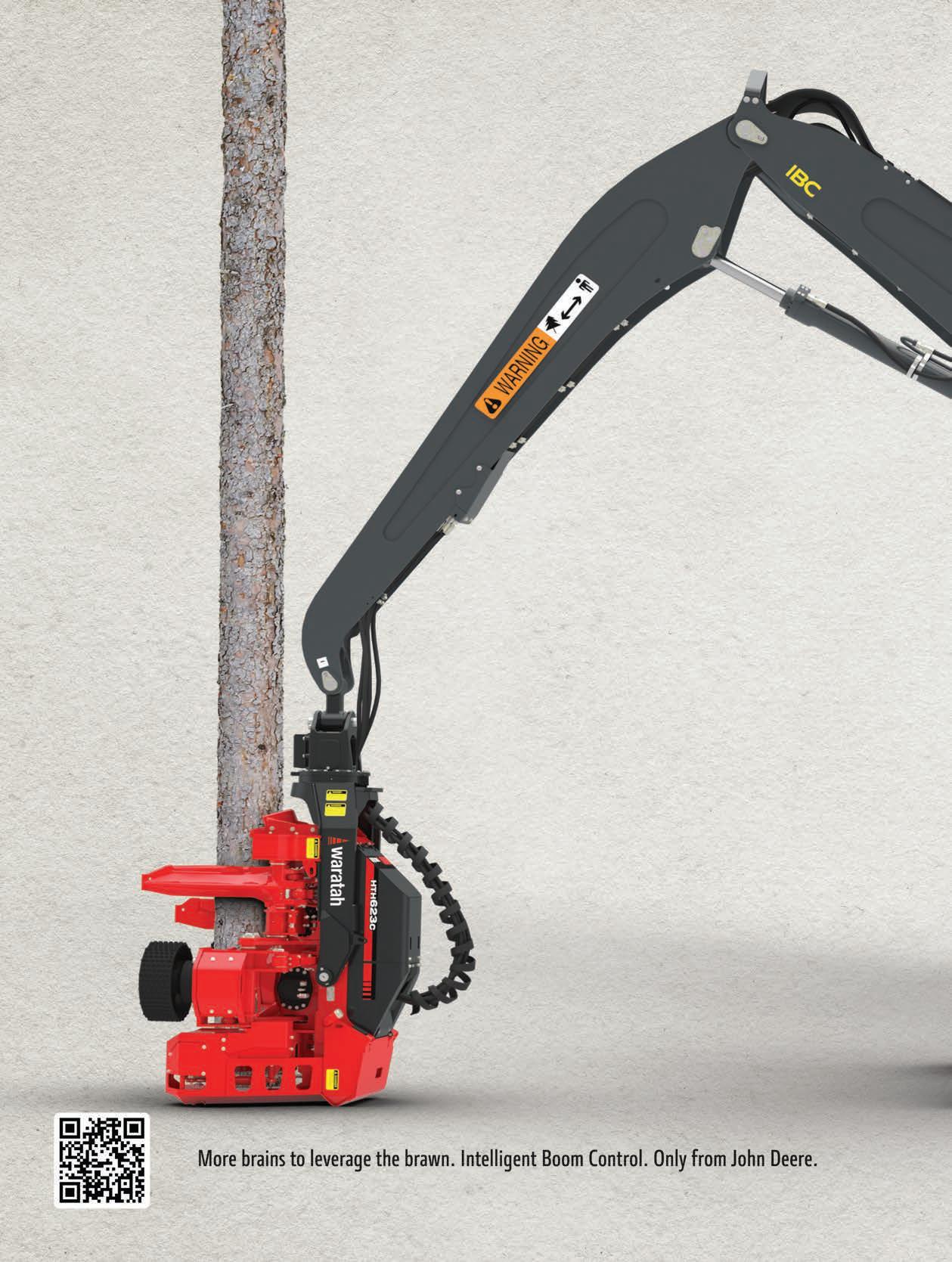
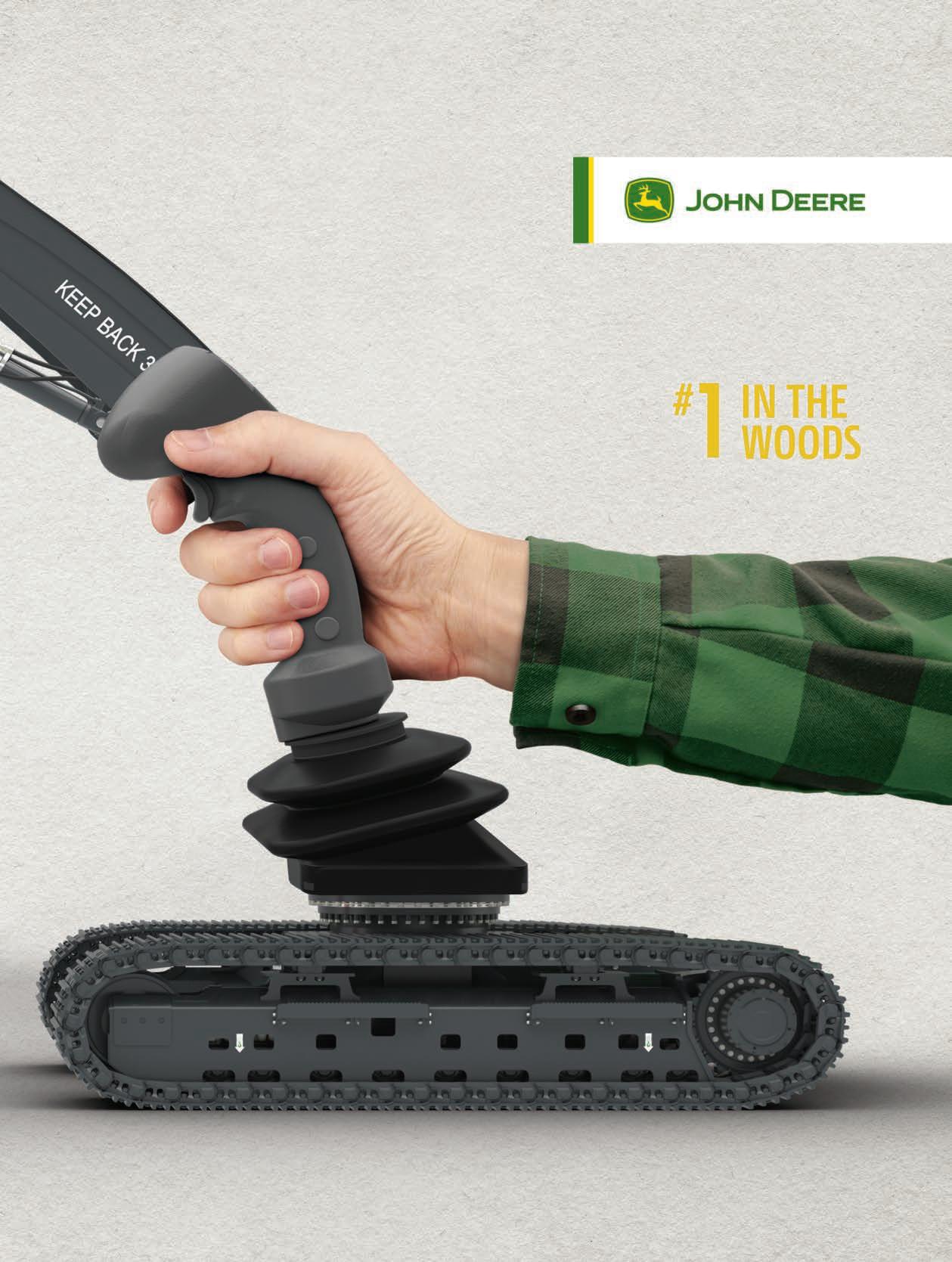
BKT: Top Tire Performance
Logging conditions can be extreme, and it is essential to use the best equipment and components that operate easily and safely. Tires play an essential role in such a difficult environment that requires safe and designed products with specific characteristics, such as load capacity, strength, resistance and stability.
BKT, which has studied the real working conditions, offers specific forestry products that allow operators to deal with the most diverse felling and skidding applications, even under the toughest conditions. BKT proposes two resistant products, characterized by a long product life that means a lower number of replacements and less downtime, with environmental and economic benefits. FS 216, perfect for loggers and skidders. It’s durable, has a great excellent cut and chip resistance and ensures maximum protection against possible damages. It has a robust log design with optimum angle and wider width to enhance traction performance. Other relevant product’s features are high puncture resistance, excellent traction, self-cleaning and high-load capacity. FS 216 is available in seven different sizes, both in steel-belted or standard versions. The F 240 is designed for log skidders. Great traction, self-cleaning capacity, maneuverability and good steering are the main features of this excellent product. Thanks to the width of the tire print, the stability on the ground is better. Finally, the superior tread compound guarantees extraordinary cut-and-wear resistance resulting in a longer service life. It is available in two sizes.
With these efficient products which stand out for their specific features, BKT wants to contribute and provide a valid response to the demands of such a complex and demanding market to help daily working challenges and to respect the environment. Visit bkt-tires.com

Deere Bogie Skidder Tackles It All
John Deere’s six-wheel 768L-II Bogie Skidder is a true woodland warrior designed to conquer wet conditions and steep slope terrain. Incorporating the proven, durable features found on the John Deere L-II Skidder lineup, the 768L-II maximizes productivity, performance, and comfort when carrying hefty loads over long distances in challenging conditions. The 281 HP 768L-II features heavy-duty bogie axles, which incorporate large components to maximize durability and stability for long axle and tire life. The heavy-duty axles are purpose-built for tough applications, effortlessly pulling heavy loads and maneuvering tough terrain. The smooth, stable operation results in reduced machine vibration, ultimately minimizing operator fatigue. Another key feature is the excellent tractive ability and floatation. When combined with the bogie axles, ground pressure is reduced, allowing the 768L-II to work in wet terrain not accessible with a four-wheel skidder. As a result, the harvesting window is extended, adding more working days to the calendar.
The new arch design provides the operator with an expansive rearward view of the grapple and work area, providing excellent visibility. Improving maneuverability, the long wheelbase and boom-arch envelope boost reach and lift capability for the boom and grapple, increasing dexterity in the woods. The tight turning radius enhances agility at the landing.
The 768L-II retains the other customer-favorite features introduced on the L-II product lineup. Streamlined and redesigned electrical and hydraulic systems result in improved uptime and increase guarding and protection of key components. An increased grapple squeeze force and two-speed winch further increase productivity, while articulation steering sensors improve the operator experience.
Highly regarded by customers, all L-Series II models feature a spacious cab, including ample storage space, configurable controls, and an effective HVAC system. Armrest-mounted electrohydraulic controls offer accessible, hand-finger operation of all machine functions, and joystick steering provides smooth control of steer, direction, and ground speed. The industry-exclusive Continuously Variable Transmission (CVT) marries the efficiency of a direct-drive transmission with the smoothness of a hydrostatic drive. As a result, CVT provides more power to the ground by sensing the load, increasing torque and tractive effort as needed to maintain the desired speed. Visit deere.com
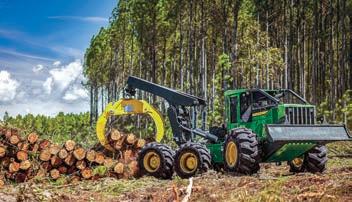
Forest Chain Protection
Forest Chain’s wide range of ring skidder chains, are available in fixed ring, multi ring, and studded with 9/16", 5/8" or 3/4" tag chains to fit all popular tire sizes. Designed to give as much as 60% more traction to your skidder, Forest Chain Skidder Chains provide quicker skid times, more production and increased bottom line profits. Forest Chain premium Multi-Ring heavy duty chains offer superior traction putting steel in strategic points providing protection from rocks, stumps and site debris, protecting your expensive rubber tires.and are available in 9/16, 5/8, 3/4, 7/8 and 1". The Double Diamond configured chains equipped with U-shaped studs are especially effective in the worst conditions like mud and snow, the deep biting lugs dig deeply into the terrain to keep production moving. All Forest Chains are manufactured with top quality materials and workmanship and designed to provide puncture protection from rocks, stumps and debris. Repairs are easy using common welding techniques and materials for longer life. Call 800-288-0887; email forestchain@gmail.com
NAF Axles Deliver Top Performance
NAF AG has been manufacturing axles and gearboxes for over 60 years! As one of the world’s leading drive train producers for self-propelled forestry machines, we bring our proven modular minded approach of rigid and bogie axles to the forests’ functional, economical, and logistical challenges.Cut-to-length, whole tree harvesting, mulching, transporting, loading, and planning all have unique opportunities. NAF is proven in the forest and ready for your next challenge.
NAF has created a durable lineup of our bogie axles with 12 different models varying in size/payload and wheelbase. Our bogies are all gear driven, can be equipped with our patented Permanent Balancing Bogie System (PBBS), oil immersed capsuled brakes and have multiple differential lock options.Optimized ground clearance allows our bogie axles to walk the timber with six or eight wheeled machines.The Skidder Bogie can be a portal type, or fix planetary allowing for up to 36 tons of timber payload.These bogie options will allow for your machine to gain the speed and tractive effort needed to move the wood you need!
NAF AG has spent the last seven years supporting the North American market with its most recent location NAF North America, in Morris, Ill. Opening in 2015 as part the NAF AG Company, this wholly owned subsidiary has taken North America’s forests to the next step in the NAF family.Sales, support, parts, and just in time axle delivery are all available from this location.
NAF additionally is helping North American forestry customers with a complete durable range of rigid axles for Skidder and Wheel Feller Buncher harvesting, right of way mulching, and whole tree skidding.NAF can help loggers quickly roll in and harvest trees with ease, using heavy-duty axles and gearboxes designed for each sustainable tree harvesting method.
NAF AG and NAF North America are here for forestry, construction, agricultural and material handling needs of the world.To meet your next challenge, we will listen first to understand your situations, converse with our staff to define the modular approach, develop and support you with our engineering team’s technological solution to fit your needs. Our modular minded approach will balance proven methods and new technology against your technical requirements and economical needs. Prototyping all the way through serial production, our team will help produce a solution that everyone on the team supports and understands. Visit nafaxles.com

Olofsfors Boosts Skidder Productivity
Olofsfors is a Swedish based company founded in 1762 with North American operations in Brantford, Ontario, Canada. Olofsfors is the market leader in bogie tracks for CTL machinery and wheel tracks for skidders and wheeled feller bunchers. Specific to skidders, Olofsfors offers ECO-Wheel Tracks to boost productivity and increase traction. ECO- Wheel Tracks are traction aids developed and designed to suit the most demanding terrain and machine sizes. ECO-Wheel Tracks provide numerous benefits over conventional chains including increased traction, less spin and grab, easier and less maintenance, and can fit on used tires. ECO-Wheel Tracks are available for tire sizes 23.1 x 26 to 35.5 x 32 and come standard with the 1" link system. ECO-Wheel Tracks are only available in one model which is based around the bestselling ECO- Track model. For the CTL machines, Olofsfors offers a wide range of bogie track models and linkage systems for various machine configurations and ground conditions. Most track models are now available in the next generation of curved cross members for increased flotation, less ground disturbance and easier machine turning.
The track assortment ranges from traction only, flotation only and all around. Along with five different link systems, Olofsfors has the most track options available on the market today.
The All Around tracks are ECO-Track and KovaX. Both of these models provide good traction along with good flotation. The Traction tracks include EX, OF and EVO with EX providing the most traction. The Flotation tracks consist of Baltic, U and CoverX.
New for 2022 is the continued development of the larger track cross members. Along with ECO HD, the next model is Kovax+. Kovax+ is thicker and stronger compared to standard Kovax and is a great option for the newer 29mm link system.
Visit olofsfors.com

Ponsse Head Offers Felling Speed, Accuracy
The completely upgraded Ponsse H8 harvester head features a powerful feed, firm grip and solid yet agile frame. Active Speed is available for the harvester head as a new feature, giving it a superior performance.With Active Speed, the harvester head’s operating speed can be adjusted based on the tree species and stem diameter. Equipped with this new function, working with the H8 harvester head is smooth and productive, no matter what the tree diameter is.
“We have developed our product range of harvester heads actively with our customers. Many of our customers work in challenging conditions, which is why their development ideas give us the best possible feedback for product development.
With its completely new structure, the new H8 harvester head is ideal for processing large trees,” says Janne Loponen, product manager for harvester heads.
The new harvester head can be mounted on Ponsse Ergo, Scorpion Giant and Bear, the strongest harvesters in our product range. The saw box area is even wider, making the harvester head an excellent choice for trees with a high butt diameter. The harvester head’s structure has been designed for easy maintenance, and the frame has been built to be even more durable. A powerful feed, combined with a geometry that firmly supports larger stems on feed rollers, guarantees high productivity and fuel economy. The automatic features of the Opti control system, developed and built by Ponsse, control the feed speed and saw movement, according to the tree diameter, and ensure fast and precise sawing.
All Ponsse harvester heads have been designed to withstand the toughest conditions. They are characterised by a simple and solid structure, which is why they can be used in various harvesting applications. All Ponsse harvester heads are manufactured and designed at the Ponsse factory in Vieremä, Finland. Comprehensive design applies to both mechanical components and the electronic control system, controls and software. The manufacturing process is highly automated, guaranteeing a high level of quality and measuring accuracy. Visit ponsse.com
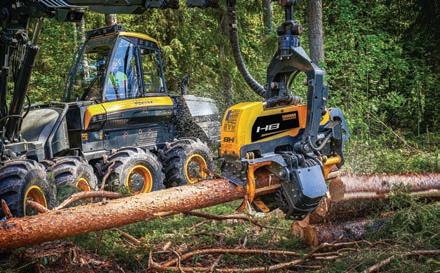
Cutting Downtime With Schwab Brothers Hydraulics
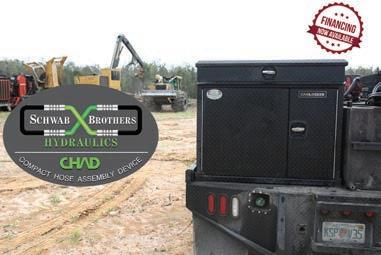
The wear and tear on your cutters and skidders day-in and day-out is relentless. We’ve all been in the dreaded situation where we’ve had to stop production due to a hydraulic hose failure on a skidder or buncher. That is now a thing of the past with our in-woods hydraulic hose crimping unit! Our Compact Hose Assembly Devices are an asset to any logging operation no matter where you are or how many crews you have! These mobile hydraulic crimping units allow you to build your hydraulic hoses on the job site eliminating unnecessary trips to town. These downtime eliminators were designed to keeps loggers logging! Call today to learn more about our Compact Hose Assembly Devices, we look forward to serving you! Call 850-838-6487; visit schwabbrothershydraulics.com
Tigercat FBs For All Felling Applications
Tigercat builds drive-to-tree feller bunchers for the full range of thinning and final felling duties. The 720G and 724G are designed for thinning and clear fell applications and the large capacity 726G fells large diameter timber in tough terrain.
The G-series machines cabs are designed for productivity and operator comfort. Visibility is enhanced with a larger front window and larger rear quarter windows. The view over the back tires is the best in the industry—an asset in thinning applications.
Only Tigercat offers WideRange, the infinitely variable transmission for drive-to-tree feller bunchers. WideRange allows the operator to travel more quickly than conventional two-speed transmission equipped feller bunchers. Quicker travel boosts productivity and reduces cost per ton in high production thinning and final fell applications. Tigercat’s unique WideRange drive system is standard on all G-series feller bunchers. A two-speed transmission is optional on the 720G and 724G.
Tigercat has recently added the 822E to its track buncher line-up. Based on the popular 822D, the 822E is designed for challenging thinning and final felling applications.
The powerful lift capacity, tight-tuck ER boom geometry, and compact tail-swing make the 822E the perfect choice for selective felling where minimum site impact is important.
A redesigned engine enclosure provides improved roof access for cleaning debris. A boom slider also reduces debris build-up in hard to reach areas. The clamshell style enclosure and drop-down side platform allow easy access to all sides of the engine. The updated cab on the 822E includes a durable, roomy, air ride seat with heating and cooling. The fulllength front window and narrow side posts give the operator an excellent view of the tracks and surrounding area. Visit
tigercat.com

Wallingfords, Pewag Combine For Quality
Since 1975, recognizing industry needs has been a core strength of Wallingford’s Inc. Wallingford’s Inc. announced its acquisition by pewag group this past April, and has positioned itself as an industry leader for the sales of forestry tracks for both the cut-to-length and full-tree length harvesting markets. pewag bogie tracks for cut-to length machines offer case hardened C-links to extend longevity, and is an innovation that only pewag offers. pewag tracks come in multiple styles for different applications, and we aim to maintain good inventory and assembly capabilities in the USA to reduce lead times for our customers. pewag also offers single wheel tracks for skidders, and we are working to increase the diversity of tire sizes offered with 28L26 being a welcomed addition to our offering for 30.5 and 35.5 tire sizes. In addition to pewag tracks, we will also be offering pewag skidder chains with a new double diamond design for this coming season. This will complement our offering of both studded diamond and ring chains from BABAC. Please contact us for any track or skidder chain needs, we specialize in the design and fabrication of difficult to find tire sizes. Call 800-323-3708; visit wallingfords.com
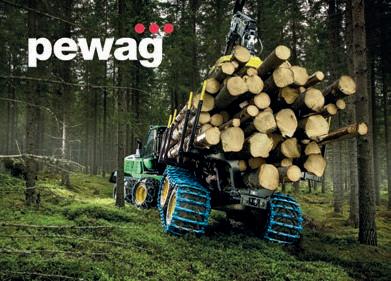
Yokohama Expands Primex Log Stomper Line
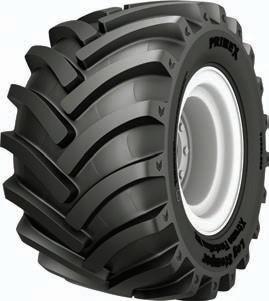
Yokohama Off-Highway Tires has expanded its rugged Primex Log Stomper Xtreme skidder tire to include an extra-wide 78x45.00-32 size for added flotation and a greater ability to handle the high torque of today’s powerful skidders. Loggers in deep mud and standing water were immediately interested in the added flotation and traction from the 45-inch-wide version of the popular Log Stomper Xtreme, said Terry Goodwin, National Product Manager—Forestry for Yokohama Off-Highway Tires America, Inc. He added that the 78" diameter and 26 ply rating of the tire efficiently turns the machine’s torque into pulling power without excessive strain on the beads, lugs and sidewalls. “The feedback we’ve been getting has been nothing but positive on the new 78x45.00-32 Xtreme,” he said. “The tires show almost no signs of stress where you would expect to see strain from continuous high torque and heavy pulls. Loggers are working harder than ever with bigger machines than ever, and our job is to make sure to keep them going.”
Goodwin pointed out that the extra-wide Xtreme is also gaining a growing following in less-saturated soils because it creates significantly less soil compaction. Compacted soil does not have as much space between soil particles for air and water that sustain roots, and is often too dense to allow good root growth. Goodwin predicts that landowners and regulators will push for less compaction in the years to come.
The 78x45.00-32 features the unique, variable angle Log Stomper Xtreme lug design, with its distinctive wide nose and tapered design that offers greater durability and a stable ride. The tire’s heavy, reinforced sidewall and chunking resistant forestry compound deliver exceptional tire life in the toughest conditions. The Xtreme also features a reinforced dual bead to deliver more torque and greater durability. And the tubeless design of the 78x45.00-32 Log Stomper Xtreme reduce hassles during mounting or repair.
The Primex Log Stomper Xtreme is also available in DH73x50.00-32, 73x44.00-32, 67x34.00-26, 66x43.0026, 67x34.00-25 and 66x43.00-25 sizes. Call 800-777-
9926; visit yokohama-oht.com.
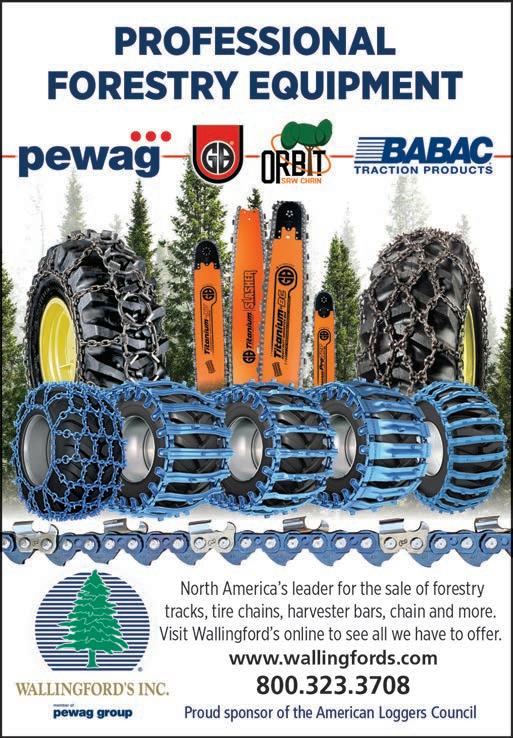
Ponsse Announces Electric Forwarder
Promising to “walk the talk” of its commitment to environmental sustainability, Finnish forestry equipment manufacturer Ponsse hosted an online event on August 17 announcing the introduction of a new forestry machine concept, the electric Ponsse EV1. Ponsse has been developing the concept for the last three years with Epec, a Finnish technology company, owned by the Ponsse Group, that specializes in advanced electronics. Juho Nummela, Ponsse’s President and CEO, and Jyri Kylä-Kaila, Epec’s Managing Director, took the opportunity to discuss the emerging technologies. A recording of the online event is available to watch on Ponsse’s YouTube channel.
“Technological development is fast and offers us excellent opportunities to develop our solutions further, even in unexpected directions,” Nummela says. “We have worked hard with our technology company Epec to enable this concept. At the same time, both companies have developed their capabilities, and we have gained significant new knowledge during this project. This launch of a new technology concept is a peek into the future and one of the solutions offered by electric powertrains. Sustainable development is a significant future success factor for Ponsse. We want to strongly develop our solutions with Epec. Our strategy reform has been successful at Epec, and we’re very happy with Epec’s excellent development.”
Aiming to lead the way in developing machine technologies for sustainable forestry, Ponsse seeks carbon neutrality in its operations and solutions. This launch of a new technology concept is part of the company’s strategy and represents a tangible step toward the goal of carbon neutrality.
Ponsse has been studying and developing such new technological solutions for several years.The EV1 concept took its first steps in 2019 when Ponsse and Epec started to investigate responsible power source solutions in line with sustainable development.
While Epec’s technology can already be used in electric or hybrid-electric commercial vehicles and non-road mobile machines, the EV1 forest machine is still in testing and a few years away from serial production for commercial availability. The prototype machine will be presented at FinnMETKO 2022, a heavy machinery expo held in Finland in early September.
The EV1 concept has been developed for forwarders with a 15-tonne (16.5-ton) load-carrying capacity, the most popular Ponsse forwarder size category. The machine features a fully electric powertrain, as well as Epec’s power distribution unit and hybrid control unit. The machine’s powertrain operates fully with battery energy. Batteries are charged using a Range Extender, which is a combustion engine at this stage of development. This technology provides significant improvements in fuel economy in this size category.
According to representatives of Epec’s engineering team during the online event, the machine is designed to charge while it works, running half the time on the battery alone and half the time with the onboard diesel engine serving as a generator to charge

It charges while it works, and what logger doesn’t dream of bypassing the fuel pump these days?
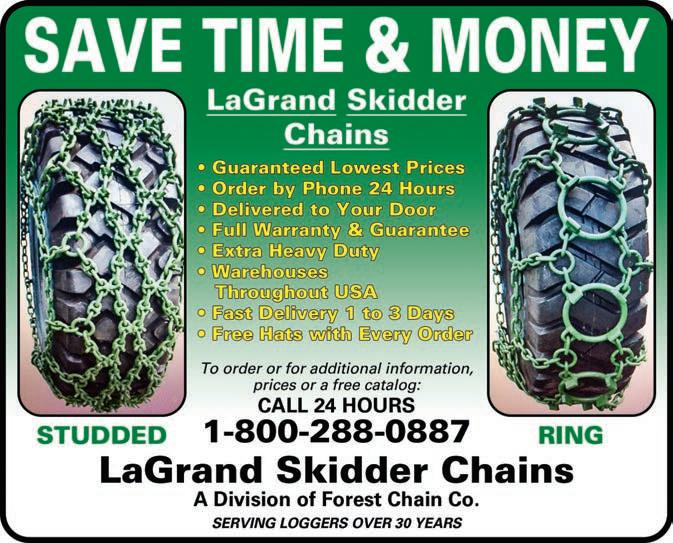
the battery while in operation (it does not require external charging). It reportedly affords equivalent power but with greater fuel efficiency compared with conventional, fully diesel models. The concept features a 700v DC power system, potentially enabling compatibility with other (non-diesel) power sources in the future, such as hydrogen or biogas.
The EV1 features Epec Flow, Epec’s electromobility system solution. The solution is based on the Epec Flow Power Distribution Unit (PDU), to which electric motors, batteries and various devices can be connected. The PDU’s integrated safety solutions enable effective manufacturing and maintenance of the machines, as well as their operations in demanding conditions.
Ponsse seeks to provide sustainable harvesting solutions by listening closely to customer needs, and as such invited several customers from Uruguay, Sweden and Finland to witness the EV1 in action firsthand. They seemed both surprised and impressed by how advanced and work-ready the concept is. As one customer, Paulo Mancinelli of Suzano, put it, “I think the future is coming shorter and faster than we thought it would be.”
Visitponsse.com or epec.fi/ ponsse-ev1/ for more information.
Deere Debuts Tracked F-B Boom Control
Deere officials hosted a live event in mid summer at Brandt Tractor’s Kamloops, BC branch that debuted the company’s Intelligent Boom Control (IBC) technology in its 800/900 MH-Series Harvesters. Customers, trade press and others on site were able to watch and even operate the equipment in Brandt’s yard, while an international Zoom audience watched. Afterward, a panel of experts answered questions.
Deere’s IBC technology was introduced on forwarders in 2014 as an operator assistance feature. Adapting it to other models is the result of collaboration between the company’s CTL team in Finland and conventional forestry group in Iowa, said Deere’s Jim O’Halloran, Product Marketing Manager, Tracked Feller Bunchers and Harvesters, DSFH. The IBC brings “intuitive control” to both boom and swing functions that creates straight line boom motion with adaptive swing functionality and also develops uniform and consistent boom velocity.
The IBC has proved so popular it’s rapidly becoming a standard feature on Deere boom-equipped machines, O’Halloran added.
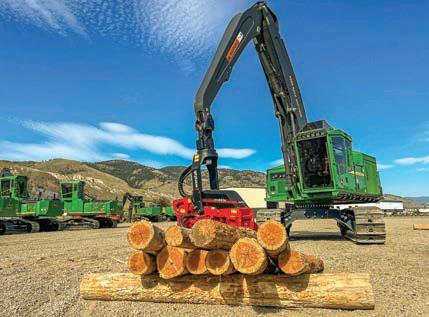

Schwab To Distribute Proteng Fire Suppression
Schwab Brothers Hydraulics has entered into a partnership with Proteng, a maker of automatic fire detection/suppression systems, to serve as a distributor for Proteng’s THIA system. Schwab Brothers will bring the product to market in the forest products industry, buying the units at wholesale and selling to the end users, as it does when manufacturing its CHAD mobile hose crimping device.
Several THIA systems are already in use on logging machines operated by M.A. Rigoni, the affiliated logging company owned by the Schwab family.
Fire prevention is always critical, but never more so than right now. Ryan Wood, director of sales and business development for Schwab Brothers Hydraulics, points out that if you have a catastrophic fire and lose a machine, you may not be able to replace it right away, given ongoing supply chain bottlenecks.This was the driving factor for the Schwab group to get involved with Proteng, he adds: they are constantly seeking solutions to alleviate downtime on todays logging operations.
THIA is an acronym used to describe the Proteng system; it stands for Tube + Heat = Instant Action. The system consists of a polyamide tube that is filled with FM-200 fire retardant and sealed using hydraulically crimped brass ends. FM-200, or hepafluoropropane, is a state-of-the-art substance that eliminates many of the drawbacks of other retardants. Unlike dry chemical or foam retardants, it leaves no residue, is nontoxic, and is safe to use on equipment without causing any collateral damage.
Automatic extinguishers that use aqueous film forming foam (AFFF) can be effective, but most are limited to engine compartments and can cause extensive damage. Proteng fire suppression devices are self-contained (require no power source), fully automatic, non-toxic, and non-corrosive. THIA is heat-activated and can even stop a fire before it starts if the temperature gets hot enough.
For more information, contact Ryan Wood at Ryan@schwabhydraulics. com or call 850-843-8615 (office) or 850-838-6487 (cell).
MacDonald Takes Over As President Of Tigercat
Grant Somerville has stepped away from his role as president of Tigercat Industries. The timingis related to Somerville’s original intention to serve as president for a five-year term when he took on the role in 2017. Tigercat founder, Ken MacDonald, has assumed the role of president.
“I wish to thank Grant for all of the contributions that he has made to our company during his entire 30 years with us,” MacDonald says. “I want to particularly recognize the leadership he provided during his presidency.
Somerville will continue to serve the company as a director. In his new role, he will offer advice, and support various engineering initiatives focused on the development of new products and the improvement of existing products.
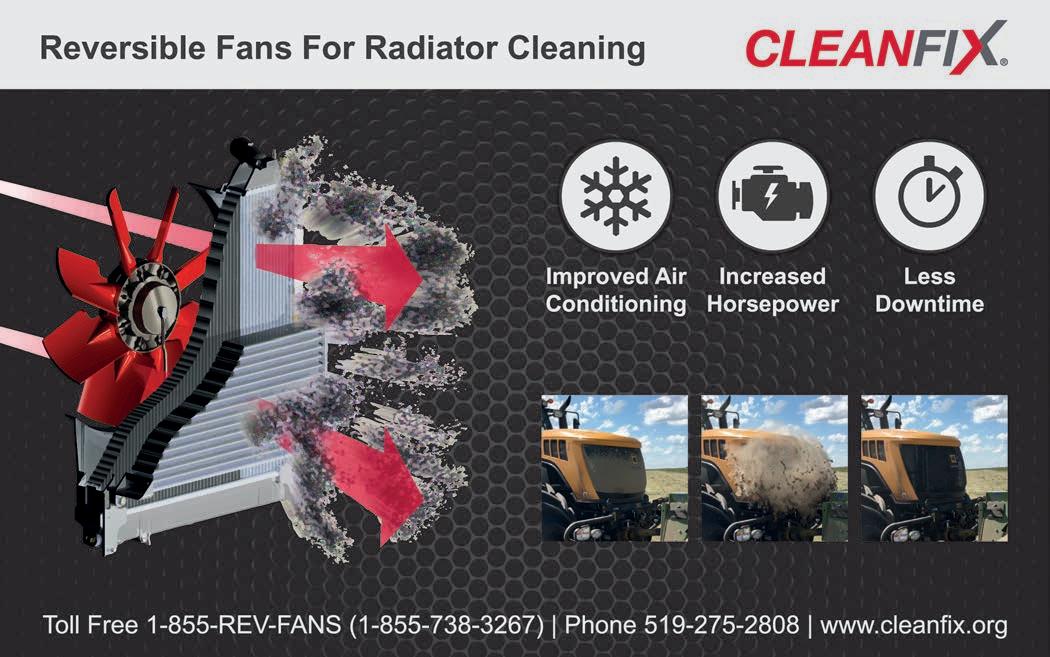
Doosan Delivers First Dozer To Mulching Business
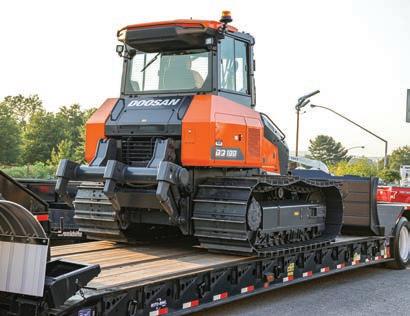
Doosan dozer arrives in Pennsylvania.
Doosan Infracore North America recently delivered the first Doosandozer, a DD100, to aBest Line Equipmentcustomer in Pennsylvania.
The 9-metric-ton machine is among the first Doosan dozers to arrive in North America, and it’s the first DD100 to be delivered to a customer: Ratoskey and Trainor Inc. Owners Ray Trainor and Rob Ratoskey operate a grinding and mulching business in East Norriton near Philadelphia. The company sells topsoil, mulch and other products to customers in southeastern Pennsylvania.
Best Line Equipment transported the first Doosan DD100 dozer from its Allentown, Pa. location to Ratoskey and Trainor on August 4. Upon arrival, the machine quickly went to work in a large pile of dirt that will be turned into topsoil.
Best Line Equipment is one of the top North American Doosan dealers and has nearly a dozen authorized Doosan dealerships in Pennsylvania and New Jersey.
Komatsu Buys Silviculture Firm
Komatsu is acquiring Bracke Forest AB, headquartered in Bräcke, Sweden, which develops, manufactures and sells application-specific attachments for silviculture. Since 2014, Bracke and Komatsu have engaged in joint development by sharing respective technologies and experience. Komatsu will continue to incorporate Bracke’s technologies and expertise in the field of planting in order to accelerate the pace of mechanization.

Maintenance, Safety Pay Big Dividends
Pursuing safety during service or maintenance operations is just as important as any other facet of a logging operation. One of the vital cogs in any good logging company’s arsenal is its maintenance program. Modern-day logging equipment is made for the rough terrain and sometimes brutal weather here in northern Minnesota. Operators run hard during the winter season, which is when most logging companies make or break the majority of its financial capital for the year. But even equipment sometimes valued at $500,000 or more breaks down and needs some TLC.
Some logging companies have maintenance shops to work on such equipment during the “spring break up” or when road restrictions in Minnesota restrict heavy-equipment hauling for six weeks or so. Others are forced to park it on their property and work on it in the elements of mother nature. During the relatively short season, when profit margins are thin, a logger can’t afford to have a vital piece of equipment down for even a few days.
Good heavy-equipment mechanics are hard to come by. They often travel into the woods to repair busted hydraulic hoses or maybe to repair a track-tensioner spring that breaks from hitting a stump, or snaps from the heavy build-up of snow/ice.
Rieger Logging, Inc., out of Northome, Minn., is a logging company with an excellent safety record. But even employers with clean histories, in terms of employee injuries, can have a hiccup.
One of Rieger’s mechanics was injured last season when working on a piece of equipment in the woods. The mechanic was working to heat and pound out a pin on an equipment track when it shattered, and a piece of the pin embedded in his leg. A trip to the emergency room and some medical care resulted in a nearly $2,500 workers’ comp claim. After reviewing the accident, company officials determined that the employee was acting within company’s safe operating procedures.
“It really wasn’t anything out of the ordinary, it’s just something that could happen anytime or not ever again,” a company spokesperson said. “He had his safety glasses on and long pants. Sometimes those things just get you.”
So what can owners do to ensure they’re prepared for the hazards and the potential of having maintenance people injured while working on machinery?
The Occupational Safety & Health Administration (OSHA) says one of the biggest tools employers can use is to develop, implement and enforce a comprehensive written safety program that includes safe work procedures for all tasks performed. Designate an employee who is knowledgeable about equipment to conduct periodic safety inspections. Try to ensure that workers are performing their assigned tasks according to established safe work procedures. And finally, immediately correct any identified hazards or improper work practices.
According to an article published in the Canadian Forest Industries newsletter in September 2018, before beginning work, try to identify any hazards and implement appropriate controls.
Operators should review pins and bushings, hoses and fittings and identify leaks. Hydraulic hoses and belts should also be checked for wear and tear and be replaced if damaged. Examining electrical components and electrical connectors and wiring is also important, as damage to these parts can be costly. Monitoring for any cuts or scars, as well as signs of water damage on connectors is recommended.
Keep an eye out for depleted areas and replace tires as necessary to get ahead of any surprise maintenance issues. Take the time to review chains and tracks while changing any damaged or loose areas along the way. Windshields as well as wipers must be in optimal shape for visibility purposes before starting the day. Battery fluid levels should be regularly checked to ensure the charge holding capacity is still up to par.
Find opportunities to refresh the crew’s knowledge. Empowering the crew to learn new maintenance tips as well as the basic inner workings of the machines gives them ownership and ensures that machines are properly maintained.
First and foremost, focus on safety. Use this time to listen to the crew and ensure they have all the necessary gear
to keep them safe. Consider implementing a refresher course for employees. Create a few topics to discuss, including checklists for proper daily and weekly inspections, maintenance activities, and operating tips.
The machinery that loggers depend on is extremely expensive and is certainly needed in order to be productive. Every piece of equipment needs to be working properly and operating efficiently to turn a profit. But the folks who keep it running are even more important to keep safe and healthy. It’s up to every owner, and really all the employees, to make sure both man and machine are well cared for. TH
JOHNSaccoman
Safety is a necessary investment, just like equipment.
John Saccoman is a loss control consultant for Choice Instance, based in Grand Rapids, Minnesota. This article originally appeared in The Timber Bulletin and is reprinted with permission of the Minnesota Timber Producers Assn.
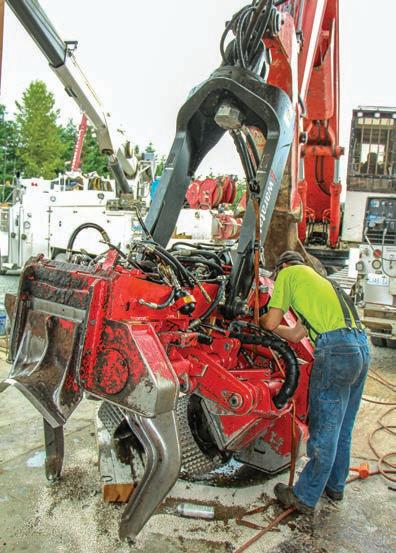