4 minute read
45 The Heat is On: Heat Illness / National Emphasis Program
from wph
Next Article
Phillip B. Russell
The U.S. Occupational Safety and Health Administration (OSHA) has launched a national emphasis program (NEP) to help prevent heat-related illnesses in outdoor and indoor workplaces. The program, CPL 03-00-024, entitled “Outdoor and Indoor Heat-Related Hazards,” was announced by Labor Secretary Marty Walsh with Vice President Kamala Harris at a union training center in Philadelphia.
Changes in Inspection Procedures
Programmed Inspections Under the program, OSHA will conduct, in certain outdoor and indoor workplaces, programmed inspections on any day for which the National Weather Service (NWS) has announced a heat warning (105° Fahrenheit or higher for at least two days) or advisory (100° Fahrenheit or higher for at least two days) in the local area. Those workplaces include the high-hazard industries named in Appendix A to the program.
Non-Programmed Inspections The NEP also requires OSHA inspectors conducting an investigation or inspection not related to heat hazards to open a heat-related inspection if a hazardous heat condition is recorded in an OSHA 300 log or 301 incident report, or if an employee brings a heat-related hazard to the inspector’s attention. The program also will require inspectors to ask during non-heat inspections whether the employer has a heat-related hazard prevention program that applies when the heat index for the day is expected to be 80° Fahrenheit or more. The NEP requires each OSHA regional office to double its number of heat-related inspections. We have already seen many seemingly unrelated OSHA inspections get expanded into heat hazards. For example, an inspection following a trenching incident in May in South Florida was expanded to include a heat-related inspection based just on the heat index. OSHA has spent far more time focusing on the heat issues than the trenching issues.
What OSHA Will Do During a Heat-Related Inspection
During heat-related inspections, the program requires OSHA compliance safety and health officers (CSHOs) to:

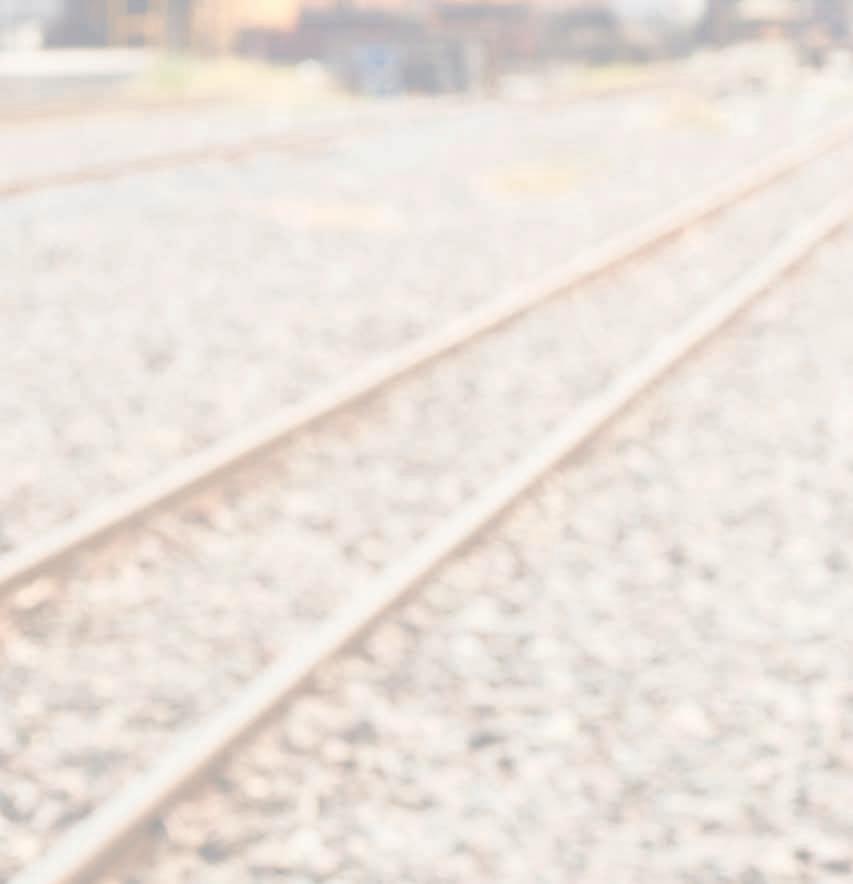
• Review OSHA 300 logs and 301 incident reports for evidence of heat-related illnesses • Review records of heat-related emergency room visits or ambulance transport • Interview workers for symptoms of headache, dizziness, fainting, dehydration, or other indicia of heat-related illnesses • Document the existence of conditions, such as high temperature, that cause the heat-related hazards • Determine whether the employer has a heat illness and injury program, including whether: • The employer has a written program • The employer monitors temperature and worker exertion • There is unlimited cool water easily accessible to workers • There are required hydration breaks for hydration • There are scheduled rest breaks • Workers have access to a shaded area • New and returning workers are provided time for acclimatization • A “buddy” system is in place on hot days • Work is scheduled to avoid hot parts of the day • Job rotation is used to limit heat exposures • Employees are trained in the importance of hydration, heat illness signs, first aid, and summoning of emergency personnel
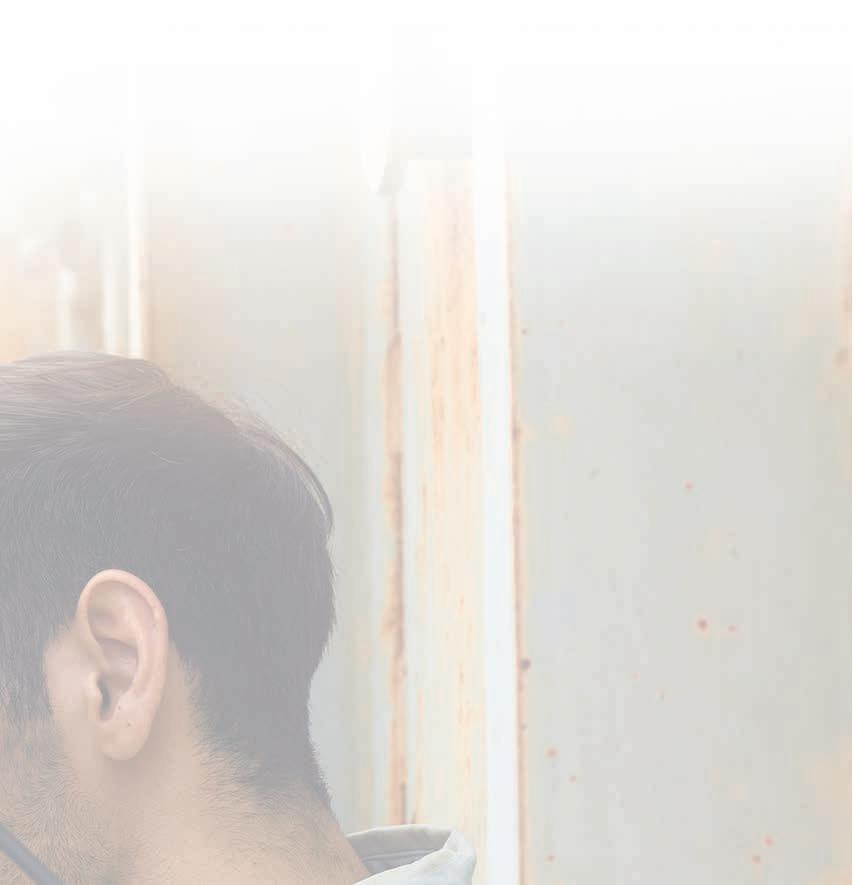
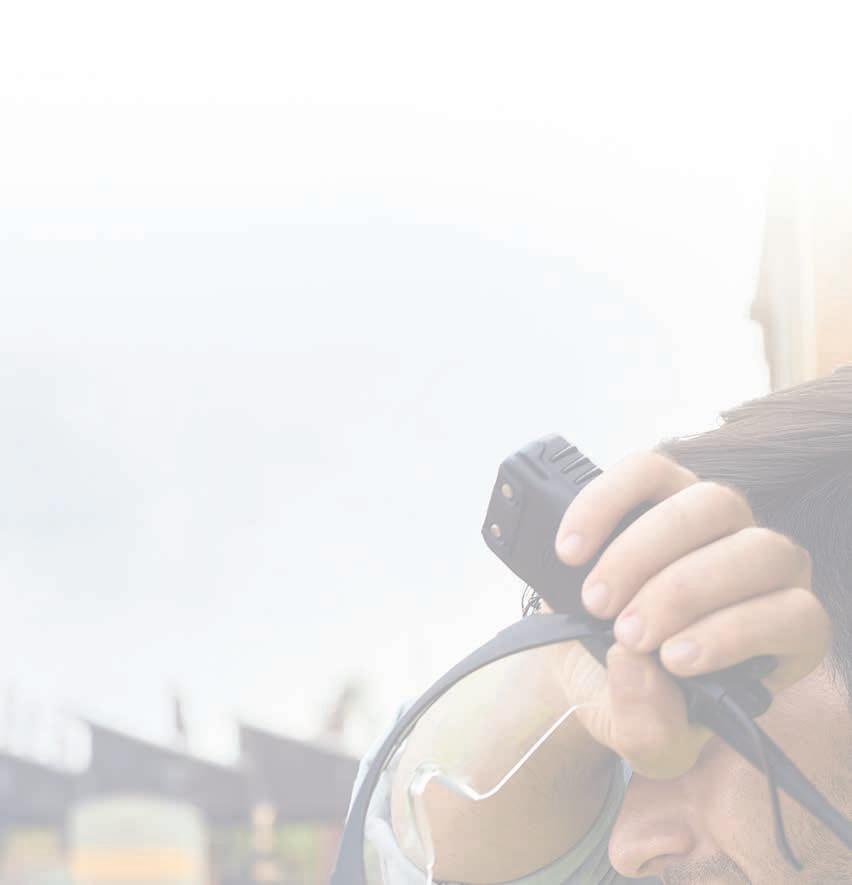
An interesting aspect of the directive is its reference to the legends and heat index ranges used by the National Weather Service’s heat index chart—“Caution” (80°F – 90°F HI), “Extreme Caution” (91°F – 103°F HI), “Danger” (103°F – 124°F HI), and “Extreme Danger” (126°F or higher HI). OSHA knows, after the scientific bases for these legends and ranges were questioned, its attorneys declined to rely on them and an administrative law judge of the Occupational Safety and Health Review Commission (in a case handled by my firm) found they lacked a scientific basis.
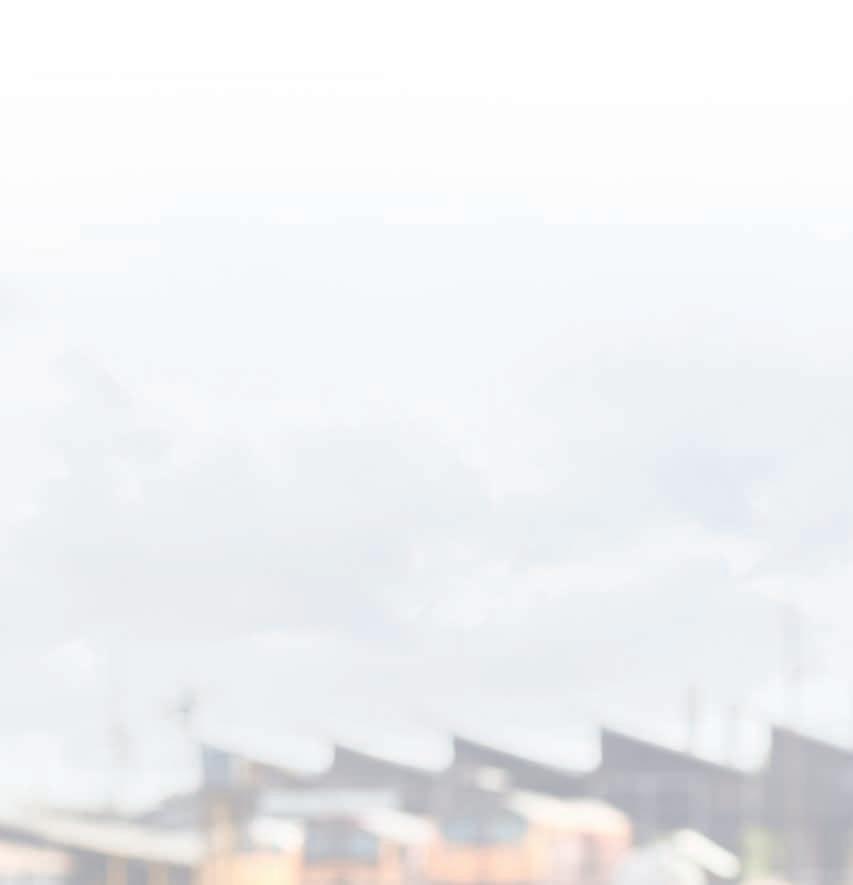
Employers with possible exposures to heat hazards may want to consider reviewing:
1. Policies - review and update (or create) a written heat illness and injury program; consider using a post-offer medical questionnaire that includes questions about conditions or medications that heat exposure may exacerbate. 2. Training - train employees on recognizing symptoms and supervisors on the entire program and how to handle emergencies 3. Compliance - monitor heat exposure projections and compliance with the program 4. Enforcement – take action when the program is not followed
These actions will help keep workers safe from heat-related illnesses and injuries and avoid or minimize any OSHA inspections or citations.
Phillip Russell is an OSHA and Employment Lawyer for Businesses with Ogletree Deakins Nash Smoak & Stewart PC. He can be reached at phillip.russell@ogletree.com or online at https:// www.linkedin.com/in/phillipbrussell/
Workplace Health Magazine gets around the WC Community!

Past Chairman of Georgia Workers Compensation Board Judge Frank McKay and Georgia Insurance Commissioner John F. King GWCA exhibitor- Sponsors Emily Whitley, Jill Jacobs both with Team Rehab, Alexis Hill with Athens Orthopedic Clinic and Alicia Trammell with Alliance Spine Dr William Brooks in Macon at the annual Workers Compensation Seminar
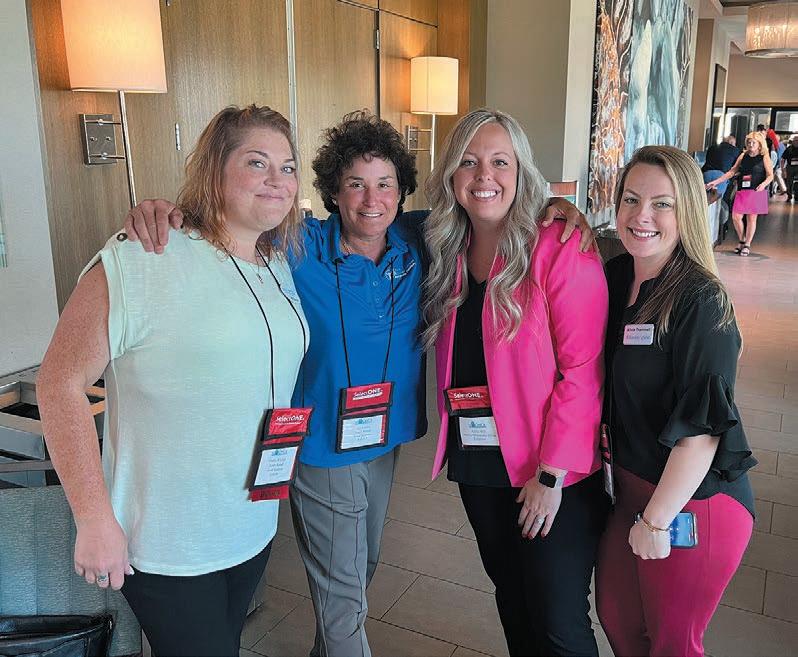
