9 minute read
Honouring research and development teams from companies and universities
Their work helps to bring new technology to market readiness.
Several companies and institutes from Germany and abroad competed for the bauma Innovation Award 2022, under five categories, at bauma 2022, the World’s Leading Trade Fair for Construction Machinery, Building Material Machines, Mining Machines, Construction Vehicles and Construction Equipment. After a multi-stage selection process, five winners were announced.
The five categories and winners are:
• Climate Protection – Liebherr France SAS, for the hydrogen-powered excavator.
• Digitalisation – MiC 4.0 Machines in Construction with one common digital language for construction sites.
• Mechanical Engineering – Herrenknecht AG, for the continuous tunnelling process.
• Construction – Holcim (Germany) GmbH, for CPC – Carbon Prestressed Concrete bauma 2022 was held from 24 to 30 October 2022, in Munich, Germany.
• Research – Freiberg University of Mining and Technology Mechanical Engineering Institute, for Deep Sea Sampling.
A total of 133 entries were received, of which 41 finalists made it to the next round. In two rounds of voting, the expert jury and task force chose their favourites. The trade journalists attending the bauma Media Dialog in Munich also had the opportunity to cast their votes in the final round.
The competition is a joint project under the auspices of the VDMA Construction – Equipment and Plant Engineering, Messe München, the Federation of the German Construction Industry (HDB), the German Construction Confederation (ZDB) and the German Building Materials Association (bbs).
HYDROGEN-POWERED EXCAVATOR FROM LIEBHERR FRANCE
SAS
Winner 2022. Category: Climate protection
The H2 drive in the crawler excavator does not require a permanent energy supply and produces very low NOx and CO2 emissions. Depending on the assessment method used in each case, and if the entire life cycle of the machine is taken into account, the hydrogen combustion engine can help to reduce CO2 emissions by almost 100%, when considering ‘tank to wheel’, or by 70% , when considering the ‘cradle to grave’ principle.
The H966 engine – heart of the machine
The first Liebherr hydrogen engine, the H966, is the heart of the new R 9H2 crawler excavator. This is an engine designed for both demonstration and field trials, and is based on an intake manifold injection technology (also known as PFI). The achieved results offer evidence of a great potential for hydrogen propulsion and indicate the possibility of using such drives for off-road applications, as well.
In addition, the company’s components product segment is working on further hydrogen-based drive technologies, such as H2 direct injection. This would enable a higher power density than the established H2 intake manifold injection and is, thus, particularly suitable for heavy-duty applications in demanding working environments, such as the construction and mining industries.
The design of the R 9H2 crawler excavator is based on the current and future Generation 8 of crawler excavators. It shares a focus for a more comfortable and efficient application. The excavator reaches the same overall performance as its diesel engine counterpart, both in terms of power output, engine dynamics and response. Suitable for extreme temperatures, shock and dust-intensive site operations, the R 9H2, with its operating weight of 50 t, can become as robust a solution for earthmoving and quarrying applications in the future, as the conventionally powered Liebherr crawler excavators in the same class already are. The only differences are in refuelling the machines. Fast and safe refuelling is ensured via infrared communication between the excavator and the refuelling station, where users benefit from the standardised high-speed protocol.
One Common Digital Language For Construction Sites
Winner: 2022. Category: Digital-
Isation
Today, many types of machines work together on construction sites. They become more digital and virtually connected every day. However, communication between construction machines and their attachments is still manufacturer-specific and is not compatible across manufacturers.

In cluster 7 (attachments) of the Machines in Construction working group MiC 4.0, a standard is being developed for cross-manufacturer communication between attachments and construction machines. The aim is not to standardise the existing mechanical, hydraulic or electrical interfaces between attachment and construction machine, but to create a universal, uniform and manufacturer-independent data interface between construction machine and attachment. Through the cooperation of over 25 users and machine and tool manufacturers, a data interface via CAN bus is being defined under the name, MiC 4.0 BUS, which can map all relevant use cases for communication between tool and machine.
This includes the identification of the tool during coupling, so that information such as serial number, tool type and manufacturer are transmitted to the machine and are available for evaluations of the use of machine and tool. Subsequently, based on the information, such as the required hydraulic pressure, the construction machine can be automatically adjusted to the tool and the machine operator can be relieved and incorrect operation can be avoided. The MiC 4.0 BUS also provides for the transmission of control data so that operation is as simple and clear as possible. By transmitting geometry data, assistance systems, such as working area limitation, can automatically work with correct data and thus support the operators in their work.
With the MiC 4.0 BUS, the control of the tools is simplified and additional operating elements and displays, which are common today, can be omitted. The provision of tool information to assistance systems eliminates the need for time-consuming manual setup. In this way, the MiC 4.0 BUS contributes to the avoidance of incorrect operation and increases safety on the construction site.
Both customers and manufacturers benefit from the fact that with the MiC 4.0 BUS, even complex tools can be used via ‘plug and work’ and time-consuming adaptions can be avoided. This means that the use of efficient, specialised tools becomes easier and more attractive, which has a positive effect on the profitability and efficiency of construction sites.
With the help of the MiC 4.0 BUS, information on the use of tools on the construction site also becomes available. This information can be used to draw conclusions for the customer about the load and operating hours of attachments, so that the MiC 4.0 BUS represents a step in the direction of ‘attachment as IoT device’. On a higher level, knowledge about tool use can also provide insights into the progress of the construction site, so that the MiC 4.0 BUS also contributes to Construction Site 4.0.
As part of proof-of-concept tests, the MiC 4.0 BUS has already been successfully tested on prototype machines and attachments from different manufacturers.
Faster And More Efficient Progress With Continuous Tunnelling From
HERRENKNECHT AG
Winner: 2022. Category: Mechanical Engineering
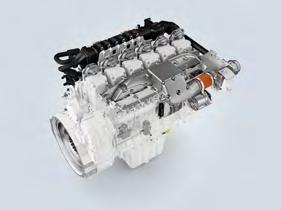
Herrenknecht AG is implementing a next innovation boost for the mechanised production of high-performance tunnel infrastructure in all common, soft ground constellations (soft ground formations with or without water-bearing layers). Using the latest technology, the continuous tunnelling process leads to a significant reduction in construction times for longer tunnel sections.
Up to now, mechanised tunnelling with shield machines in soft ground has always been a stop-and-go sequential process. Each excavation
With stroke is followed by the ring build ing sequence, so that the excavation has to pause and the subsequent driving cycle started only when the next segmental ring has been com pletely installed. The interruptions to tunnel advance in soft ground for mations caused by these sequential operations costs time, when viewed over longer distances. In contrast, a continuous tunnelling process, in which the machine can continue excavation while the lining rings are being installed, can contribute to considerable savings in construction time. For this purpose, Herrenknecht engineers designed a process based on the latest technologies and engineering.
The new continuous tunnelling system, developed by the company’s engineers, achieves a notable increase in efficiency during tunnel construction. Particularly in the case of longer tunnel sections, continuously organised tunnelling leads to measurable savings in construction time.
Basic principles of continuous tunnelling
In continuous tunnelling, the thrust cylinders that push the machine forward during advance take over the share of the force of those cylinders that are retracted for ring building.
To ensure that the machine remains on course under these conditions, the centre of thrust resulting from the combined driving forces of the applied thrust cylinders must remain unchanged in its position. At the heart of continuous tunnelling is therefore a powerful computer system and process-specific soft- ware programs that can precisely calculate the necessary pressures in the thrust cylinders. It ensures that the machine operator can reliably control the tunnel boring machine along the specified alignment as before.
Safe control in continuous tunnelling
In continuous advance, the machine operator no longer controls the pressures in the thrust cylinders manually using rotary controls (potentiometers) on the control panel. For this purpose, Herrenknecht has developed the new Center of Thrust (CoT) system, which helps the shield operator to precisely control the machine. It consists of a display panel that shows the operator the current position of the centre of pressure, based on which he select as the desired position of the centre of thrust. The corresponding control of the thrust cylinders is handled by the algorithms in the computer system. Compared to manual control by potentiometers, the CoT offers the prospect of maintaining the specified alignment more efficiently and effectively. The CoT system can thus make a sustainable contribution to the economic efficiency of the construction project, in addition to the quality of the underground structure.
With continuous tunnelling, an increase in total tunnelling performance by a factor of up to 1.6 can be achieved compared to the previous, discontinuous method. This can lead to a significant reduction in construction time for long tunnels. The unique feature of Herrenknecht’s solution is that continuous tunnelling can be used on all machine types, in soft ground.
CARBON PRESTRESSED CONCRETE FROM HOLCIM (DEUTSCHLAND) GMBH
Winner: 2022. Category: Building Carbon Prestressed Concrete (CPC) panels are made from concrete reinforced with prestressed carbon fibres, instead of the usual steel. The high-performance, thin concrete elements can help achieve material savings of up to 80% and
a reduction in the component’s carbon footprint by up to 75%.
The smaller amount of concrete massively reduces the self-load of the structure, lowers the CO2 footprint and also significantly reduces transport costs. A further CO2 reduction of the component results from the use of significantly smaller quantities of carbon, instead of large quantities of steel (factor of 30).
The thin elements can be manufactured industrially and in large formats and then cut to size. In addition to simple cuts, freely shaped cuts, surface treatments such as milling and brushing, drilling and slot milling can also be performed.
The CPC panels were developed by the Swiss company, CPC AG. Holcim Germany and its subsidiary Vetra Betonfertigteilwerke GmbH cooperate with the company in the market launch of the innovative components and further optimises their design (e.g. via concrete technology and composition). In Essen near Oldenburg (Lower Saxony), a large-scale plant for CPC panels is being built. CPC AG is supplying the technology and the carbon fibres which will be produced at a new plant that has been built in Switzerland.
With the first general building approval (abZ) for prestressed carbon concrete in Germany, which was granted at the end of 2021, the resource-saving and climate-friendly concrete components with CPC technology can now also be used without complications. The approval covers the complete structural design of the CPC slabs, which can be used to individually design many structural components, such as stair treads, balcony slabs and exterior wall cladding. Modular bridges can also be created easily, and in a resource-saving way, with CPC panels.
Deep Sea Sampling From Freiberg University Of Mining And Technology Mechanical Engineering Institute
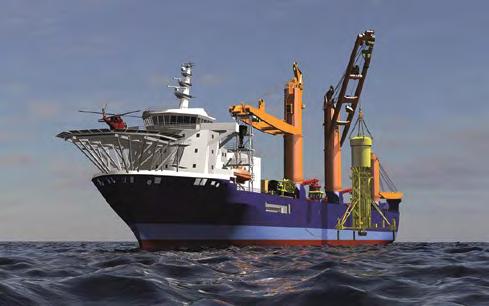
Winner 2022. Category: Research
Whether copper, cobalt or rareearth metals, the global demand for these and other raw materials is tremendous and will continue to grow in the coming years. This development is accelerated by major trends such as electrification and the energy revolution. To cover the demand for raw materials, existing capacities must be expanded, and new deposits developed. There is great potential in previously unexplored deposits (for example of massive sulfides) in the deep sea, i.e. at 2000 m or more, below sea level.
Nevertheless, new equipment and technologies are required for their exploration and extraction – which is the focus of the joint project Deep Sea Sampling, subsidised by the German Federal Ministry for Economic Affairs and Climate Action (Bundesministerium für Wirtschaft und Klimaschutz, BMWK).

The project partners are the TU Bergakademie Freiberg (Freiberg University of Mining and Technology), with its institute for treatment equipment and recycling system technology as well as its mechanical engineering institute; the University of Rostock; FAU Erlangen-Nürnberg along with Krebs & Aulich GmbH; and BAUER Maschinen GmbH. The Federal Institute for Geosciences and Natural Resources (Bundesanstalt für Geowissenschaften und Rohstoffe, BGR) as well as the Deep Sea Mining Alliance (DSMA) are also represented on the project support committee. The research project was launched in 2021 and is scheduled for com- pletion in 2024. The goal is, instead of using a surface approach for the extraction of raw materials, to electrify a compact trench cutter and transform it into a smart, semi-automated vertical mining unit. This unit separates and characterises the extracted material during the mining process directly on the sea floor. This should not only ensure a minimally invasive, efficient mining of resources, but also capture turbidity clouds generated by the work in a closed, shielded process.
When developing such technology, numerous factors must be considered. Conditions on the sea floor include water pressures of up to 400 bar, complete darkness and temperatures around 1° C – enormous challenges for equipment technology. This is accompanied by the composition of the massive sulfide deposits with their rugged surfaces and extreme slope gradients.