7 minute read
THERMAL RUNAWAY IN EV BATTERY PACKS DESIGNING A MITIGATION STRATEGY
By Tom Lombardo
Aspen Aerogels’ cutting-edge materials protect against thermal runaway
Thermal runaway occurs inside a battery cell through a fault, a crash scenario or some other defect that causes the cell to release thermal energy through chemical reactions. That thermal energy increases the temperature of the cell, the increased temperature drives faster kinetics, and more heat is released, further driving up the temperature.
Eventually, you can get to a tipping point and, essentially, the cell catches on re. ermal propagation occurs when that rst cell in thermal runaway causes its neighbors to also tip over into thermal runaway, which then spills over into the cells next to them.
Speaking at the recent Charged Virtual Conference on EV Engineering, John Williams, Vice President of Technical Services at Aspen Aerogels, gave an excellent overview of cutting-edge techniques to delay or prevent thermal propagation scenarios.
Safety standards
First, a little background. In China, the standard for thermal propagation delay is ve minutes, explained Williams. What that means is that, from the moment of detection of a hazardous situation in the battery pack, you must have a ve-minute delay before there’s a dangerous situation in the passenger compartment. ose ve minutes allows the driver to nd a place to park, exit the vehicle, and get a safe distance away.
“A ve-minute thermal propagation delay is essentially the table stakes now for manufacturers of electric vehicles,” said Williams. “As electric vehicles become more common, that ve minutes will almost certainly ratchet up to longer durations until, eventually, we would reach the promised land of having no thermal propagation at all.” e ultimate goal is that one cell can go into thermal runaway and that’s it. It will be a maintenance event and not a safety event. But we’re not there yet, and Williams explained why.
The physics of thermal propagation
e physics of thermal propagation involve multiple pathways for heat to transfer from a cell in runaway to its neighbors, Figure 1. e rst and most important is cellto-cell conduction, and Williams is an expert in this particular pathway. Aspen Aerogels manufactures a barrier material, called Pyro in, designed to prevent cell-to-cell conduction. But that is not the only thermal pathway. ere is also gas release, both primary combustion, in which the reactants come from within the cell, and secondary combustion, in which the fuel inside the cell reacts with the external environment. ese gas ows and reactions drive a lot of the behaviors inside a pack
Better C2C insulation extends time-at-temperature
Secondary combustion (internal & external reactants): depends on gas-management during a thermal propagation event. ere are also hot particulates being ejected during the initial phase of the thermal runaway. ere are secondary conductive pathways, such as busbars, cooling plates and structural interconnects between cells. ese are essentially thermal bridges—conductive pathways around a cell-to-cell barrier. Also, heat may be transferred through natural convection across air gaps that allow hot gases to spread throughout the battery pack.
“Active cooling can help draw down the energy of a cell in thermal runaway,” explained Williams, “although many times you can’t count on it, especially a er a crash scenario.”
Thermal and mechanical barriers
A thermal barrier material between the cells can reduce heat transfer through cell-to-cell conduction. Barriers in prismatic and pouch packages serve two purposes: mechanical and thermal. e ideal barrier acts as both a mechanical compression pad and a thermal insulator, but there’s a trade-o : materials that make very good compression pads o en provide little thermal resistance, and those that act as good thermal and gas barriers tend to be too sti to serve as compression pads. e right-hand side of the graph shows that materials commonly used as compression pads, such as silicone foams and polyurethane, can absorb a lot of strain energy, but their temperature tolerances max out around 100-300° C. On the le side of the graph, we see that metals and mica sheets are very resistant to high temperatures, but aren’t good at absorbing mechanical energy. e Holy Grail of barrier materials would reside in the upper-right corner of the graph, providing heat resistance ve times greater than silicone foam and mechanical absorption four orders of magnitude above that of mica sheets. According to Williams, Aspen Aerogels’ Pyro in ts the bill.
Cells will swell as they age, and breathe as they go through charge-discharge cycles. Compression pads absorb the resulting cell movement. Swelling with age occurs over extended time scales, but the breathing that occurs over a short time interval has to be absorbed by the cell-to-cell barrier in order to maintain consistent pressure. Polyurethane and silicone foams are very e ective compression pads, but, as low-temperature materials, they simply cannot withstand thermal runaway situations. ey may delay thermal propagation a bit, but rarely enough to achieve even the ve-minute standard, and certainly not more than that. A good barrier is a exible material that’s also capable of withstanding high temperatures. ose two attributes— exibility and high-temperature tolerance—are o en mutually exclusive.
Figure 2 shows potential cell-to-cell barrier materials, with the Y-axis representing the maximum exposure temperature that a material can withstand and the X-axis indicating how much strain energy a material can absorb.
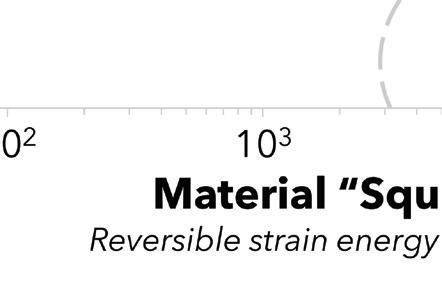
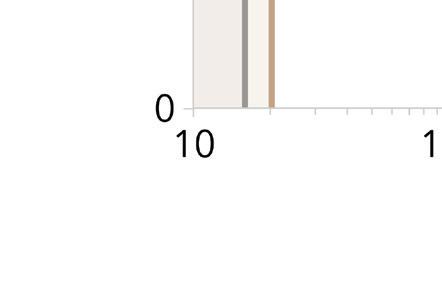
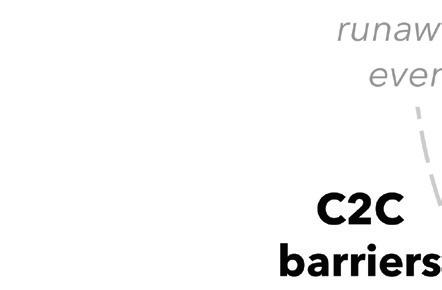
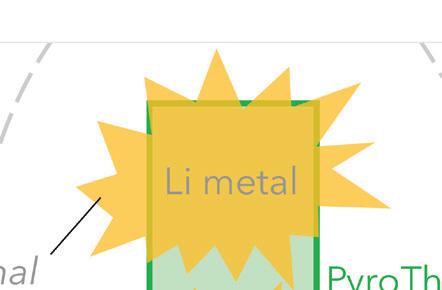
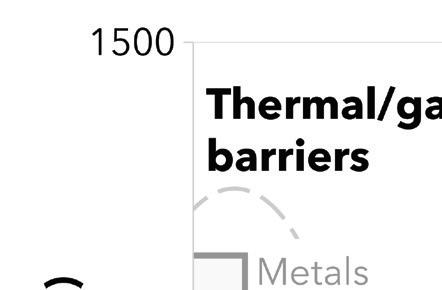
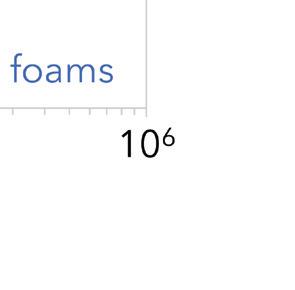
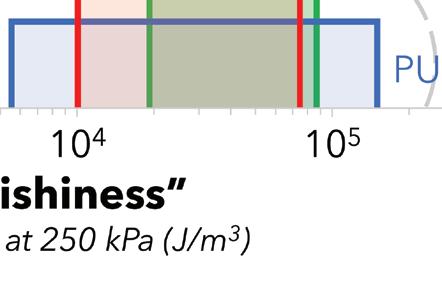
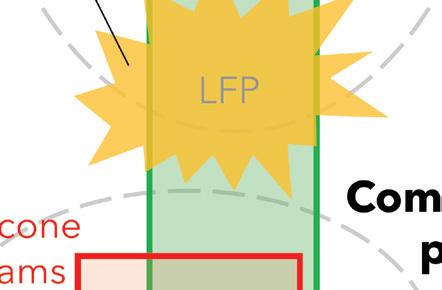
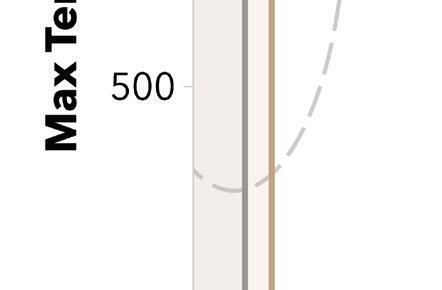
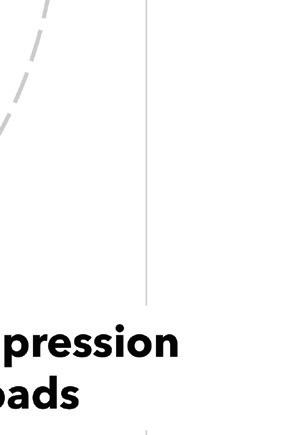
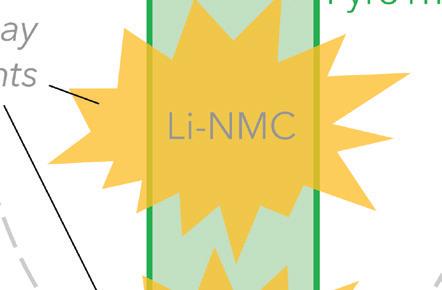
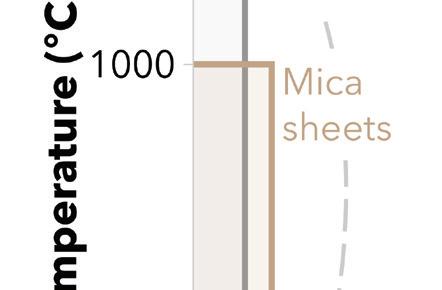
“ e universe of possible things that can live in that neighborhood is very, very small,” said Williams. “One of them is an aerogel such as our Pyro in, which is engineered speci cally to be a unitary material inside a cell-to-cell barrier, providing both the mechanical function of a compression pad and the thermal function of a re barrier.”
Aspen Aerogels has been in the aerogel business for more than 20 years, primarily focused on optimizing energy e ciency and passive re protection for industrial energy facilities. e company is now transferring its experience to the EV segment, with the goal of developing the world’s best cell-to-cell barriers. Aspen’s testing shows that a two-millimeter sheet of Pyro in material can withstand exposure to a propane torch at 1,000° C, and absorb the strain energy from cell breathing and swelling. Williams claims that Aspen’s aerogels are the thinnest insulating materials available, and that they o er the best possible thermal insulation properties.
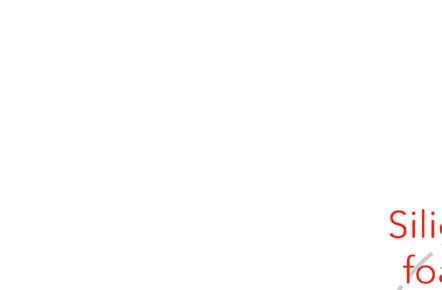
It’s the chemistry

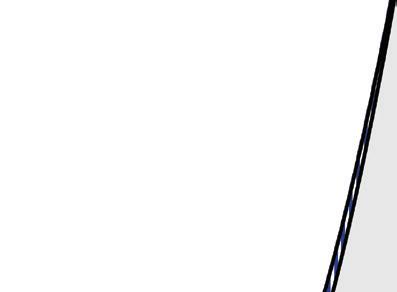
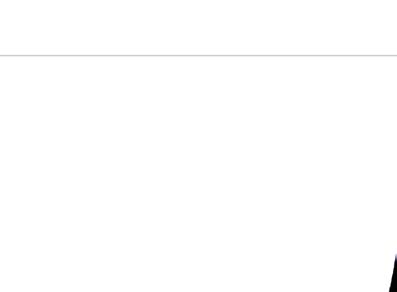
An aerogel is produced when complex polymer chains of silica molecules form through a sol-gel process. is process is similar to making gelatin, but using silica and ethanol instead of sugar and water. A wet phase of suspended silica starts out with the viscosity of water; in about two minutes, the suspension turns gelatinous. In the process, the silica self-assembles into long polymeric chains, which house tiny nano-pores.
“ at nano-porosity is the secret in an e ective thermal insulation material,” said Williams. “An aerogel’s pores are 10,000 times smaller than that of any other insulation material. In that four orders-of-magnitude di erence, the physics completely changes. Now you have a material that has a thermal conductivity lower than still air, which means that when you compress it and squeeze out the air, the thermal conductivity can actually get better, [see Figure 3]. Under the same conditions, almost every other insulation material will get worse.”
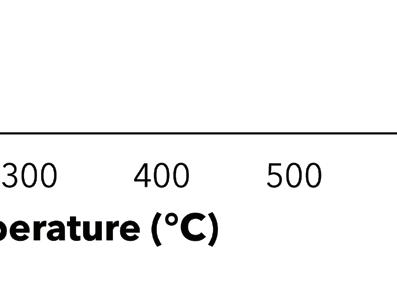
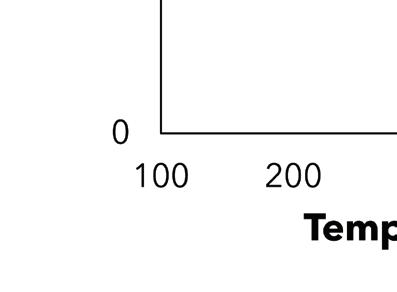
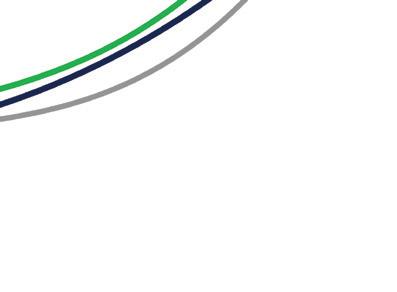
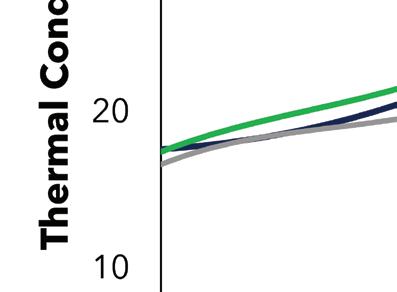
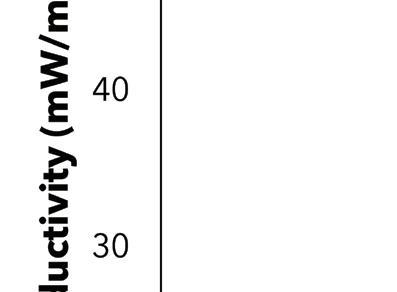
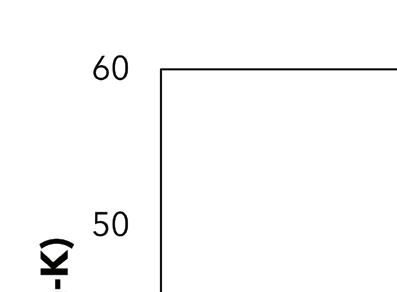

Figure 4 shows the relationship between compressive stress and strain—the area under the curve represents the amount of strain energy the material can absorb reversibly. Williams says that Aspen’s newer M-grade materials will continue to absorb strain energy over the life of a vehicle with minimal compression set or fatigue.


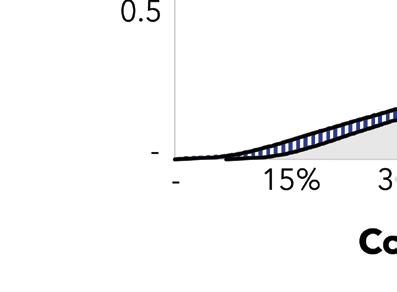

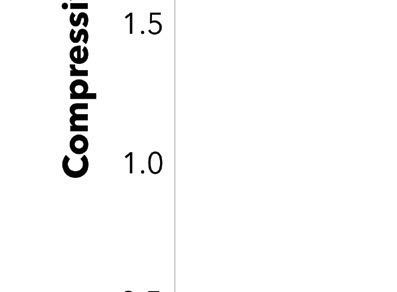
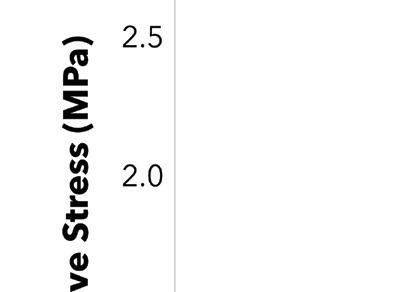
Real-world testing
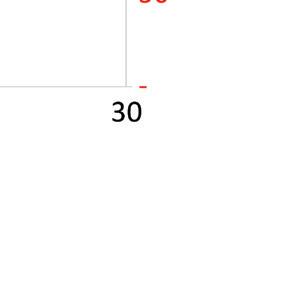
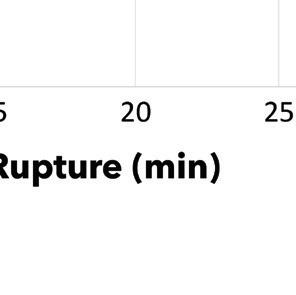

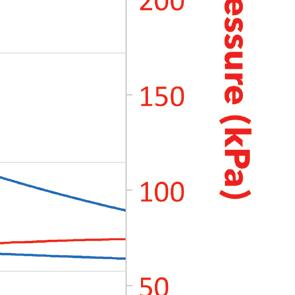
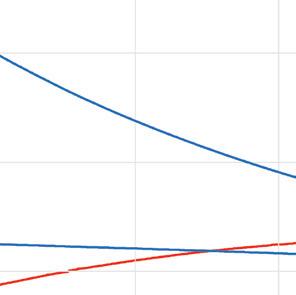
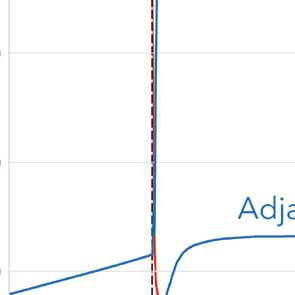

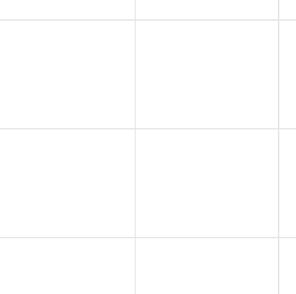
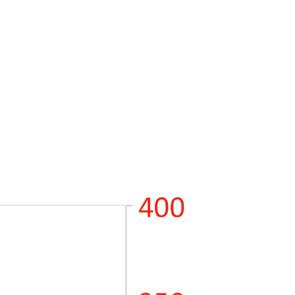
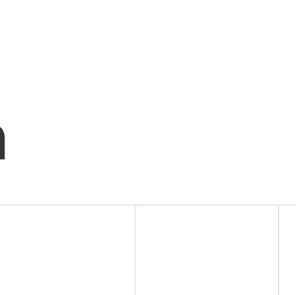
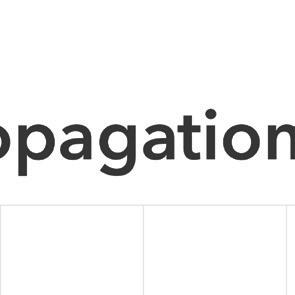
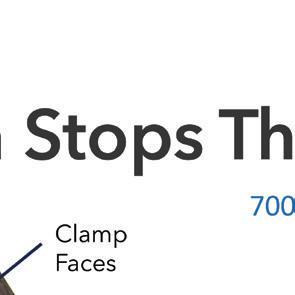
To test how materials behave during a thermal event, Aspen’s engineers subject the materials to mini-module testing. For example, they put a thermal barrier between two cells and triggered one cell with a heating pad to see if the barrier would prevent thermal propagation from one cell to the other.

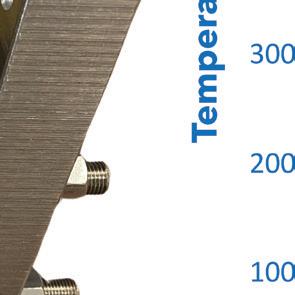

e test setup in Figure 5 includes two o -the-shelf prismatic cells compressed inside of a jig, allowing the experimenters to control the cell-face pressure. e pressure at the end of a cell’s life tends to be higher than at the beginning of its life, so Aspen conducts a worstcase scenario test by arti cially creating higher pressure inside the jig. e graph on the right shows that the elevated temperature of the trigger cell (right) is absorbed by the barrier material, keeping the temperature of the adjacent cell (le ) at a safe level.
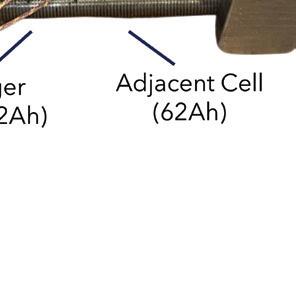

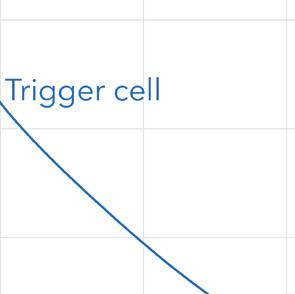

is mini-module experiment has limitations, however. In a real battery pack, other pathways—secondary conduction, hot particulates and convection—also a ect the system. is test merely demonstrates that thermal runaway can be stopped at the cell-to-cell level, allowing designers to focus on isolating the other mechanisms. Pyro in has about the same density as urethane foam, but the latter isn’t a thermal barrier. Urethane foam coupled with a thermal barrier will typically be heavier than a comparable part that’s made with Pyro in alone. Because Pyro in is both lighter and thinner than other thermal/mechanical barriers, battery designers can pack more cells into the same space, increasing vehicle range.
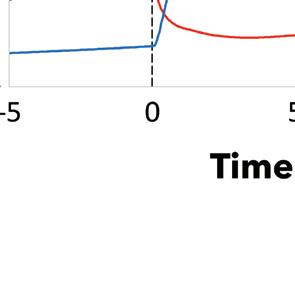

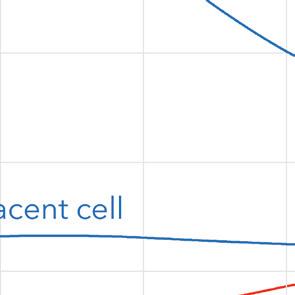
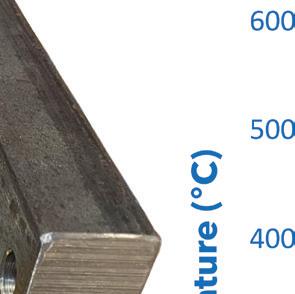
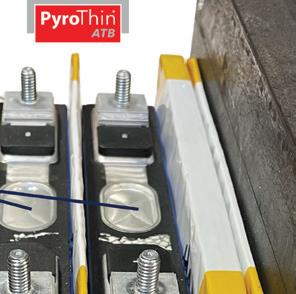
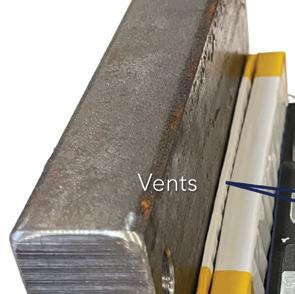
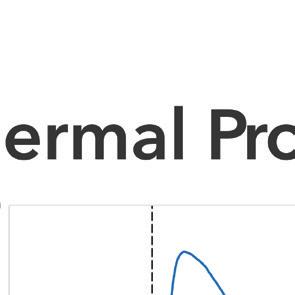
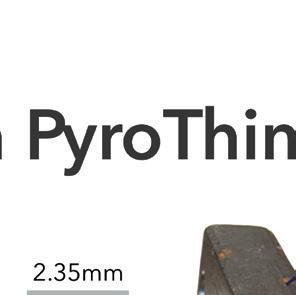
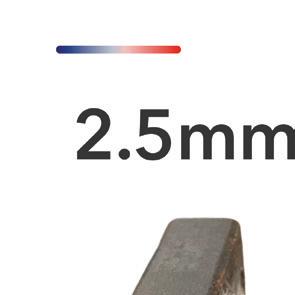
Other cell packages and battery chemistries
Aspen concentrates on Li-ion cells in prismatic and pouch packages because the aerogel material naturally lends itself to at, rectangular objects. In cylindrical cells, the interstitial space is a lot more complex, so other materials may perform better than Pyro in as cell-to-cell barriers. In those situations, Williams says that Pyro in is still suitable for pack covers, sidewall covers and other at geometries.
Some of the company’s customers have successfully used Pyro in with lithium-metal batteries, which tend to burn hotter than Li-ion cells, sometimes reaching 1,200 to 1,400° C. Lithium-metal batteries employ di erent grades of Pyro in, depending on the temperature requirement.
Partnerships
Aspen Aerogels currently o ers consulting services through its global engineering support team, which includes engineers in Asia, Europe and North America who will answer questions about battery pack and barrier designs. e company’s customers include General Motors, which has chosen Pyro in as the cellto-cell barrier for Ultium, the modular battery and drivetrain platform that will power more than 30 new EV models.
To learn more about thermal barriers, check out Aspen Aerogel’s presentation at the Charged Virtual Conference: ChargedEVs.co/AA-Webinar