6 minute read
SiC Inverter Platform
Powered by Silicon Mobility OLEA® T222 FPCU & OLEA® APP INVERTER Software
3-Phase SiC MOSFET Intelligent Power Modules
• Up to 1200V/350kW
• Integrated SiC Gate Driver
• Low-ESL DC-Link Capacitor
• Reference Liquid Cooler
Motor Control Board & Software



• ISO 26262 ASIL-D
• OLEA® T222 FPCU chip
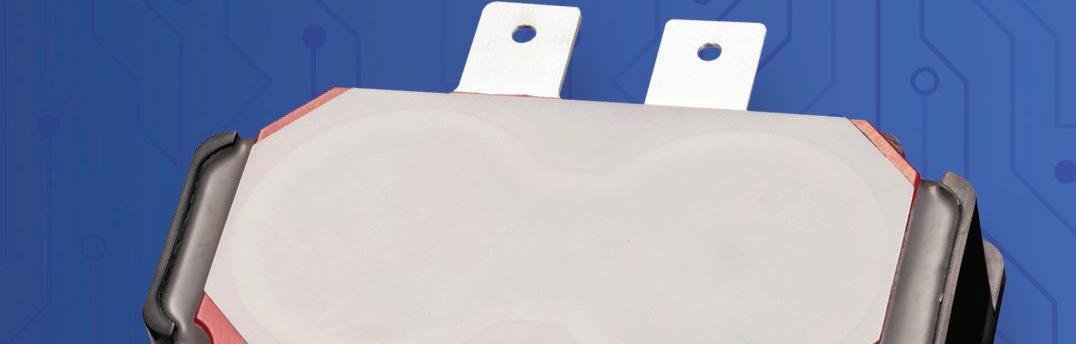
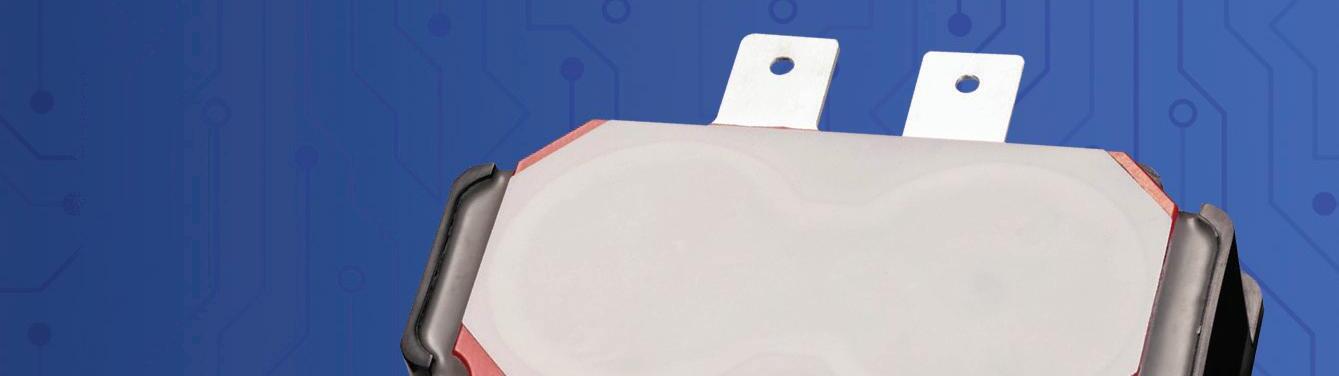
This optimal mechanical & electrical integration of a 3-Phase Silicon Carbide MOSFET Intelligent Power Module from CISSOID together with OLEA® control solution and application software from Silicon Mobility accelerates the development of Compact and Efficient e-Motor Drives! www.cissoid.com
• Advanced control algorithms & software libraries for e-motors
ZF reaches milestone: two million EV motors produced
is year, automotive supplier ZF reached the milestone of two million electric motors produced.
To keep pace with the global increase in demand for EVs, the company has been continuously accelerating production at its lead plant in Schweinfurt, Germany. It has also commissioned major production lines in Serbia and China. Another plant in North America will go into operation in 2023.
Recently the company has begun focusing on a new technology: hairpin winding, which enables wires to be packed tighter together, resulting in increased power, speed and torque while using the same amount of space.
According to ZF, there is even more innovation potential for electric motors—for example, sophisticated cooling solutions.
“Currently we are developing a solution with oil owing past—to directly cool the copper wire, which is the main heat source in electric motors,” explains VP Roland Hintringer. e company also develops electric motors with magnets that are almost free of heavy rare earth metals. Another potential future technology: separately excited electric motors that don’t need any magnets at all.
In view of globally increasing volume and the high demand for electric powertrain technology, ZF expects to reach the next production milestone soon. “Our order books are well lled,” says Hintringer. “ e next two million units of electric motors will probably be produced in less than two years.”
MAHLE receives 1.4 million euros in e-compressor orders
German auto parts manufacturer MAHLE is increasingly becoming an e-mobility supplier. e company says its electric AC compressor is particularly sought-a er thanks to its peak power of 18 kW, which makes it the most powerful e-compressor on the market at the moment.
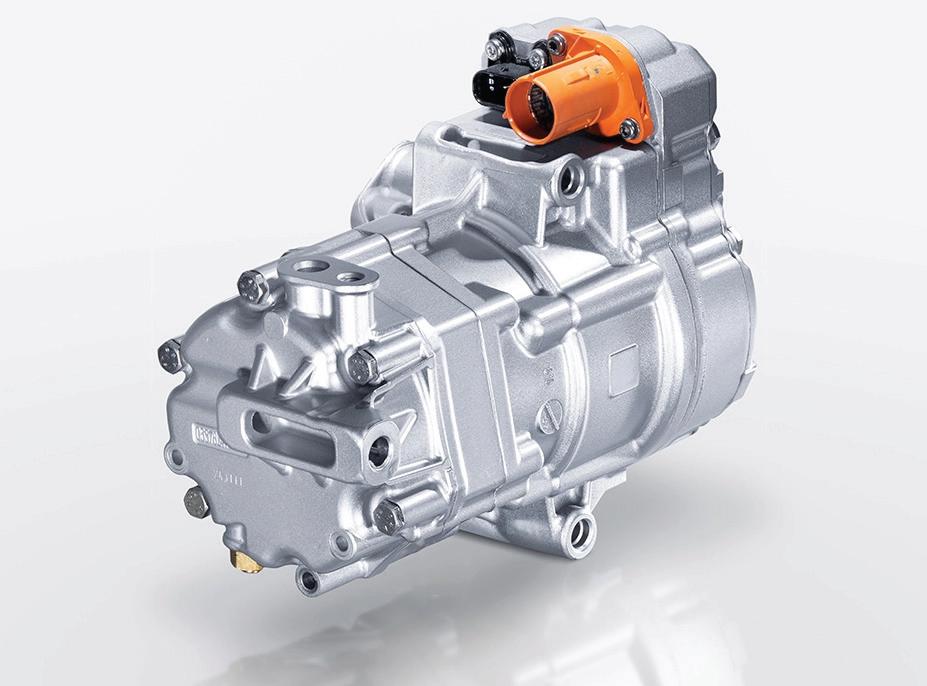

e company says it has already secured numerous series orders in the passenger and commercial vehicle sectors, amounting to approximately 1.4 billion euros.
E-compressors are one of the key components in EV thermal management. ey regulate the temperature of the electric drivetrain, and are thus crucial for the service life, charging speed and cruising range of the battery.
In addition to e-compressors for e-mobility, MAHLE develops and produces electric actuators, auxiliary components, engine accessories, auxiliary aggregates, electronics and so ware, as well as entire thermal management systems. According to the company, between 2022 and 2026, more than 20 electri ed vehicle platforms from leading passenger and commercial vehicle manufacturers will be launched on the market that rely on its technology and products. MAHLE says it already generates over 60% of its sales independently of ICE vehicles, a share that it hopes to increase to 75% by 2030.“MAHLE will continue to expand its role as a complete system supplier for air conditioning in EVs,” said Arnd Franz, CEO of the MAHLE Group.
KMD launches constant-velocity driveshafts for EVs

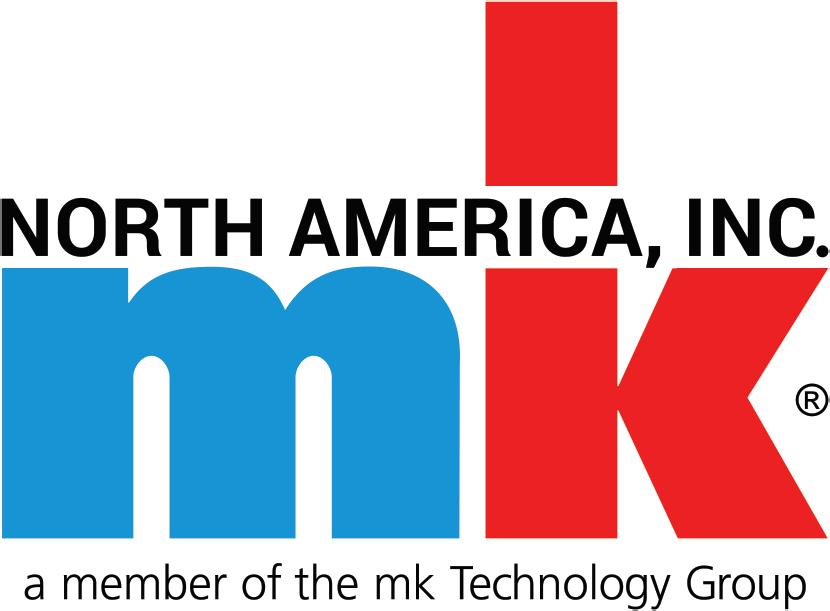
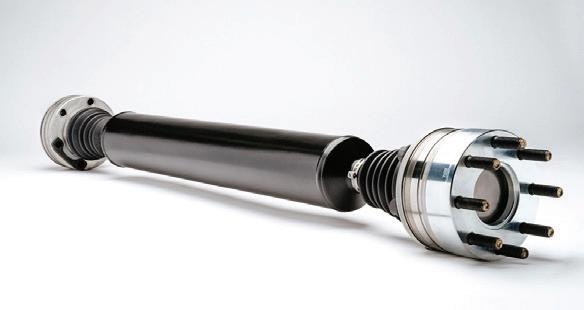
Kalyani Mobility Drivelines (KMD), a manufacturer of driveline components, has introduced a lineup of constant-velocity (CV) drivesha s for EVs and other specialty vehicles.
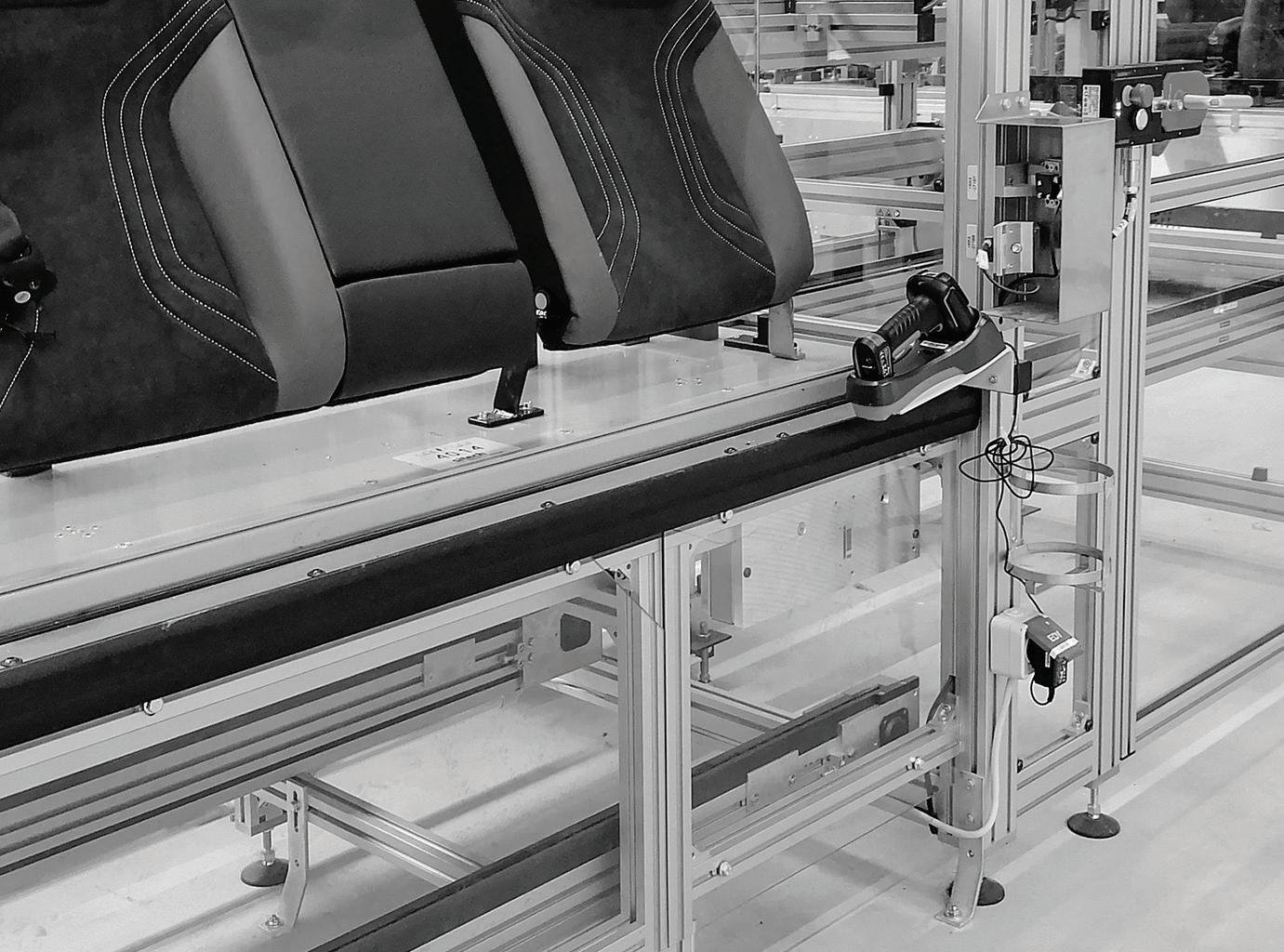
KMD’s CV drivesha s are designed using high-strength steel for optimal performance under high torque generated by EVs, military, specialty and motorsports vehicles, and are engineered for a range between 7,000 and 16,000 Nm of torque at speeds up to 8,000 rpm.
e company says its drivesha s o er design exibility with no need for the equal angle alignment required by cardan designs.
ey’re also designed to provide smooth operation and long life, even under the most extreme operating conditions faced by military and specialty vehicles.
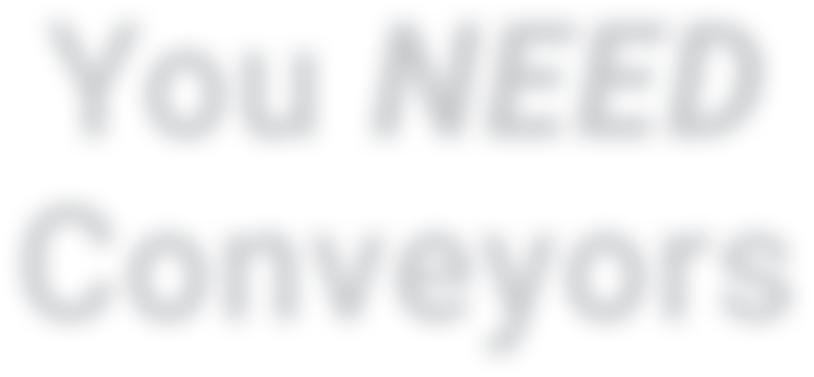
“EVs and other vehicles that create high torque put tremendous stress on driveline components. We engineer our CV drivesha s to survive under loads that would cause other drivesha s to fail,” said Dave Moore, Engineering Manager at KMD.
Maserati’s first fully-electric car powered by three Marelli 800 V motors
Italian automotive supplier Marelli developed and manufactured the three e-motors used in the new Maserati GranTurismo Folgore, and also provided its proprietary Adaptive Driving Beam Matrix LED headlamps and Telematic Control Unit connectivity system.
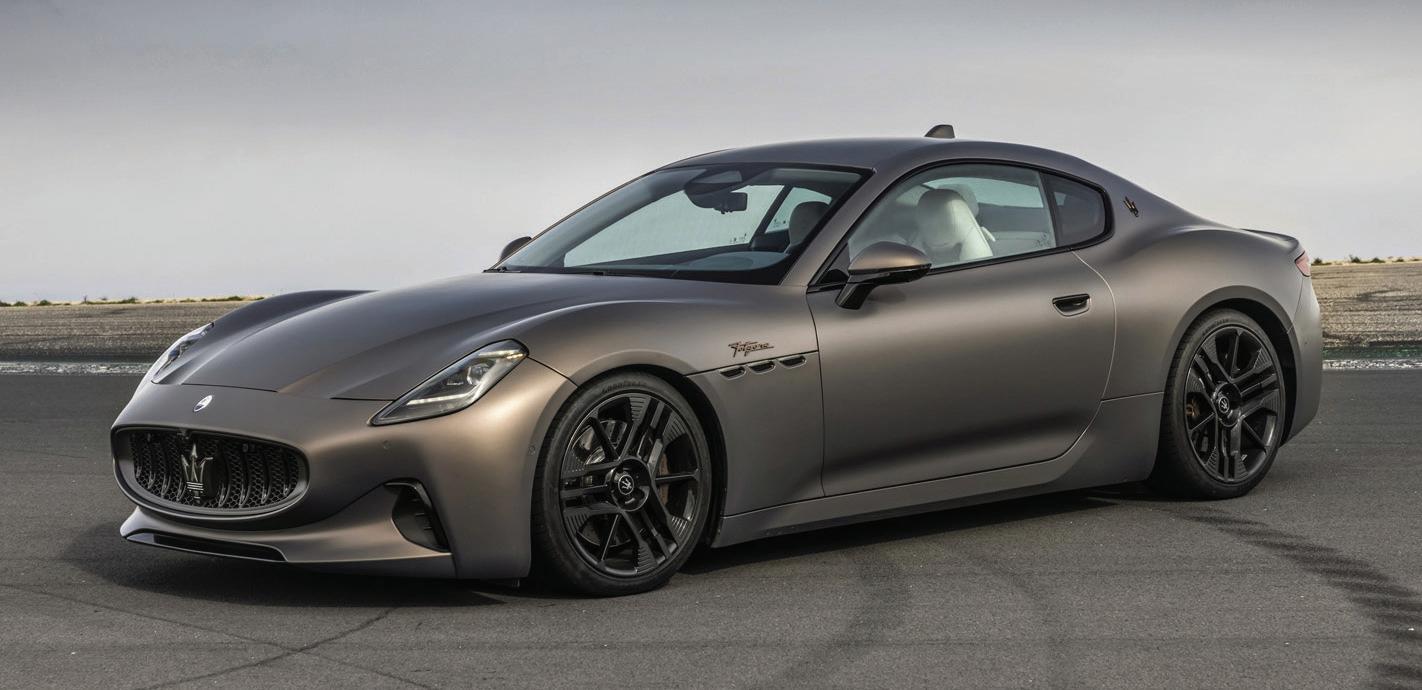
e 800 V motors, which were developed over a twoyear span and produced at Marelli’s Modugno plant in Bari, Italy, supply a total installed power of 1,200 hp in a compact pro le. ere are two motors mounted on the front axle and one on the rear, and they deliver a powerto-weight ratio of 9.2 kW/kg and total torque of 1,350 Nm.
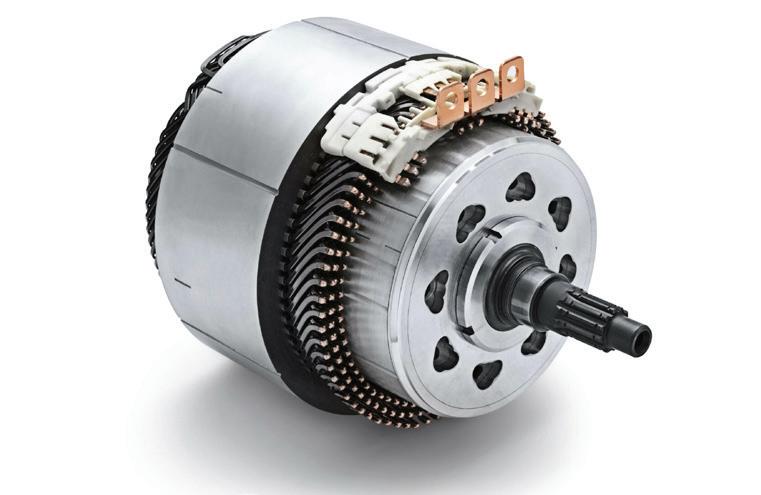
Cummins tests new ePowertrain on track at Millbrook Proving Ground
Cummins, which has been building diesel engines for heavy-duty vehicles since 1919, is methodically moving into the electric age. Now the company has successfully demonstrated a new ePowertrain for heavy-duty vehicles, using a test truck at Millbrook Proving Ground in Bedfordshire, England.
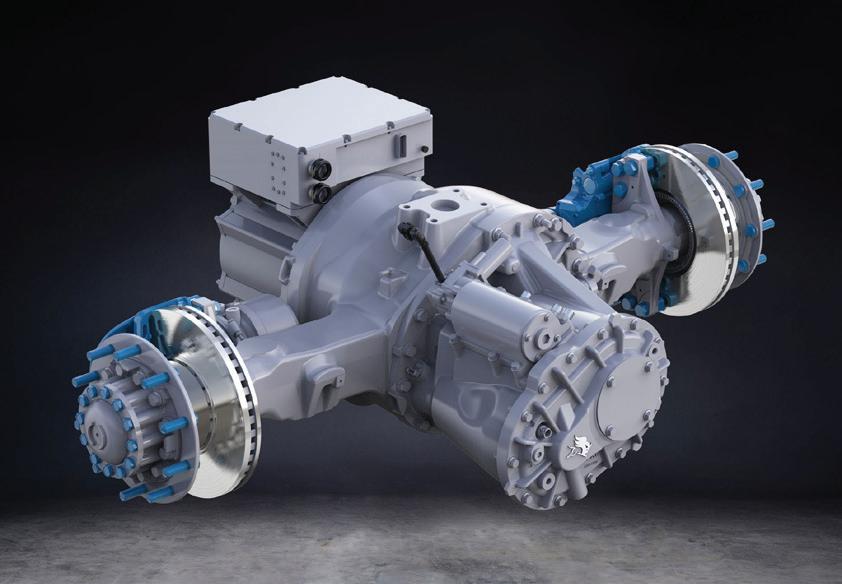
Solid conductors in the hairpin windings of the stator, Marelli says, result in improved electromagnetic and thermal performance and a greater than 80% lling factor. e company also says that its choice of rotor geometry and the use of speci c segmented magnets, as well as optimized skew of the laminate stack, reduce noise, vibration and magnetic cogging. Its cryogenic cooling process used in rotor production, reaching about -200° C, ensures perfect t of the sha into the stack.
e integrated 17Xe ePowertrain, developed by Meritor (now part of Cummins) with Advanced Propulsion Centre (APC) consortium partners Editron and Electra, features output capacity of 430 kW continuous power. It’s designed to power heavy-duty trucks and buses in 6×2 or 4×2 con gurations, and is available in a range of ratios and with three-speed transmission capabilities. Danfoss’s Editron division developed and supplied the electric motor and silicon carbide inverter powering the axle. e motor is based on a patented architecture and thermal management methodology that exceeds the APC’s 2035 Roadmap targets for power density. As a result, only one motor will be required in the electric powertrain—Cummins says current alternatives usually need two motors to meet this product segment’s power requirements.
APC Senior Project Delivery Lead Sunil Maher called the demonstration a major milestone. “Seeing this prototype vehicle in operation is a signi cant step to addressing net-zero transport challenges in the UK. I look forward to the next stage of development, which will see technical improvements and further product variation, to deliver solutions for heavy-duty and commercial vehicles.”
LEM’s new UL-certified bidirectional DC meter for fast EV chargers
e public charging industry is moving towards per-kilowatt-hour (as opposed to time-based) billing, and manufacturers will increasingly be required to incorporate certi ed DC meters into their charging stations.
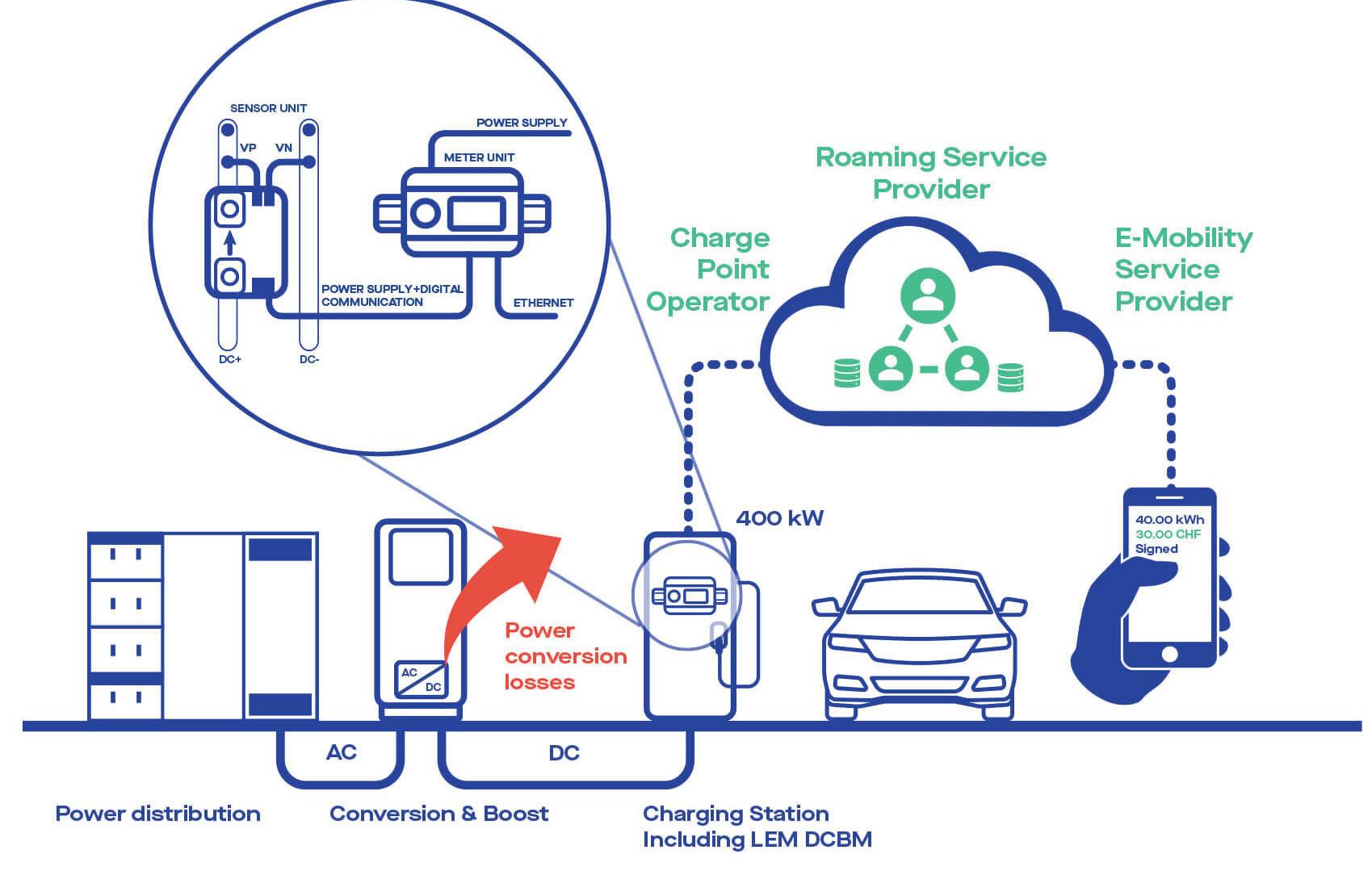
To meet this need, electrical measurement specialist LEM has introduced the DCBM, a UL-listed bidirectional DC meter for fast EV chargers.
e DCBM “will enable makers of EV charging stations to accelerate their certi cation for DC metering requirements following Certi ed Test and Evaluation Professional/National Type Evaluation Program (CTEP/NTEP) certi cation,” says LEM. “ e DCBM will simplify the process of the manufacturers having to qualify their own charging stations for UL certi cation and, for extra peace of mind, will undergo a fresh audit every quarter.” e new meter is capable of monitoring current, voltage, temperature and energy usage, and has been designed with data security and exibility in mind. e DCBM 400/600 complies with the UL 61010 and UL 810 standards in the FTRZ category for EV applications. To achieve this certi cation, the meter had to pass reinforced insulation tests, temperature testing of all its components and sub-assemblies, testing for protection against electric shock, durability of markings tests, equipment temperature limit tests, and resistance to heat/ re risk tests. e DCBM is designed for DC chargers from 25 kW to 400 kW, and integrates the signed billing data sets according to the Open Charge Metering Format (OCMF) protocol. It can be retro tted to existing charging stations, and has a moveable measuring element for use with any type of charging station architecture. It is accurate in temperatures of -40° to 185° F, and has an IP20-rated casing.
Other features include Ethernet support and bidirectional energy metering, which makes it compatible with V2G (vehicle-to-grid) and V2X (vehicle-to-everything) applications.

“ e US and Canadian markets for EVs are continually expanding, but this growth could be held back by insu cient access to rapid DC charging stations,” said Claude Champion, General Manager at LEM USA. “LEM understands exactly what the sector needs, and has worked closely with EVCS manufacturers and installers when developing solutions like the DCBM 400/600.”