2 minute read
Prefab Apartment Buildings — A Coming Phenomenon?
The technical term is “Modular Construction,” meaning a building constructed in modules in an off-site factory under controlled plant conditions using almost identical materials as conventional construction (primarily wood, concrete, and steel) and adhering to all local building codes.
Prefabrication is a concept that’s been around for a century, though adoption as a mainstream construction option has been slow to take hold. More recently, however, evolving technologies, economic forces, and societal needs have sparked interest.
Tom Hardiman, executive director of the Charlottesville, Virginia headquartered “Modular Building Institute” (MBI), the industry’s non-profit trade association, advises that annual production of factory-built projects has doubled in the last five years, accounting for 5.6% of buildings constructed nationwide last year (excluding detached single-family residences). And of interest to the rental housing community, apartments are the fastest growing sector in modular construction.
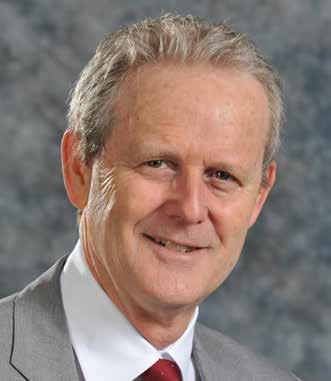
Prefabricated buildings had been somewhat stigmatized in the past, carrying a connotation of inferior quality properties. However, that notion seems to be dissipating as modern modular buildings are now virtually indistinguishable from site-built projects to the casual observer.
Larry Armstrong, CEO of Irvine architectural firm, Ware Malcolm, explained that modular construction is just as safe and durable and can be just as aesthetically appealing as conventionally built properties. Armstrong went on to explain that modular also carries the added benefits of faster construction schedules and greater environmental efficiency, discussed in more detail below.
Overall Cost /Construction Time Savings
Hardimen, the MBI executive director, estimates that costs for building modularly generally run 5-10 percent less than conventional construction. Moreover, the shortened construction period is a key aspect of the allure of modular. Hardimen estimates that modular construction on average saves about six months from start to completion versus a conventionally constructed property, a major factor in the return on investment calculus.
For example, if an Orange County developer of a 100-unit apartment brings his product to market six months faster with a prefabrication approach versus on-site construction, and assuming average rents of $2,748 per month (that’s the average OC rent as of Q3 2022, per adjacent chart), the developer banks $1,648,800 in gross rents (less vacancy) before he would cash his first rent check using a traditional construction format. Hardimen says this construction time savings is often the most compelling reason why developers turn to modular, and enables some projects go forward that otherwise wouldn’t but for the accelerated revenue stream.
Building Heights for Modular Apartments
Hardimen indicates that the typical prefab apartment is usually three-tofour stories. But with advancing technologies and innovative design modular can now go much higher. The world’s tallest modular multifamily structure spans 44 floors. The 2020 completed project, named Ten Degrees, is located in the London borough of Croydon. This Greystar managed property also features an adjacent 39-story apartment tower. The two modular buildings together provide 546 residences with a mix of one-, two-, and threebedroom units. A total of 1,500 modules were factory-fabricated to produce the finished product.
Affordable Housing/Housing for Homeless
The hue and cry for affordable housing in recent years, particularly in California, begs the question of whether prefab structures might be helpful to the cause. As of a 2019 study, the Golden State had a 978,000 home shortfall (inclusive of detached houses, condos, and apartment units) — easily