20 minute read
THE SHORTAGE OF QUANTITY SURVEYORS IN HONG KONG
HONG KONG
THE SHORTAGE OF QUANTITY SURVEYORS IN HONG KONG
By Dr. Peter Ng FAIQS, CQS
HONG KONG
Hong Kong’s construction expenditure over the next ten years is forecast to range from US$28 billion to US$42 billion per annum across both private and public sectors. The government will continue to invest in public housing and infrastructure developments, such as land resource expansion, hospital redevelopment, and road and railway network development. Undoubtedly, these plans will require a large amount of construction professionals such as quantity surveyors. However, given the current industry status, there is a shortage of these professionals in Hong Kong. Due to the shortage of quantity surveyors, the industry will need to enhance the efficiency of quantity surveying works. Such drivers encourage us to discover newer technologies including Building Information Modelling (BIM), IoT and block-chain and consider how they could assist in their work being completed in a more effective manner. An example would be the wide use of BIM when conducting measurement and cost estimation. To a certain extent, it saves time in the heavy loading resulting in a faster takeoff while maintaining accuracy. In addition, the necessity of digitalisation makes documentation work more effective and accessible. It is believed that the wide use of BIM will diminish the use of traditional Bill of Quantities (BoQ), alongside the concurrent rise of smart building developments with the exploitation of big data, artificial intelligence and machine learning supported by input from quantity surveyors. There is an opportunity for quantity surveyors to create a niche for themselves in the market as the best people to manage the models, as they can analyse the vast amounts of data generated by this new modelling process. At Beria Consultants, we are currently adopting the use of 5D via the BIM model for taking off, estimating, and achieving cost control. In parallel, we are processing the digitalisation of our cost data and relevant contract data with the aim of consolidating our knowledge to enable a more effective and efficient practice for future projects. We are exploring the possibility of applying artificial intelligence and machine learning into our field and with the aim of assisting cost plan preparations. With the COVID-19 outbreak, there has been a noticeable shift in working practices, driven partly by limitations on in-person gatherings (i.e., face-to-face meetings) and working from home. The pandemic accelerated the adoption of new technologies and creative initiatives. At Beria Consultants, the advancement of cutting-edge technologies has allowed us to smoothly implement work from home arrangements, using video conferencing software to foster digital collaboration. As a result of the implementation of many COVID-19 policies, a lot of work will still need to be done in order to recover lost ground as companies and personnel relocate away from Hong Kong. One of the most significant changes brought about by the rise of new technologies in the workplace has been on working practices; the younger workforce is in favour of more flexible working arrangements, as they are able to deliver their work just by linking up to fast wi-fi and making use of data hubs like the cloud.
There is much potential for quantity surveyors to adopt these technologies to work remotely. Be it making the building site a potential office, quantity surveyors can update cost plans remotely and
The industry will need to enhance the efficiency of quantity surveying works.
HONG KONG
create BoQ whilst on site. Not only will this make for a faster costing process, but it will also ensure a more accurate final model. The new technologies have the potential to cut down some of the heavy labour required for BoQ measurement and the large filing process of cost data and documentation.
The recent wave of emigration from Hong Kong has also worsened the shortage of quantity surveyors situation, particularly across middle management staff. Just in the past year alone, Beria recorded almost 4% of staff leaving Hong Kong to immigrate abroad. This was primarily around staff between the ages of 30 to 50, as they saw an opportunity to gain better development for their children, better quality of life, or becoming a permanent resident in foreign countries.
There is much potential in these technologies that we can adopt to enable quantity surveyors to work remotely.
Beria's experience is consistent with the findings of a recent survey published by the Hong Kong General Commerce Chamber that suggested middle-aged employees were more likely to emigrate, as respondents in the survey indicated that the age 30 to 50 bracket is the dominant group leaving Hong Kong. The survey also described a significant increase of about 35% in the number of companies facing brain drain. It also highlights that the increase in professionals leaving Hong Kong would undoubtedly have major economic implications on the city. For example, Beria experienced a high turnover rate of over 40% last year. Given the increased competition in hiring experienced quantity surveyors in the market, there has been a knock-on impact driving up salaries as well.
Employers, as a result, will need to consider increasing salary and other benefits as retention measures to encourage staff to stay. Meanwhile, the job pool is still in demand – quantity surveyor graduates from local universities this year are believed to have 100% employment rate, with most graduates holding several offers at hand. In attempt to address the quantity surveyors shortage, Beria is trying to take on apprentices to attract young professionals from other fields to transition into the construction industry. While early results are promising, it requires extra resources to be allocated towards in-house training as well as extending our recruitment drive to trainees currently undertaking part-time courses in local institutions. We hope that these efforts can contribute to reducing the employment shortage in the future. In my view, to overcome the current shortage of quantity surveyors, a rethinking of quantity surveying works is necessary and requires a timely adoption of new technology. This needs to be supported by higher and further education institutes to ensure training can adapt to the changing image of the quantity surveying profession. In particular, this needs to reflect working environments that suit young professionals who expect flexibility and habits that are influenced by a modern, global community supported by disruptive technologies and social media. This new high-tech image is what quantity surveyors should come together to figure out.
This article is written by Dr. Peter Ng FAIQS, CQS. He is the Chairman and Founder of Beria Consultants Limited in Hong Kong.
TIMBER
EXPLAINED: TIMBER SUPPLY AND PRICING
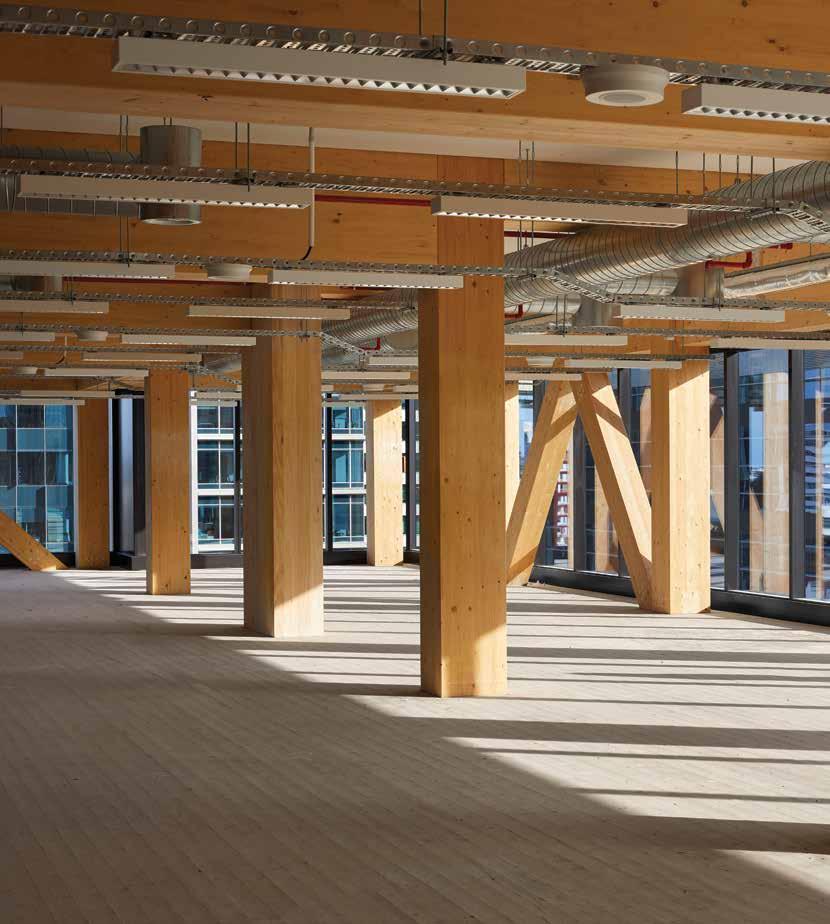
By Laurence Ritchie
TIMBER
This image is authorised for the promotion of FWPA only. For non-FWPA usage you must obtain permission from studio@tomroephotography.com
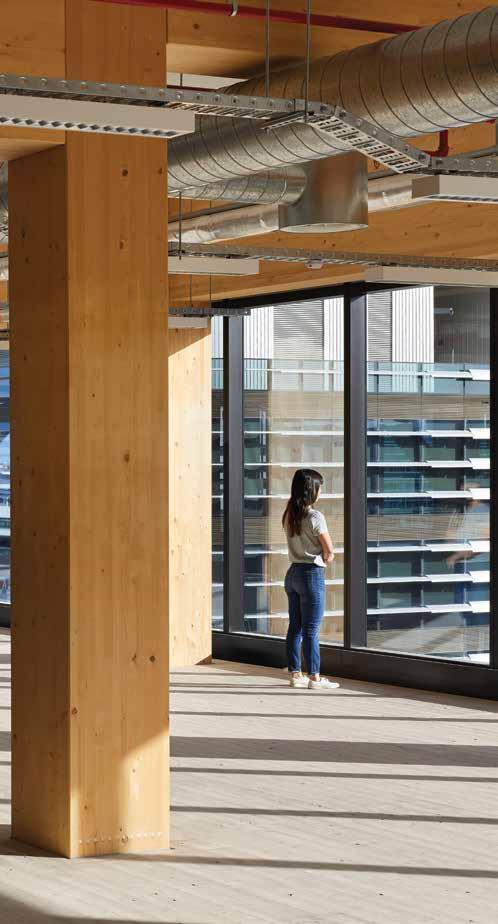
INTRODUCTION
Tall timber projects have seemingly popped up all around the nation in recent years. Whether it’s 10+ storeys in Perth, Brisbane or Melbourne or 30+ storeys in the centre of Sydney (albeit in composite form), timber construction appears to be mainstream for forward thinking, climate responsible developers. As this premiere selection of towers grows, so too have the prices of structural timber, which have risen at unprecedented rates since late 2020. A key issue in a booming housing market, it seems as though every man, woman, dog, cat, and galah have their own take on the reason for this price growth and what we can expect next. In this article, we take a closer look at the reasons for the price growth in structural softwood in Australia and around the world and suggest what price movements we might be able to expect in the coming months. This article draws on a range of information and data sources, but perhaps none more so than the highly topical and valuable insights offered by Kevin Peachey, Statistics and Economics Manager at Forest and Wood Products Australia (FWPA). Kevin regularly releases the ‘StatisticsCount’ newsletter, which should be required reading for any cost consultant wanting to explain movements in the price of timber-based building products in Australia. Articles from Kevin’s newsletter can be found on the Forest and Wood Products website (https://www.fwpa.com.au/news/ newsletters/statisticscount-newsletter. html). Before we delve into the inner machinations of Australia’s timber pricing, it is helpful for us to have a highlevel understanding of the landscape of Australia’s timber industry. While certainly not wholly to blame, Australia’s
TIMBER
Image credit: Laurence Ritchie current market position leaves the economy vulnerable to international price fluctuations for structural timber. This is hardly unique to timber – many of the products that make up Australia’s homes are imported from somewhere – but it may be felt more as timber framing is difficult to substitute. Yes, builders can move to steel framing, but this market suffers from a similar dynamic, and requires a leap of faith for builders who have always preferred the superior workability of timber framing (our only renewable building material, I might add). Over recent years, it has been typical for approximately 25% of the ~2 million cubic meters of structural softwood products used in construction and DIY projects around Australia to be imported. While we will generally purchase these softwood products from whoever is selling at the lowest price, it is normal to see the majority of our structural timber imports sourced from Eastern and Northern Europe, with a healthy portion also sourced from Canada.
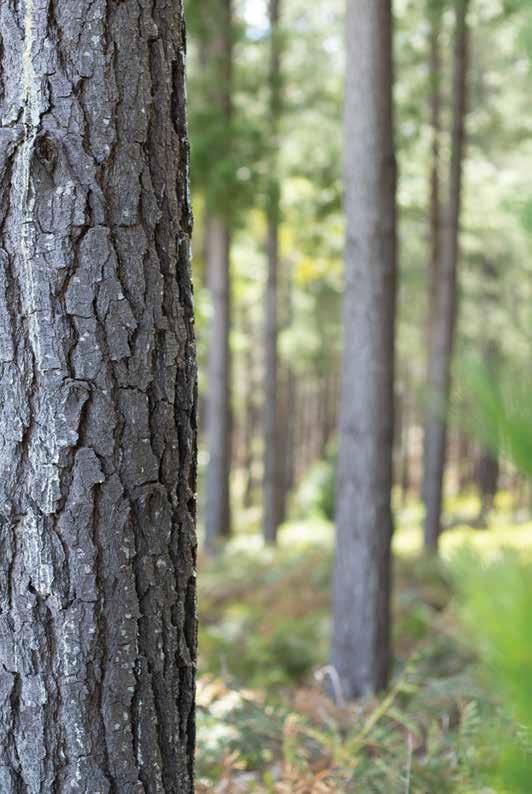
While analysts have noted the minimal growth of Australia’s softwood plantation area since 2009-10, and the expectation that imports of softwood will need to double by 2050 in order to keep up with demand, until mid-2020 there were few concerns about immediate supply beyond the expected seasonal bushfire damage. Cue the entrance of COVID-19, and the accompanying cash splash by governments desperately trying to prop up economies via the building sector. Almost overnight, the world’s construction industry was turbo charged. Buoyed by government grants and mammoth announcements of social housing and public infrastructure, demand for the building products which go into renovations, detached, and
TIMBER
low-rise semi-detached housing spiked around the world. While necessary, this spike in demand came at a difficult time for the structural softwood industry in North America.
Canada is renowned as a timber powerhouse, in 2016 pumping out more export timber (known as ‘lumber’ in their dialect of the Queen’s English) than any other country. It may not surprise you then to know that Canada also dominates the USA’s lumber imports, accounting for over 80% of those received in 2020. This extreme reliance left US construction market sensitive to shocks from Canadian producers, and what do you know… there just happened to be a number of severe shocks which coincided with COVID-19.
Canada’s largest structural timber producing state, British Columbia, has had a few difficult years. Swept with wildfires in 2017 which collectively decimated hectares of productive forest, and victim to a plague of mountain pine beetles which destroy ecosystems and wreak havoc for foresters, supply was starting to constrict years before COVID-19 induced supply chain and logistics stresses. With a significant uplift in construction activity (either new build or renovations) resulting in increased demand for structural wood products, and declining supply from their largest importer, American distributors had to look to other markets in order to feed their hungry economy. Desperate for stock, these distributors were willing to pay more in order to secure the product, resulting in sky rocketing price growth in the US (up to and exceeding 400% of pre-pandemic prices). Some may recall social media posts from this time comparing how much lumber US$1,000 would buy before and after this record growth. While often tongue in cheek, the few lengths of lumber shown in the images were not far from the truth. Seeing this need, some international producers who typically supply Australia quickly rose to the occasion, diverting much of their Australian stock to their higher-paying American customers. Even with our local industry operating at maximum efficiency – which included processing logs partially burnt in the 2020 bushfires – it was impossible to increase total supply to meet demand, resulting in price growth for fabricators and distributors which then trickled down to the jobsite. Australian builders have been fortunate to avoid the magnitude of price growth witnessed in the USA, however nonetheless, price growth has been significant, and supply stunted since the pandemic (and associated stimulus measures) began. So, what comes next? With structural softwood pricing at an all-time high and our local sawmills running at full capacity, the industry is questioning what is around the corner.
While the US timber pricing eased slightly through 2021, further natural disasters – this time in form of floods and landslides which cut the world off from much of British Columbia’s timber industry – resulted in another spike, keeping international supply tightly constrained. This demonstrates the sensitivity of the American lumber market, which in turn affects Australia’s local supply. Assuming there are no further shocks to the USA’s timber supply, and that the extreme demand for new detached homes (and therefore structural softwood) wanes as government stimulus is wound back, we may expect timber supply to start to return to pre-pandemic levels.
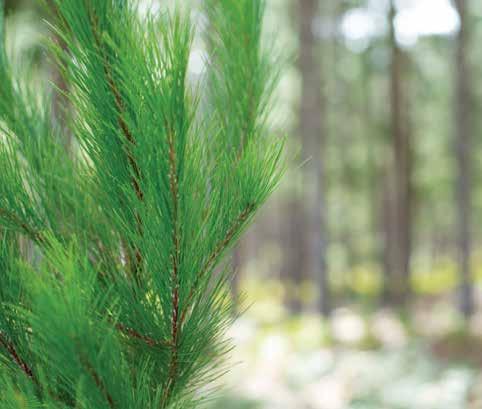
Image credit: Laurence Ritchie
TIMBER
Image credit: Keith Webb
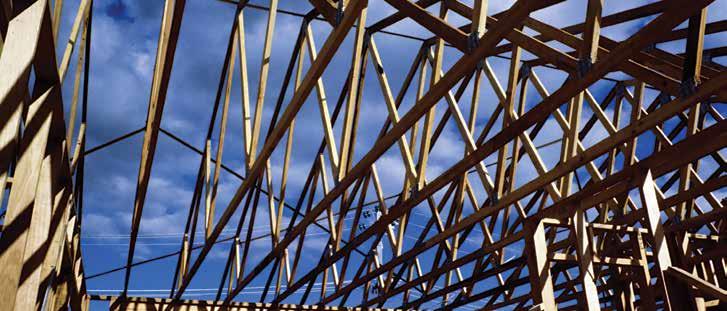
This rebalancing of our market may take a further 12 months to occur as builders work through their backlog of projects which have necessarily been delayed due to material (and labour) shortages. While this forecast considers the immediate future of supply, it is also important for us to look to the medium and long terms. Continued uptake of timber construction is a great win for the environment, not to mention the builders and building occupants who work with or around it every day. Every piece of sustainably sourced timber that goes into a building, locks up carbon which has been removed from the atmosphere through photosynthesis, directly fighting climate change while delivering a warm, relaxing, and welcoming environment. However, as Australia’s demand for structural softwood increases so too should our areas of plantation softwood if we are to shield our market from fluctuation in international supply and pricing. Engineered Wood Products (EWPs) offer a partial solution to this problem. Made by joining multiple smaller timber elements together to produce a complete product, EWPs can render lower grade timber – which is currently chipped or used to make pallets – suitable for structural loads typical in residential design. While EWPs with higher performance and structural capacity are turning mainstream in Australia’s commercial construction market, the lower-strength versions will find their place in smaller scale detached residential construction in the coming years. In parallel, it’s important that Australia accelerates the growth of our softwood plantation area. Plantations offer a host of benefits for our people – they are great carbon sinks, they offer both wind and sun protection (most useful when implemented alongside agriculture), they play host to a range of recreational activities, they support entire regional communities and of course they supply our construction industry. However, with a typical softwood plantation taking decades to reach harvesting maturity they say the best time to plant them was 30 years ago, but the next best time is now.
Ongoing support of and investment in the timber supply chain will bring stability to our market in future years. As presented in this article, there are both short- and long-term strategies which will insulate Australians from the dynamics of global timber pricing, supporting sustainable, efficient, and affordable construction for decades to come. While COVID-19 has had major impacts on all construction supply chains, it has exposed underlying problems which we now have the opportunity to address and resolve for a more sustainable future.
This article was written by Laurence Ritchie. Laurence Ritchie is the Cost and Program Estimator at WoodSolutions.
Woodsolutions have paid for, and written, this advertorial. Learn more at https://www.woodsolutions.com.au
TENDER PROCESS
THE TENDER PROCESS
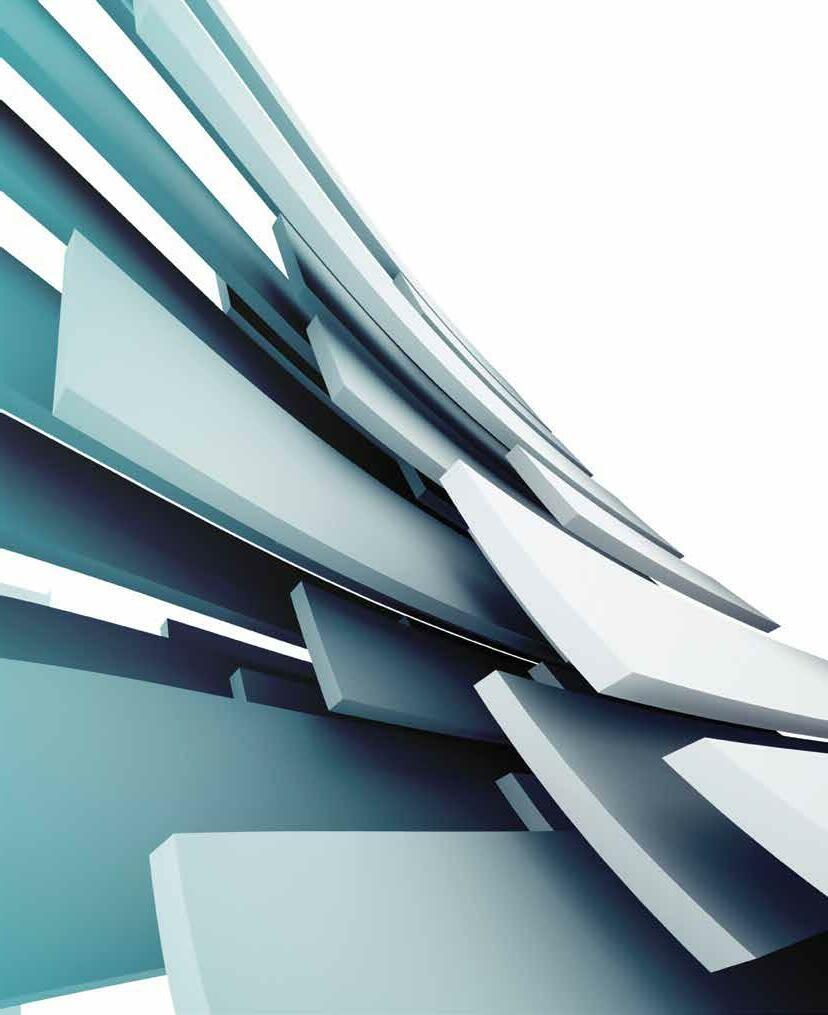
AND ITS POTENTIAL IMPACT THAT CAN THEN LEAD TO PROJECT COST CHALLENGES
By Paul Johnson MAIQS, CQS
TENDER PROCESS
This article came about following a LinkedIn post I wrote in March 2022 after the collapse of two building contractors with operations in South East Queensland. The post was specifically about the construction tender process, and how their typical short durations can lead to project cost challenges. Some of the feedback at the time included:
“And it gets shorter for us further down the food chain at subcontractor level and the issuing of every document, drawing, specification, and brief with the statement that we are to comply and cross check all these documents and allow for the most onerous condition” –
Matthew Leitch (Fredon) Since then, I have discussed this topic with colleagues and in meetings with contractors. Many people are of similar opinion that short tender timeframes, and the subsequent delay in appointment creates undue pressure on contractors.
… I consider that a generally longer tender period would alleviate some of the cost and time pressures during a tender period.
In my over 25-year career in the construction industry, I have worked as an estimator, cost planner and quantity surveyor for developers, contractors, subcontractors and in consultancies. I have also taught measurement and contract administration subjects at Bond University. As an estimator/cost planner I have been involved in projects of up to $500m including working in the direct delivery on site. I have worked in Sydney, Gold Coast, Brisbane, Auckland and in Orlando Florida. I currently run Alto Cost Management, a quantity surveying consultancy that I established in July 2018.
The Australian construction market in 2022 is wrought with challenges and continues to evolve:
• Material price escalation is at an alltime high • Many materials have long lead times • Construction contracts limit the ability to pass on rising material costs • Skilled labour is in demand with availability of staff impacted by
COVID-19 lockdowns
• Tender margins vary and can sometimes be extremely low for the relative risk
• Tender periods are typically of short duration.
Whist tender periods have almost always been that way, it is becoming more and more common for owners and their consultant advisors to take significantly longer to appoint a successful tenderer. Given the usual delay in appointing a contractor, I consider that a generally longer tender period would alleviate some of the cost and time pressures during a tender period. The duration for a construction tender varies depending on the project value or complexity. The majority are less than three months, many even under one or two months.
A construction tender can operate broadly as follows, this example is for a fairly typical four-to-five-week tender
TENDER PROCESS
period on a fully documented or design and construct tender:
WEEK 1
• Document set received from the client
• Workload assessed and decision made whether to prepare builders Bill of
Quantities (BoQ) in-house or to issue to external quantity surveying forms • Documents issued to quantity surveying firms for preparation of a bill of quantities, and to a programmer for a schedule and/or methodology • At the same time these documents may be issued to the market, sometimes without a clear scope of works • Estimator communicates with the market.
WEEK 2
• BoQ is underway and tender RFI’s sent back to the client for a response • Request made for extension of time • An addendum could be received and range in complexity from one or two new reports to a full document reissue • Estimator communicates with the market.
WEEK 3
• BoQ continues and is issued to the contractor
• Contractor adds rates or the BoQ to determine the budget • Bulk checks carried out (if time available) and packages sent out to the subcontractor market
• Request for extension of time could be made and a further addendum could also be received for inclusion in the tender • Bid team meets to review scope of works, programme, and methodology • Potential value engineering items proposed.
WEEK 4 – WEEK 5
• Rated BoQ's and tenders return from the subcontract market
• Pricing comparison/ subcontractor analysis carried out • There may or may not be trade coverage and the contractor may have to use historical rates from previous projects to fill the gaps • Value engineering items (or smarts) are proposed to assist in winning the project • Some value engineering items may not even be viable or accepted by the client but are still utilised to potentially win the project • In-house tender reviews performed and price finalised • Tender issued to the client/project manager. In that relatively short tender timeframe, the contractor will have been required to include all designed scope, all scope gaps and everything else for a completed tender price, should they be successful in winning the project. It is then likely that they will wait a number of weeks or months for a response, or for the successful contractor to be appointed. These are two project examples over the past year.
PROJECT 1
The project was tendered in the latter half of 2021 for a proposed design and construct contract.
• Documentation Period:93 days (four
months) from February 2021 • Construction Tender Period: 25 days (just over one calendar month which commenced on 1 July 2021 and was initially proposed for completion on 4
August 2021) • Forecast Tender Award: 1 September 2021 (one month following tender close). There were six addenda issued during the tender period and the tender close date was extended to circa 11 August 2021. Our office was appointed by one of the four tenderers to operate the tender for them, we were successful in that regard over other consultancies due to the extensive cost planning and estimating work we have carried out.
Our works included builder’s BoQ trade packages, pricing of the BoQ and subcontractor price analysis to produce the final tender.
During the tender period, the bills of quantities were issued to the builder after two and a half weeks and subsequently issued out to the tender market.
As is often the case with design and construction projects, the design may not be complete at tender, and it is the responsibility of the contractor to complete the design. The scope gaps in the documents were required to be included in the tender price. Even after the initial tender period which closed on 4 August 2021, and with award forecast for 1 September 2021 the works only commenced on site in late November 2021, close to three months after the initial forecast tender award date.
At the time, the tender period was extremely compressed. The design was incomplete, and a series of assumptions were required to enable a complete tender to be submitted.
TENDER PROCESS
All builders would have been required to allow substantial tender allowances in their respective pricing.
PROJECT 2
The project was tendered in early 2022 by a local client-side project management company: • Construction Tender Period: Just over 1 Calendar month which commenced on 10 January 2022 and was initially proposed to close on 10 February 2022) • Forecast Tender Award: 25 February 2022 for Design and 14 March 2022 for
Construction.
As at 23 April 2022, this tender has still not been awarded.
In both of the examples described above, the contractor and subcontractor market would have devoted significant resources for a project with a forecast award date that was then extended three or more times longer than the initial tender period. In those short tender timeframes, there would almost certainly not have been a high level of trade coverage, with any gaps potentially covered with historical cost data. Commitments for material orders would have to have been placed on hold until potential approval/ appointment. Given current price escalation, this could pose significant risk and I know of one contractor in mid-2021 that was still using reinforcement rates 30% lower than what the market was advising. In instances where a contractor may have included value engineering options to secure a project and not accepted by the client, the contractor would then be under a high cost pressure from the outset. There was also one project I know of in Queensland where this occurred for a façade element where the contractor proposed an alternative at tender which ultimately was not accepted during construction.
SUMMARY/CONCLUSION
Noting the above, a tender period can be significantly compressed, often relying on an incomplete design, and then leaving the builder to bear all the risk, in the hope of then gaining a few percent margin over the project. I feel that incorporating longer tender periods where project risks can be effectively evaluated could lead to less project cost challenges and potentially avoid receiverships that have occurred recently in this South East Queensland construction market.
This article has been written by Paul Johnson MAIQS, CQS, Managing Director of Alto Cost Management.